Machine Learning
Vision & Sensors
V&S
H2 Deck By Bold Name
h2 xxxxxx
H1 xxxxxx
h2 xxxxx
While machine learning is a subset of AI, deep learning should be viewed as a subset of machine learning. By David Dechow and John Butler
Machine Learning
for Automation & Quality Inspection
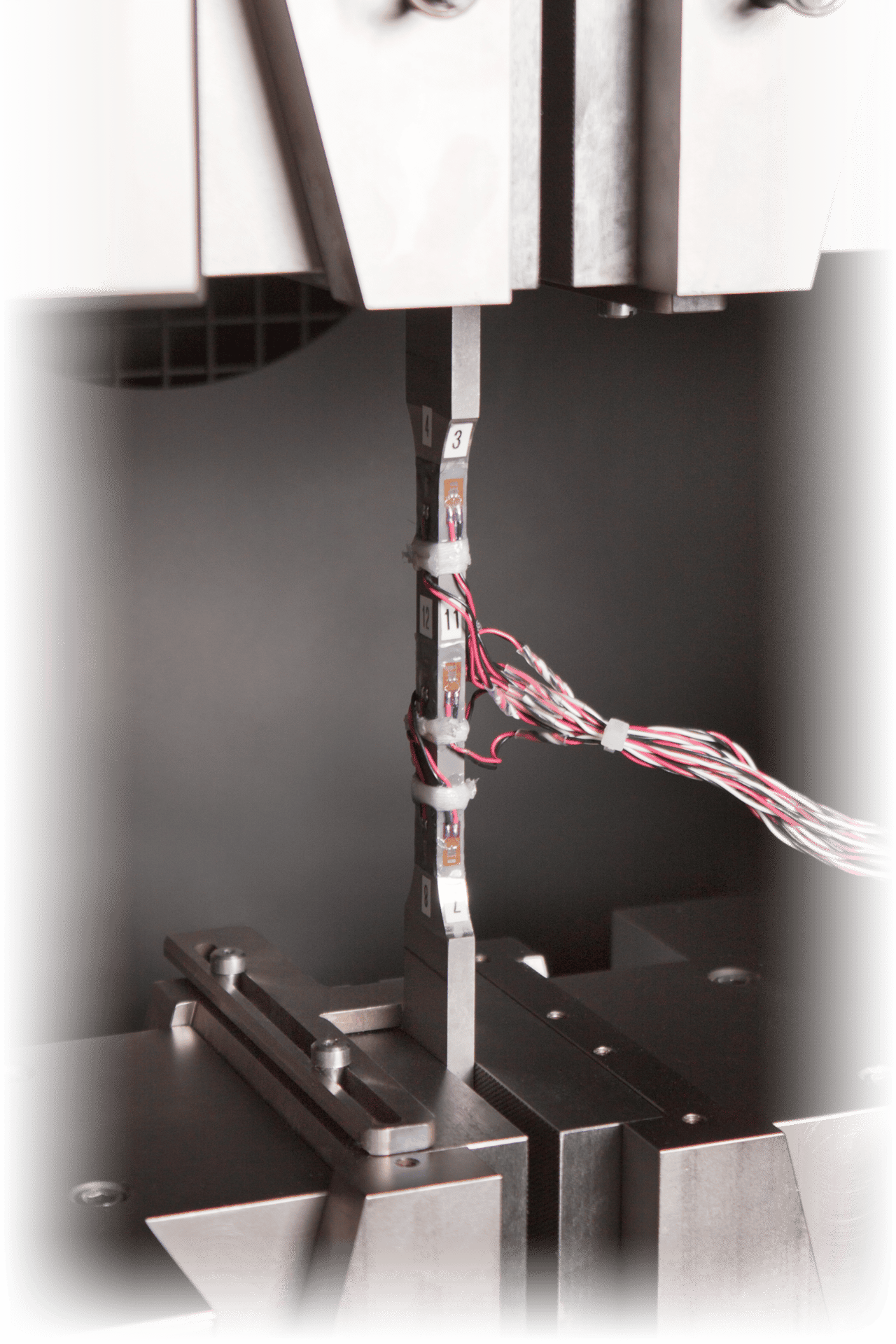
H2 Deck By Bold Name
h2 xxxxxx
H1 xxxxxx
h2 xxxxx
Artificial intelligence or AI is a hot topic these days and an oft-used term in nearly every industry. Automation, quality inspection and manufacturing are no exception. Rather, these are a major proving ground for development, experimentation, and implementation of AI for industrial applications. In many instances however, AI is a bit of a catchall term, often referring to the application of some level of computer-assisted decision-making. When we unpack it, the more relevant pieces that people often speak of are machine learning, deep learning, and computer vision – individually different but collectively referred to as AI. The discussion stands to benefit from some untangling to enable an improved level of clarity around what each does, why they matter and the value and benefit that machine learning brings to the industrial automation and quality inspection landscapes.
Machine Learning vs. Computer Vision
Put simply, computer vision is the process of interpreting information from images or videos in an automated fashion using computers instead of people. The algorithms and models used in computer vision applications tend to be rigid in that they are tailored to find and identify specific items in a scene – these could be defects, the absence or presence of something, or incorrect characters on a label. The inspection environment needs to remain static as do the items being inspected. Changes in the variables almost always mean that the model must be updated, reconfigured, and redeployed – by humans.
Machine learning on the other hand uses historical data to make decisions related to the interpretation of information from images or videos. Relying on patterns and inference, computers can identify defects or inaccuracies in a scene using algorithms or models that can adapt to changes or to variables in the environment. Initial models are often trained with supervised learning – using people to characterize and label pass/fail or good/bad results based on an existing dataset and feeding that information into the model. From that baseline, the system can begin to perform inspection tasks without explicit instructions.
Where Does Deep Learning Come In?
While machine learning is a subset of AI, deep learning should be viewed as a subset of machine learning. Using artificial neural networks, it aims to mimic the learning process of the human brain, eliminating the need for human involvement to learn from its environment. Whereas machine learning algorithms often rely on human correction to help them to overcome mistakes, deep learning leverages high-performance computing to improve through repetition on its own. To accomplish this, deep learning relies on data sets that are significantly larger than those needed to train a machine learning algorithm along with substantially longer processing and training times to achieve reliable accuracy and sophistication.
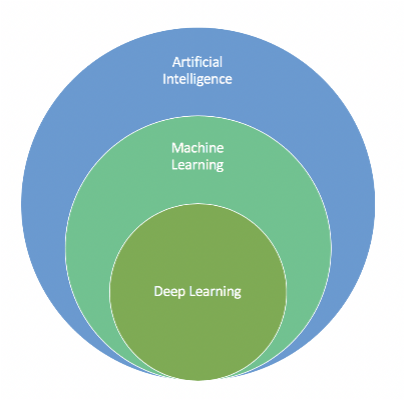
Image Source: JavaPoint
Deploying Machine Learning to Solve Practical Problems in Industrial Automation
When we aggregate the various technology subsets – computer vision, machine learning and deep learning the result is an artificial intelligence solution that can extend across a multitude of use cases for automation and quality. Machine learning as the potential to play a major role in the successful implementation of AI across the industry, combining traditional computer vision capability with added intelligence that enables increases in productivity, safety and efficiency within applications and tasks that have traditionally been served by human operators. In addition to traditional applications for identifying defects in a product or missed steps in a process, opportunities to create value can be found where processes are subjective, and rules not easily defined or organized into logical steps or decisions. Likewise, scenarios where outcomes are known but the action to be taken is difficult to predict or dependent on many conditions are well-suited to machine learning technology.
Industrial Robots
The number of robots being sold and deployed continues to grow and is currently setting records annually. Although robots have been used in industrial automation for decades, early functionality consisted of fixed, repetitive routines in a setting that remained static. Today however, Autonomous Mobile Robots (AMRs) extend far beyond the scope of set parameters and due in large part to machine learning, can self-navigate and respond to changes in factory floor configurations, the presence of people or objects as well as other robots. Similarly, robotic arms used in packaging, warehousing and logistics can analyze materials to be loaded onto a pallet or into a carton and can make decisions that result in optimal placement and stacking.
Predictive Maintenance and Failure Prevention
Equipment failure in a production or manufacturing environment often represents one of the worst problems – a halted production line which can have a cascading impact on other operations in addition to impacting a manufacturer financially for every minute lost. Machine learning offers the ability to develop and deploy intelligent systems which can monitor and evaluate production equipment continuously. Systems that can self-learn utilize data from production line sensors to identify patterns and anomalies and alert to drops in performance. With these insights, maintenance can be scheduled proactively at cost-effective times rather than reactively when something breaks. The results are improved productivity and a reduction in costly repairs and downtime.
Defect Detection
Defect detection is perhaps the most popular use-case for implementing machine vision in an automation or quality inspection application. Like the evolution of robotics, traditional machine vision applications are programmed with rigid instructions – configured to look for specific defects in the same product or material in repetitive fashion. Machine learning brings advanced analysis and decision-making to quality inspection by enabling those systems to become more dynamic and tolerant of changes in inspection environments and other variables. For example, in label verification, conventional machine vision is designed to inspect specific fonts or typesets. Utilizing machine learning provides for the ability to inspect varying font styles as well as to make correct pass/fail decisions despite changes in contrast levels and text placement. Advanced machine learning can have the benefit of reduced false positives resulting in less waste, reduced manufacturing costs and higher manufacturer profitability.
Accelerating the Trend
The capabilities that are made possible with AI are largely the result of advances in software development and evolution. The potential to enable computers to simulate human interaction through data analysis and pattern identification has dramatically altered the complexity, ability and accuracy of our automation and quality systems. While less talked about, hardware progression makes large-scale deployments possible and until recently, many AI implementations have been limited in terms of where and how they could be used, relying on large computer infrastructure to execute their programming.
Recent advances in peripheral components including CPUs, GPUs, and TPUs, embedded processing and data transfer technologies have created the conditions for dramatic reduction in the physical size, power consumption and cost of deploying machine learning solutions. These advancements, coupled with sophisticated software are accelerating deployment in the form of edge and mobile computing, have made it possible to implement AI in applications where just a few short years ago it was thought impossible. If history is any indication, we are primed for rapid expansion of the market segments and industries served by machine learning along with continued growth in its use across existing and new applications for the foreseeable future, fueled by our drive for greater productivity, efficiency, quality and safety in the work we do and the products we make.