The Rise of Differential Pressure (DP) Decay Leak Testing in North America
Test & INspection
What is DP and how are manufacturers using this test method to achieve better resolution and quicker cycle times? By Gordon Splete
What is DP and how are manufacturers using this test method to achieve better resolution and quicker cycle times? By Gordon Splete
The Rise of Differential Pressure (DP) Decay Leak Testing in North America
Your choice of leak test method and technology can make a substantial difference in the results of your test, affecting your throughput, repeatability, product quality, and cost.
Pressure Decay leak testing is a popular leak test method used by manufacturers across North America. While traditional Absolute Pressure Decay (integrated with a 24 bit A-D circuit) proves effective for most applications, when manufacturers require better resolution and quicker cycle times Differential Pressure (DP) Decay is becoming a popular alternative. DP offers high-sensitivity, low resolution testing, allowing manufacturers to identify problems faster, increase Gage R&R, and shorten test times.
DP leak testing mixed with a lesser A-D circuit has been a favored pressure testing method in Europe for decades. As transducer technology has become more robust, and manufacturers needed to test to lower leak rates and faster cycle times, DP integrated with a 24 bit A-D circuit has started to become more popular in North America over recent years. Let’s explore why more manufacturers are choosing DP.
How Differential Pressure (DP) Decay Differs From Absolute Pressure Decay Leak Testing
Absolute Pressure Decay Leak Test Procedure
All pressure decay leak tests involve measuring the drop in pressure on the interior of a part. To conduct an Absolute Pressure decay leak test, air is injected into a test part until it reaches target pressure. The air source is then cut, isolating the pressure and the loss of pressure (decay) is measured over a specified time. With an Absolute Pressure test, we use Absolute Pressure transducers to compare pressure related to Absolute Vacuum on the other side of the transducer. A leak is identified when there is a loss in pressure greater than the setpoint. (see Fig 1)
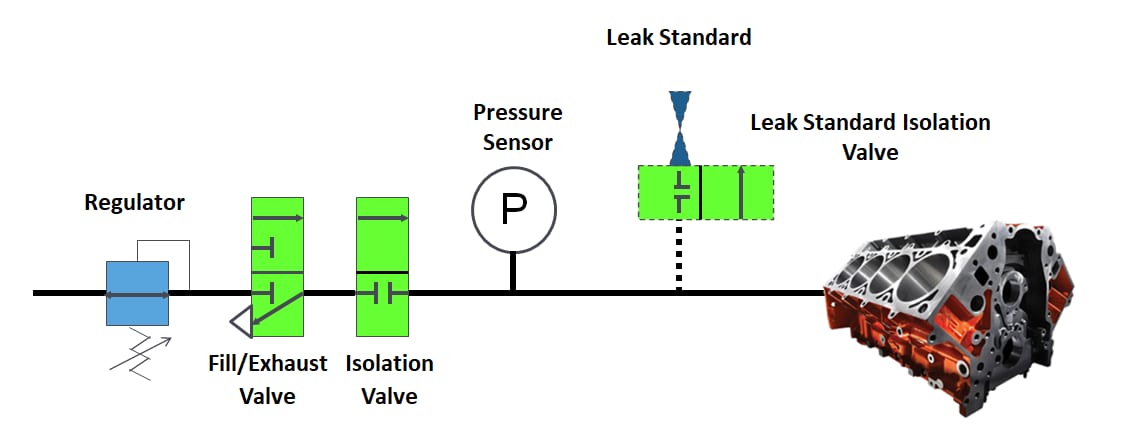
Fig 1: Example of an Absolute Pressure Decay Test Circuit
Differential Pressure (DP) Decay Leak Test Procedure
Differential Pressure (DP) decay leak tests use similar parameters, but tests for leaks by measuring a pressure change between a reference volume of air and the test part volume using a Differential Pressure transducer. The DP leak test cycle fills a test part and a reference volume to a specified test pressure. The air source is then cut off by the fill valve and the test pressure stabilizes between the two volumes. The reference air isolation valves are closed as the exhaust valve is opened, isolating pressure on both sides of the Differential Pressure transducer. The transducer measures for a change in pressure between the test part volume and the non-leaking reference volume during the set test time. If the DP decay measured is within the set test limits, the part passes the leak test. (see Fig 2)
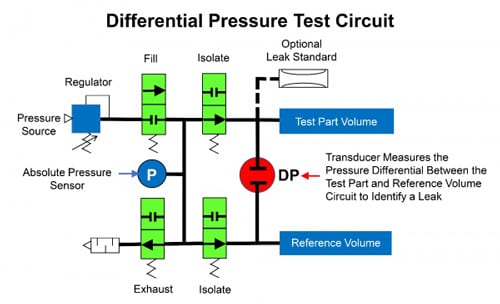
Fig 2: Example of a Differential Pressure Decay Test Circuit
How DP Technology Delivers Higher Test Sensitivity
Depending on the testing application, DP leak detection will provide a higher level of sensitivity than standard pressure decay tests. DP removes the thermal event that occurs from pressurizing to a test pressure during an Absolute Pressure decay leak test. Mix this result with a high resolution 24 bit A-D circuit and a small range DP transducer and the system will have a very high precision measurement. This allows the test to go into stabilization more quickly and allows us to get a clearer signal, with greater separation and tighter data to quickly and more easily identify between good and bad parts, resulting in a very repeatable test. (see Fig 3 & 4)
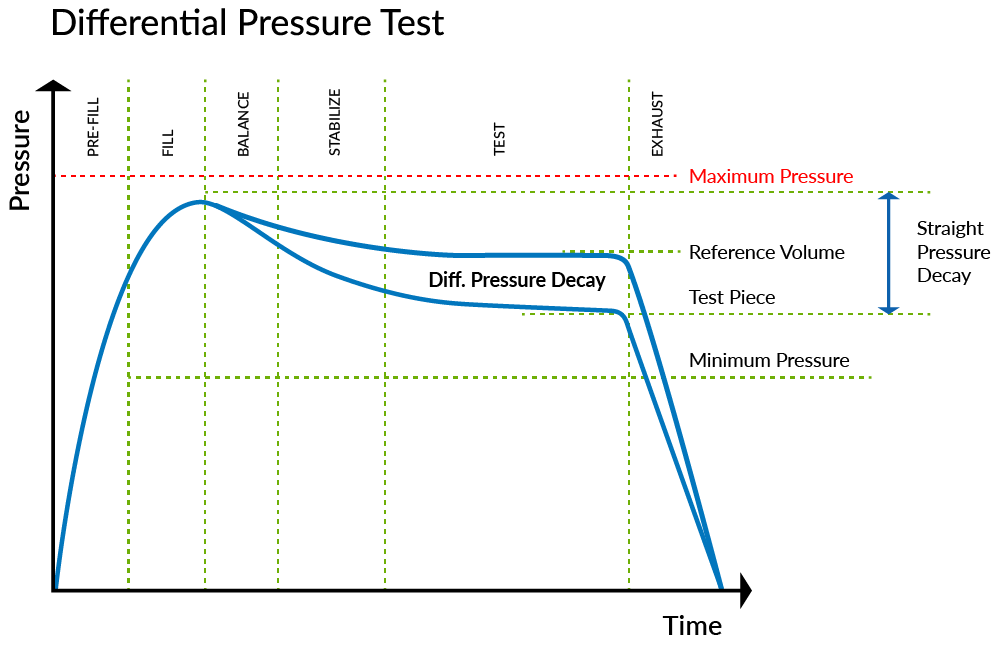
Fig 3: By using a reference volume during Differential Pressure decay leak testing, your test is able to stabilize more quickly, which cuts out the ‘noise’ in your test data.
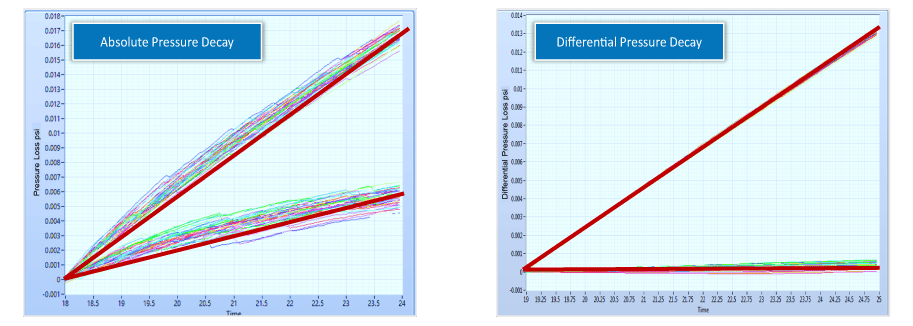
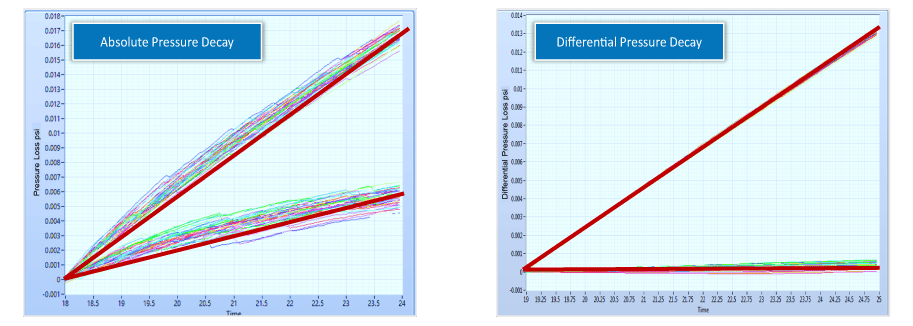
Fig 4: In the above representations of test processes, you can see that the results are much tighter and more repeatable using the Differential Pressure decay leak test method.
Resolution Example (24 bit A-D Circuit and Transducer Range)
Absolute pressure decay technology has a pressure loss measurement resolution of 0.000021Dpsi (0.14 DPa), and a leak rate resolution of 0.006 sccm. You can expect to achieve Gage R&R >25%.
Differential pressure decay technology has a pressure loss measurement resolution of 0.000001 Dpsi (0.007 DPa), and a leak rate resolution of 0.00005 sccm—10x better! You can expect to achieve Gage R&R <10%.
Choosing Your Reference Volume for Differential Pressure Decay Leak Testing
One extra consideration with DP is that it requires a reference volume. Generally, I have found that 90% of applications don’t require an external reference volume, instead they can use a capped reference on the backside of the transducer.
However, roughly 8% of manufacturers do use reference parts. Though not always necessary, this can be due to preference or depending on the type of part this may provide a clearer picture of the pressure when associated with an actual reference part.
A small 2% of manufacturers will test two parts side by side during their production process. This increases throughput, but if these two parts leak the same amount at the same time, you can mask a leak and receive an inaccurate result.
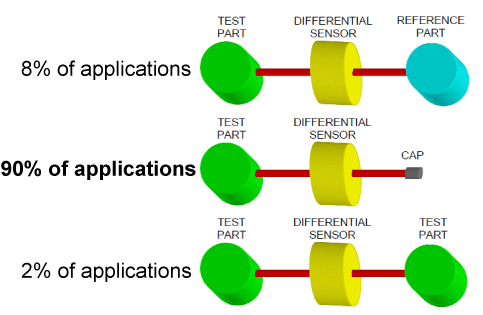
Best Applications for Differential Pressure Decay Leak Testing
Differential pressure decay testing can be used in nearly any case where you’re looking to test non-expanding parts more quickly and to lower leak rates. However, if you don’t have a need to test quicker and you’re testing 10 sccm/10 psi, there’s no major benefit to going with DP over Absolute. But if you’re testing >1 sccm, DP will deliver better resolution and it’s worth looking at how the DP test option would improve your repeatability and cycle time.
The following are some prime examples of common applications best tested using DP:
Testing large non-expanding parts: Ideal DP testing applications include parts and assemblies like EV batteries and drive systems, engines, transmissions, and coolant system final assembly testing.
Testing parts with very small pressure loss, small leak rates: Parts with very small pressure loss could include items like consumer electronics. Parts with small leak rates (0.1-1 sccm) could include industries that require refrigerant testing. Coolant components, for example, may require more stringent testing that can result in bottlenecks on your line. You could use DP during sub assembly testing or to test smaller components with smaller leak rates to improve cycle times and decrease these bottlenecks.
Testing at high pressures (>30 psig): When testing parts at higher pressure (above 30 psig), like brake lines, hydraulic systems, fuel pumps, fuel lines, fuel fittings, or oil passageways, there is a thermal event that occurs and using DP technology for these leak tests helps to decrease the stabilization time necessary for an accurate test, thus lowering cycle time in these applications.
Testing pressure drop over time: Applications that require a measurement of pressure drop over time, including many products in the medical industry, require the increased sensitivity that DP offers to achieve an accurate result.
The Cost of DP
The biggest difference in terms of DP equipment over Absolute Pressure Decay is that the circuit for DP requires an extra valve and there may be an extra cost depending on which reference volume option you choose. However, the cost difference is minimal, and the ROI manufacturers can receive in terms of improved resolution and cycle time can be well worth it, depending on your application.
I’ve had many manufacturers come to me over the past few years looking to achieve lower leak rates and better cycle times and the switch to Differential Pressure decay leak testing has been key to getting them to their desired results and line performance.