Machine Vision 101
Machine Vision 101
Vision & Sensors
V&S
Automated Inspection 101: Benefits for Industry
Automated inspection can take many forms and show up in a wide variety of industries. By Filip Szymanski
Automated inspection can take many forms and show up in a wide variety of industries. By Filip Szymanski
Automated Inspection 101: Benefits for Industry
As a technology, automated inspection has transformed the manufacturing industry, especially for very small, high-value items like semiconductor chips or lithium-ion batteries. Integral to the manufacturing system, automated inspection can be used to determine if a part meets specific quality criteria – and if not, it can reject the defective part – ensuring higher-quality finished goods. In addition to flaw detection, automated inspection tasks can include positioning, identification, verification, and measurement.
Some of the most common applications of automated inspection in manufacturing include finding potential anomalies in tiny parts such as microchips and transformers, discovering scratches or other microscopic defects in TV screens and computer monitors for flat panel inspection. The same vision systems can utilize similar camera technology for inspection of other flat subjects, such as solar panels, but can also include other targets such as food and beverage products. By using specific wavelengths such as near-infrared (NIR) and techniques such as the Normalized Difference Vegetation Index (NDVI), new details can be revealed not normally detected through visible light. An important benefit of automated inspection is that it can detect problems as soon as possible. Since faults cost more to fix later in the production process, it is critical to identify and correct mistakes early.
In addition to manufacturing, automated inspection is used in life sciences and pharmaceuticals, where its applications can range from reducing the probability of cross-contamination to identifying abnormalities in cells.
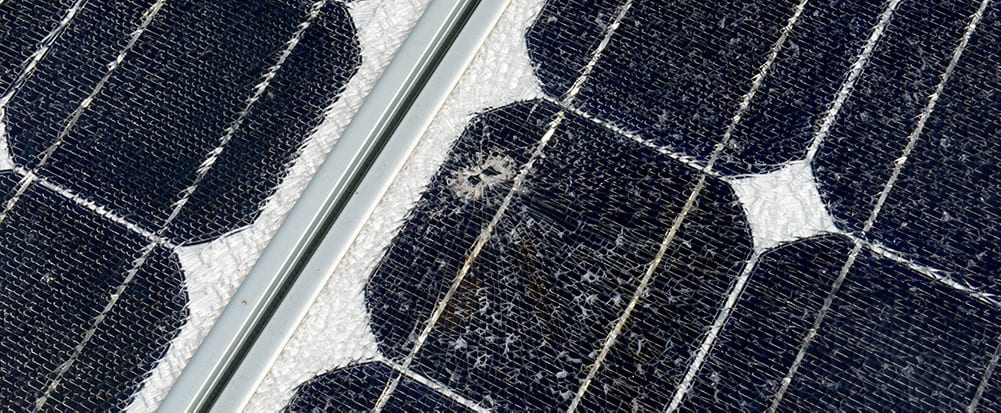
Imperfections in the glass layer can makes cells more susceptible to breakage. Source: Courtesy of Teledyne
What is Automated Inspection?
Automated inspection uses digital or computer-aided inspection for the measurement and analysis of components. Automation can be used to manipulate an object, collect measurements, or assess a component against a specification.
One specific subset of automated inspection is called automated optical inspection, or AOI, which focuses on visual inspection. AOI systems can acquire millions of data points in a fraction of a second, which are then used for visual inspection and precision measurement. Although AOI is often referenced as an inspection system for printed circuit boards (PCBs), it can be used nearly anywhere that visual inspection is required.
An AOI system relies on machine vision to perform the inspection processes. Machine vision uses imaging (cameras or sensors) to acquire visual information from the surrounding environment. It then processes the images using both hardware and software to prepare the information for use in various applications. Machine vision technology often uses specialized cameras or sensors to acquire images, depending on the needs of the application. Choosing the best camera will depend on the application, some common camera interfaces include USB3 and GigE that can plug directly into a host device, while CXP and CLHS require a frame grabber to achieve even higher imaging speeds. Image data is then used for the processing, analysis, and measurement of certain characteristics of the image.
As machine vision cameras continue to advance with higher resolutions and new techniques to capture fast-moving objects, automated inspection has become more precise and sophisticated. Software and processing algorithms continue to improve as well, leading to the growing use of artificial intelligence (AI) and deep learning that is changing the face of automated inspection.
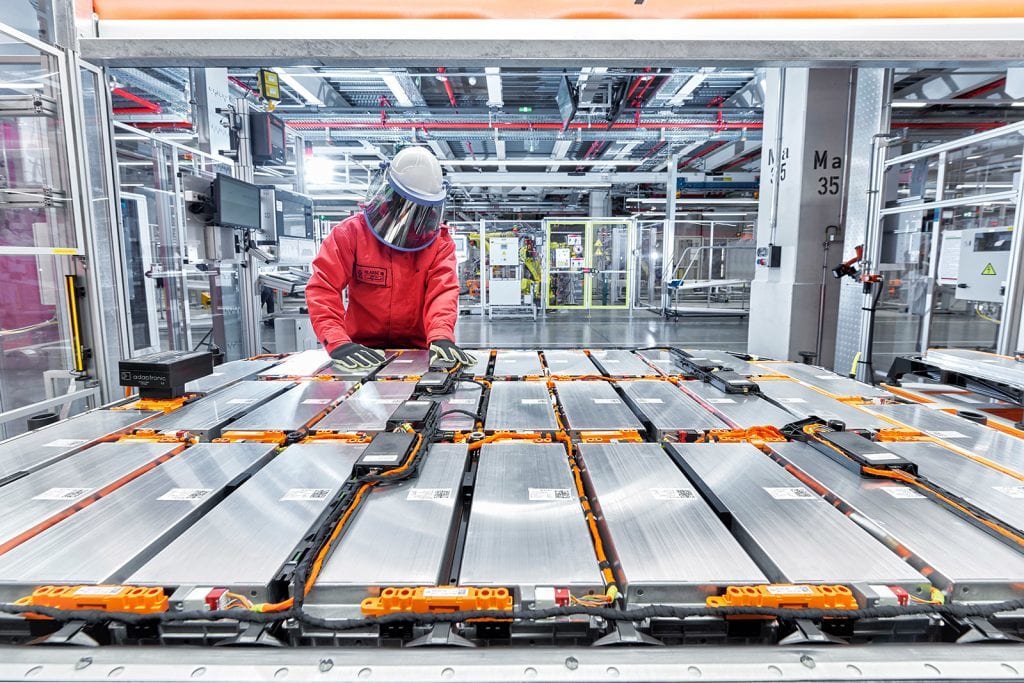
AUDI e-tron Production at the CO2-neutral plant at Brussels: Final acceptance of battery cell module controller and cabling. (Copyright Audi AG) Source: Courtesy of Audi
How does AOI Work?
AOI is the integration of optics, mechanics, electronic control, and software to replace the human eye for visual inspection to aid in quality control.
In its simplest form, a machine vision camera and light source capture an image of the object being inspected. This is analogous to the human eye seeing the object, but the camera can capture more detail, record that image forever, and potentially learn from it. Image analysis software then reviews the image and compares it to the standard of how the object being inspected is supposed to look. This is analogous to the human brain recognizing the part and making a judgment to see if it looks right – however, the software ensures a consistent decision takes place every single time.
Human visual inspection is often contrasted with the automated optical inspection process. With computer-based inspection, items can be inspected at much faster speeds, with more consistent and reliable results. And, unlike humans, computers never get tired, never need a break, and do not mind repeating the same task over and over again.
A human could never effectively inspect today’s printed circuit boards or other tiny components due to their small size, complexity, and fine detail. As PCBs get smaller and more complex, even a relatively simple board can be made up of thousands of components. Yet, the comparison to human vision inspection helps us to conceptualize the process, and manual inspection is still conducted in some industries.
Which Industries Use Automated Inspection?
Automated inspection is ubiquitous for the manufacturing of exceedingly small, low-profile parts like semiconductor chips, but this is not the case for larger objects such as the many cast, forged, and machined parts in a car engine or transmission. According to Metrology News, only about 20% of manufacturing sites rely on automated processes for the inspection of medium and large parts, which has led to major issues for some manufacturers.
To implement a robust and automated inspection process on these types of manufactured parts, it is necessary to measure shape irregularities at high speed, with high accuracy, while being completely impervious to the ambient light of the factory floor. Yet, in-line measurement equipment that meets those requirements has not been available until recently, so manufacturers still rely largely on the human eye for these types of inspections. As automated inspection equipment continues to evolve, manufacturers of larger parts are likely to embrace the benefits of automated inspection.
From semiconductors and consumer electronics, to automotive and aerospace, to biotechnology and genomics, automated inspection facilitates safer, higher-quality products.
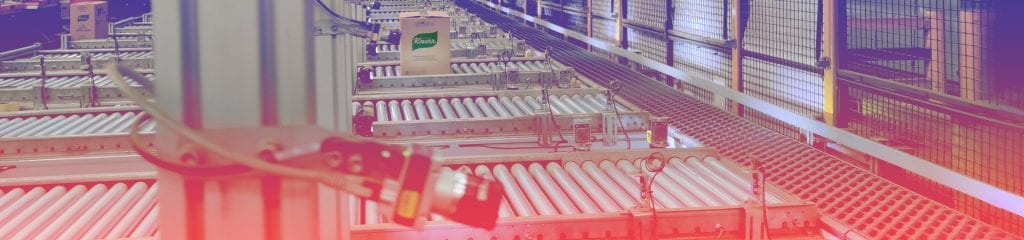
At the beginning of each packaging station, a camera reads barcodes on the boxes, which are used to classify the product type and assign it to the correct conveyor belt. Source: Courtesy of Teledyne
What are the Benefits of AOI?
Manufacturers often work with a systems integrator to develop a specific AOI system for their application, integrating the various components and training the manufacturer on how to best use the system. These AOI systems deliver many advantages for the companies that use them, including:
- Increased productivity – Automated inspection enables mass production, round the clock
- Constant availability – The systems can work 24 hours a day
- High Speed – They enable high inspection speeds and throughput
- Precision, Accuracy, Reliability, and Consistency – The systems can be programmed to identify precise detail, and they do so accurately and reliably at a constant and continuous pace
- Adaptability andProgrammability - They can adapt, quickly and easily, to various products and surfaces, and can be programmed and monitored remotely
- Long-term cost reduction – After the initial investment, AOI delivers long-term cost benefits
- Improved safety and working conditions – Automated inspection systems remove safety issues and tedious repetitive tasks for human inspectors, with the opportunity to let employees do higher-value work
- Superior product quality – Ultimately, the goal is higher-quality products that are safer, last longer, and do not break down
These benefits of AOI will be amplified as AI and deep learning are employed. With AI, the systems can continually “learn” over time by updating their training models with better datasets, resulting in performance improvements. AI software also enables more intuitive programming of inspection systems.
AI and Deep Learning Advance Inspection Further
AI and deep learning are the latest technologies that are advancing automated inspection. The combination of software, new deep learning techniques, the power of parallel processing, and ease-of-use tools are at the core of this transformation. AI is used to train machine vision systems to identify defects and anomalies.
Traditionally, image-processing software relied on task-specific algorithms that required hundreds, or even thousands, of high-quality, manually classified images to train the system. But today, deep learning software classifies a lower number of objects with a high degree of predictability. Additionally, with a well-trained AI vision system, software can quickly identify targets within an image with a high degree of variability that would normally result in many errors for a traditional machine vision system.
A newer deep learning technique for classification is called anomaly detection, where only good examples are used to train a network. In this case, the network recognizes what is considered normal and identifies anything outside that data set as abnormal. Anomaly detection tools enable the expansion of deep learning into new applications that could not take advantage of its benefits previously. The inclusion of anomaly detection helps to reduce the engineering efforts needed to train a system. If they have the data, even non-experts can train the systems, reducing costs significantly. Deep learning software has improved to the point that it can classify images better than any traditional algorithm. However, for very predictable inspection applications that do not expect much variability, it can be advantageous to use traditional vision algorithms to reduce the processing capacity on a system.
Inspecting Solar Panels, Packages of Tea, and Lithium-Ion Batteries
To exemplify how this works in the real world, here are three applications of automated inspection that demonstrate the wide array of inspection applications and the benefits achieved.
- In solar panel manufacturing, automated inspection is critical. Like many areas of electronics manufacturing, leading solar panel manufacturers have already moved to 100% automated inspection and the rest of the industry is working to catch up. Microcrack inspection is crucial because such faults can eventually cause an entire solar panel to shatter, causing damage to other panels and equipment, which then necessitates an expensive shutdown of the manufacturing line for cleanup and repairs.
- In their food packaging facilities in Istanbul, Kibele-PIMS has developed and commissioned two state-of-the-art, fully automated systems for the Unilever companies Knorr and Lipton, where cartons of both soup mixes and teas are identified, sorted, and then stacked on pallets by robots. Before switching to fully automated solutions, the food packages were manually sorted, which was a very exhausting task. In the new setup, the boxes arrive every 1.5 to 2 seconds, which has resulted in a significant increase in profitability and considerably fewer errors.
- Lithium-ion batteries (LIBs) are used in smartphones, tablets, power tools, and more commonly in electric vehicles, which are expected to account for most of the LIB demand. The failure of a battery system in almost any electric system poses multiple hazards, so automated inspection is essential. The best quality strategy is to start inspection as early in the production process as possible, so as not to waste time and resources on scrapping or recycling nearly finished products. Manufacturers are finding it important to look for these defects from the 50-micron level all the way down to 10 microns.
Automated inspection can take many forms and can show up in a wide variety of industries. For high-value products – such as semiconductors, lithium-ion batteries, and solar panels – AOI delivers a more immediate return on investment due to the cost of materials and the implications if a faulty component is not discovered. However, the benefits of AOI continue to drive fewer errors, higher overall quality, greater productivity, and increased profitability across many industries. With the integration of AI and deep learning, exciting new inspection techniques are expected to advance significantly in the coming years.