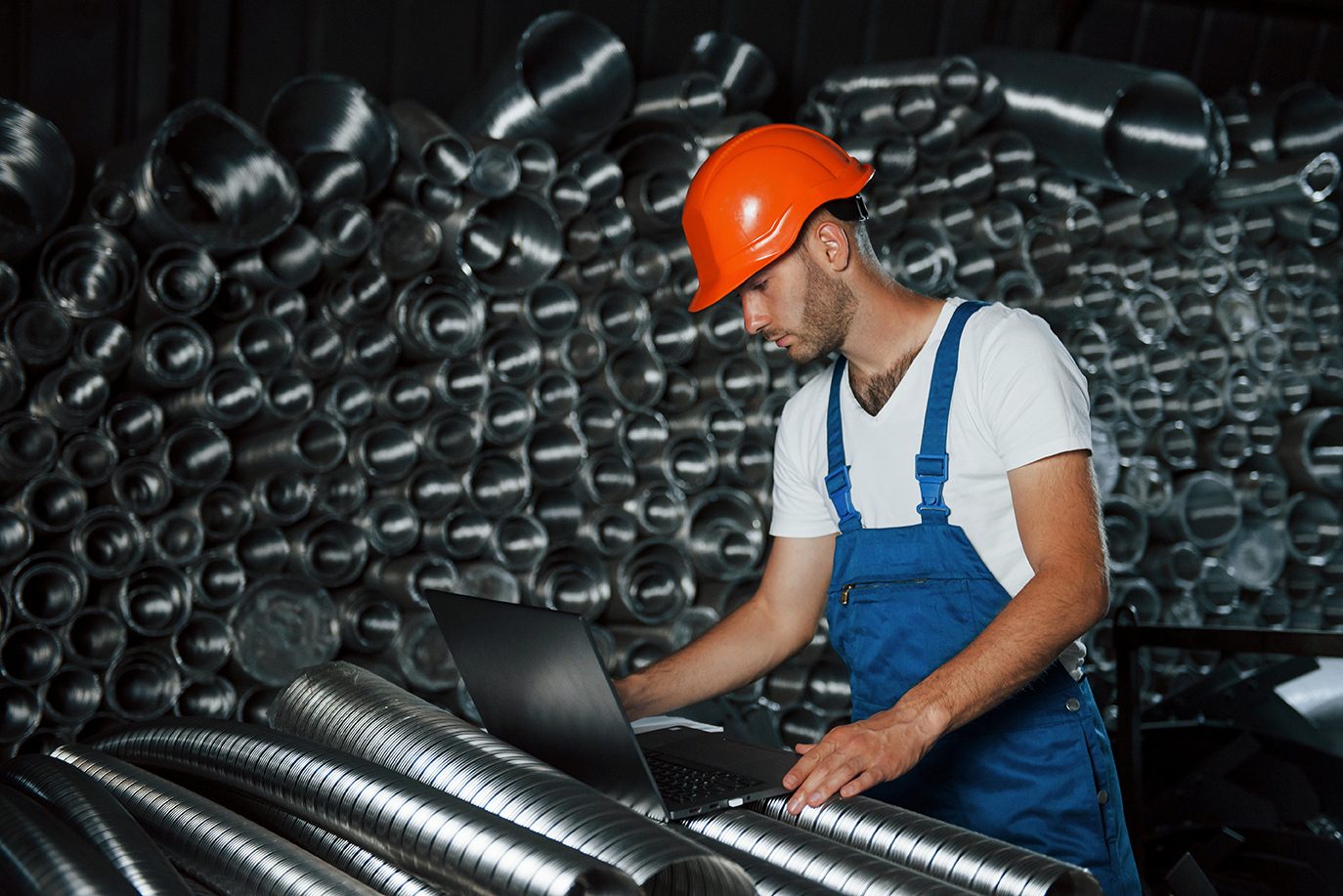
This Case Studies Special Advertising Section features manufacturing companies with real-world challenges using quality equipment, software and services to solve their problems and improve their processes. These problem-solving stories describe myriad manufacturing challenges and how the correct application of a supplier’s product or service made the difference, providing quantitative benefits to quality and manufacturing issues.
The suppliers in this special section present these real-world problems and solutions to help Quality Magazine subscribers who may have similar experiences.
Case Studies
— Special Advertising Section —
Nipro Gets the Whole Package with GAGEtrak®
Nipro Corporation was established in 1954 under the management philosophy of contributing to society through its business activities. Today, Nipro PharmaPackaging products are used on a global scale and lead the world market. The Nipro brand is highly regarded worldwide for its technological superiority and high quality.
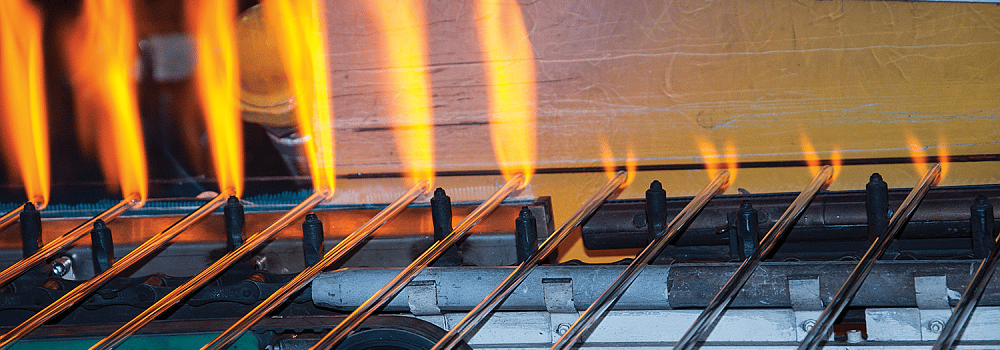
Diana Coblentz of the Westport, IN location reports that prior to GAGEtrak, the company used an Access program that was designed in-house. They later decided that a validated system was required to track their gage and calibration data, so they selected GAGEtrak, the world’s #1 calibration management software solution.
Since 2007, Coblentz has used GAGEtrak to manage the calibrations of approximately 250 gages and notes that she has configured the software to email her a list of calibrations due every day, which saves time and assures that no gage will be forgotten. Coblentz says that GAGEtrak is, “…efficient – covers all areas needed for calibration.” Coblentz also reports, “Our customers like this system better than what we had.”
The company has also taken advantage of GAGEtrak regional training and the calibration label kit to reduce the learning curve and improve efficiency even further. And about the CyberMetrics support team, Coblentz says, “Everyone I have worked with for support was very helpful and nice to work with. The support team does a great job.”
GAGEtrak is used at thousands of facilities worldwide to help quality programs thrive. Contact the GAGEtrak experts today to learn how GAGEtrak will do the same for your company.
Humanetics Optimizes its 3D Measurement Process and Becomes More Clever in the Face of Growth and Staff Changes
Discover how Humanetics uses a universal 3D measurement platform across multiple facilities and equipment for greater knowledge, efficiency, and flexibility in a period of tremendous growth.
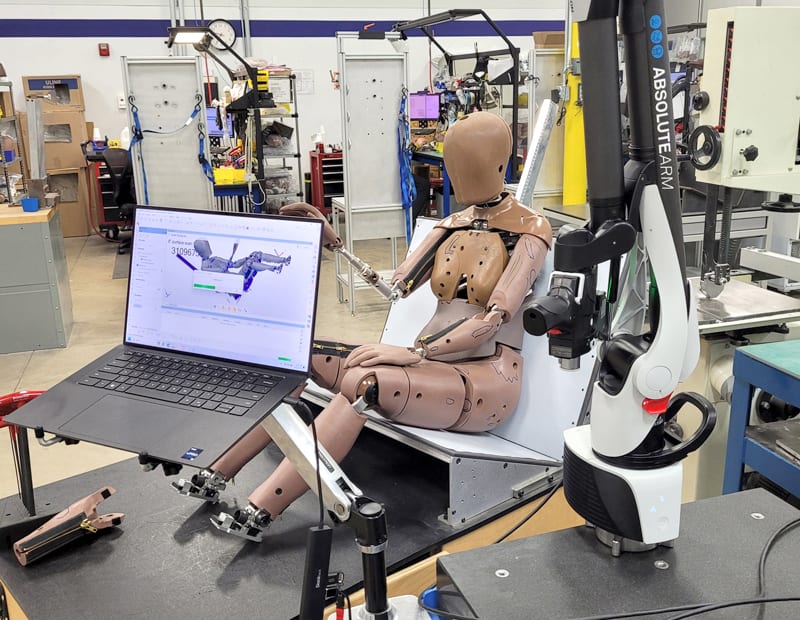
As the world leader in crash test dummies, Humanetics manufactures advanced anthropomorphic test devices equipped with cutting-edge sensors and bio-fidelity. Amid rapid expansion, their quality department faced challenges with tightening tolerances, time-consuming CMM programming, and inconsistent reporting across facilities.
To address these issues, Humanetics implemented PolyWorks|Inspector™, a universal 3D metrology software, transforming its inspection and reporting workflows. This innovative solution enabled consistent inspection workflows across devices, easy-to-master no-code CMM programming (76% faster, on average) and intuitive operation, even for new employees.
Humanetics is now well-positioned to meet the growing demand. Are you?
Manufacturer Saves Over $1,000,000/yr. With QI Macros
One aluminum manufacturer was having trouble with excess scrap. While there was significant, unavoidable startup scrap, other opportunities to reduce scrap became obvious after some analysis.
While many pounds of finished material was inspected and found wanting before shipment, roughly 40,000 pounds of finished metal was returned each month. Shipping and return costs ate into profitability. Finished metal cost about one dollar per pound. Returned metal had to be chopped up and fed back into the furnace for remanufacture.
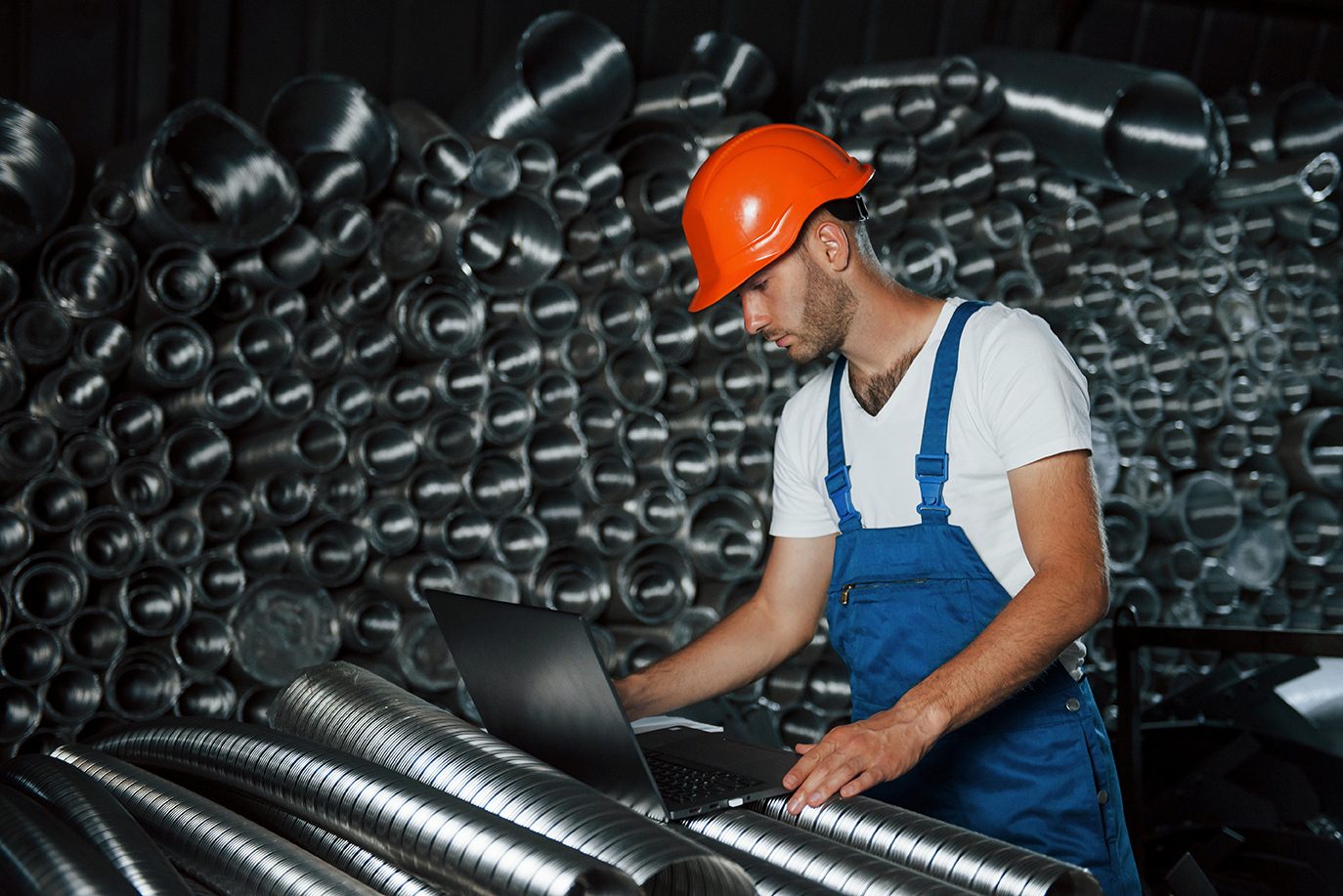
Using QI Macros for Excel, it was possible to use PivotTables to analyze and chart ongoing scrap. Control charts showed a stable process producing consistent levels of monthly scrap. Drilling down into the data, Pareto charts showed that one machine out of many was producing most of the scrap. A few hours of root cause analysis with operators of that machine identified simple ways to reduce scrap just by changing the setup and ongoing adjustment process.
Annual savings amounted to over $1,000,000 after only a few hours of analysis.
Million-dollar opportunities lay hidden in data about defects, mistakes, errors, scrap, waste and rework. Using Excel and QI Macros it is possible to mine and find those opportunities—the invisible low-hanging fruit in any company. QI Macros Improvement Project Wizard automates this analysis, creating improvement projects in just minutes.
This analysis works in manufacturing, healthcare, telephony, banking and any industry that tracks waste and rework. Haven’t you waited long enough to find your hidden, low-hanging fruit?
Company Name and Contact INfo
www.