Sensors
Sensors
Vision & Sensors
V&S
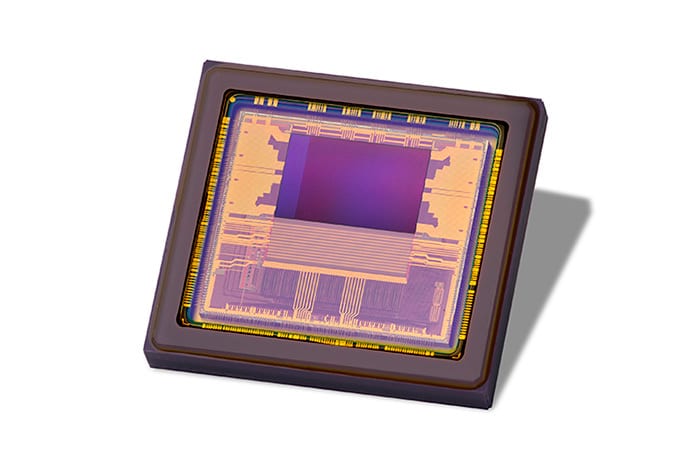
Manufacturers can rely on sophisticated sensors to revolutionize the way they do business, enabling enhanced quality control, improved efficiency, and increased safety. By Ha Lan DO THU
Unleashing Potential:
How Advances in 3D Vision Sensors are Transforming Manufacturing and Logistics
H2 Deck Info By Paragraph Style Bold
Headline
As 3D sensor technology advances, it is poised to shape new applications in areas such as manufacturing and logistics, enabling greater efficiency, productivity, and the ability to accurately scan fast-moving objects without motion artefacts.
The global 3D sensor market is projected to reach $57 billion by 2031, growing at a CAGR of 13% from 2022, according to Allied Market Research. The technology’s first commercial use was in the gaming field for 3D imaging and detection, and 3D depth-sensing technology in consumer devices has been increasing over the past decade driven by smartphone demand and the ability to unlock the phone using 3D facial recognition instead of a fingerprint or PIN.
Recently, applications requiring 3D depth-sensing technology have expanded to include manufacturing and logistics and augmented reality. 3D sensor technology brings benefits such as improved quality control, increased automation, enhanced safety, and optimized storage. For example, this technology can be employed in warehouses to maximize space and enable robotic pick and place.
This article will explore some of the latest advances in 3D sensor technology and give an overview of use cases in manufacturing and logistics.
How Industrial CMOS Image Sensors are Changing
New CMOS image sensors designed for 3D solutions are emerging onto the scene and represent a major step forward in industrial applications. For laser profilers, these sensors use state of the art global shutter pixel technology and sensor architecture to provide very high-speed sensors with high dynamic range in a rectangular sensor format to fit with the application constraints.
In the case of Indirect Time of Flight (iToF) systems, these sensors embed a brand-new pixel design to enable fast 3D detection without motion artefact and need to incorporate key features specific to the Time-of-Flight technique such as a powerful high dynamic range management to deal with wide distance range and wide reflectivity range. This enables iToF to be an ideal technique for reliable real-time decisions in complex conditions and changing environments. The demand for iToF devices continues to grow as the technology is being used in industries such as robotics, logistics, construction mapping, and intelligent transportation systems (ITS).
Increasing automation and monitoring, the use of robotics, and other aspects of Industry 4.0 initiatives are generating demand for 3D imaging solutions that offer high levels of precision and distance measurement in a variety of challenging conditions.
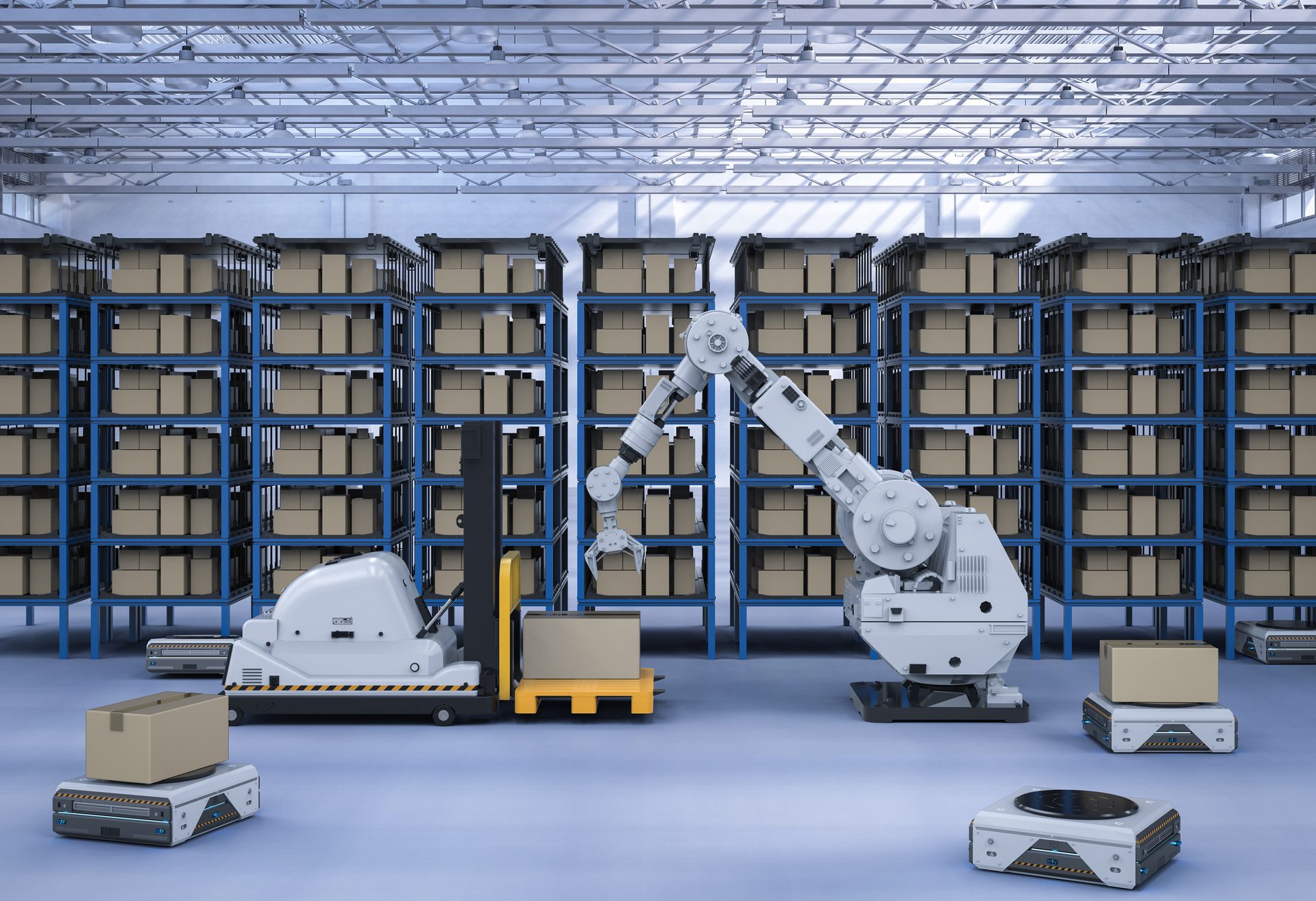
AdCreative Missing.
(double-click to add)
New Applications for 3D Sensors in Industry 4.0
As defined by McKinsey & Company, Industry 4.0 is the next phase in the digitization of the manufacturing sector, driven by disruptive trends including the rise of data and connectivity, analytics, human-machine interaction, and improvements in robotics.
The arrival of the Industry 4.0 has increased demand for 3D vision due to the limitations of 2D vision around precision and distance measurement for complex object recognition and dimensioning. In addition, 3D imaging supports the interactions between humans and robots. With 3D vision, factory workers are protected from potentially dangerous situations on the manufacturing floor with 3D surveillance systems that can distinguish people from robots and other objects to create a safer environment.
3D vision improves the autonomy and effectiveness of factory automation robots and machine systems and is essential for more accurate quality inspection, reverse engineering, and object dimensioning. Furthermore, the use of vision system-assisted robotics is increasing, necessitating 3D vision for better remote guidance, obstacle recognition, and accurate movement.
Two specific use cases of in-motion dimensioning in factories and warehouses include large freight or cargo dimensioning and high-speed parcel or package dimensioning which will be explored further.
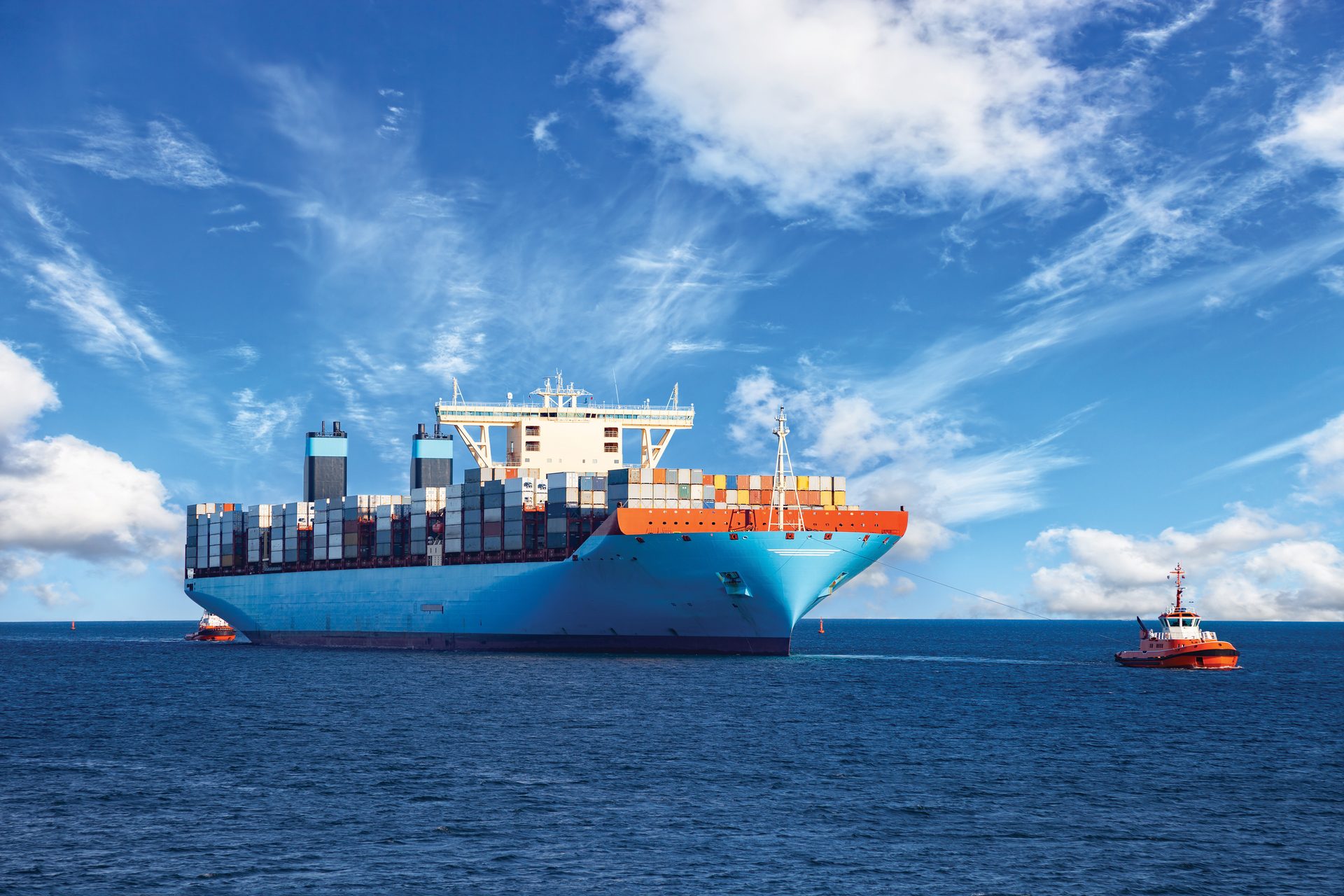
Large freight or cargo dimensioning
In-motion dimensioning involves the process of capturing and measuring the dimensions of objects or packages while they are on a conveyor belt or moving platform. This technology is commonly used in logistics, warehousing, and shipping industries to automate the dimensioning process and improve efficiency. 3D vision-based systems can precisely measure the length, width, and height of objects as they pass through the system – reducing the need for manual measurements or estimations.
The industrial application of 3D sensor technology for large freight/pallet dimensioning offers significant advantages over static stations. With real-time dimensioning capabilities, higher efficiency can be realized. Efficient palletization, including packing and truckload optimization, can be achieved through the utilization of this technology. With advanced on-chip features at the sensor level, 3D systems can seamlessly work together without any interference in both indoor and outdoor settings, while maintaining good performance levels. With a high-resolution offering, these 3D sensors enable a large field of view and an excellent angular resolution to get complete coverage of the entire pallet, exceeding one meter in size. By eliminating motion artefacts, real-time and reliable measurements are obtained, leading to time and cost savings, and ultimately enhancing productivity. Furthermore, advanced 3D sensors can handle a wide range of reflectivity coverage, so that even for materials with very low reflectivity, like black rubber, a consistent precision level can be maintained.
The captured dimensional data from these systems can be used for several purposes, including freight and shipping optimization, warehouse space management, automated sorting, and compliance and documentation to meet regulations such as safety standards or transportation regulations.
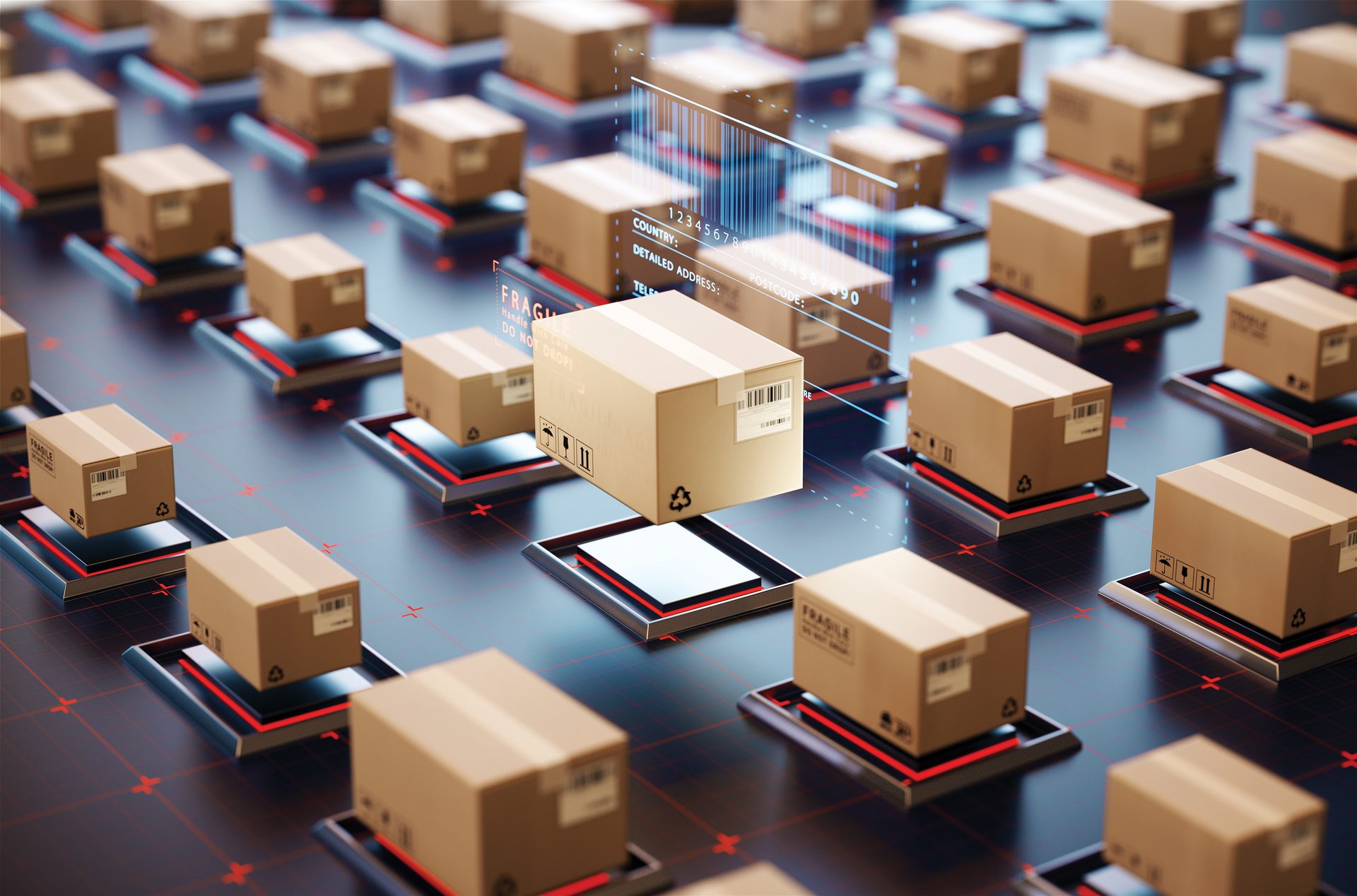
High-Speed Parcel/Package Dimensioning
High-speed parcel or package dimensioning is another use case and refers to the process of quickly and accurately measuring the dimensions of parcels or packages in a high-speed automated manner. Advanced 3D sensors are part of the specialized dimensioning systems used to capture the length, width, and height of the packages, as well as other relevant parameters. The high-speed aspect of this use case is crucial in environments where large volumes of packages need to be processed rapidly. By automating the dimensioning process, it reduces the need for manual measurements, which can be time-consuming and prone to errors. This technology enables faster throughput, improves operational efficiency, and facilitates accurate pricing, sorting, and logistics planning.
For industrial applications, 3D sensor technology offers innovative solutions for high-speed dimensioning of packages. Innovative 3D sensor technology surpasses static stations by enabling real-time dimensioning, resulting in significantly higher efficiency. Besides the need to comply with high-speed production lines, these solutions cope with a short and scalable range detection, precisely measuring distances from two to four meters, for example, with millimeter-level accuracy. Even when faced with conveyors operating at extreme speeds exceeding 30 frames per second, these sophisticated sensors get rid of motion artefacts. Additionally, they boast extensive reflectivity coverage, accommodating various surfaces, including materials with low reflectivity, while consistently maintaining a stable and excellent level of precision throughout the entire detection range.
High-speed parcel or package dimensioning systems are commonly employed in various industries, including e-commerce, retail, courier services, distribution centers, and logistics hubs. They are often integrated into conveyor systems or material handling equipment, allowing packages to be dimensioned as they move along the processing line. Overall, high-speed parcel/package dimensioning plays a vital role in optimizing logistics operations, ensuring accurate shipment calculations, and enabling efficient management of the entire supply chain.
10 Attributes to Consider for 3D Systems
When considering 3D systems for industrial applications, several key application parameters should be taken into account. Here are some important factors to consider:
- Distance range: The distance range of the use case to be covered by the 3D systems. For instance, Autonomous Guided Vehicles (AGV) and Autonomous Mobile Robots (AMR) applications typically require 3D techniques to perform at longer ranges to detect obstacles and navigate effectively in various industrial settings, whereas bin picking requires only a short distance range.
- Precision: Depending on the precision required by the application, one 3D technique will be more suitable than another, and then, a 3D sensor technology will characterize the level of precision that could be achieved.
- Resolution: The level of detail captured in the scene or the size of the object to be measured will determine the 3D sensor resolution.
- Field of View (FoV): The field of view will have an impact on the 3D sensor resolution to be selected and on the 3D system design.
- Speed: Fast 3D detection needs to happen without motion artefacts to avoid false distance measurements. Not all 3D techniques deliver a 3D measurement at a reasonable speed or can cope with high-speed moving objects.
- Reflectivity: What is the minimum and maximum reflectivity that your 3D system needs to handle? In industrial applications, the reflectivity range to cover could be wide from 2% to 98%, for instance, and the 3D systems should provide good enough precision at the extreme limits of the range and a stable level needs to be maintained.
- Outdoor operation: In some applications, the 3D system needs to operate both indoors and outdoors, and the chosen 3D technique should be robust to the ambient light while maintaining a good level of performance.
- Adaptability to various scenarios: Not all 3D techniques are suitable to work in multiple and changing operating conditions (light, range, indoor/outdoor, precision….) and particularly if this needs to happen frame-to-frame.
- Ease of integration and operation: What would be the effort to integrate the 3D system into the final system? What would be the calibration and manufacturing effort? Does the 3D system need a specific setup to operate properly in the factory or warehouse? All the questions need to be considered and will have a direct impact on your cost.
- Cost: Evaluate the cost-to-performance ratio of the 3D technique, considering the specific needs of the application.
All these factors should not be considered individually as many dependencies exist between them and they must be assessed altogether in the selection of a 3D technique, a 3D system, or a 3D sensor.
Conclusion
As advances in 3D sensor technology progress, customers in manufacturing and logistics can rely on sophisticated sensors to revolutionize the way they do business, enabling enhanced quality control, improved efficiency, and increased safety. Applications such as large freight dimensioning and high-speed package and parcel dimensioning enable precise measurements and optimization of warehouse space leading to enhanced quality control, reduced costs, reduced waste, increased safety, and overall improved operational efficiency.