H2 Deck By Bold Name
h2 xxxxxx
H1 xxxxxx
h2 xxxxx
Test & INspection
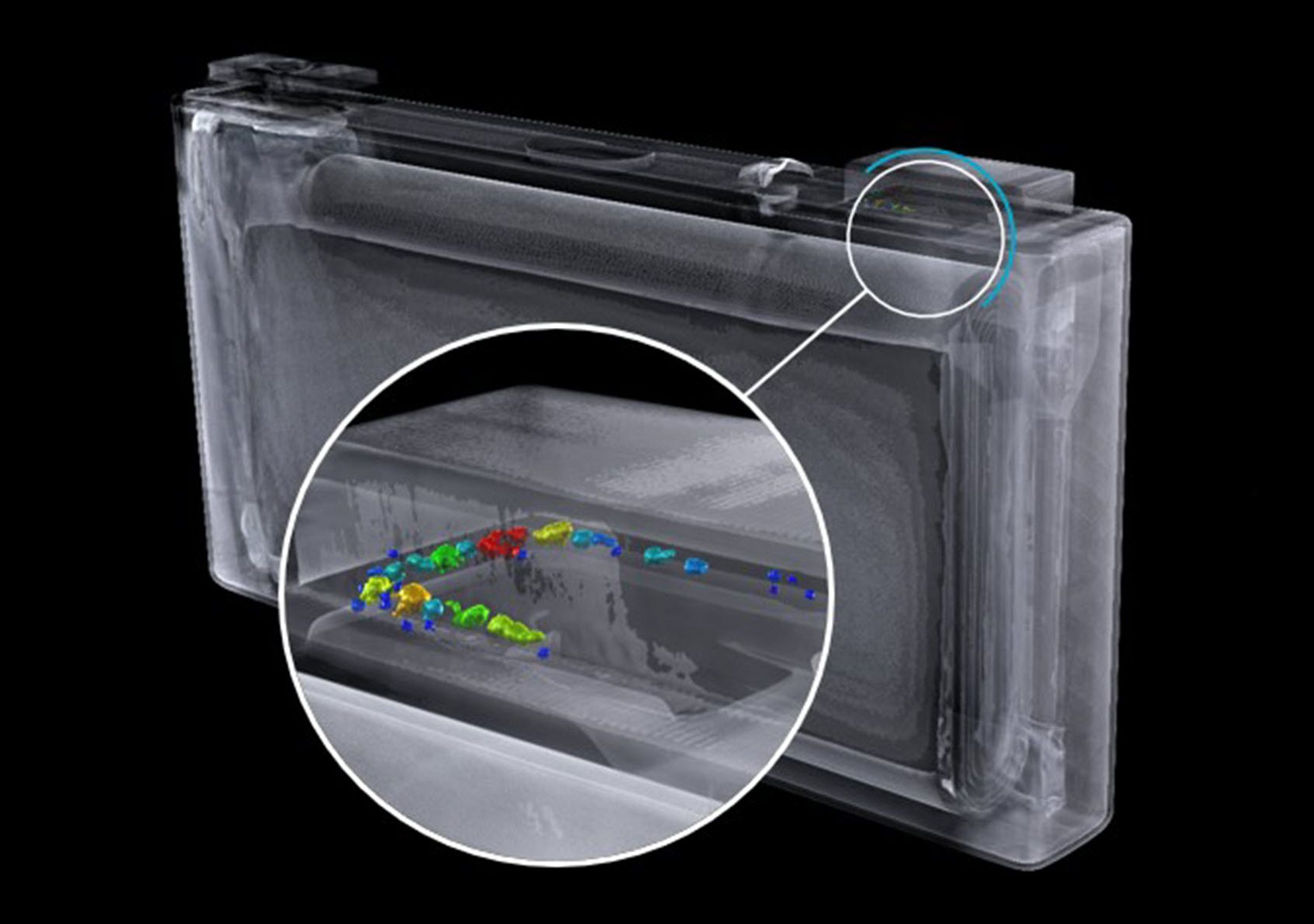
Higher volumes of new batteries and faster turnaround of recycled materials from those batteries—along with testing of used and repurposed ones—demand the most efficient quality-inspection approaches possible. By Dr. Daniela Handl
How CT Quality Analysis
of EV Batteries Can Help Address Demand and Performance
Test & INspection
H2 Deck Info By Paragraph Style Bold
Headline
There are two market forces at work in the electric vehicle (EV) segment that foreshadow the greater use of Computed Tomography (CT) for quality inspection: the need to address the significant demand for EV batteries via improved yields with faster, scaled production; and the related need for consumer confidence in the reliability and improved performance of those batteries.
EVs are forecast to reach 45 to 58 percent of all vehicles made by 2030. In a 2022 analysis, the McKinsey Battery Insights team projected that the “entire lithium-ion (Li-ion) battery chain, from mining through recycling, could grow by over 30 percent annually from 2022 to 2030.”
But will the production quality of these batteries improve or decline with higher vehicle volumes?
The scaling up of battery production to meet anticipated demand presents huge challenges to existing facilities. Because the battery is the most expensive component in today’s EVs, the entire end-to-end process of making batteries must be as efficient and as environmentally sustainable as possible to lower costs and win over consumers and regulators.
What’s more, while the current generation of EV batteries is largely still on the road, the used-car EV market is growing. Reuse of EV batteries in secondary markets for home and business energy storage is also on the rise. Repurposing is one pathway to optimizing battery supply-chain investments, total costs, and use of rare minerals.
Higher volumes of new batteries and faster turnaround of recycled materials from those batteries—along with testing of used and repurposed ones—demand the most efficient quality-inspection approaches possible.
CT analysis for better and faster battery development
The process of making batteries is complex. The manufacturing, chemistry, and inspection required is true science—and a finished battery is a closed system that doesn’t lend itself to open inspection via destructive testing methods that inevitably make it unusable.
To ensure that the manufacturing and mechanical/chemical aspects of battery development are the best they can be, research and development teams, manufacturers, test engineers (and even EV OEMs who want to inspect outsourced batteries) are turning to industrial CT scanning, followed by data analysis with software programs, specifically created for battery inspection, that even non-experts can employ to support quality-control efforts.
While X-rays, ultrasonic testing for electrolytes, and/or visual checks can serve certain applications, industrial CT scanning analysis software provides deep insights that can inform almost every discipline in the battery creation stream. This includes R&D, design, simulation, assembly-stage inspection, final production inspection, and forensic/root-cause efforts that aid in understanding accidents and failures, or re-certifying used batteries for other uses.
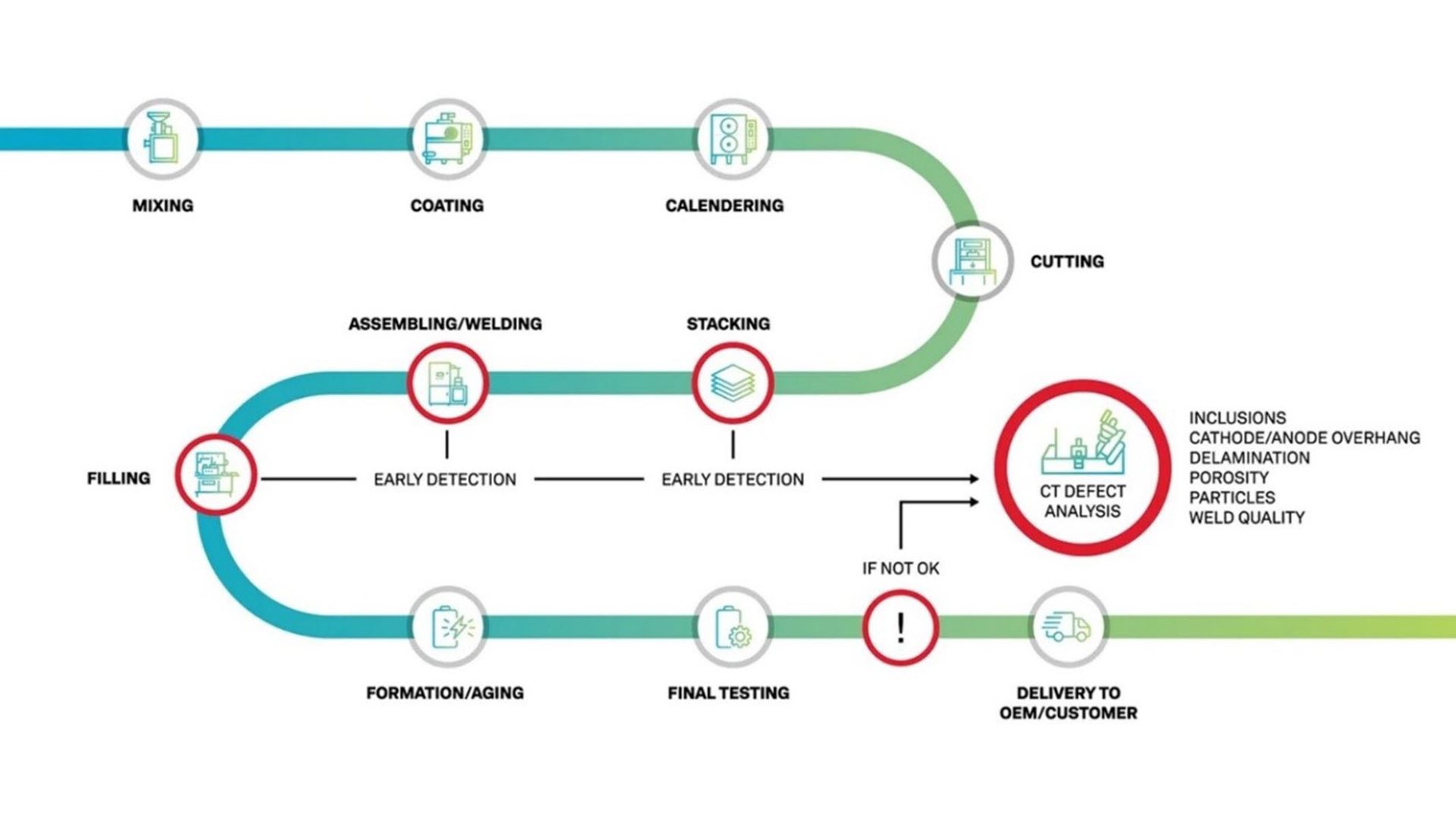
CT scanning captures 3D images of battery components at critical production stages, for early detection of quality defects that can arise during stacking, assembly, welding, and/or filling. Advanced inspection software processes this image data into holistic, accurate visualizations and analyses of any anomalies. In addition, it can provide critical feedback for designers and engineers to incorporate as they model, refine, and optimize geometries, materials, and processes. This saves valuable time, resources, and ensures that the final product is of the highest possible quality. Image courtesy of Volume Graphics, a Hexagon company.
Such end-to-end use of CT scanning software across the battery enterprise will help the industry realize a future of efficient, scaled-up battery production.
Battery developers can benefit from closed-loop digital CT inspection in the following ways:
- Improved upfront R&D knowledge and innovation/validation test loops
- Superior design-to-simulation-to-manufacturing optimization feedback cycles
- More detailed materials and structural inspection during specific phases of assembly; inline measurements, captured via CT scans, should ideally be made at every critical stage of the battery-making process
- Higher-speed final inspection via AI/Deep Learning analysis solutions and inline systems
- Better insights into end-use markets and durability based on battery data returned to design teams so the end-to-end process can be optimized for better quality
Such test and collaboration capabilities are at the heart of the digital enterprise. Each discipline is improved by validating earlier steps against a scanned, digital interior inspection. Simulations, for example, are validated by what the scans reveal after manufacturing. Data on post-manufacturing porosity and structural defects can enrich the simulation model, which in turn cuts time and improves the master CAD model and various digital twins.
The result is fewer or no failure points—and improved yields—critical to meeting demand and cost targets. Volume can also increase because the overall process is streamlined, transparent, predictable, and avoids stoppages.
Battery-related quality issues that impact production and costs
Here are some examples of battery-related quality issues that can be detected and categorized, using CT-scan-data-analysis software.

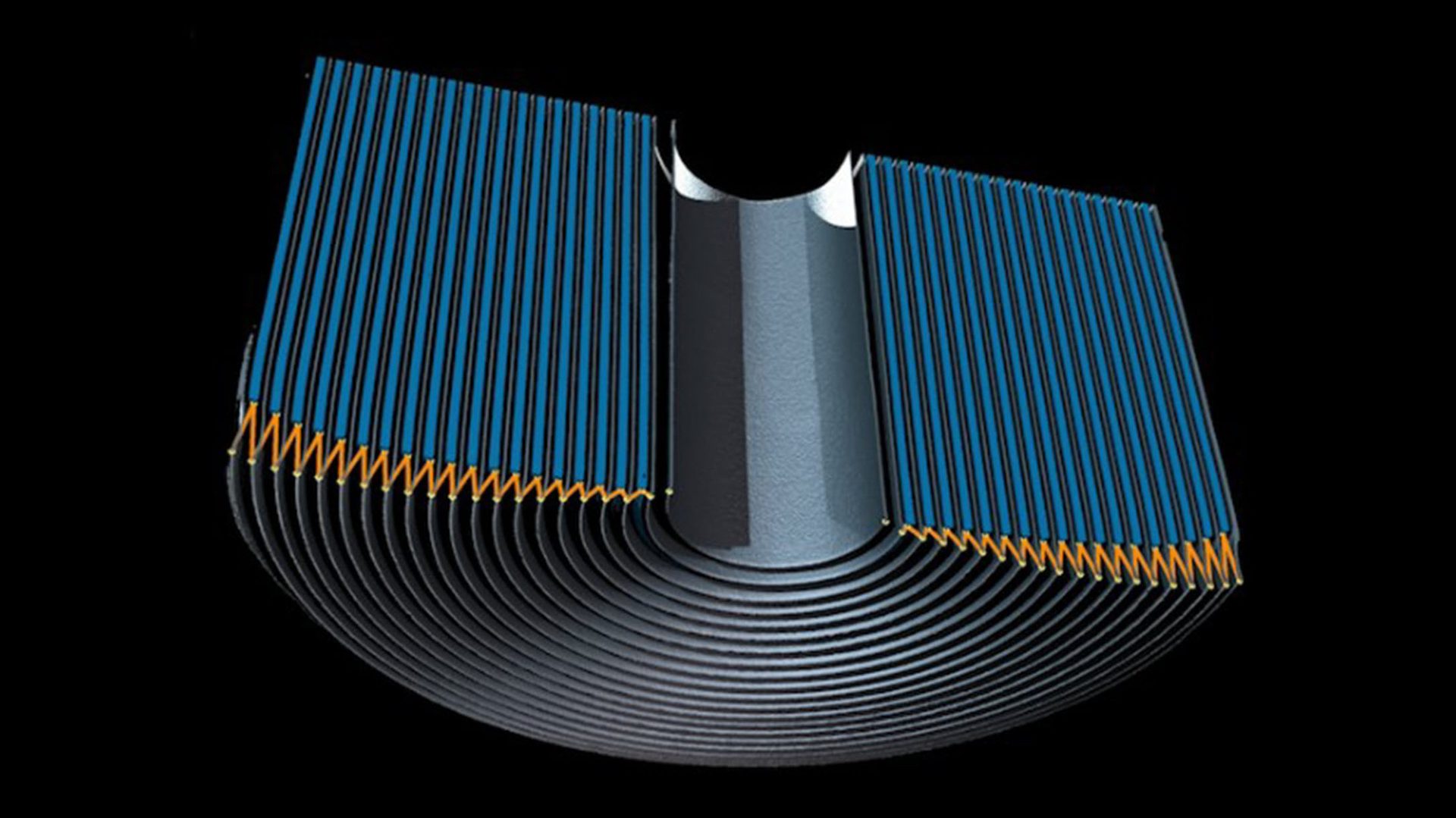
Two views of battery anode overhang analysis. Left shows the anode overhang in a 2D slice where the anodes are coded by color with respect to their corresponding anode overhang. Right is a 3D representation of the jellyroll to get an overview of the dataset e.g. to judge the segmentation quality. Image courtesy of Volume Graphics/Hexagon
The anode overhang in lithium-ion batteries is a crucial safety criterion. Advanced inspection software helps manufacturers and researchers measure and design anode overhangs that balance electrode utilization, current distribution, cycling stability, and safety considerations. Carefully controlling and optimizing the overhang improves a battery’s efficiency, capacity, stability, and overall performance.
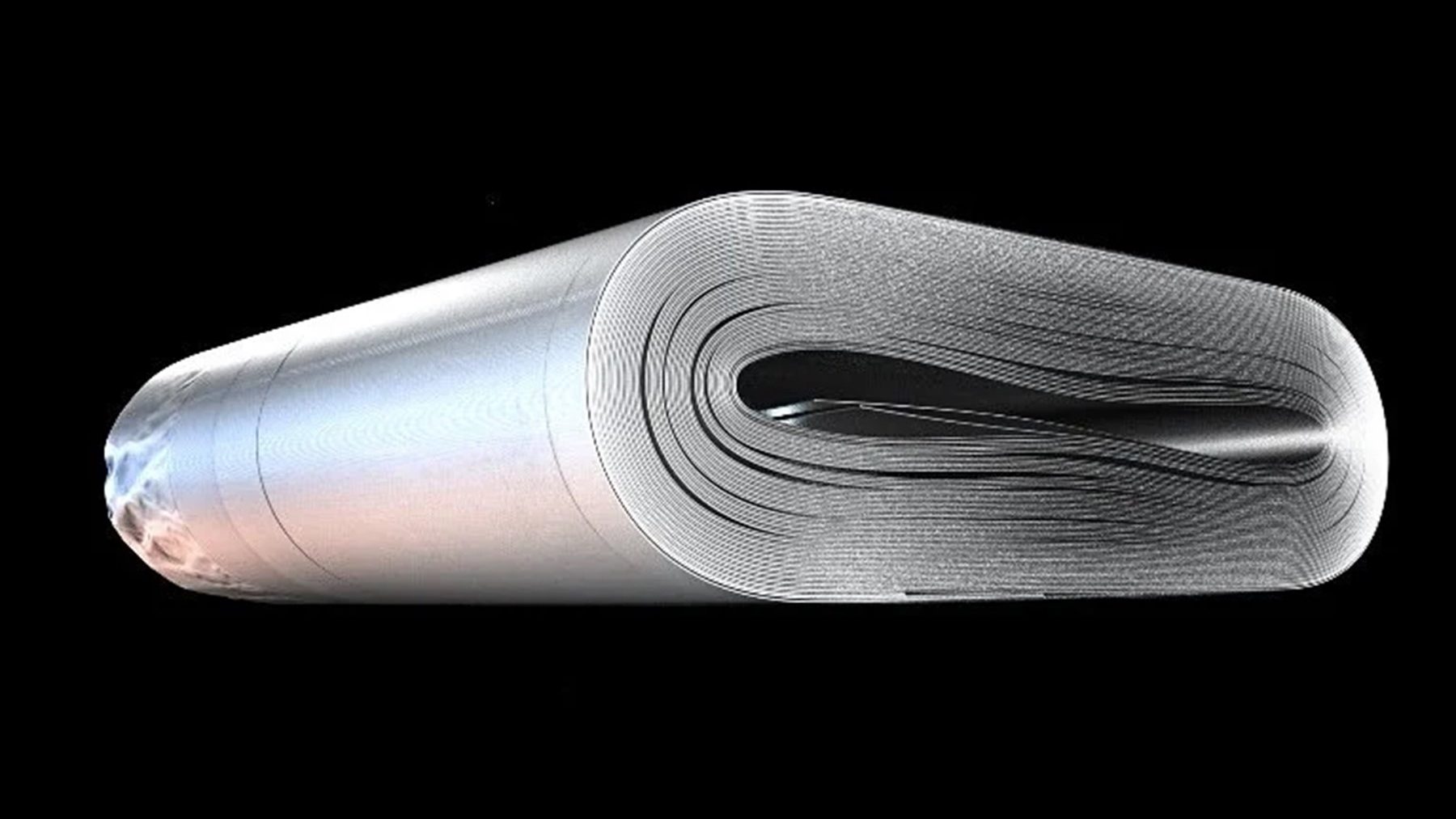
Delamination in a wound battery. Scan courtesy of Waygate Technologies
Delamination reduces the capacity and lifetime of the cell. Inspection software can detect and visualize delamination not only during manufacturing, but also in later maintenance if delamination occurs after multiple charging cycles.
Any time the active material in a battery becomes separated from the current collector, be it during manufacturing or over time, it affects electrical output. Ripples in the metal sheeting can develop—more prevalent with wound batteries than stacked ones—creating undulations that can affect anode and cathode alignment, impacting performance and lifespan.
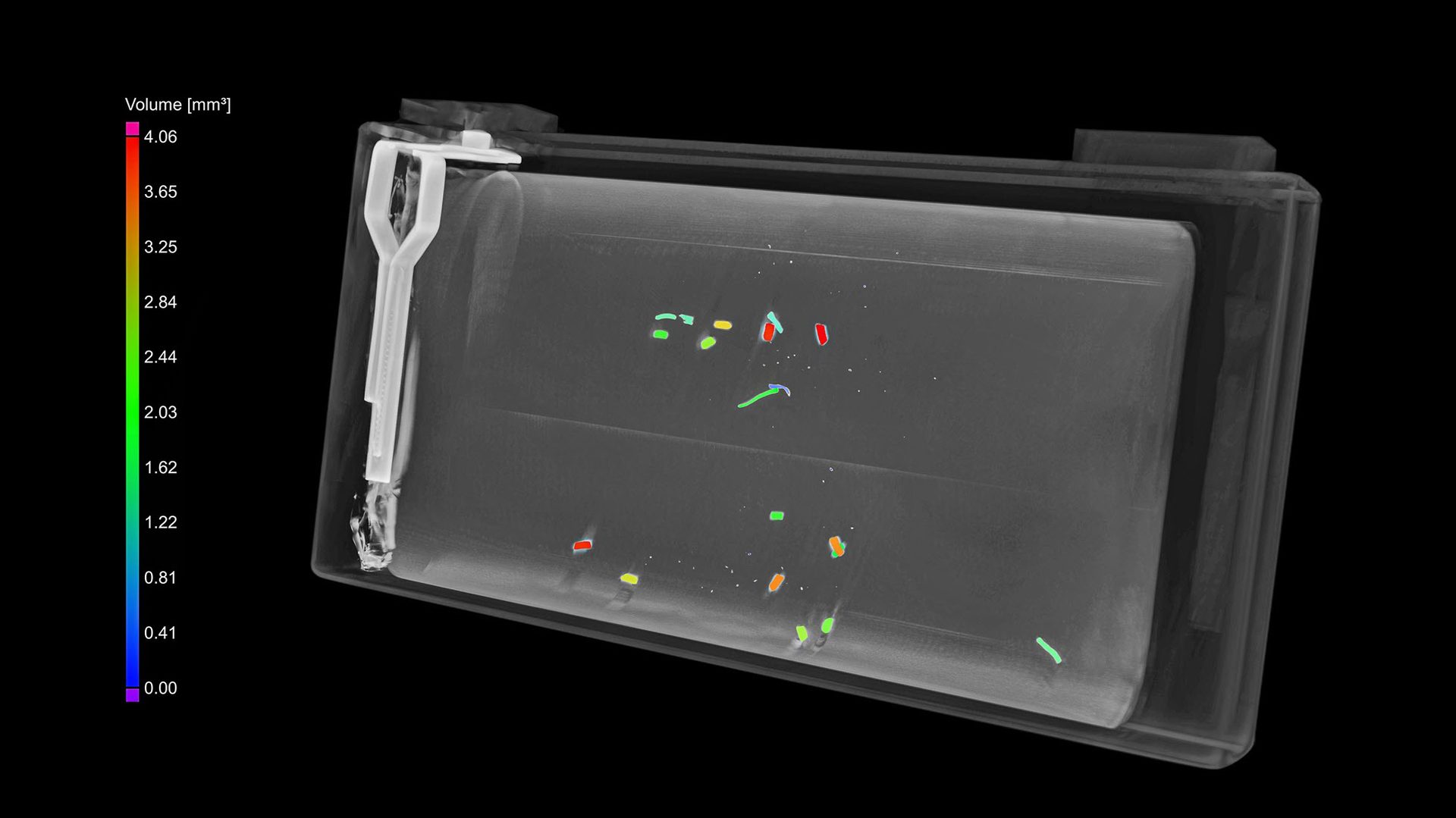
Analysis of particles in the jellyroll of a battery in VGSTUDIO MAX. The software classifies the shapes and sizes of these tiny, foreign inclusions and, based on customized criteria, calls them out by highlighting them in colours that indicate size. Scan courtesy of Waygate Technologies
Foreign particles can make their way into a battery at several stages of production. Porosity inclusion analysis allows engineers to detect these in the CT-scan data and quantify their size and location to help determine whether they are critical.
Unwanted particles can be a side-effect of welding, resulting from flying hot metal as it cools. Particles can also occur when anodes and/or cathodes are cut from sheets of aluminium or copper. When a CT scan captures flakes, analysis software calls out their irregular shapes and anomalies to support decisions about potential battery quality.
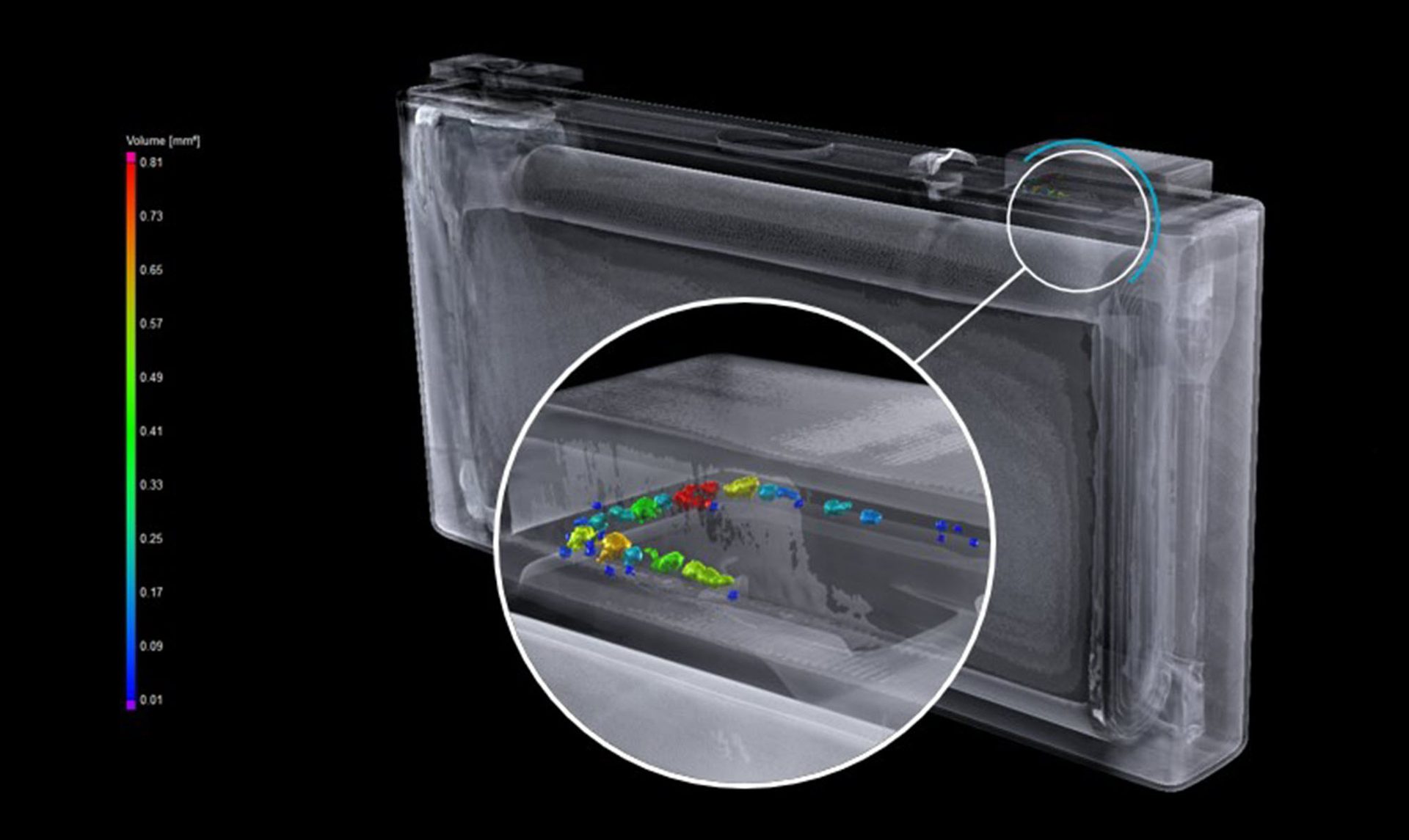
Porosity detection in the weld seam of a battery; the size of individual pores is indicated by color.Image courtesy of Volume Graphics, a Hexagon company. Scan courtesy of Waygate Technologies.
During prismatic cell production, porosity caused by welding battery-casing components together may cause dangerous leaks and reduce battery function. Weld-seam porosity is almost impossible to avoid completely, but it can be reduced through post-analysis weld-parameter optimization.
Porosity inclusion analysis helps quality engineers decide whether a particular pore is a reason for concern; manufacturers can leverage this analysis to ensure the integrity and optimal performance of their batteries.
Quality checks for the second-life market
As demand for used EVs grows, safety and reliability become even more paramount to determining a battery’s suitability for second-life applications.
Defects that can arise over time, such as delamination, threaten the internal structure and integrity of any battery long after it leaves the production line. Software analysis can support CT-scan inspections of aging batteries. These support systems help engineers identify and characterize various defects and learn more about a particular battery’s active materials, electrode thickness, and overall cell uniformity.
The approach also promotes sustainability by extending the lifecycle of batteries, reducing waste, and maximizing the battery’s value across any industry that depends on them.
Harnessing deep learning and AI to build a better battery
In today’s manufacturing world, huge quantities of design and engineering data are captured, classified, and analysed—increasingly aided by automation—to gain insights into the quality of products, as well as how production-parameter variations might be affecting outcomes.
The AI and deep-learning capabilities currently being developed in CT-scan data analysis software will be key to reaching the highest levels of accuracy, speed, and automation in battery inspection. These emerging approaches are already being used by certain leading manufacturers to overcome some of the most complex and challenging aspects of inspection. The results promise greater yields, scalability, and production output via both inline and at-line systems.
By providing real-time insights into the stability of the entire production process, CT analysis capabilities help engineers make informed decisions and take necessary actions to ensure the continued quality and efficiency of the entire battery production enterprise. More widespread adoption of the technology should go a long way to nullifying the uncertainties of meeting high future demand for EV vehicles and their power sources.
Opening Image courtesy of Volume Graphics, a Hexagon company. Scan courtesy of Waygate Technologies.
Dr. Daniela Handl, general manager, Volume Graphics, Hexagon. For more information, call Volume Graphics GmbH at +49 6221 73920 60, fax +49 6221 73920 88, or email press@volumegraphics.com.
READ MORE: