paragraph style text goes here
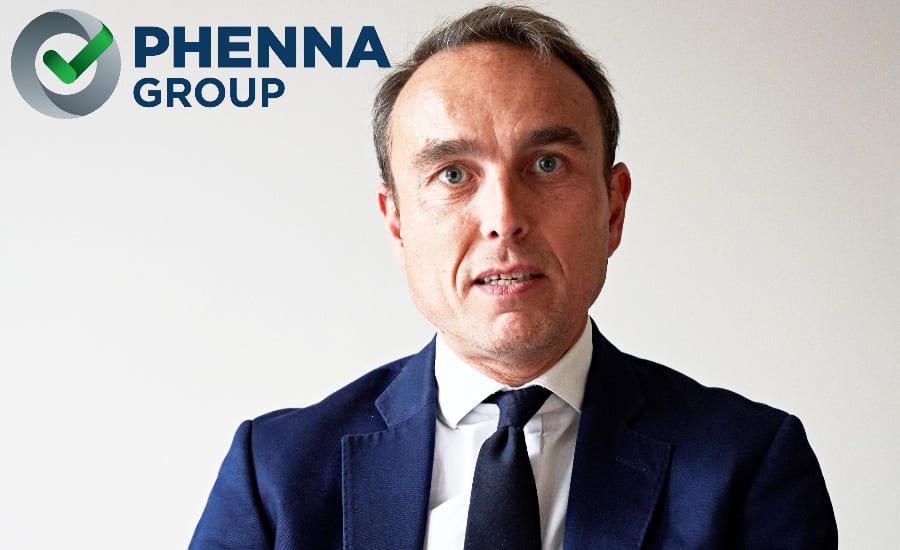
H1 headline goes here
Phenna Group Appoints New Group Head of Corporate Development
Phenna Group, a global testing, inspection, certification, and compliance services provider, has appointed Jon Harrison as the Group Head of Corporate Development.
Jon brings a wealth of experience to his new role at Phenna Group. He joins from the Global Investment Bank, Houlihan Lokey (HL), where he successfully built and led HL’s sector-leading European Business Services practice for the last six years.
Jon started his career in accountancy with Price Waterhouse in 1994 and transitioned to Investment Banking in 1997. He spent most of his banking career, focused on M&A in the Business Services sector for global players such as HSBC/Samuel Montagu, Deutsche Bank, and Robert W. Baird. His experience spans many sectors, although his specialization is in testing, inspection, certification, and compliance (TICC), where he has become one of the pre-eminent global advisers in the sector.
Based in London, UK, Jon has advised clients across the globe and is particularly well networked on the international TICC scene through his deal activity, as well as through organizing and participating in numerous industry events. He is also an active participant in various industry associations.
Phil Marshall, Phenna Group CEO, commented on Jon’s appointment: “Jon is very well known and respected across the global TICC market, and I’m delighted to attract someone of his experience to our team. He will support the growth of our business globally, driving and accelerating our M&A plans, a fundamental tenet of our strategy”.
In response to his appointment, Jon expressed his excitement by saying, “I’m delighted to embark on this new role with Phenna Group which will allow me to make the most of my deep knowledge and contacts within the TICC sector as well as my corporate finance experience while also giving me the opportunity to work with the team to grow the business with a particular focus on global M&A. I have already enjoyed working with many of the Phenna team over the past few years and am really looking forward to both deepening those connections as well as building new ones as our corporate development team grows. I can’t wait to get started”.
With this latest appointment, Phenna Group reaffirms its commitment to excellence and innovation, poised to continue its trajectory of growth with Jon playing a pivotal part in its M&A strategy.
For more information, visit https://phennagroup.com/.
Education: Technical University of Applied Sciences Würzburg-Schweinfurt Relies on MVTec HALCON for Academic Training
At Technical University of Applied Sciences Würzburg-Schweinfurt (THWS), Professor Christian Zirkelbach is teaching robotics and machine vision at Faculty of Applied Natural Sciences and Humanities. He has integrated advanced machine vision tools into its robotics curriculum, leveraging MVTec HALCON software since 2019. We’ve talked with him about the most recent project in robotics education.
Q: How did you come to incorporate MVTec software in your teaching and research?
Zirkelbach: Our faculty has adopted state-of-the-art technology to advance its educational and research initiatives. The institution began its journey with MVTec HALCON in 2019, marking a pivotal step in incorporating the sophisticated machine vision tool into our curriculum.
HALCON supports a wide array of cameras and offers numerous algorithms for understanding 3D images. That’s the reason why we’ve chosen HALCON for our educational and researching purposes.
Q: What use case for machine vision software do you have within your project?
Zirkelbach: One of THWS's standout projects features a 7-axis MRK robot, the KUKA iiwa, programmed to play chess on a physical board with the aid of stereo cameras and HALCON. This project highlights the practical application of machine vision in robotics.
In this endeavor, HALCON's robust capabilities were employed for various tasks such as identification, robot vision, and position recognition. Techniques like matching, classification, and blob analysis were utilized to enable the robot to understand and interact with its environment, effectively giving it "eyes" to navigate and make decisions.
Q: What impact does the integration of MVTec HALCON have on education and research at THWS?
Zirkelbach: Integrating MVTec HALCON into the THWS curriculum has yielded numerous benefits. It has not only added practical relevance to our lectures but also spurred the development of innovative research projects. The ability to give a robot eye to understand and interact with its environment has been invaluable. Feedback from students and the research team has been overwhelmingly positive, highlighting the enhancement in learning and research capabilities.
The project's success was further validated when Bavarian Prime Minister Markus Söder visited the installation. An event that garnered media attention and underscored the institution's commitment to technological advancement.
Q: What makes the student-driven masterpiece at THWS using MVTec HALCON stand out?
Zirkelbach: This groundbreaking work was realized through a master's thesis project by a dedicated student, emphasizing the hands-on learning approach promoted at THWS. The MVTec on Campus program has proven to be instrumental in providing students with the tools and knowledge necessary to excel in machine vision and robotics.
Through the utilization of HALCON, Technical University of Applied Sciences Würzburg-Schweinfurt continues to push the boundaries of robotics and machine vision, preparing the next generation of engineers and researchers to lead technological innovation.
Q: Which advantages result from the participation in the MVTec on Campus program?
Zirkelbach: Integrating MVTec HALCON into our robotics curriculum has significantly enhanced our educational and research capabilities, exemplified by projects like the chess-playing robot.
Moreover, our students are getting effectively prepared to be leaders in the fields of robotics and machine vision by hands-on learning.
For more information, visit www.mvtec.com.
Beamex US Office to Move to New Location in Atlanta, GA
Beamex announced the relocation of its U.S. operations, including its state-of-the-art calibration laboratory and warehouse, to a new, expanded facility in Atlanta, GA. This move is a significant milestone for Beamex, as it underscores their commitment to enhancing services and capabilities in the United States.
The new Atlanta location, boasting over 11,000 square feet of space, with an expanded laboratory and warehouse of more than 3,000 square feet, provides the room necessary for Beamex to continue expanding services. The new calibration laboratory will offer advanced facilities, including capabilities for pressure, electrical, and temperature calibrations. This upgrade ensures that Beamex can better serve its customers who rely on Beamex for high-quality recalibration and repair services.
With increased space, environmental control, and an optimized layout, the new calibration laboratory is designed to improve turnaround times and support the goal of achieving ISO 17025 accreditation for Beamex in the United States. These enhancements will enable Beamex to expand its service offerings and maintain the highest standards of calibration excellence.
In addition to the upgraded laboratory, the new office space includes additional meeting rooms and co-working areas. This allows Beamex to operate more efficiently and provides a welcoming environment for customers to meet with its team of calibration experts.
"We are thrilled to share this exciting news with our valued customers and partners," said Jukka Syrjä, Beamex Operations Director. "Our new location in Atlanta is a testament to our dedication to providing exceptional calibration services and support. We look forward to continuing our partnership with our customers and delivering the best possible solutions from our new, enhanced facility."
For more information, visit www.beamex.com.
ASME Announces Four Leadership Promotions to Advance Strategic Plan
The American Society of Mechanical Engineers (ASME) has announced several promotions on its leadership team. Keith Bloesch has been named ASME’s chief information officer (CIO), effective immediately, and Anand Sethupathy will become the Society’s chief strategy officer (CSO) following the retirement of Michael Johnson on September 30. Stephanie Viola has accepted expanded responsibilities as managing director of programs and philanthropy and executive director of the ASME Foundation, and Iana Aranda has been promoted to the newly created position of managing director of sustainability.
“These four outstanding leaders have built strong connections with ASME’s supporters, board members, key volunteers, and staff, delivered positive results in their previous roles, and understand where ASME must evolve to better serve the engineering community. They bring a diversity of expertise and experience to our leadership team and have the vision to help ASME achieve our business and sustainability goals,” says ASME Executive Director/CEO Tom Costabile. “We are grateful for Michael Johnson’s important contributions to the Society in the establishment of the strategy office and congratulate him on his retirement.”
Keith Bloesch is an information technology, finance, accounting, project management, and operations professional with 25 years of experience driving measurable business success. He has been with ASME since 2012 and was most recently the Society’s senior managing director of business and technology solutions. Previously, Bloesch was a director at PricewaterhouseCoopers (PwC) in Philadelphia, New York, and Amsterdam. In his new CIO role with ASME, Bloesch will provide global vision, leadership, and oversight for the Society’s information technology strategy, and will be responsible for developing the roadmap and implementation plan to help the organization leverage new and existing technologies to enhance its competitive advantage and improve stakeholder value delivery. He earned Bachelor of Science degrees in finance and accounting at DeSales University, as well as several business and technical certifications from Massachusetts Institute of Technology (MIT) and Villanova University.
Anand Sethupathy is a strategy, technology, and social impact leader with over 25 years of experience driving growth and impact. He specializes in building programs that enable the nonprofit sector to leverage technology to scale and accelerate social impact. His prior experience includes founding and leading two technology startups and working across both private and nonprofit sectors. Since joining ASME in 2018, Sethupathy has served in a variety of roles, from managing ASME’s philanthropic portfolio of programs to leading international growth and workforce transformation. In his new CSO role with ASME, he will lead the organization’s focus on strategy, innovation, international operations/growth, sustainability, and government relations, overseeing several organizational units. He is primarily responsible for developing, communicating, executing, and sustaining the organization’s global strategic initiatives. Before joining ASME, Sethupathy helped to build and lead the Technology for Social Good program at JPMorgan Chase & Co. He earned a Bachelor of Science degree in information systems and finance from New York University and a Master of Business Administration degree from Yale University.
Stephanie Viola has more than 20 years of experience in development and non-profit management, with an impressive track record of securing corporate, foundation, and individual gifts to meet ambitious philanthropic goals. She has served as ASME’s managing director of philanthropy and executive director of the ASME Foundation for the past two years. In addition to the development, implementation, and assessment of ASME’s fundraising strategy, Viola will now also oversee ASME’s programs spanning engineering education, workforce development, and sustainable innovation, and associated data-driven impact measurement efforts. Before joining ASME in 2019, she helped plan fundraising strategy, led campaigns, planned giving programs, events and communications for the AIChE Foundation, first as manager of individual giving and later as development director. In 1997, she founded Riot Group, a critically acclaimed, multi-award winning not-for-profit experimental theater company in New York, and served as co-artistic director and performer. She earned a Bachelor of Arts degree in anthropology and theater from Sarah Lawrence College in Bronxville., NY. She is also a member of the CHIEF network, the largest network of senior executive women.
Iana Aranda has 20 years of experience in engineering, design, business strategy, and sustainability, including 16 years with ASME. Most recently, she served as ASME’s senior director of engineering for sustainable development and president of ASME’s Engineering for Change LLC. In her new role as managing director of sustainability for ASME, Aranda will lead cross-functional efforts to develop sustainability business strategy focusing on advancing engineering knowledge, enhancing technical workforce readiness, facilitating the energy transition, and accelerating innovation to improve the quality of life for people and the planet. Aranda will also ensure the Society’s internal operations, net zero strategy, and external advocacy reflect its mission to advance the engineering profession while positively impacting humanity and the environment. She will oversee ASME’s Engineering for Sustainable Development and Engineering for Change teams, and its emerging climate technology and sustainability stakeholder engagement groups. Aranda earned a Bachelor of Applied Science degree in mechanical engineering from the University of Toronto and a certificate in global affairs from New York University. She is passionate about developing and supporting diversity and inclusion, particularly women in STEM, and is a member of the CHIEF network.
For more information, visit www.asmefoundation.org or www.asme.org.
From Hupmobile to High-Tech Bore Solutions; Sunnen Innovation Turns 100
Founder Joe Sunnen’s quest to sell his honing inventions started 100 years ago with cross country sales calls made from the back of his 1916 Hupmobile. Today, Sunnen technology is used worldwide to make performance engine parts, energy exploration equipment, aerospace components, gears, fuel injectors, fluid-power components and more.
In 1924, a young auto mechanic – Joseph Sunnen – saw the need for a tool to help repair cylinder heads without injuring his fingers. His spirit of innovation drove him to develop a unique valve compressing tool which made the job quick and safe. Soon after he started a mobile business, selling his new tools out of the back of a converted 1916 Hupmobile where he and his wife also camped. Early success led Joe to develop and patent a manual cylinder hone for auto garages. Decades later, this basic honing device has evolved into a highly capable CNC machining process by the company he founded. Today, St. Louis, Missouri-based Sunnen Products Company is the world's largest vertically integrated manufacturer of precision honing systems, operating sales, service and manufacturing facilities in 14 countries worldwide.
“As we celebrate our 100th anniversary, Joe Sunnen would be proud to see that his spirit of innovation lives on in our drive to develop new products and techniques,” said Tom Dustman, Sunnen Director of North American Sales. “The Hupmobile remains on display at our St. Louis headquarters, and it reminds us not only of where we came from, but also what we can accomplish.”
The success of Joe’s first tool fueled his imagination and in 1928 he designed the first manual cylinder hone, establishing Sunnen’s roots in precision bore solutions. Ever since, Sunnen experts have conceived, developed, and delivered a continuing line-up of advanced honing systems, tools, and abrasives. The company has also branched into lapping, deep-hole drilling, and skiving/roller burnishing – furthering its reputation as a provider of total bore solutions.
Automotive, marine and air race winners learned in the 1930s their engines got a significant performance boost from precisely sized and finished cylinder bores made with Sunnen hones. Today, the desire for more speed, power, and accuracy – with lower noise, emissions, and fewer maintenance problems – is leading manufacturers to employ Sunnen bore solutions for an ever-expanding range of products, in more industries than ever before.
The company's latest generation of automated honing systems provides a unique capability to control hole size with accuracy of ten millionths of an inch (0.000010"/0.25 µm), correct geometric errors in the bore, and produce a specific surface finish to enhance lubrication and sealing properties. The results produce gearboxes and transmissions that run quieter, smoother and longer; hydraulic systems that are more precise, responsive, efficient and leak resistant; chainsaws and weed trimmers that deliver higher power densities with lower emissions; and firearms that are more accurate and easier to clean. Sunnen controls all R&D, manufacturing, service, and support of its products, including specialized abrasives and tooling. This dedication allows for development of end-to-end processing systems that are custom designed and single-sourced to ensure they meet customers' required quality and production levels.
Sunnen roots are in the U.S., but its reach extends around the world. In addition to its U.S. headquarters, Sunnen has operations in Switzerland, Germany, Austria, France, Italy, U.K., China, India, Brazil, Belgium, the Czech Republic, Poland, Mexico and Canada. A worldwide network of over 30 authorized distributors assures that the sun never sets on Sunnen’s global sales capabilities.
“To this day, Joe Sunnen’s story of commitment and reliance reminds us of how far we’ve come and inspires us to push to boundaries of what’s possible,” added Dustman. “What began in the back of a Hupmobile has grown into a massive operation bringing innovative machinery and advanced tooling to some of the world’s greatest manufacturers. We are excited to carry the Sunnen legacy forward.”
For more information, visit www.Sunnen100.com or www.sunnen.com.
Data I/O Announces CEO Transition Plan; Industry Veteran Wentworth to Lead Company
Data I/O Corporation announced a Chief Executive Officer (“CEO”) transition plan, with industry veteran and current Data I/O Board member William “Bill” Wentworth to become President and CEO. Bill will replace Anthony Ambrose through a managed transition plan.
“We are very pleased to announce a leadership transition plan today with Bill Wentworth coming on board to lead Data I/O,” said Sally Washlow, Independent Chair of the Board of Directors of Data I/O. “Already a highly respected Board member of the Company, Bill will take on an executive role as he becomes President effective September 1, 2024 and CEO effective October 1, 2024.”
Mr. Wentworth, age 58, comes to Data I/O with a wealth of industry experience spanning over 35 years, including private equity and M&A exposure. As the CEO of Source Electronics, the global market share leader in programming and test services, he was a Data I/O customer and led the sale of controlling interest of Source Electronics to HIG Capital in 2001 and the company’s subsequent sale to Avnet in 2008 with significant investor return. Under Wentworth’s leadership, Source developed compelling programming solutions for the automotive and consumer industries, expanding the business and limiting its industry and customer concentration. More recently, as president and owner of Wentworth Advisors, he has consulted in the programming, IT, and private equity markets, focusing on expanding deal flow, performing due diligence and Board service. Wentworth has been a member of the Board of Directors of Data I/O since May 2023, serving as Chair of the Corporate Governance & Nominating Committee and member of the Audit and Compensation Committees.
“I am incredibly excited to become the next leader at Data I/O,” said Bill Wentworth. “Data I/O is the leading supplier to the global automotive industry and has developed industry-leading programming technology, automated solutions, and software. As a longtime customer of Data I/O over the past 40 years, I was a hands-on user of the industry’s first programming solution, the Data I/O 1. As a Board member for the past year, I’ve brought unique perspectives to the Company’s products and go-to-market strategies. Data I/O has the best balance sheet in the industry, an impressive global customer base, and critical programming technologies for automotive electronics market leadership, thanks to Anthony and his team. Our first objectives will be to capitalize on these attributes to generate growth, add new revenue streams, investigate new go-to-market models, and build the most robust, consistent, and reliable solutions for the markets we serve. The team and I will be evaluating from day one a comprehensive set of organic and inorganic opportunities for growth. Using our current strengths and industry-leading position, we will invest and innovate for the future with a goal of attaining sustainably greater profits and returns for shareholders.”
“I would like to thank Anthony Ambrose for his 12 years as CEO,” said Sally Washlow. “Anthony led our transition to Automotive First and introduced the PSV family of programming systems, the most successful family of programming systems in the industry with over 500 systems sold in the past decade. Anthony will assist Bill during his transition period and will be available to consult for the Company for the next 12 months. We all wish him well in his retirement from Data I/O.”
“It’s been my great pleasure to lead Data I/O for the past 12 years,” said Anthony Ambrose. “I recently discussed succession planning with the Board of Directors and I am pleased to hand off leadership of Data I/O to Bill Wentworth. He has the experience in our industry and financial markets to take Data I/O to the next level, and I look forward to fully supporting him during the transition period and beyond.”
Wentworth will continue to serve on Data I/O’s Board of Directors, although he will be reclassified from an Independent member to an Executive member, with Committee participation subject to change. After October 31, 2024, Ambrose will no longer be a member of Data I/O’s Board of Directors following his retirement as CEO of the Company, leaving four members of which three will be independent.
For more information, visit dataio.com.
US Cutting Tool Orders Totaled $208.1 Million in June 2024, Narrowing Year-to-Date Gains to 2.6%
Shipments of cutting tools, measured by the Cutting Tool Market Report compiled in a collaboration between AMT – The Association For Manufacturing Technology and the U.S. Cutting Tool Institute (USCTI), were $208.1 million in June 2024. Orders decreased 2.9% from May 2024 and were down 4.2% from June 2023. Year-to-date shipments totaled $1.27 billion, up 2.6% from shipments made in the first six months of 2023.
“While 2024 started on a positive note, we have seen significant stagnation in several markets utilizing cutting tools,” said Steve Boyer, president of USCTI. “Aerospace has seen many challenges this year, and while we expect to see that market improve in 2025, it has impacted growth for 2024. Modest gains have been realized with orders for the automotive markets but have not fully offset some of the slides attributable to the aerospace industry. While tempering our enthusiasm for the second half of 2024, expectations for cutting tool order growth are still very positive for 2025.”
Looking at the remainder of the year, Eli Lustgarten, president of ESL Consultants, said: “Cutting tool demand is likely to show further softness in the second half of 2024, driven by widespread inventory liquidation in many industries. While there are pockets of strength in markets such as government-financed infrastructure and data centers, the farm equipment sector will show dramatically lower production in the second half of 2024. Energy, construction, and mining sector output will decline. Heightened uncertainty also exists in automotive and commercial aerospace markets.”
The Cutting Tool Market Report is jointly compiled by AMT and USCTI, two trade associations representing the development, production, and distribution of cutting tool technology and products. It provides a monthly statement on U.S. manufacturers’ consumption of the primary consumable in the manufacturing process, the cutting tool. Analysis of cutting tool consumption is a leading indicator of both upturns and downturns in U.S. manufacturing activity, as it is a true measure of actual production levels.
For more information, visit www.amtonline.org.
Manufacturing Technology Orders Grow 4.3% in June 2024 as Year-Over-Year Order Gap Narrows
Orders of manufacturing technology, measured by the U.S. Manufacturing Technology Orders (USMTO) report published by AMT – The Association For Manufacturing Technology, totaled $402.3 million in June 2024. New orders of metalworking machinery were up 4.3% from May 2024 but down 1.6% from June 2023. Year-to-date orders reached $2.2 billion, down 10.7% compared to the first half of 2023.
While the value of orders maintained momentum in June 2024, with the average value increasing significantly, the number of units ordered for the month dropped to 1,471 units, the lowest since July 2023. This divergence indicates manufacturers are generally investing in more automated, task-specific solutions. This trend is further confirmed, as inflation among machine tools, measured by the producer price index, has stayed relatively flat for the last several months.
- June 2024 orders from contract machine shops dropped over 10% from May 2024 in both the number of units ordered and the total order value. Through the first half of the year, the value of these orders was the lowest since the first half of 2020, but the number of units ordered fell further, reaching its lowest level since the first half of 2010.
- Primary metal manufacturers have also pulled back machinery orders in 2024, dropping to the lowest levels in both unit count and value since the first half of 2010. Demand for machinery in this sector has been waning, as the World Steel Association reports that global steel production in the first half of 2024 was flat compared to the first half of 2023.
- One notable exception to this recent trend is the aerospace sector, which has increased orders in the first half of 2024 to the highest number of units since the first half of 2018, yet the value of orders remains about 2% below orders placed in the first half of 2022. With capacity utilization in the aerospace sector reaching post-COVID peaks, this confirms that these manufacturers are in need of additional machinery to meet growing demand.
Orders of manufacturing technology are down nearly 11% in the first half of 2024 compared to 2023, but that difference has narrowed in the past several months after the beginning of the year failed to meet the optimistic expectations formed from anticipated interest rate cuts and strengthened consumer and business sentiment. Despite the lingering uncertainty around the Federal Reserve’s interest rate policy, the pending election, and escalating geopolitical tensions, the remainder of 2024 seems ready for a rebound in demand for manufacturing technology – perhaps even more so with the opening of IMTS 2024 – The International Manufacturing Technology Show in September at Chicago’s McCormick Place.
For more information, visit https://www.amtonline.org/.
America Makes Honors 2024 Award Recipients
America Makes, the national additive manufacturing (AM) innovation institute, announced the recipients of its 2024 Ambassador Awards and Distinguished Collaborator Award at the annual Members Meeting and Exchange (MMX) event held on August 6-7 in Youngstown, OH.
The Ambassador Award Program, launched in 2017, recognizes individuals who have continually demonstrated outstanding dedication to advancing America Makes and its mission. The 2024 class represents a cross-section of the industry whose work helped further advance additive technology and demonstrated the resilience of the AM community. These champions also represent the progress made in AM technology, ecosystem expansion, and workforce development.
Congratulations to the following Ambassadors:
- Rachael Andrulonis, Director of Advanced Materials Research, National Institute for Aviation Research (NIAR)
- Cheryl Bowman, Chief, High Temperature& Smart Alloys Branch, NASA Glenn Research Center
- Robert Carter, Deputy Chief, Materials & Structures Division, NASA Glenn Research Center
- Sarah Jordan, CEO, Skuld, LLC
- Mark LaViolette, Managing Director, Deloitte Consulting
- Thierry Marchione, Laser Engineering Specialist, Caterpillar (CAT)
- Kay Matin, President, AlphaSTAR Corporation
- Travis Mayberry, Additive Manufacturing Lead, RTX Corporation
- Frank Medina, Associate Professor/Director of Technology & Engagement, University of Texas at El Paso
- Marlee Rust, Business Development Manager, General Electric Global Research
Also, during the event, Mark D. Benedict, Ph.D., Senior Scientist, Convergent Manufacturing, Air Force Research Laboratory, was presented with the 2024 Distinguished Collaborator Award. Established in 2014, recipients of this award are celebrated for cultivating effective collaborative relationships with academia, government, and industry. Serving as the Chief Technology Advisor at America Makes for nearly six years, Benedict has played a pivotal role in the Institute's strategic planning, defining project requirements, and the selection and execution of its technical portfolio. He is recognized for his outstanding leadership and unwavering dedication to advancing the technologies, practices, and innovation in the additive manufacturing industry and his contributions to the Institute.
“The Institute has been pivotal in forming a Joint Services community focused on additive manufacturing and connecting that community with the companies and universities looking for problems to solve,” stated Benedict. “There has always been such positive energy in this ecosystem. I am fortunate to have played a small part in connecting Department of Defense stakeholders with enthusiastic technical teams working to mature this technology. It is an honor to be recognized by the Institute for helping to make progress in this important technology.”
For more information, visit https://www.americamakes.us/.