Guest Column
Harshala Patil
Guest Column | Harshala Patil
A good QMS will control nonconformities by acting as a defense line, catching discrepancies and abnormalities in products before they ever reach the customer.
How QMS Helps with Nonconformance Product Management
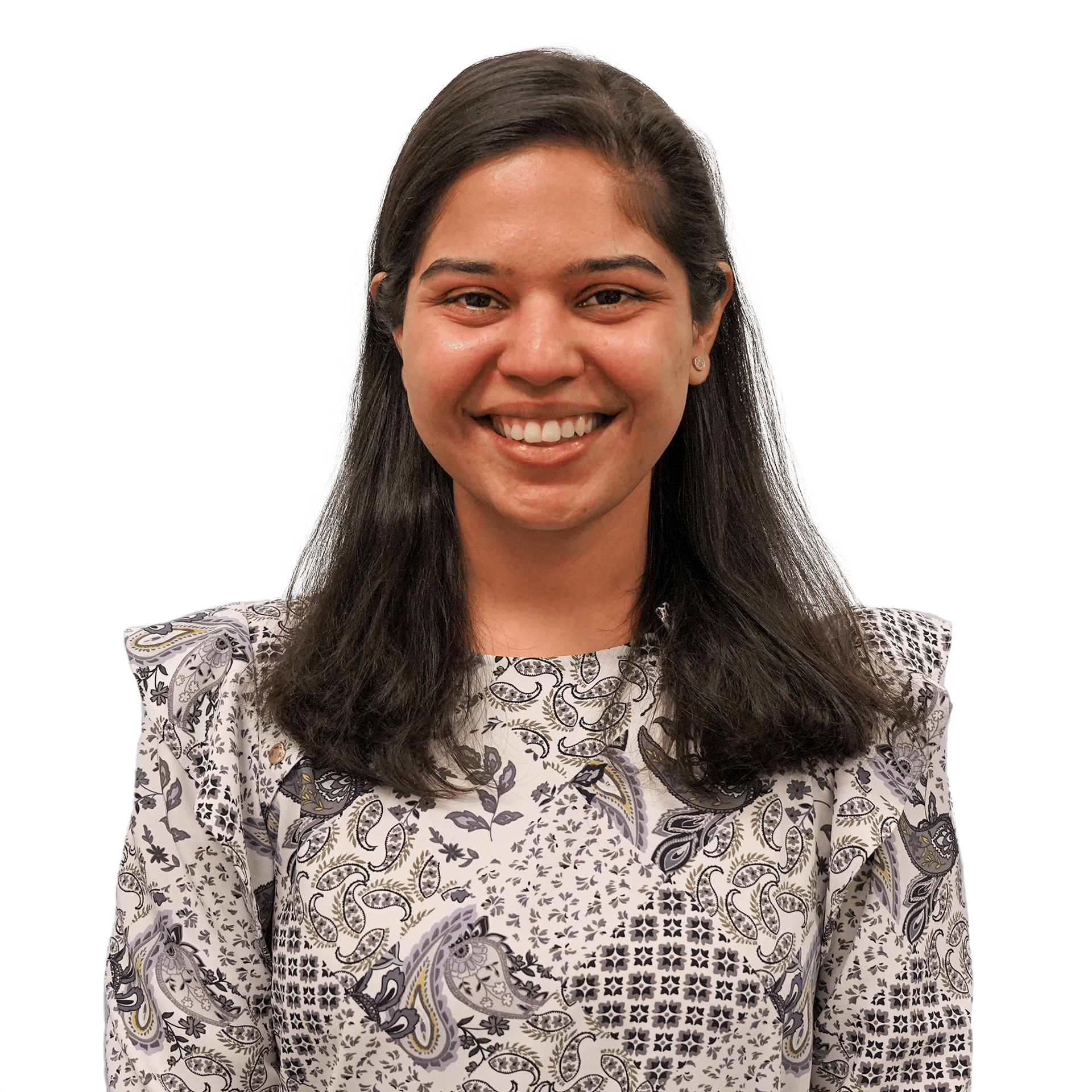
How do manufacturers continue to flourish in a world that is more competitive than ever? Most are driven by the essential customer parameters around price, quality, and delivery. A business will survive only if it creates trust and maintains customer loyalty by responding to fundamental customer needs, expectations, and requirements for any product or service. But in today’s demanding marketplace, “Quality” is the key element that is vital for long-term success.
While material cost, profit margin, and market dynamics all feed into the product price, delivery is a function of the manufacturer’s productivity and competence. Distinctly, quality is governed by how the products work as specified at the time they are manufactured and beyond the point of sale/shipment.
The importance of QMS
A Quality Management System (QMS) can be described as a defined program that documents processes, procedures, and responsibilities for achieving quality objectives. A manufacturer can help administer, drive tasks, and improve its proficiency on a continuous basis through an effective QMS. Additional benefits associated with a QMS include increased consistency, standardization of processes and outputs, reduced errors, increased operational efficiency, and improved customer satisfaction through the delivery of quality products and services.
Based on local or international standards, there are different approaches to QMS that correlate to an organization’s needs and scenarios. Manufacturers usually implement one methodology or integrate a mix of multiple approaches. Established global standards such as ISO 9001, Lean Management, Six Sigma, and Total Quality Management (TQM) are some of the most commonly used QMS methodologies.
Caption
The standard provides a systematic approach to sampling without overtaxing resources.
P - Main body. paragraph of text goes here. Main body. paragraph of text goes here. Main body. paragraph of text goes here.
“Pull Quote Goes Here”
A manufacturer can help administer, drive tasks, and improve its proficiency on a continuous basis through an effective QMS.
What is nonconformance?
Manufacturers employ product testing and verification to ensure that products conform with their standards, specified requirements, and expectations. These factors are typically determined by the product design, regulations, or customer needs. Nonconformance occurs in the presence of failure to act in accordance with any quality issues, deviation from specifications, safety concerns, or process failures arising from any inconsistency or defects.
During quality audits, nonconformities are usually classified as major and minor: a major nonconformity is appraised as a significant failure to meet quality requirements, while a minor nonconformity is an escape or deviation from the QMS that does not result in a serious repercussion. For example, a major nonconformance could be a serious safety hazard in the workplace, distributing a product that is unsafe to use, or identifying multiple missing or unsigned documents. Minor nonconformance examples include a single missing or unsigned document, a single failure to meet an internal deadline, or slight variations in product dimensions within acceptable tolerances. Nonconformance is an essential aspect of QMS because it helps manufacturers identify and address issues that could impact the quality of their products.
Why managing non-conformance matters
Nonconformances can manifest in diverse ways. For instance, imagine the potential impact of nonconformances in various areas of pharmaceuticals, medical devices, defense applications, home appliances, or automotive, where compromised quality could result in human injury or death. Because identifying nonconformances is a proactive measure to warrant the overall quality and safety of products and services, manufacturers must have procedures in place for identifying, investigating, and correcting non-conformances effectively.
Industry standards for nonconformance identification in quality assurance involve a methodical, step-by-step process for detecting deviations, understanding root causes, and implementing corrective actions to avoid recurrence. These steps include identification and documentation, segregation and control, evaluation and risk assessment, disposition and decision-making, corrective and preventive actions (CAPA), and record keeping and reporting. While the primary goal is to meet regulatory requirements, managing nonconformance also promotes the manufacturer’s commitment to delivering products that consistently meet or exceed customer expectations.
A good QMS will control nonconformities by acting as a defense line, catching discrepancies and abnormalities in products before they ever reach the customer. When product problems make it to market, the cost of nonconformance can be significant, making it crucial for all manufacturers to proactively reduce such events. Minimizing nonconformance is a critical component of operations that drive product quality, safety, operational efficiency, cost savings, and regulatory compliance.
Minimizing risk
Preventing nonconformances, or minimizing the risk of similar events happening again, involves implementing preventive actions to reduce the occurrence of excursions and/or deviations from established requirements. To prevent or minimize nonconformances, consider strategies such as conducting regular internal and external audits, performing customer surveys, enabling automated alerts, providing clear procedures/SOPs (standard operating procedures), improving documentation, training, and record keeping, performing comprehensive root-cause analyses, and developing a robust QMS. With today’s innovative technologies, more manufacturers are adopting electronic/digital QMS programs to replace legacy paper-based and/or hybrid systems for managing nonconformances, as these newer systems offer several benefits that improve quality and compliance efforts.
Although nonconformance investigation may appear to be a subset of quality management, in fact the two are closely intertwined. While a stringent quality process reduces the risk of nonconformance, manufacturers can also use the nonconformance data for continuous improvement of the QMS. As a whole, in the quality cycle, the two feed each other and facilitate improvement for the overall quality, performance, and compliance of the processes and products. Thus, maintaining a strong nonconformance identification process will ultimately produce a more effective QMS that benefits both companies and consumers.