xxxxxx xx
xxxxxxxxxx
Fatigue Testing
NDT
NDT
H2 Deck By Bold Name
h2 xxxxxx
H1 xxxxxx
h2 xxxxx
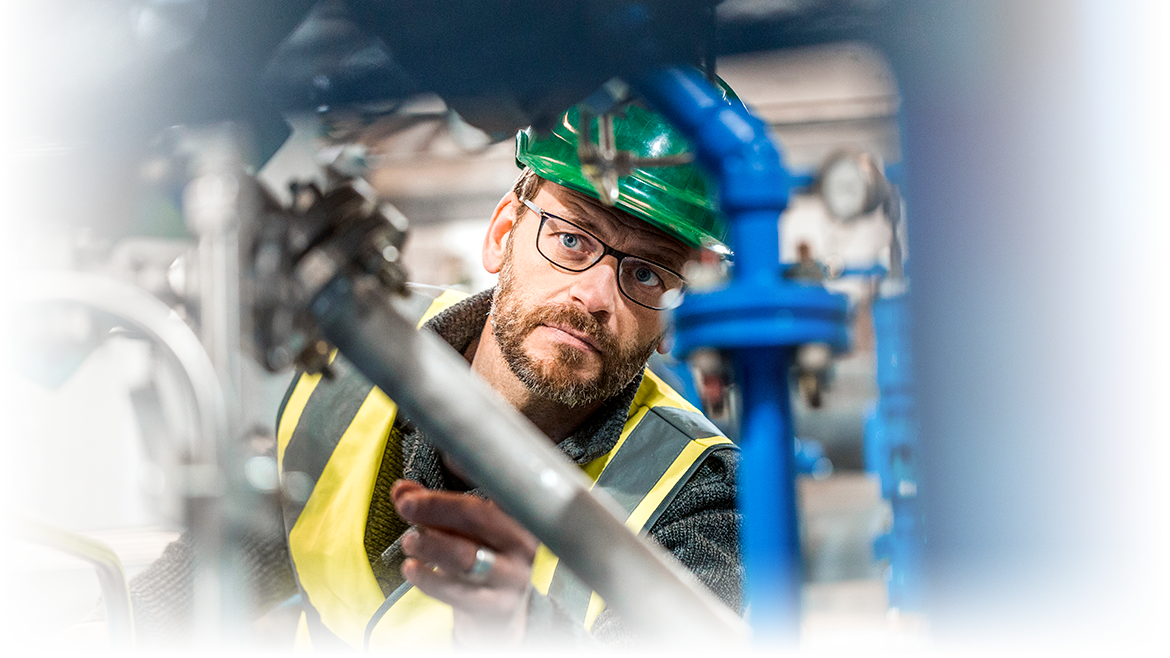
Equipment needs to be more intuitive and automated, making it easier to set up, control, and process test results without requiring expert skills. By Genevieve Diesing
Adapting to Modern Demands in
Fatigue Testing
Fatigue testing is changing.
While its technology is mature, and recent improvements may only be incremental, it’s still developing in subtle ways, experts say.
Organizations are increasingly adopting linear electric motor driven actuators over hydraulic ones, as they offer more cleanliness and precise control of small forces — both of which are mission-critical in biomedical testing laboratories, said Pete Bailey, principal scientist, Instron Dynamic Systems.
When it comes to advanced measurements, “the biggest impact is probably from commercialized and easily usable digital image correlation, for analyzing the strain distribution on the whole specimen,” Bailey said. “This is particularly desirable in research labs, and when examining structures or components rather than simple materials characterization specimens. Also associated with this, more advanced video extensometers are now available, which can give simple live measurement (instead of calculated post-test) of strain without contacting the specimen.”
Fatigue testing has made “enormous progress” in recent years, particularly in terms of test and environmental conditions, such as corrosion and hydrogen fatigue testing, said Frank Walther, PhD, head of Chair of Materials Test Engineering in the faculty of mechanical engineering, TU Dortmund University.
And remote monitoring of fatigue testing has advanced with the use of AI-enabled camera systems that can read existing sensor displays, making it easier to integrate legacy instruments, said Jarid Barthold Robinson, product specialist, physical measurements, Shimadzu Scientific Instruments.
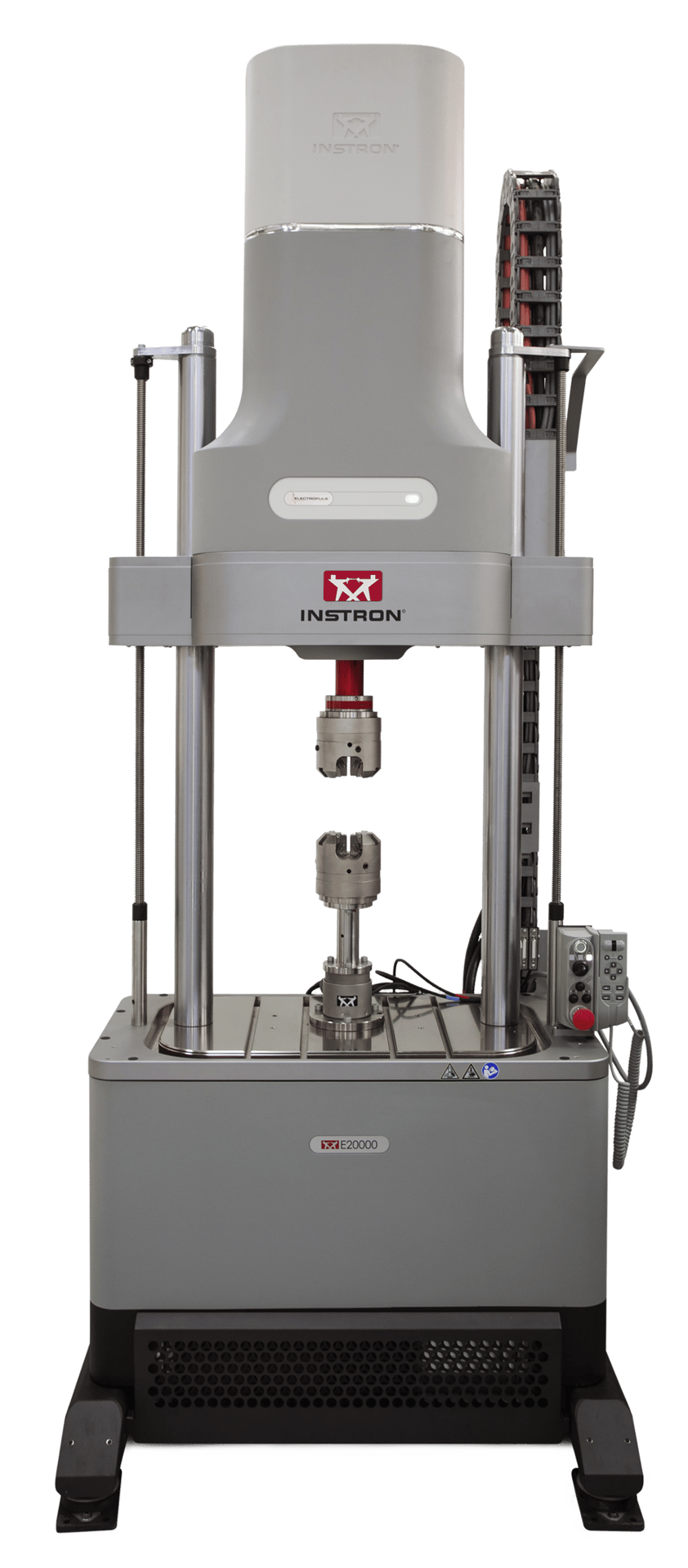
Caption
Trends in Fatigue Testing
Two major trends are already impacting the industry, and there is much discussion in the mechanical testing community of how to embrace them, said Bailey.
“Additive manufacturing technologies have reached such maturity that the high-value research and manufacturing industries who we serve are adopting them. Additively manufactured materials can be tested just like any conventionally produced material, but it is not always appropriate; factors such as specimen sizes and preparation methods might not be representative of the real application, and can themselves affect the results obtained,” he explained.
Many mechanical properties of materials are still determined by visually analyzing graphs, which can lead to inconsistencies, Bailey said. To address this issue, there is a growing interest in automating data analysis and tightening standardization around this aspect of testing.
“Some may be surprised to consider that a majority of mechanical characteristics of materials are still determined using methods which are based on visual analysis of graphs, others may be equally surprised by just how much uncertainty can be introduced when two analysts examine the same dataset,” Bailey said. “In fracture mechanics tests especially, inconsistent analysis can create over 10 percent difference in result from the same data. This is leading to increasing interest in automation of data analysis, and increasingly tight standardization around this aspect of testing.”
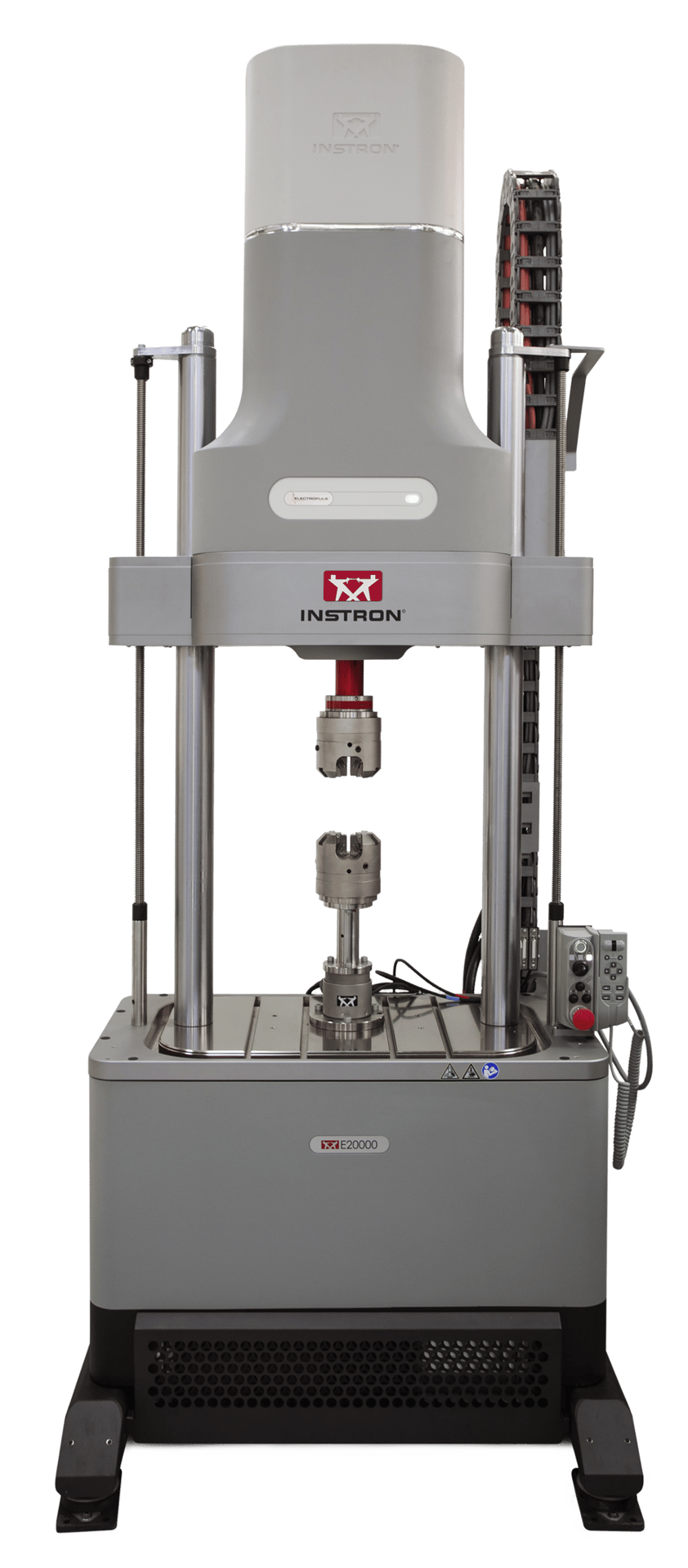
The all-electric test instrument has twice the linear capacity of the E10000 system but in virtually the same size package. Source: Instron Dynamic Systems
The focus on hydrogen-induced fatigue is also an influential trend, said Walter. “We are currently establishing a new hydrogen laboratory where we can conduct in situ testing on hydrogen-charged samples, addressing the increasing importance of hydrogen as an energy source. Additionally, the rise of additive manufacturing brings new challenges related to defect analysis and fatigue performance. We are preparing to address these challenges by developing specialized testing protocols and equipment tailored to additive manufacturing with the main goal of later being able to additively manufacture fatigue-optimized components and structures with guaranteed local properties and capabilities.”
To combat the nature of lengthy fatigue testing, rapid very high cycle or ultra-high cycle techniques are being used to shorten the duration of fatigue tests, said Robinson. The American Society for Testing and Materials, or ASTM International, is developing guides and standards for these techniques to help them become more widely adopted. “This will increase sample throughput therefore the amount of fatigue data that can be produced,” he explained.
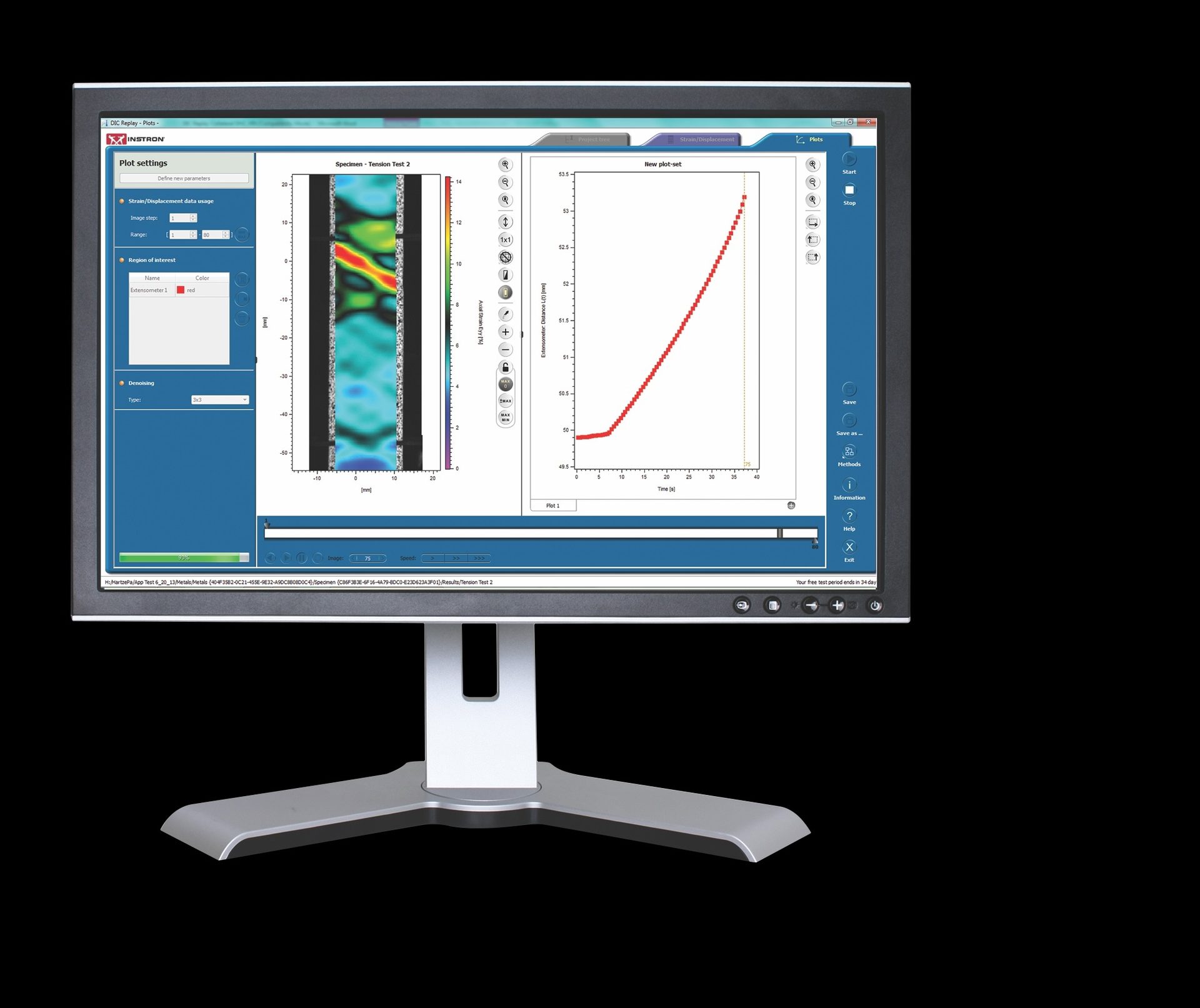
DIC is an optical technique that compares images of a tested specimen’s surface to generate full field strain and displacement maps. It creates pictures that can be used to visualize strain and displacement over the full two dimensional surface of the test specimen. Source: Instron Dynamic Systems
Shifts in the Field
The most significant industry changes are probably around expectations of usability and convenient output, Bailey said. These shifts are driven by the change in personnel and in the levels of automation seen in electronics and equipment we interact with in daily life.
“There are both new and long-established laboratories, coming under the management of a very different generation of engineers, who find themselves asking why some aspects of equipment and post-test operations are still so manual,” he said. “The answers usually lie in a combination of upgrading old systems and procuring new ones. Often those users who have grown up working with much older (but still good) equipment, are astonished at what are now expected features from many manufacturers.”
The advent of short-term testing methods and application-oriented testing, involving multiaxial stress states and environmental conditions, have also shaken things up, said Alexander Koch, PhD., senior engineer, Chair of Materials Test Engineering of the faculty of Mechanical Engineering, TU Dortmund University.
“These advancements allow for more efficient and relevant testing procedures that better simulate real-world conditions,” he said. “We have embraced these changes by integrating advanced testing techniques and equipment into our laboratories, ensuring we provide cutting-edge testing services that take current trends into account and meet the evolving needs of customers. Simply lifetime-oriented fatigue testing a few samples and using models to interpolate how the components behave under different environmental conditions is no longer up to date and very dangerous against the background of the above-mentioned failure rates.”
Modernized Testing in Demand
Manufacturers are challenged by increasing the accuracy and repeatability of tests, and enabling less experienced staff to perform these tests.
This means equipment needs to be more intuitive and automated, making it easier to set up, control, and process test results without requiring expert skills, said Bailey.
“The implications of these are principally to deliver equipment which requires less insight and craftsmanship to use it well – more intuitive and more automated, both in setting up and controlling the test and in processing the raw data into results,” he said.
Amid climate change and the need for efficient use of resources, component requirements are increasing to maximize lightweight construction.
“To ensure that such highly loaded components can be used safely, it is crucial to achieve reliable fatigue testing strategies and databases,” Koch said. “This is linked to the importance of considering all accompanying test circumstances, specifically the environmental conditions in service. For example, it is relevant how the component is used regarding temperature, corrosion and hydrogen environment. All these factors have to be taken into account.”
Staying Up to Date With Training
The mechanical and fatigue testing sector lacks strong individual training programs.
Instead, accreditation in mechanical and fatigue testing is linked to specific laboratories rather than individual operators, Bailey said.
“Unlike in NDT where specific training and certification are a long-standing approach, in mechanical testing and fatigue testing, accreditation is associated with a particular laboratory, since the equipment is not portable and good practice should depend more heavily on equipment, procedures and processes, than on the individual operator,” he explained.
Yet, despite past failures, fatigue continues to be a major cause of industrial damage, Koch said. Adequate training and state-of-the-art testing are important for addressing fatigue-related issues.
As such, “Training programs are evolving to incorporate the latest technological advancements and methodologies in fatigue testing,” he said, including TU Dortmund’s. In fact, the university regularly offers “interested partners” the opportunity to “learn from us on site during workshops and seminars.”