Measurement
Automation and robotics have accelerated CMM technology, enabling 24/7 operation, improved accuracy, and streamlined maintenance. The integration of AI, IoT, and cloud-based systems has further enhanced CMM capabilities. By Genevieve Diesing
Advances in
Automation
and Robotics
Make CMMs More Efficient, Accurate
Automation and robotics significantly enhance the efficiency and accuracy of coordinate measuring machines (CMMs) and CMM software. By utilizing new metrology technology coupled with data analysis, automation eliminates the need for human intervention in the process of taking and recording measurements. This automation allows for continuous operation, enabling CMMs and CMM software to function 24/7.
Automation also helps to monitor metrology and robotic equipment, identifying potential maintenance or downtime issues. This includes tasks such as equipment calibration, basic preventive maintenance, and fault detection for possible failures.
In the past, CMMs were programmed manually, one measured object at a time. Operators were fully responsible for collisions caused by a CMM’s moving parts and the objects measured. It might take a week to create a new program. But advances in robotics and modern robot programming software have forced CMM software to evolve, says Marc Soucy, president and co-founder, InnovMetric.
CMM Software Then and Now:
How to Measure Parts Faster
InnovMetric's Marc Soucy explains how CMM software can help you measure parts quickly and accurately, how to use these techniques most effectively, and how automating can help.
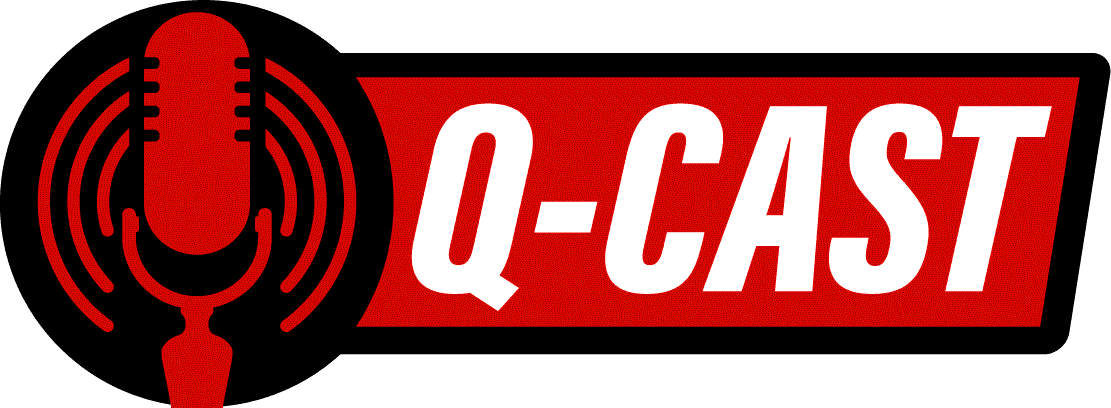
For example, CMMs now use CAD models to detect and prevent collisions, or to automate the planning of trajectories, Soucy says.
Automation and robotics have improved efficiency by enabling customers to measure more parts faster, says David Wick, manager, product management, ZEISS Industrial Quality Solutions. As a result, manufacturers’ costs per part have decreased, saving them overhead.
“Improvements in CMM software have dramatically reduced the cost and time required to measurement programs, enabled reporting of 100% of the measurement results on every part measured in every plant, and simplified the creation of connections to automation equipment—all contributing to reduced setup time and cost,” Wick adds.
AI, IoT and other integrations
The integration of CMMs with other digital technologies has led to significant developments in the field.
One notable advancement is the ability to manage the maintenance and use of a fleet of CMMs using centralized solutions. This allows for efficient coordination and control of multiple CMMs, streamlining operations and ensuring consistency. Additionally, CMMs can now be digitally interconnected with data management systems, eliminating the need for manual file management by operators. This enables instant sharing of measurement results with other teams within the company, promoting collaboration and facilitating data-driven decision-making. And, measurement data stored on central servers can be integrated with other digital enterprise solutions, accelerating root cause analyses and ensuring process traceability.
“AI is not in the mainstream, yet,” says Gene Hancz, CMM product manager, Mitutoyo. “To some degree the automatic program generation tools such as MiCAT Planner has elements of AI now, examples are the ability to select the most appropriate probe/stylus combination to measure a given feature.”
These tools possess the capability to select the most appropriate probe/stylus combination for measuring specific features, enhancing efficiency and accuracy. Plus, advancements in path generation algorithms have resulted in streamlined processes and minimized cycle times.
CMM software has also made significant strides in automation and intelligence. It can now read CAD files containing product manufacturing information (PMI) and autonomously create measurement programs with minimal human intervention. This form of AI eliminates the need for manual programming, speeding up the measurement process and reducing the risk of passing on out-of-spec parts. Additionally, CMMs can communicate with machine tools through the MTConnect protocol, enabling information sharing that allows machine tools to adjust for subsequent machining or milling operations.
Cloud computing has also made its mark in CMM technology. CMMs can store part-by-part measurement results in the cloud, enabling easy access and sharing of data. Cloud-based statistical reporting software, available on a subscription basis, allows for real-time analysis of measurement results against control limits. This software can aggregate results by production lot, plant, or even across multiple plants, providing trend information and facilitating global collaboration.
Future trends
In the near future, businesses should keep an eye on cloud-based systems for CMMs, says Hancz. These systems offer greater flexibility, scalability, and mobile-ready support, allowing for efficient and flexible maintenance operations. Cloud-based solutions have the potential to expand maintenance capabilities as businesses grow, and they are expected to bring new features and capabilities to CMM software.
Another important trend is the expansion of analytical predictive maintenance in CMMs. With advancements in IoT, machine learning and AI, CMMs can utilize integrated sensors and data collection software to monitor programs and predict potential mechanical failures. By leveraging AI and statistical analysis, businesses can schedule maintenance more effectively, simplify operations, and reduce operating costs.
Internet of Things (IoT) devices are increasingly being deployed in factories to collect data on various aspects of production. By integrating IoT devices with CMMs, businesses can expand manufacturing capabilities and enhance the features and capabilities of CMM software. For example, an IoT device integrated with a CMM can automatically generate repair requests based on collected data. When an anomaly is detected, such as a temperature spike, a CMM work order can be generated for the maintenance team to investigate and resolve the issue, minimizing costly repairs and downtime.
In terms of technology advancements, businesses should look for ease of use in measurement software and automation software, says Wick. User-friendly interfaces and faster automation processes can significantly improve productivity. Additionally, a complete ecosystem for measurement and reporting, including software for handheld, optical, and tactile systems, is an important trend to watch for. The integration of plug-and-play sensors and automatic sensor changing on CMM machines will also contribute to productivity improvements.
CMMs are particularly valuable in aerospace, automotive, and medical industries, where additive manufacturing (3D printing) is utilized, Wick says. CMMs help ensure that printed parts meet dimensional specifications consistently, providing insights into the 3D printing process and enabling businesses to make quick process adjustments.
Advancements in CMM technology
CMM technology has shifted from manual programming to more user-friendly and automated methods in recent years. This has enabled a new generation of operators to quickly learn and utilize CMMs, reducing the reliance on expert operators who are nearing retirement. Additionally, easier-to-use CMM software has broken down silos in metrology labs, allowing portable metrology operators and CMM operators to learn each other’s skills and facilitate seamless work organization.
Several advancements have specifically addressed the limitations of CMM systems. The use of lighter weight materials, such as ceramic and aluminum/carbon graphite, in place of traditional materials like granite and steel has made moving structures lighter, resulting in increased speed and acceleration during measurements. The introduction of 5-axis probing technology has significantly reduced measuring time by up to 80%. Furthermore, multi-sensor capable CMMs can now incorporate high-speed scanning, laser sensors, optical sensors, and roughness sensors, eliminating the need for multiple devices and allowing a single CMM to perform a variety of measuring tasks.
Real-time temperature compensation has also been implemented, enabling CMMs to be used near-line or in-line for measuring purposes. Automation and artificial intelligence (AI) programming tools have significantly reduced programming time, with the ability to utilize CAD models with Product Manufacturing Information (PMI). This integration has the potential to reduce programming time by as much as 90%.
Advancements in CMM technology have also facilitated the utilization of captured measured data to control manufacturing processes throughout the entire lifecycle of a part. Data visualization software, coupled with AI, enables continuous product improvement by leveraging the collected data. Automation of data collection processes ensures harmonious and disruption-free data acquisition, which is a crucial tool in driving quality control and process optimization.
These improvements have significantly increased the productivity and efficiency of manufacturing operations, making CMMs an indispensable tool in quality control across various industries.