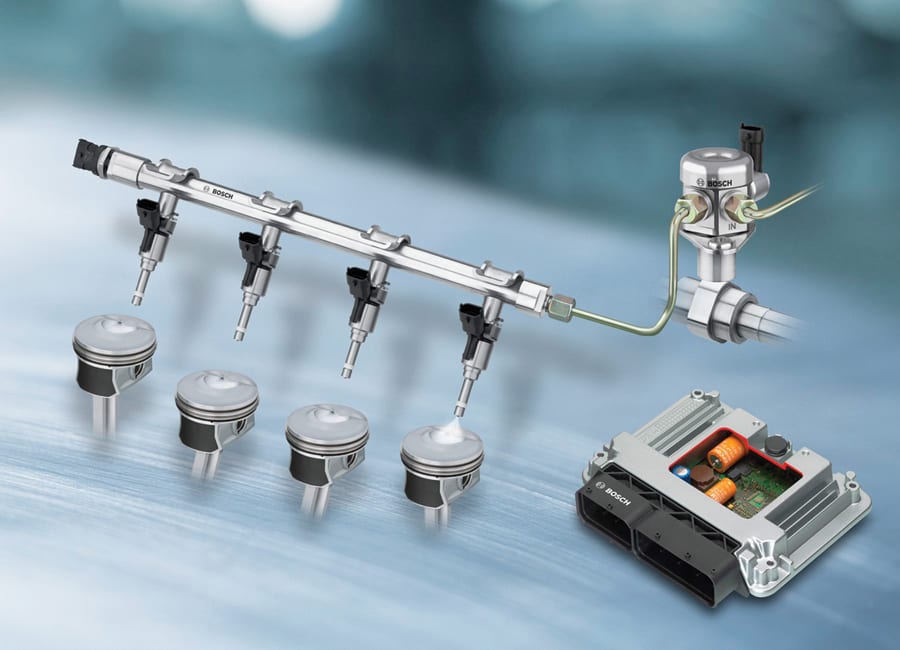
This Case Studies Special Advertising Section features manufacturing companies with real-world challenges using quality equipment, software and services to solve their problems and improve their processes. These problem-solving stories describe myriad manufacturing challenges and how the correct application of a supplier’s product or service made the difference, providing quantitative benefits to quality and manufacturing issues.
The suppliers in this special section present these real-world problems and solutions to help Quality Magazine subscribers who may have similar experiences.
Case Studies
— Special Advertising Section —
The Bosch Group is a leading global supplier of technology and services in the areas of automotive and industrial technology, consumer goods and building technology. The Automotive Technology division is Bosch’s largest business sector in North America employing approximately 12,200 associates at approximately 30 primary locations.
While there are 29 Bosch US and international facilities that have GAGEtrak installed, the Anderson, SC location of Robert Bosch is responsible for managing 4,500 gages and conducting 4,000 calibrations each year to ensure accurate and reliable measurements of their gasoline systems products.
Bosch chooses GAGEtrak Calibration Management Software to track their metrology assets, schedule their calibrations and maintain a system that is compliant with their corporate quality requirements and standards.
Prior to GAGEtrak, the company used filing cabinets and index cards to track calibrations. With GAGEtrak, the calibration tracking process at Robert Bosch became almost paperless. “GAGEtrak streamlined our recall process,” says Thomas.
As a leading global supplier of automotive and industrial technology, Bosch is serious about quality and performance and chooses GAGEtrak to help ensure measurement accuracy and reliability.
GAGEtrak is used at thousands of facilities worldwide to improve measurement quality, assure compliance and increase efficiency. Contact CyberMetrics today to learn how GAGEtrak will do the same for your company.
At the Tremec Queretaro plant, transmission systems are produced for Daimler, Volvo, GM, John Deere and CNH. Tremec decided that its manufacturing process could be improved considerably, since the process control of parts was taking far too long. With a new Daimler gear project it decided to use Renishaw Equator™ gauging system for a different approach during grinding and green gear turning. “By analysing our customer’s specifications, looking at the features to be gauged and controlled, we realized that we were going to cut down on the number of devices, as the Equator can gauge everything—distances, dimensions and diameters.”
A manufacturer of swimwear and athletic gear upgraded their incoming inspection and material characterization processes through the use of Mark-10 force measurement equipment.
Of principal interest to their Engineering and Quality teams was the strength and durability of the company’s swim goggles. Various components of the goggles require testing, including the rubber straps and lens bridge. Several types of tests were developed:
Mark-10 supplied a complete testing solution, consisting of a motorized test stand, force gauge, and several types of standard and custom grips. Data collection software records the data for the destructive tests, providing curves, tabulated data, statistics, and customizable reports.
The small footprint of the system easily settled into the company’s busy facility and was quickly mastered by their staff.
A customer discovered their new Component Engineering TruPosition probes were not compatible with their installed wireless measurement collection system. They asked MicroRidge for a solution that would allow them to collect measurements wirelessly from the TruPosition and their other installed gage devices with the least disruption to their current data collection process.
With 38 years of expertise in designing measurement collection products, MicroRidge created a MobileCollect Wireless solution compatible with the customer’s new TruPosition probes and their installed base of calipers, micrometers, and RS-232 serial output gage devices. This solution is now available to other MobileCollect Wireless customers as a standard product.
The MobileCollect Wireless product offers compatibility with over 70 gage brands and thousands of gage models. MicroRidge is constantly researching gage devices to expand the list of compatible devices. Our “connect any gage into any software” philosophy differs from other “single-brand only” wireless system providers in that it allows companies to implement gage devices that best address their specific needs, regardless of the brand or model.
Our gage connectivity expertise and extensive line of wireless receivers and transmitters allow MobileCollect Wireless to offer data collection solutions not available from other wireless system providers. The free MicroRidge product demo program will enable companies to evaluate the MobileCollect Wireless products to confirm it provides the required solution before making a financial commitment.
AEREM is a French company that designs and manufactures assembly and maintenance tools, as well as mechanical and fluidic test benches, for the aeronautics, aerospace, and pharmaceutical industries. MSL Métrologie is a partner who offers 3D measurement services on industrial sites in France and abroad, based on several years of experience with large aeronautics and aerospace companies. Both companies wanted a single metrology software to control their park of measuring devices.
In 2019, AEREM decided to retrofit their measuring instruments and review the software component. They consulted MSL Métrologie, a user of PolyWorks® Metrology Suite, and chose PolyWorks|Inspector™, a 3D dimensional analysis and quality control software solution. It can control their CMM, laser tracker, and measuring arm through plug-ins provided at no additional cost. “With this solution, we can quickly switch from CMM-based measuring to portable-arm based measuring,” says Vincent Renaud, Methods and Product Quality Control Officer at AEREM. He also appreciates the excellent training and technical support and uses PolyWorks|ReportLoop™ to send data to Excel and PolyWorks|Talisman™ to replicate the PC display on a mobile device.
MSL Métrologie uses PolyWorks to control their laser trackers, arms, and CMMs. They like the user-friendly, and intuitive interface, value its advanced features, and appreciate the follow-up and support provided by PolyWorks Europa, all of which help them offer customized solutions to their clients.
“For the InnovMetric group, service is an essential element,” says Thibault Hehlen, Commercial Manager of PolyWorks Europa. Together with its network of partners, InnovMetric has a technical support team with extensive experience in industrial metrology, product engineering, and manufacturing that includes over 150 application specialists directly supporting users in 43 countries.
“At MSL Métrologie, we believe PolyWorks is set to become the must-have software in the field of 3D metrology,” says Benoît Rotereau, company founder.
InnovMetric Software Inc
info@innovmetric.com
1‑888‑688‑2061
www.innovmetric.com
Pacemakers and other implantable medical devices must be free of even minor defects. Being able to verify the performance of a medical device, as well as ensure that it meets the required quality standards and regulations, is of paramount importance in order to eliminate the risk to the patient.
3D Computed Tomography (CT) is a nondestructive scanning technology that allows you to view and inspect the external and internal structures of an object in 3D space. Computed Tomography works by taking hundreds or thousands of 2D Digital Radiography projections around a 360 degree rotation of an object. Proprietary algorithms are then used to reconstruct the 2D projections into a 3D CT volume, which will allow you to view and slice the part at any angle.
When imaging a pacemaker, most medical manufacturers are looking for possible defects in the battery, circuitry and the laser welded casing that holds and protects the electronics. Because access to the circuitry of implantable devices is impeded by the packaging of the device, and because the packaging may have influenced the failure, nondestructive testing techniques must be used extensively in R&D, product development as well as final production.
Medical device manufacturers must adhere to the strictest quality requirements and nondestructively testing these parts can not only save time and money but ultimately save a life.
(866) 718-2471
sales@4nsi.com
Recent evolution of Morgan cars has relied on technology advancements in metrology. Graham Chapman, Technology Manager, has deployed new measurement and inspection software to ‘digitise’ and preserve certain key characterises of Morgan chassis and body structures. “We needed a solution that was easy to use but provided high-end model-based functionality to meet our exacting engineering standards here at Morgan Cars. Morgan is a tradional methods car builder but that does not mean we reject new technologies to achieve our goals of a ‘British Classic,” said Graham.
Verisurf Software was selected as the measurement, inspection, and reverse engineering software of choice along with a portable CMM scanning arm. The software/hardware combination provides Morgan with a user-friendly digital route from hand-built components and assemblies to the CAD engineering team. The engineers can then produce up to date CAD designs of tradional legacy car platforms. This provides great insight into the current build process and gives a planning method for repeatability.
Model-Based Workflow Maintains Digital Continuity
Verisurf software is based on a CAD platform and supports Model-Based Definition (MBD) workflow, which is key to maintainng data integraty and relavance as part of the overall design and manufacturing process. When using MBD, the CAD model is the nominal to which all parts are measured and inspected against, keeping the all-important digital thread intact - from design to manufacturing to inspection and quality reporting. Everything that defines the part exists in a single digital archive, including how to manufacture and inspect the part. Based on its CAD platform and MBD functionality, the software is well suited for scan-to-CAD reverse engineering, inspection, tool building, and assembly guidance.
Challenge:
When a customer in the surface metrology industry needed help finding a better way to inspect freeform optics, they asked Aerotech for a solution that would allow them to measure faster, more precisely and with the smallest possible machine footprint.
Solution:
With 50 years of expertise specializing in custom-engineered precision motion products, Aerotech was able to develop a custom solution to measure parts up to 40 percent faster with a 60 percent smaller machine footprint than conventional Cartesian systems. The measurement device, called the surface measurement motion platform (SMP), is now available to other Aerotech customers as a standard product that can be customized to meet their specific needs.
The SMP integrates four axes of motion to deploy an innovative spiral scan. The workpiece is positioned on the lower-axis, rotary, air-bearing stage. Linear, vertical and rotary stages on the bridge above it move the measurement sensor, allowing the user to maintain a constant distance and normalcy to the optic being measured. This configuration gives users precise control of the measurement.
Unlike a Cartesian system using a raster-scanning technique, the SMP’s spiral scan saves time by eliminating extraneous linear motion. Because the part is continuously rotating below the sensor, users can scan over the entire part with less motion, which enables a smaller machine footprint as well.
With manufacturing ramping back up in the USA, quality departments are looking to standardize their inspection process. These companies are looking at Gradient Lens Corporation to simplify and modernize their operations. The unique factors making Gradient the logical choice are image quality, seamless integration, economical price and our dedication to streamlining your visual inspection process.
We understand that customers often contact us with an immediate need. We strive to keep all of our products on the shelf for immediate delivery. In addition to being manufactured in the USA, our products are repaired and supported in the USA as well.
An automotive manufacturer was experiencing water leaks around the windshield seal after final assembly. A robotic dispensor was programmed to apply a fixed amount of sealant; but as the nozzle became dirty or clogged, the adhesive material applied to the surface was not a consistent shape. When the adhesive hardened, the inconsistent shape caused irregularities in the seal.
To verify that a consistent amount of adhesive was being applied, the height and width of the sealant bead needed to be measured. The polyurethane sealant had to be measured immediately after being applied, while it was still hot, and before the windshield was pressed into place. Each vehicle had to be inspected quickly as it continued to move down the assembly line.
A LaserGauge® HS702 DSP sensor with a 1.2" field-of-view was chosen for the application because of its processing speed, light weight, and its portability. A special standoff was developed to make it easy for the inspector to position the sensor at the correct height over the sealant bead. Inspectors were able to make each measurement within a couple of seconds and the in or out-of-spec condition was shown by a color-coded GO/NO-GO indicator.
Using the LaserGauge® HS702 sensor, the manufacturer was able to quickly identify if the amount of the sealant was sufficient to prevent water leaks and to monitor the condition of the application equipment.
Lloyd Instruments offers the powerful and advanced LD Series of materials testers that includes five dual column testers ideally suited to test a full range of packaging materials from 5 to 100 kN whether paper, plastic, textile, or metal based.
Whether evaluating raw materials or new container designs, through monitoring the production process to quality testing finished articles, thorough testing at various stages eliminates potentially disastrous product contamination in storage, transport and use.
With a full 452 mm space between the columns and a crosshead travel up to 1070 mm, the LD Series features an extra large work area offering the flexibility for complex testing of small as well as large and odd shaped samples on the same machine.
The LD Series are designed for ease of use. They help automate testing, reduce costs and save time. A CANBUS interface provides fast, accurate communication between the test machine and add-on accessories such as extensometers and temperature chambers.
The LD Series are supplied with the NEXYGENPlus analysis software, which makes advanced analysis and reporting quick and simple to perform. An extensive library of pre-programmed test setups ensures error-free testing, while built-in wizards guide users through advanced customized test setups. Test results can be automatically exported directly into Microsoft Word or Excel.
With their rugged design, the LD Series are built for long life and reliable operation. An advanced electrical design with a modern AC drive and preloaded ball screws ensure better speed and displacement accuracy. High stiffness frames help prevent frame deflection and crosshead movement.
Made To Measure is a leading quality inspection laboratory providing metrology equipment and services to companies throughout North America. We have the most comprehensive offering in the industry ranging from dimensional inspection, programming and reverse engineering to CMM service, CMM equipment and metrology training. We can support any company no matter their level of metrology proficiency, from small scale manufacturers to advanced quality departments. Our team of highly-experienced metrologists are AUKOM-certified, trained in all aspects of dimensional inspection, and are proficient at finding custom solutions! In fact, finding custom solutions is what we do best!
While our typical project calls for us to inspect anywhere from one to a few dozen parts at a time, recently a client asked us to take on a high-volume inspection project requiring us to measure and sort 60,000 of the same large part! To keep the inspection price down and the lead-time short, we designed & built custom multi-part fixtures and created specialized measurement programs for several CMMs and Renishaw Equators. To get the most efficiency during inspection, the fixture plates were designed to hold 12 parts at a time allowing our CMMs to measure multiple parts in a cycle. This innovative approach dramatically increased our inspection output and significantly reduced our lead-time, providing our customer with considerable savings.
From dimensional inspection, CMM programming, custom fixture designs & more, we’ve got you covered. We specialize in creating custom metrology solutions for challenging inspection projects! Learn more about our services at www.madetomeasurecmm.com/cmm-services or contact us today to discuss your project.
Scroll Down
Scroll Down