Products
the latest products to help you improve your manufacturing process
Harold G. Schaevitz Industries ILPS-13Z Miniature LVIT Position Sensor
Harold G. Schaevitz Industries announced the release of the ILPS-13Z Series Miniature Linear Variable Inductive Transducer (LVIT) Position Sensor. Made in the USA, this innovative sensor is designed to deliver exceptional performance and reliability for a wide range of industrial and laboratory applications, including automotive R&D, motorsports, motion control, medical, military, and aerospace.
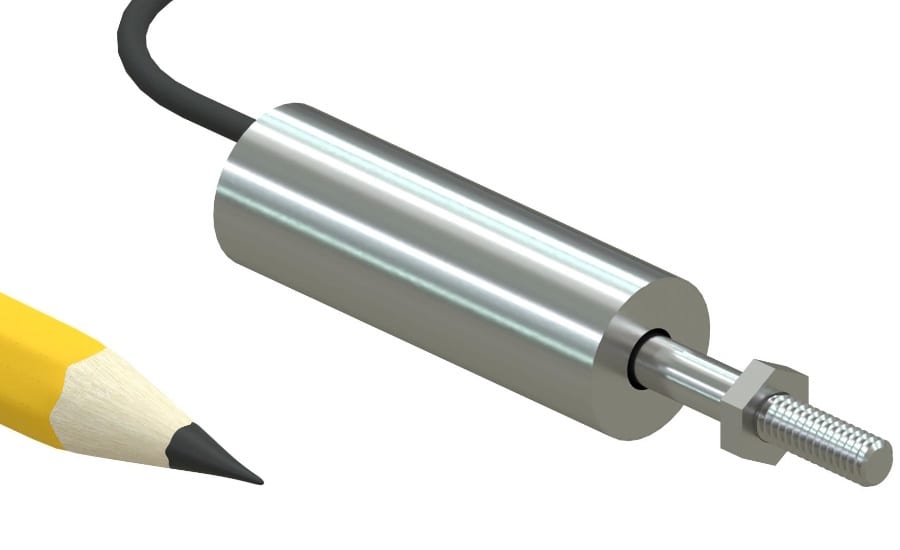
The ILPS-13Z series sensor features a ruggedized design with a ½” OD stainless steel housing, incorporating an inductive coil and spoiler combination that eliminates the wear and dithering issues commonly associated with potentiometer-type sensors. The integrated amplifier electronics remove the need for an external signal conditioner, streamlining installation and operation.
ILPS-13Z Features:
- Contactless Operation: Eliminates wear from dither or cycling
- I/O: 15-30VDC input with an option of four different analog outputs including 0-10VDC and 4-20mA
- Versatile Range: Available in ranges from 0.1 to 8 inches (2.5 to 200 mm)
- Compact and Durable: 0.5 inch (13 mm) diameter stainless steel housing, rated to IP-67
- Flexible Configurations: Radial cable exit version with swivel rod eye ends, and axial termination versions with either M12 connector or cable
The ILPS-13Z series is constructed from industrial-duty materials to resist dust, water, temperature, shock, and vibration, ensuring reliable performance in the harshest environments.
For added convenience, a Mini Connector can be installed on the adjacent wire lead termination end upon request.
Harold G. Schaevitz Industries
https://www.hgsind.com/miniature-linear-position-sensors-landing-page
SINAMICS DriveSim Basic
- New SINAMICS DriveSim Basic software solution for fast and easy simulation of drives
- Seamless integration of models into commercially available simulation programs
- Validated function units accelerate development phase
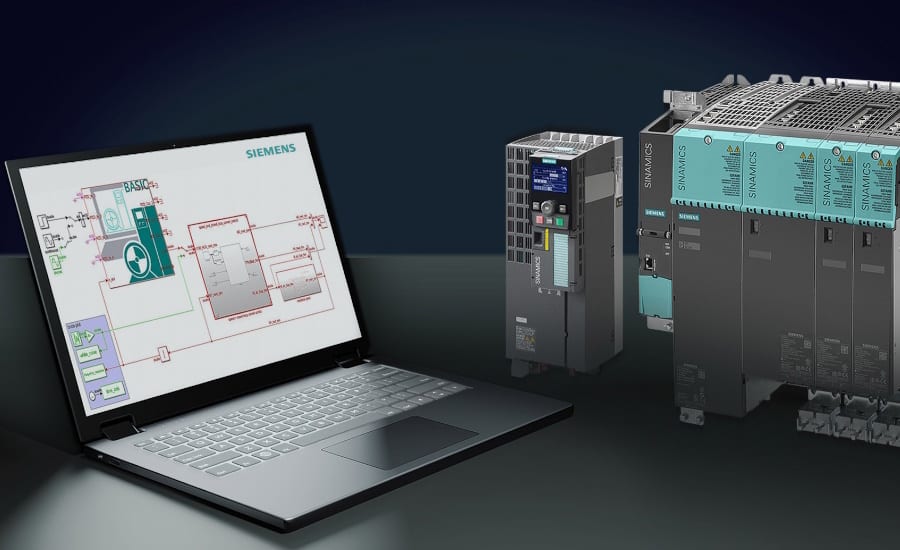
With SINAMICS DriveSim Basic, Siemens presents a new software solution, with which drives and their behavior in machines and plants can be simulated, adapted and optimized. With this new solution, Siemens offers a quick and easy entry into the drive simulation and enables machine and plant manufacturers to accelerate their own development phase.
SINAMICS DriveSim Basic bridges the gap between logical and mechanical simulation. The application focus is on simulation support of the customer application, i.e., the components that interact with the drive. The simulation provides answers to drive questions even before a concrete product selection has been made. For the virtual commissioning of the PLC control with known Profidrive telegrams or complex mechanics on the virtual drive shaft, the model provides a reliable representation of the drive system in the required level of detail.
One possible application scenario is the coupling of the PLC and the mechanical model via SINAMICS DriveSim Basic. The calculated load profiles can then be loaded into the TIA Selection Tool or SIZER and a drive selection can be made. The required drive parameters and interfaces known from the real world are available for the simulation.
Users configure only the part of the drive that is needed for simulation purposes — and a time-consuming complete virtual commissioning of the drive is not required — ultimately saving time and costs. The models in SINAMICS DriveSim Basic seamlessly link to the existing drive documentation and have been validated against real SINAMICS drives using the same test vectors.
For easy handling, SINAMICS DriveSim Basic is available as a standardized Functional Mockup Unit (FMU) model. The software offers the same FMU file for every SINAMICS drive. For example, SINAMICS S120 and G120 drives including the motor can already be represented. Additional drives will follow.
This FMU can be imported directly into the simulation program used. SINAMICS DriveSim Basic is compatible with many commercially available simulation programs, such as Simit, Simcenter Amesim, NX Motion or Matlab Simulink. Together with other virtual Siemens solutions such as SIMATIC S7 PLC SIM Advanced or NX Mechatronics Concept Designer, a consistent model-based development process can be implemented.
Siemens
mc.us@siemens.com
www.siemens.com/drive-virtualization
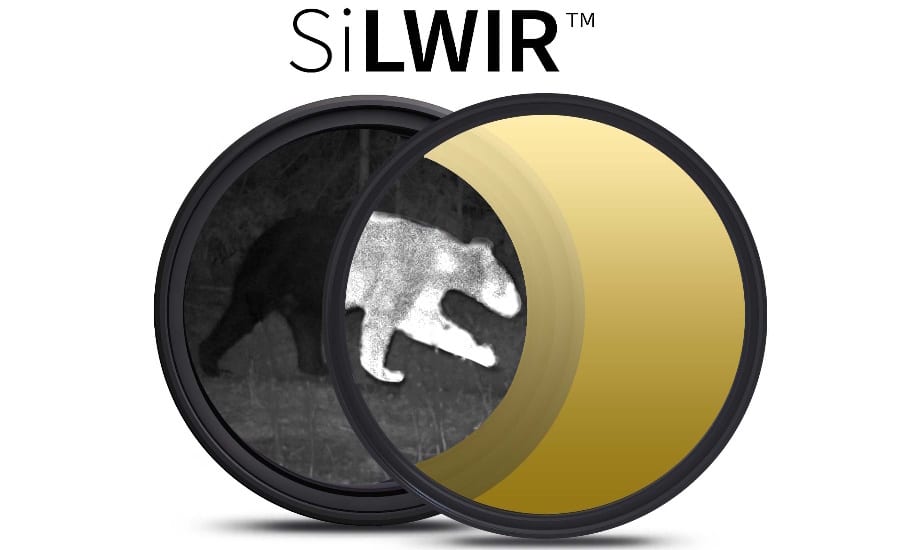
MidOpt SiLWIR Silicon Protective Windows for Industrial Imaging
The cost and lead times for Germanium optical components have skyrocketed. Enter SiLWIR™ Protective Windows by MidOpt®, utilizing a more highly transmissive silicon material optimized for Long-Wave-InfraRed (LWIR) imaging applications. SiLWIR Windows feature abrasion-resistant DLC (diamond-like carbon) and AR coatings. A lightweight, far lower cost and far shorter lead time alternative when compared to Germanium, SiLWIR™ windows are also more thermally stable and breakage-resistant. Silicon will operate at temperatures up to 150°C, while Germanium is usually limited to around 70° C.
Teledyne Next-Gen AI-Powered Smart Camera
Teledyne DALSA announced its next generation AI-powered BOA™3 smart camera for industrial automation and inspection.
The new BOA3 smart camera is designed to leverage the best features from previous BOA generations and combine them with new sensor and AI (Artificial Intelligence) inspection technologies developed by Teledyne. BOA3 is a highly integrated vision system in a compact, rugged smart camera format designed to meet the needs of the most complex, demanding machine vision applications.
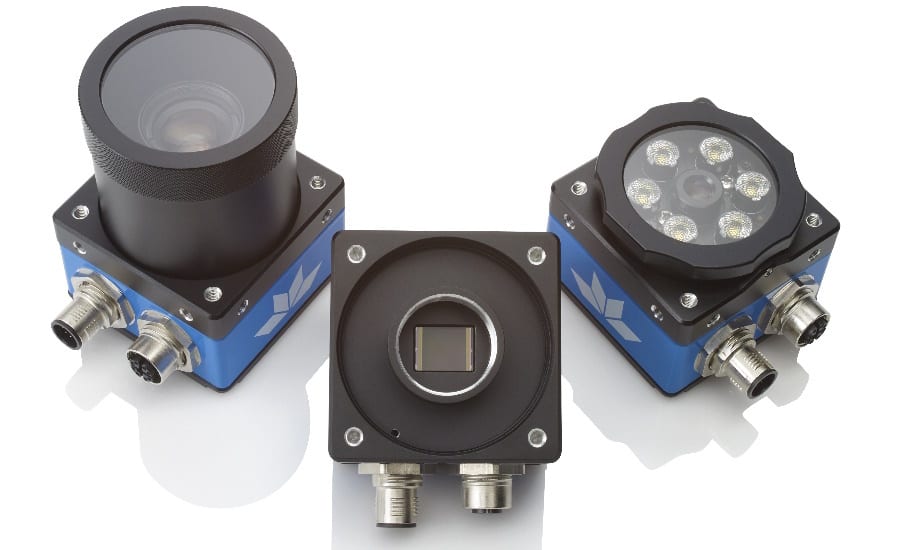
The new BOA3 is an exciting next step in our smart camera development,” said Szymon Chawarski, Product Line Manager, Vision Systems. “Its modular and flexible architecture will allow us to offer new and powerful solutions for embedded machine vision inspections.”
BOA3 offers sensor resolutions from 1.2 to 12MP, integrated or C-mount lens options, onboard I/O, and includes easy-to-use machine vision software, all in one common platform. BOA3 smart cameras deliver the flexibility and uncompromised functionality to enable quick, cost-effective embedded machine vision deployments.
BOA3 comes with iNspect™, an easy-to-use, no-code inspection development software with tools for positioning, part locating, pattern matching, measuring, barcode reading, feature or defect detection, including automatic reading of characters (OCR) based on a pre-trained AI inference network. Combine the broad range of traditional vision tools with powerful AI Classification or Object Detection models created in Astrocyte™, Teledyne DALSA’s GUI-based AI Trainer software.
BOA3 models with 1.2, 5MP, and 12MP monochrome sensors are available immediately. Color versions are planned for release at the end of 2024. New sensor and lens options will be added to the platform in 2025.
Teledyne DALSA
www.teledynedalsa.com/imaging
Nikon’s Scatter Correction CT
Nikon Metrology NV (Nikon Metrology), a subsidiary of Nikon Corporation (Nikon), has announced the launch of Scatter Correction CT, a software solution designed to address the challenges posed by X-ray scatter artifacts in industrial computed tomography (CT) scanning. By employing advanced physics-based modeling techniques, Scatter Correction CT significantly improves image clarity and measurement accuracy, particularly for dense materials such as aluminum, steel, ceramic, and Inconel.
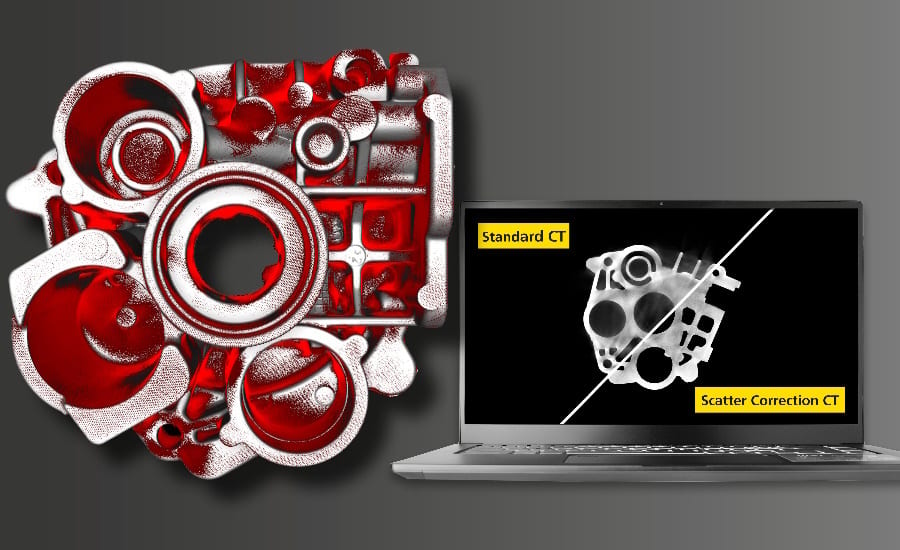
X-ray scatter artifacts have long been a significant issue for CT scan operators, hindering their ability to obtain clear images of internal and external structures. X-rays, like visible light, typically travel in straight lines but are sometimes absorbed and re-emitted, which can change the direction of travel. This issue can manifest as cloudy haloes surrounding high-density regions, false inhomogeneities within homogeneous regions, and edge blurring across material boundaries. Scatter Correction CT effectively simulates and corrects these complex interactions, removing the detrimental effects of scatter.
Key benefits of Scatter Correction CT include:
- Enhanced image clarity: By correcting for X-ray scatter artifacts, Scatter Correction CT dramatically improves image quality, enabling more precise visualization of internal and external structures, defects, and fine details.
- Improved measurement accuracy: More precise and reliable measurements of component geometries and internal features, critical for quality control and Industry 4.0 manufacturing.
- Significantly faster scan times: More than 100 times faster than traditional scatter-free 2D CT methods, allowing manufacturers to significantly improve throughput and accelerate product development.
- Wide compatibility: Scatter Correction CT is available across all Nikon X-ray sources and systems in the 225 kV and above range and is fully compatible with all Nikon CT scanning acquisition modes, providing a versatile solution for diverse industrial applications.
- Ease of use: The correction is seamlessly integrated into the scanning workflow, requiring only a single click to enable. This reduces the need for specialized skills and improves overall productivity.
Scatter Correction CT substantially benefits various industries, including aerospace, automotive, additive manufacturing, and castings.
“We are excited to introduce Scatter Correction CT, a game-changing solution that addresses a critical challenge in industrial CT scanning,” said Nikon’s X-ray and CT Global Product Manager Dr. Andrew Mathers. “By correcting for X-ray scatter artifacts, our software provides manufacturers with significantly better image quality and measurement accuracy in their CT scans, ultimately enhancing quality control, product development, and research capabilities.”
Nikon is actively reaching out to existing customers to showcase the advantages of Scatter Correction CT. New customers are encouraged to contact their local Nikon representative to arrange a demonstration and discuss how this innovative software can benefit their specific applications.
Nikon Metrology, Inc.
www.nikon.com
Gardco Viscosity Calculator, Psychrometric Calculator Apps
Paul N. Gardner USA (Gardco) announced two new custom Gardco mobile apps to enhance efficiency and precision, the Gardco Viscosity Calculator App and the Gardco Psychrometric Calculator App.
James Fusco, Product Manager for the Paul Gardner Company, stated, “These mobile applications feature user-friendly interfaces, real-time data access, and time-saving functions, making it easier than ever to perform complex calculations on the go”. Ideal for professionals in manufacturing, HVAC, material science, and more, both apps ensure accuracy and efficiency while minimizing time and reducing errors.
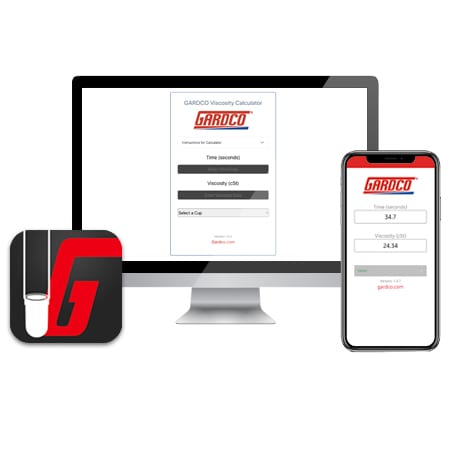
Designed specifically for those who need to quickly and accurately calculate kinematic viscosity or drain time, the Gardco Viscosity Calculator App eliminates the guesswork in determining fluid behavior under various conditions. Whether users are working with paints, coatings, or other viscous materials, this app makes it easy to input variables such as drain time or viscosity along with choice of cup and the app automatically populates the remaining variable. The app’s intuitive interface simplifies complex calculations eliminating the need for manual tables or spreadsheets. The Viscosity Calculator App is particularly useful in quality control environments, research labs, and production settings where precision is critical. Whether you are evaluating batch consistency or fine-tuning product formulations, this tool delivers with the most accurate data right to your fingertips.
- Easy to use desktop and mobile versions available
- Fast and Efficient, saves time and money
- Data for 50+ viscosity cups to choose from
The Gardco Psychrometric Calculator App makes it easy to calculate the inter-relationship of air temperature and moisture content with dew point and wet bulb temperature, as measured by a psychrometric thermometer. In the paint and coatings industry, understanding psychrometric conditions is crucial, as humidity and dew point directly impact paint application quality. Simply fill in the dry bulb field and either the wet bulb or dew point field, and the app will instantly calculate the remaining value. Its simple interface ensures that even complex calculations are accessible to all users, making it an essential tool for fieldwork and quick decision-making, reducing the margin for error.
- Simple and easy-to-use
- Fast and accurate calculations
- Desktop and Mobile versions available
Both the Gardco Viscosity Calculator and Psychrometric Calculator apps are available for download now on the Apple App Store and Google Play Store. Search for "Gardco Viscosity Calculator" or "Gardco Psychrometric Calculator" to start improving your workflow and streamline essential calculations today.
Paul N. Gardner Company (Gardco)
www.gardco.com
Kawasaki Collaborative Robots
Kawasaki Robotics CL Series intelligent collaborative robots (cobots), available for order in multiple payloads, and the new industrial robotic solutions featured for applications such as welding, machine tending and material removal give manufacturers limitless flexibility and advanced capabilities when choosing automation to meet their diverse needs.
“Kawasaki Robotics is committed to delivering the advanced automation technology manufacturers need to maintain production schedules without having to compromise quality or safety,” said Seiji Amazawa, president, Kawasaki Robotics. “We lead the robotics industry by collaborating with innovative partners such as AMT, Hurco, Wauseon Machine and NEURA Robotics, integrating our technology with theirs to harness the best in human ingenuity.”
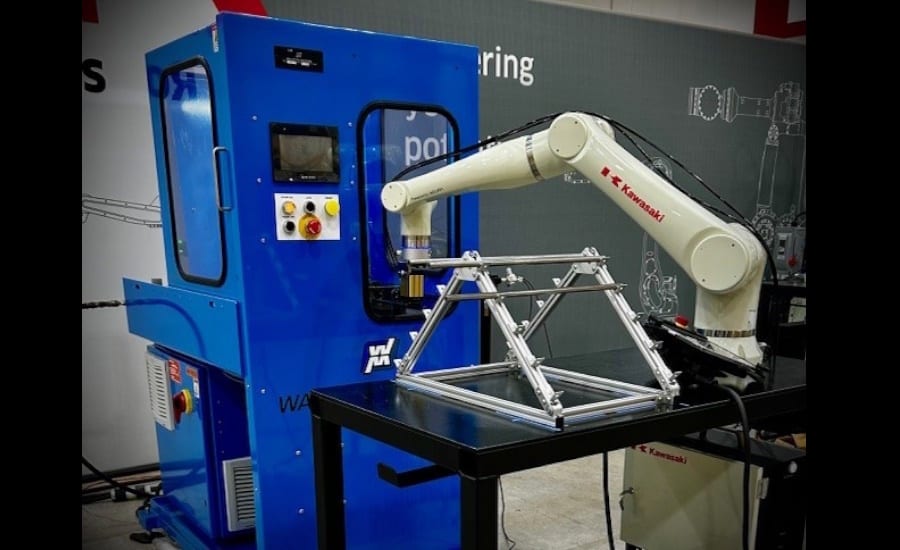
Developed in partnership with NEURA Robotics, the CL Series cobots challenge the current understanding of collaborative robots, offering full-on industrial scale performance and speed paired with maximum protection without compromising the safety and flexibility advantages of human/robot collaboration. Compact and robust, using the same durable casing as Kawasaki Robotics’ industrial robot arms, the CL Series cobots can operate without protective covers in crowded and harsh environments that may not be suitable for other cobots. Operating in Zero Gravity (Zero G), the CL Series cobots requires only light guidance and precise adjustments by hand to create highly efficient solutions for applications such as machine tending and welding.
“With our CL Series cobots, we’re entering a new era of collaborative automation,” Amazawa said. “By providing advanced capabilities along with industrial scale performance and speed as standard features, we boost productivity, improve product quality and worker safety, and reduce rework requirements. Our entirely new way and agile approach to collaborative robots enables manufacturers to more easily address labor shortages while yielding excellent return on investment.”
The CL Series cobots support a variety of payloads and reach from 3 kg/590 mm to 10 kg/1000 mm, with higher payloads such as 15kg expected to hit the market within the next year. Built with high-quality components such as integrated 24-bit encoders, the CL Series operates with industry-leading speed of 200°/s and a repeatability of +/– 0.02 mm. The intuitive user interface makes automating production lines easier than ever before. Free mounting orientations, extremely small footprint, and IP66 classification provide unparalleled flexibility. The proprietary safety architecture includes such features as limits and collision detection, enabling CL Series cobots to operate reliably alongside human workers.
Kawasaki Robotics
https://www.kawasakirobotics.us/