Guest Column
Praveen Gupta
Guest Column | Praveen Gupta
Attracting and retaining a quality workforce is the number one issue for the manufacturing sector.
Manufacturing Needs Focus on Excellence
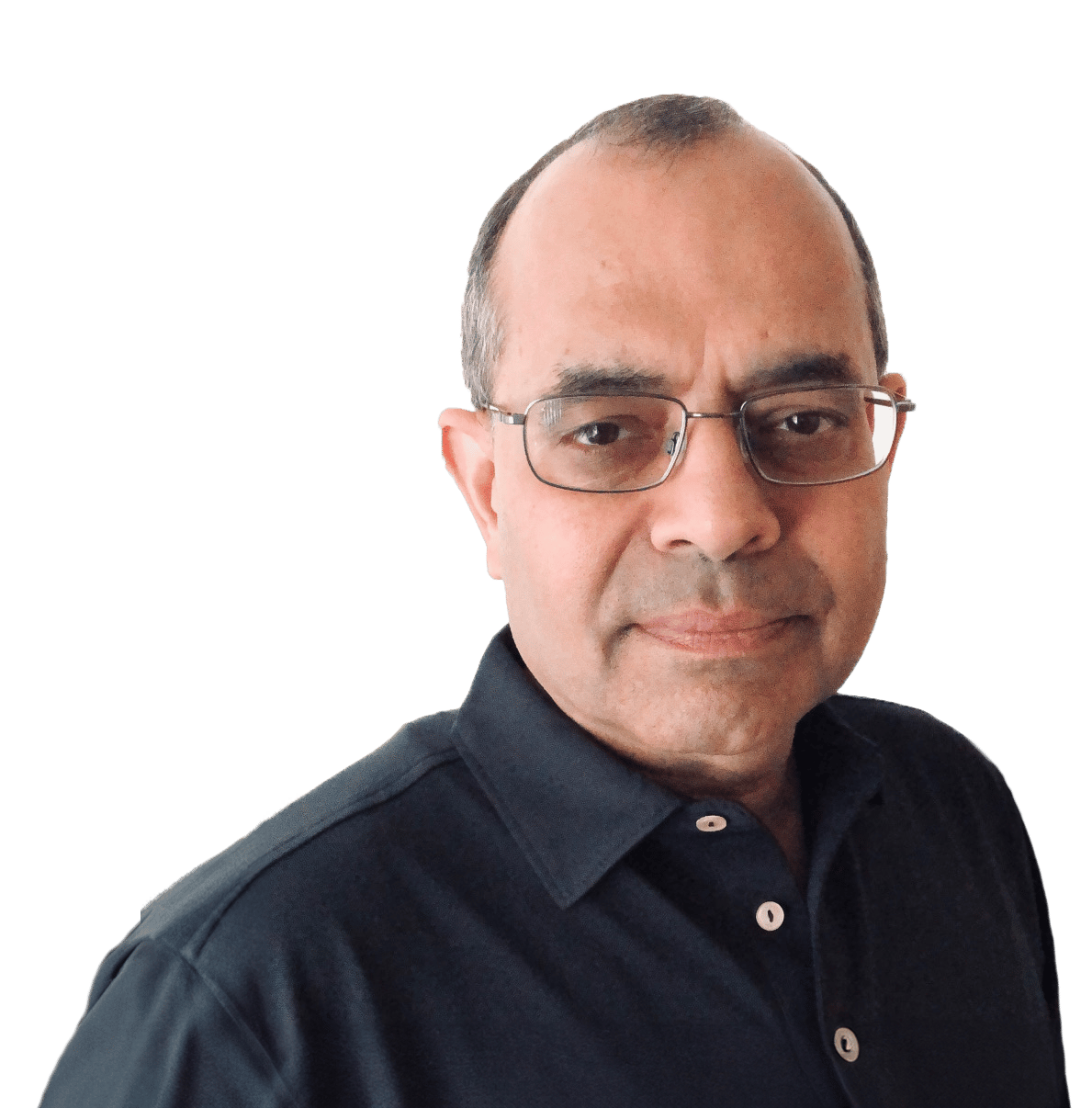
Reports have been published about bringing manufacturing back to the USA for many years. However, we do not feel that manufacturing is back based on our visits to local department stores such as Macy’s, JC Penny, or Saks, hardware stores like Home Depot or Ace Hardware, office supply stores like Staples or Office Max, or other small retail stores alike. It is rare to find anything made in the USA anymore.
I decided to look for some national voices in manufacturing. I visited the NAM (National Association of Manufacturers), with about 14,000 member companies employing about 13 million people. NAM raises the manufacturer’s voice at the government level and drives the nation’s priorities for manufacturing. Since 2020, NAM has been active in pursing the return of manufacturing to the land.
The U.S. Government has also been busy promoting manufacturing in the U.S. The Department of Commerce Economic Development has announced 31 Regional and Innovation & Tech Hubs in various industries as shown below:
According to the government, major companies have committed investments over 500B in Cleantech Energy, 230B in Semiconductors, 140 in Electric Vehicles and over 20B in Biotechnology.
The NAM Annual Report highlights various issues related to the manufacturing industry. The key findings include: workforce challenges, regulatory onslaught, tax policies, operational and supply chain resiliency, artificial intelligence (AI), protecting intellectual property (IP), healthcare supply chain, recruitment & retention, and manufacturing employment. Attracting and retaining a quality workforce is the number one issue for the manufacturing sector.
Workforce development seems to be a critical issue to elevate the manufacturing skillset. This includes sharing best practices, developing technical skills and other skills. These are solutions to various causes of loss of manufacturing.
However, I haven’t seen any research showing why we lost the manufacturing edge. Without knowing the cause of losing manufacturing from the U.S. to abroad, any tax incentives, investment incentives or other boosting acts to promote manufacturing will eventually suffer from the same cause as earlier and will start the next wave of manufacturing departure.
As manufacturing was evolving, so were the customer expectations, and thus the advances in quality control.
In my experience in the mid-‘80s the outsourcing of manufacturing started due to the poor quality, or lower yields, and the strength of the dollar internationally. We could not fix our quality problems, so we shipped the production abroad for improvement in yields and production at lower wages for lowering the product cost.
My research in 2006 showed that loss of manufacturing for poor quality was pervasive, thus it might be an old principle ingrained in American culture. Further analysis led me to the quality principles developed in the late 19th century or the early 20th century. In those times, the quality thinking was more geared towards product quality. As manufacturing was evolving, so were the customer expectations, and thus the advances in quality control. After inventing SPC (statistical process control) concepts, Walter Shewhart of AT&T developed OCAP, out of control action plan to bring the process back in statistical control. This was followed by Ed Deming’s PDCA (Plan, Do, Check, Act) model to ensure product quality. It meant to plan to produce a number of items to leading to the customer required number of units at a certain failure rate of yield. Shewhart and Deming’s work was a great U.S. asset during and post-world war era.
To rebuild Japan and its manufacturing, Deming was assigned to Japan for quality. Kaoru Ishikawa, a professor at the University of Tokyo, developed the Fishbone Diagram to conduct root cause analysis and improve a process. The challenge was still the concept of producing acceptable output within allowed specifications. This was further studied by Genichi Taguchi, an engineer who developed methods to improve quality. He developed methods to improve the quality of products in design. He must have figured out that many of the manufacturing quality problems were related to its design. He developed, so called, the off-line quality methods, for optimizing designs. He articulated the intent of quality to produce on target, not within specifications.
We already know that Juran’s focus was on excellence through execution and Deming’s focus reduction in variability. Integrating all the improvements in parts of the PDCA resulted in the 4P (Prepare, Perform, Perfect and Progress) model for process management. With this model the yields could be aimed and produced at virtually perfection levels.
Now, the challenge is not limited to developing new tools, or developing skills, instead it is the challenge of changing American culture to aim for excellence irrespective of being the largest economy, the richest society, etc. In the corporate world, we have been developing employee skills in basic math, reading, SPC, communication, teamwork, Design for manufacturability, reading drawings/prints, Lean, Six Sigma, TQM, ISO 9001, etc. The real challenge is to change the state of mind of people in America from the White House down to any house, school, university, or for-profit or not-for-profit organizations. Acceptability means mediocrity and rewards ‘C’ grade in education. Eradication of mediocrity would require leadership at top down, bottom up, middle out in every institute in America. Since it is fundamental to our success as a society, we need this inculcated as a child, taught and reinforced in education, required at work, and practiced in life.
Whether it is National Association of Manufacturers (NAM), Manufacturers or Service Providers, Department of Education or Commerce, Academia, AIAG (Automotive Industrial Action Group), ASQ (American Society for Quality), SME (Society of Manufacturing Engineers) or any other organizations, we need to figure out how to create the quality state of mind, which is striving for perfection, or performing to a target, right on the money instead of in the ball park.