Column
Jeromy Peterson
Column | Jeromy Peterson
By integrating extensive data and employing advanced analytics, digital twins help predict potential issues, optimize processes, and ensure consistent product quality.
Enhancing Quality Management in the Automotive Industry with Digital Twins and Augmented Reality
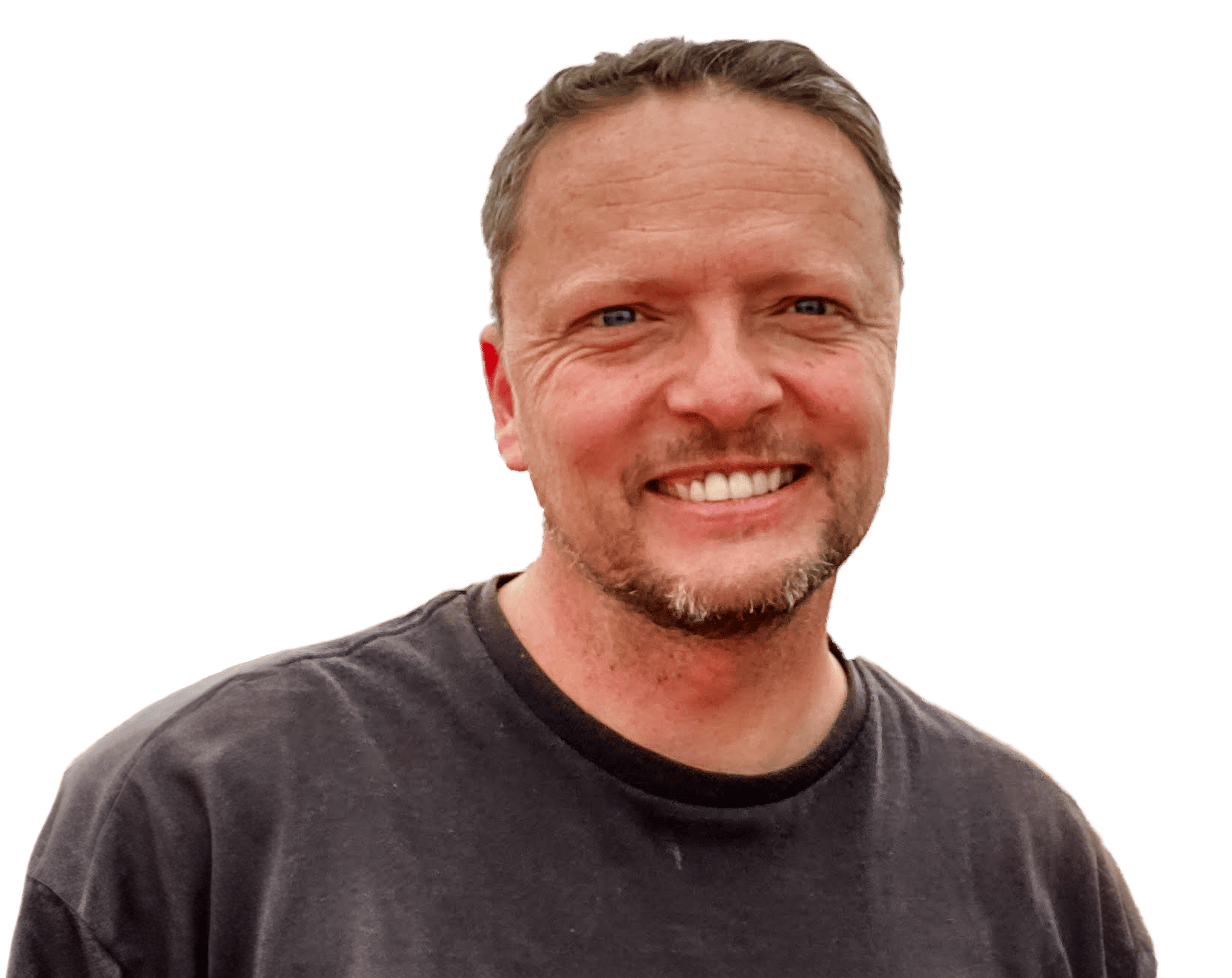
The automotive industry is at the cutting edge of technological innovation, striving to produce vehicles that are increasingly safe, reliable, and efficient. Maintaining high quality standards is crucial, as even minor defects can have serious safety consequences. Digital twins and augmented reality (AR) are two transformative technologies revolutionizing quality management in this sector. This article examines how these technologies are reshaping quality control, along with the challenges they pose.
Understanding Digital Twins and AR in Automotive Manufacturing
A digital twin is a real-time virtual replica of a physical asset, process, or system, continuously updated with data from sensors. In automotive manufacturing, digital twins can represent anything from individual components to entire production lines. By integrating extensive data and employing advanced analytics, digital twins help predict potential issues, optimize processes, and ensure consistent product quality.
Augmented reality, meanwhile, overlays digital information—like 3D models or data visualizations—onto the real world, enhancing the user’s perception. Combined with digital twins, AR becomes a powerful tool for real-time quality management, allowing technicians and engineers to interact with digital models and data intuitively.
Applications in Automotive Quality Management:
Predictive Maintenance and Quality Control
In automotive manufacturing, machinery must operate flawlessly to produce high-quality vehicles. Digital twins enhance predictive maintenance by monitoring machinery in real-time, predicting component failures, and scheduling maintenance proactively. This approach minimizes downtime and reduces the risk of defects in the final product.
When integrated with AR, maintenance technicians can use AR devices to overlay the digital twin of machinery onto the physical equipment. This enables them to view real-time performance data, identify wear and tear, and follow step-by-step maintenance instructions, all within their field of view. This integration not only improves maintenance accuracy but also boosts efficiency and safety.
Process Optimization
Digital twins are also vital for optimizing manufacturing processes. By modeling and analyzing production workflows, automakers can pinpoint bottlenecks and inefficiencies. For example, a digital twin of an assembly line might show how adjustments to robotic arm timings or resource allocation can enhance throughput and quality.
AR complements this by offering engineers and operators real-time, interactive visualizations of the production process. For instance, AR can highlight inefficiencies directly on the assembly line, enabling immediate adjustments. This real-time interaction speeds up decision-making and ensures precise implementation of changes.
Enhanced Traceability and Compliance
The automotive industry faces stringent regulations for safety, emissions, and quality. Digital twins improve traceability by providing a real-time view of the entire manufacturing process, from raw materials to finished vehicles. This transparency aids in meeting regulatory standards and responding effectively to quality issues, such as recalls.
AR further supports traceability by allowing inspectors to visualize the production history of a component or vehicle on the factory floor. By pointing an AR device at a component, inspectors can access detailed records and compliance documentation instantly, streamlining audits and enhancing accuracy.
Digital twins are vital for optimizing manufacturing processes.
Challenges and Considerations
Despite their benefits, implementing digital twins and AR in automotive quality management involves challenges. Significant investment is required for infrastructure, data management, and skilled personnel. Data security and privacy concerns also need to be addressed, as both technologies rely on continuous information exchange between physical and virtual systems.
The effectiveness of digital twins and AR depends on the quality of the data they use. Inaccurate data can lead to flawed simulations and predictions, potentially compromising quality management. Thus, robust data collection and processing systems are essential.
The Future of Digital Twins and AR in Automotive Manufacturing
As digital twin technology and AR evolve, their applications in automotive quality management are expected to grow. Advances in artificial intelligence and machine learning will enable more sophisticated simulations and predictions, while improvements in AR hardware will enhance usability. As the cost of sensors and AR devices decreases, these technologies will become more accessible, broadening their benefits.
In conclusion, digital twins and augmented reality are powerful tools for advancing quality management in the automotive industry. They enable real-time monitoring, predictive analytics, and interactive process optimization, offering substantial rewards in quality, safety, and competitiveness for those who invest in these innovations.