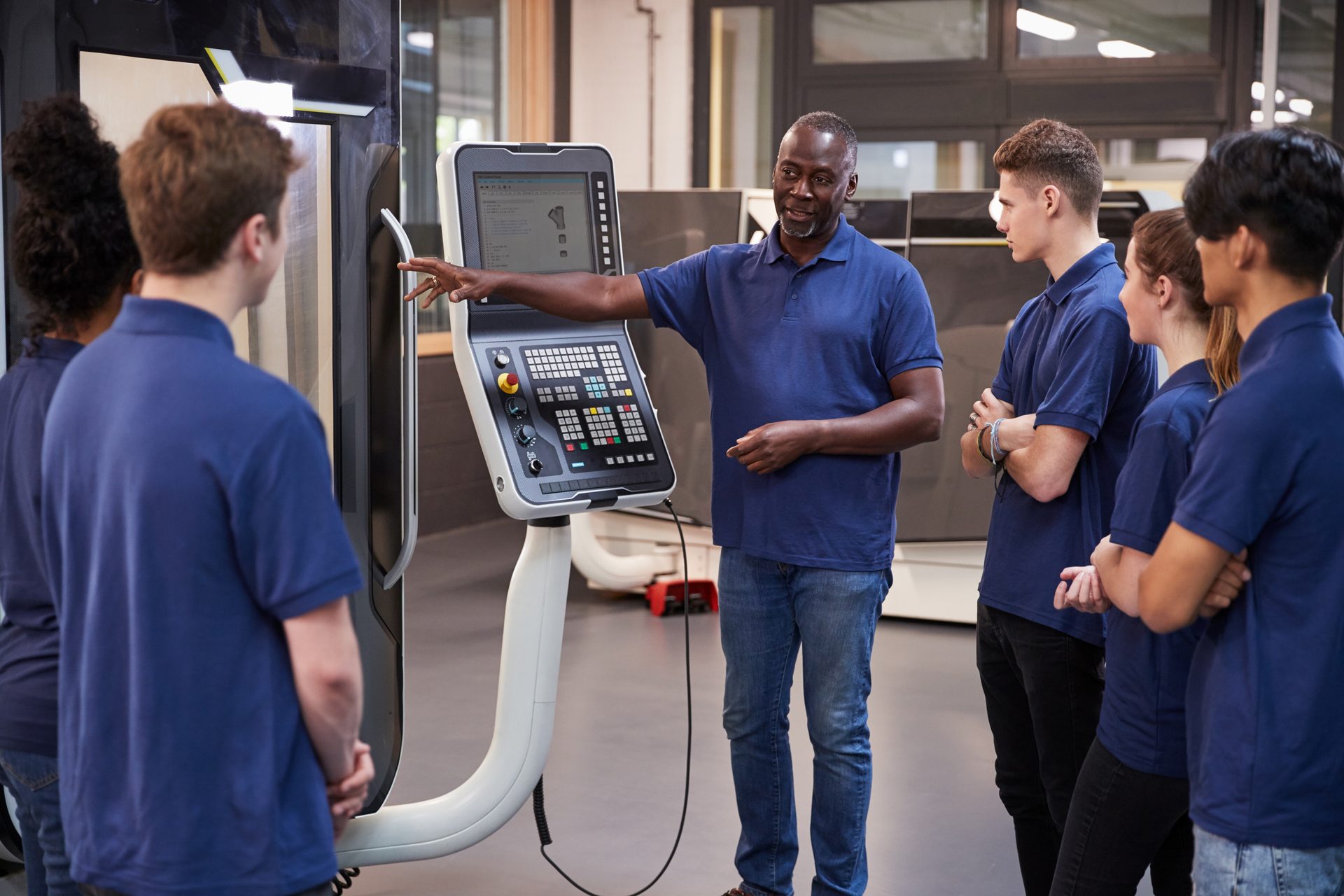
Management
Training programs paused during the pandemic, but manufacturers are upping their game to attract workers. By Genevieve Diesing
COVID Has Not Helped the
Skills Gap
Manufacturers accounted for 11.39% of the economy’s total output in 2018, as plants across the country created more than $2.3 billion in product output for a wide range of industries and consumers, according to the National Association of Manufacturers (NAM).
Despite offering workers an average annual compensation of $84,832 in 2017, manufacturers struggle to fill positions. A 2021 study by Deloitte and the Manufacturing Institute (MI) forecasts that 2.1 million manufacturing positions will go unfulfilled by 2030. These empty positions could cost the nation about $1 trillion in GDP.
It has become such a predicament that Executive Order 13806 was signed to address it, says Josh Worthley, metrology instructor, The Institute for Advanced Learning & Research. This order launched initiatives including the National Imperative for Industrial Skills, led by the Industrial Base Analysis and Sustainment office of the Department of Defense.
With many baby boomers retiring and lack of training equipment and technology in Career Technical Education (CTE) programs, manufacturers have difficulty finding workers with the right skills, says Kimberlee A. Humphrey, president and CEO of Association for Manufacturing Excellence (AME).
“Every business leader will agree that finding not only the right people, but people with the right skills and mindset, is a serious challenge for enterprise,” Humphrey says.
The Great Resignation has only fueled this problem.
“In a very tight labor market, the competition for workers has become intense, especially locally, with manufacturing competing in ways that it has not before with nontraditional players,” says Gardner Carrick, vice president of Workforce Solutions at the Manufacturing Institute.
While job openings are even more prevalent than before the pandemic, it is difficult to find employees in the trades and with science, technology, engineering, and math (STEM) skills.
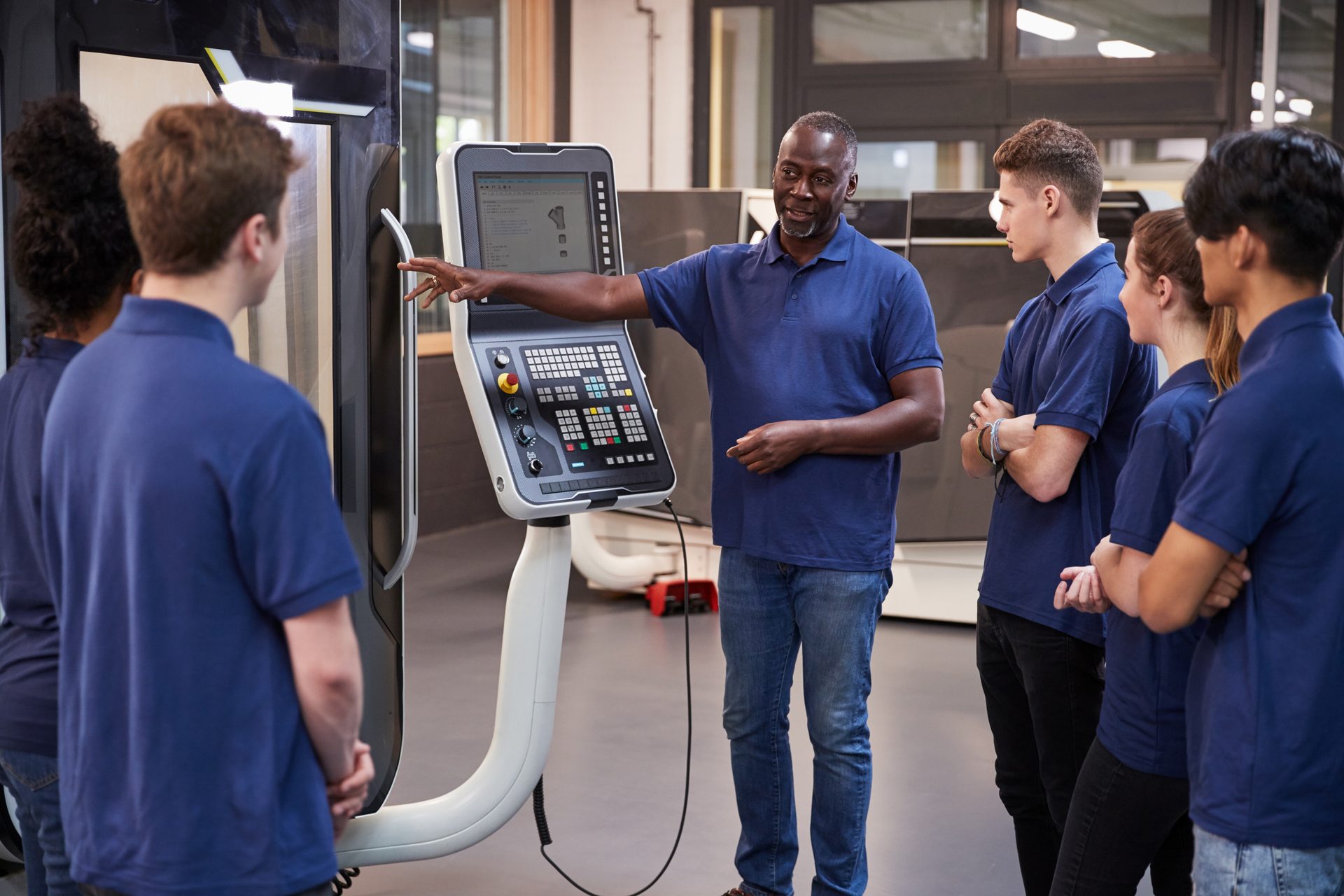
“This ranges from engineers, quality inspectors and software developers to machinists, mechanics and welders, and the educational requirements vary by occupation,” Carrick says. “Some require advanced degrees, but many of these roles require less education, with credentials and apprenticeships being more important.”
In such an environment, leaders and hiring managers should not get hung up on traditional education requirements, experts say.
“Using a four-year degree as a proxy for employability means relying on talent with potentially redundant skills rather than lifelong learners with ever-relevant skills. It hurts us all, too – because our current over-reliance on college degrees further alienates already vulnerable jobseekers,” says Humphrey.
Employees looking to work in the field need a STEM background as well as mechanical skills. This could come in the form of a high school diploma with experience and technical training at the minimum, or a completed registered apprenticeship, Humphrey says. They would also do well with critical thinking skills and an associate degree in a technical trade or with foundational skills in reading, writing, math and science.
“Looking across the manufacturing environment and the implications from COVID to the economy, there are movements in what is required in terms of skills,” says Wanda Sturm, Chair, ASQ Technical Communities Council, ASQ Board of Directors member and 2024 ASQ Chair-elect.
“Lack of stability in the supply chain and the ongoing demand for products impact the quality of products. In addition, organizations are doing more with less personnel which impacts safety, productivity rates, time available to advance skills and ensure internal communication is effective.”
Based on ASQE’s Insights on Excellence benchmarking for 2020-2021, most manufacturers require three technology-based skills of their staff:
- Experience with big data and analytics,
- Cloud computing, and
- Software integration.
Artificial intelligence and machine learning know-how are part of these skills, Sturm adds.
The resolution of the skills gap depends on intentional partnerships between industry and the entire educational chain, Worthley says.
“If there was ever a call to action for our manufacturing future, consortiums of industrialists need to support and engage all their local academic partners for the betterment of the whole,” he explains.
Carrick echoes this. “Manufacturers need to play a central role in solving these challenges,” he says. “On the training side, this includes strengthening partnerships with their colleges and training providers through apprenticeships, internships, co-ops, and other opportunities that enable students to experience work in a manufacturing company and learn from current manufacturing employees.”
The pandemic also contributed to the loss of manufacturing workers. Jobs were lost during the beginning of the crisis, but were not refilled at steady rates as workers returned to the office — or shop floor.
Training was impacted, too. COVID forced many companies and training providers to develop creative alternatives to the traditional in-person training methods, Carrick says.
“Virtual reality training options have expanded significantly, and many programs are now using a blended or hybrid approach to technical training,” he says. “Even as COVID abates, these new models will likely become a permanent feature for many training programs.”
On the recruiting front, COVID greatly expanded the remote work model in many industries. This is not an option for many manufacturing positions, Carrick says, but companies are now looking at flexible shifts and other work arrangements to recruit people looking for a non-traditional schedule.
During COVID, training in CTE, high schools, and community colleges paused, Humphrey says. “We had a pipeline pause occurring at the same time of mass retirements and resignations. The talent pool decreased, and we are now trying to work our way back to attracting craftsman to the trades training.”
Manufacturing has been hit hard and the challenge is not over, Sturm says.
“The world is continuing to change daily as we witness change in the earth’s environment, change in individual needs, and growth in technology,” she says. “Producing goods and services to meet the demand becomes increasingly more difficult.”
With this in mind, Sturm says, it is incumbent on organizations to review their approach.
Manufacturers can also raise wages and improve culture to attract workers, Carrick says.
“Companies have told us that they have needed to increase base wages several times over the past couple years to remain competitive locally, and nationally, average hourly earnings for production workers have risen 5.2% over the past year, near a 40-year high,” Carrick says.
“The company’s culture also matters in this conversation,” he adds. “In the aftermath of COVID-19, health and safety, a family atmosphere and work-life balance are also important for both existing and prospective workers.”
While manufacturers will continue to face significant challenges with attracting and retaining workers, there is a light at the end of the tunnel, Carrick says.
“Manufacturers have differentiated themselves from their competitors,” he says, “highlighting their excellent pay and benefits, focusing on how they contribute to a better world, and stressing that a manufacturing job provides an avenue for a successful career.”