paragraph style text goes here
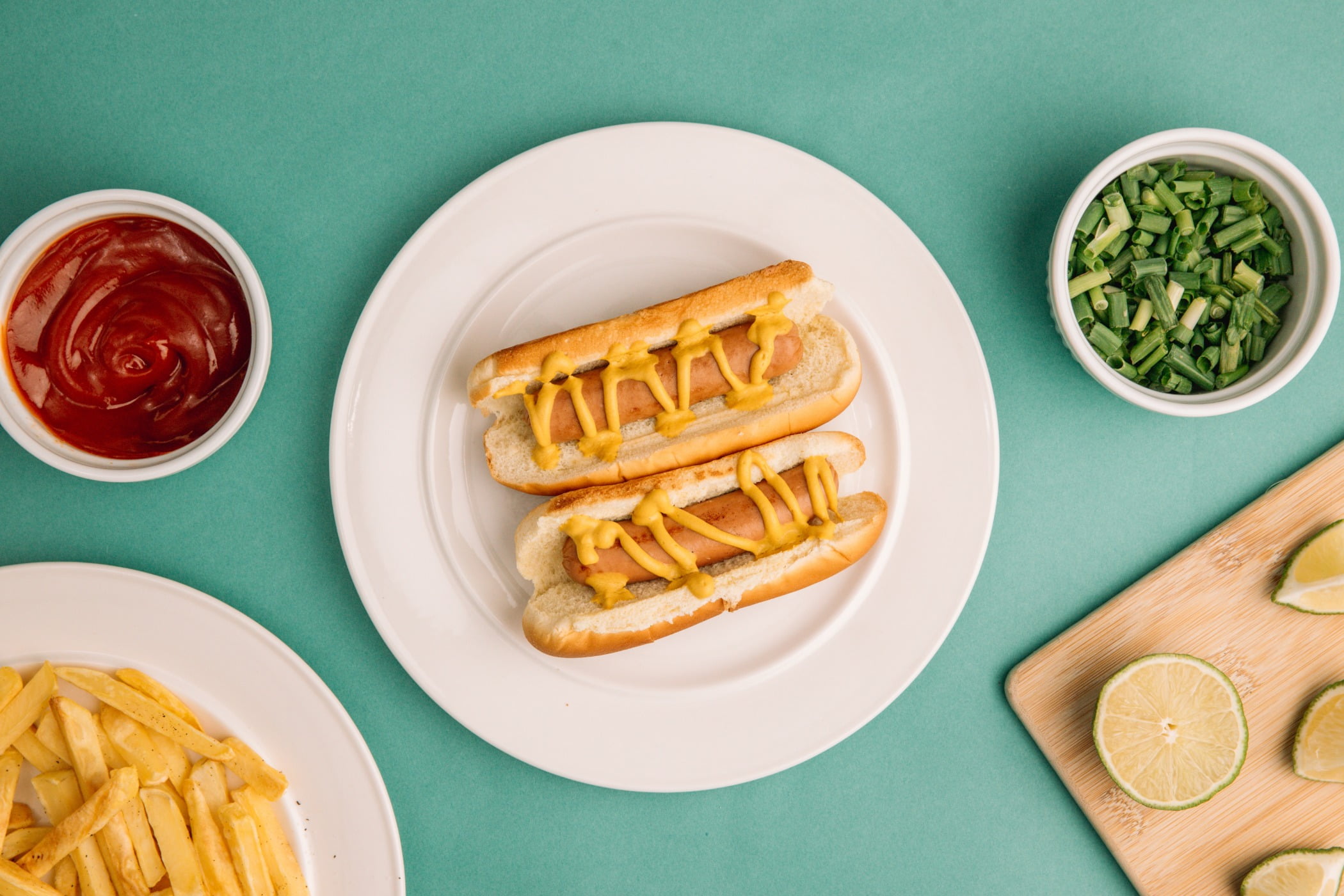
H1 headline goes here
H1 headline goes here - NO IMAGE
paragraph style text goes here
Missouri Protoplex Partners with Solvus Global
Solvus Global, a leader in advanced manufacturing headquartered in Massachusetts, has become the first major company to partner with the Missouri Protoplex at Missouri University of Science and Technology. The company signed a lease Wednesday, April 2, at the Missouri S&T campus to establish an additional facility in Rolla.
The mission of the Protoplex, which is set to open in spring 2026, is to improve workforce and economic development for the area and the state through advanced manufacturing by providing a variety of resources and skills to manufacturers.
“We are thrilled to welcome Solvus Global to our community,” says Dr. Richard Billo, director of S&T’s Kummer Institute Center for Advanced Manufacturing and Missouri Protoplex. “Their decision to establish a location here is a testament to the success of our initiatives, and it will create numerous new job opportunities within the industry.”
Solvus Global is dedicated to solving complex industry challenges by building businesses around sustainable manufacturing solutions. Once their location at the Protoplex is complete, Solvus will work alongside university experts and industry leaders in the shared manufacturing space, facilitating research, development and real-world applications of advanced manufacturing technologies.
“Dr. Richard Billo and the S&T team have been invaluable partners over the years,” says Dr. Aaron Birt, co-founder and CEO of Solvus Global. “We’re aligned with Chancellor Mo Dehghani's plans for the Kummer Institute having world-class manufacturing research. We see tremendous potential in Rolla, and we’re eager to contribute to its growth as a key manufacturing hub.”
Solvus Global plans to establish its presence at the Protoplex by onboarding an initial team of five employees and steadily expanding from there. The next phase will focus on identifying optimal manufacturing operations, securing the right facilities and recruiting people to drive growth.
“It will open more positions. — not just engineers, but technicians,” Billo says. “They've seen the quality of students that we have here.”
Birt says that additive manufacturing has been a core component of engineering curricula with hundreds of graduates entering the field each year, and that by using the existing workforce and integrating robotics, automation and 3D printing, they can enhance efficiency and competitiveness in the industry.
“That’s why the synergy between Solvus Global and the Missouri Protoplex is crucial for the ecosystem,” Birt says.
For more information, visit solvusglobal.com/careers or protoplex.mst.edu.
Mazak Names Bates VP of Sales and Regional Operations
Continuous innovation in manufacturing technology and a steadfast commitment to customer support have long been central to Mazak’s business strategy. Consistent with that strategy, the company has promoted Kevin Bates to Vice President of Sales and Regional Operations.
With more than 30 years of leadership experience in the machine tool industry, Bates will now oversee Mazak’s six U.S. regions as well as operations in Canada. He will also continue to lead the company’s SYNCREX Swiss-style turning machine product group.
“Kevin’s experience and leadership has proven invaluable to the company throughout his career at Mazak,” said Dan Janka, President of Mazak Corporation. “With his successes in the Midwest, we are confident in his abilities to ensure all regions continue to provide the utmost in service and support to customers along with the technology they need for increased productivity and business success.”
Following Bates’ promotion, Mazak has also appointed Randy Ragnini as General Manager of the Midwest Region. A proven team builder with decades of industry experience, Ragnini has held a variety of key leadership roles spanning sales, marketing, operations, and technical product development.
For more information, visit www.mazakcorp.com.
Hexagon Supercharges Design, Manufacturing Productivity with Geomagic Software Acquisition
Hexagon has completed the acquisition of Geomagic software business from 3D Systems Corporation, gaining market-leading technology that improves productivity for people that are acquiring, manipulating and reverse engineering 3D measurement data for use throughout the product lifecycle and computer-aided design (CAD) workflows.
Integrated into its Manufacturing Intelligence division, the Geomagic software solutions will be supported and sold to the discrete manufacturing market – complementing portfolios in Hexagon’s other markets such as mining and construction. The suite comprises software for measurement and quality control, mesh and surface model creation, and parametric scan-to-CAD workflows for highly efficient reverse engineering.
Josh Weiss, President at Hexagon’s Manufacturing Intelligence division commented: “We are delighted that Geomagic has joined Hexagon. The software and the team are pioneers in the creation of powerful and intuitive scan-based reverse engineering, inspection and design tools. The suite is imperative to manufacturing industry success, and provides the experience that their global customers, partners and hardware OEMs need.
“We will continue to support all hardware and software partnerships for Geomagic customers. We will invest in developing and supporting this software with our considerable expertise and IP to offer our portable metrology device users greater productivity and new capabilities”
A key aspect of the Geomagic suite is that it works with any 3D scanner or portable CMM. The software supports reverse engineering and metrology workflows with 3D scanning devices from a broad section of optical, laser and LiDAR scanning devices from any vendor, and Hexagon will continue to offer all global customers continued access to the full software portfolio and support native CAD and PMI data import from Dassault CATIA, PTC Creo, Autodesk Inventor, Siemens NX, and Dassault SOLIDWORKS.
Geomagic Design X is a comprehensive and accurate 3D scan-to-CAD solution for reverse engineering and digital documentation of physical parts. Users can reverse engineer data from any scanner, with intuitive guided workflows that provide accurate conversion and recreation of parametric CAD. Design X features powerful automated mesh-to-surface functionality where needed – for example in mould and die applications – and complements all CAD software workflows perfectly.
“3D scanning allows us to do things we couldn’t do before because of the complexity of parts. With Geomagic Design X we can create models of parts that were previously difficult to model. Once we got the training, we could model much faster than before.” - Fabien Brunet, Tool Design Technician, Schneider Electric.
Geomagic Control X brings the power of 3D scan-based inspection to more people in more places with industry-leading 3D metrology software that makes it easy to interpret scan data and report results. With strong workflow automation capabilities, Control X provides validated accuracy with NIST, PBT and NPL standards organizations, which Hexagon plans to build upon by integrating its exceptional Hexagon GD&T libraries.
“Doing reports can be very painful, so I looked through the tools Geomagic Control X had to offer and discovered the reporting functionality. It reduced the time I spend on reporting by around 70%. Before I needed about eight hours to make the report, and with Geomagic Control X it takes just three.” - Hazim Abueideh, Quality Control Analyst, air up GmbH.
For more information, visit https://hexagon.com/company/divisions/manufacturing-intelligence/geomagic.
Pharmaceuticals Calibration and Instrumentation Metrologist Honored as 2025 Inspector of the Year from ASQ’s Inspection Division
The ASQ Inspection Division has selected Pharmaceuticals Calibration and Instrumentation’s Metrologist/QA Lead, Fikremariam (Fikre) Woldegiorgis, as the 2025 Chuck Carter International Inspector of the Year. Woldegiorgis will be presented his award and duly acknowledged during the Inspection Division’s annual membership meeting on Monday, May 5, 2025, in Denver, CO, in conjunction with ASQ’s World Conference on Quality and Improvement.
Woldegiorgis has worked at the Pharmaceuticals Calibration and Instrumentation (PCI) in Raleigh, NC, since 2015. Woldegiorgis has extensive experience in calibration and management systems. As a metrologist he performs calibrations, conducts inspections, and provides training on temperature calibration. He is also responsible for leading implementation of PIC’s ISO/IEC17025 quality management system. As a quality lead he performs document reviews, quality auditing, procedure writing, and participates with CAPA activities. He ensures maintenance of the quality management system and inspects end products before reaching the customer.
Prior to joining PCI, Mr. Woldegiorgis worked as a metrologist and held various roles including standards development expert, an auditor to ISO 9001, and was the Quality Manager at Ethiopian Standards Agency.
Woldegiorgis graduated from Asmara University in 1989 with a Bachelor’s degree in Physics and in 2012 earned a Master’s Degree in Geography & Environmental Science from Addis Ababa University. He is an ASQ Certified Calibration Technician (CCT) and an ASQ Certified Quality Technician. Woldegiorgis is the author of two books, High School Physics published by Artistic Printing Press and Laboratory Experiments in High School Physics published by Educational Materials Production and Distribution Agency.
He is a member of ASQ and the American Society for Testing Materials (ASTM). He has been actively involved as an ASQ volunteer helping with CCT exam development and serving as a CCT exam reviewer.
Woldegiorgis lives in Durham, NC. He is married to Zena Takele and has two children Kirubel and Eden. He enjoys travelling, visiting places, attending soccer games, playing chess, watching television and reading.
The Inspection Division has offered the Inspector of the Year Award since 1974. For a list of the previous award recipients, an award application, or additional information about the ASQ Inspection Division and the award, visit https://my.asq.org/communities/files/folder/158/217.
Women in Manufacturing Education Foundation Board of Directors Announced
The Women in Manufacturing Education Foundation (WiMEF) announced the election of members to its 2025 Board of Directors, whose term began on April 1, 2025. WiMEF is a nonprofit organization that provides women with valuable connections, access to career pathways, and best-in-class programming at all stages of their manufacturing careers.
The board is led by Chair Laura Wilde, Vice President of Quality, Ultra Maritime, Braintree, MA; Vice Chair Kate Leiby, General Manager, Power Generation, Donaldson Company, Minneapolis, MN; Secretary Catherine Ross, Director, Community Engagement, AMT -The Association for Manufacturing Technology, McLean, VA; and Past Chair / Treasurer Mary Ellen Grom, Executive Director, Global Marketing & Communications, AFL, Duncan, SC.
New board members commencing their three-year term are:
- Daniele Caserta, Principal, CliftonLarsonAllen, LLP (CLA), Canton, OH
- Jessica Chavez, Training Manager, TRUMPF, Inc., Farmington, CT
- Heidi DeMello, Senior Vice President Supply Chain, Blount Fine Foods, Fall River, MA
- Michele Loo, Chief Diversity Officer, Linde Canada, Inc., Danbury, CT
- Sabrina Richmond, Vice President Mission Assurance, Mercury Systems, Hudson, NH
- The new board member commencing her one-year term is:
- Jane Thomas, President, Teijin Holdings USA, Inc., Teijin Limited, Sausalito, CA
“I am thrilled to welcome this distinguished group of industry leaders to the Board of Directors,” said WiMEF Executive Director Gretchen Moore. “We rely on our board leaders to provide guidance, insight, and expertise during this season of growth and innovation for both WiMEF and the manufacturing sector.”
The 21-member board of directors supports the organization’s work to build a skilled and resilient manufacturing workforce. WiMEF is the 501(c)3 partner organization to the Women in Manufacturing Association (WiM), the only national trade association dedicated to supporting, promoting and inspiring women in manufacturing.
Members of the WiMEF board who are continuing their three-year term are:
- Tara Ashcraft, Residential HVAC Communications Leader, Trane Technologies, Davidson, NC
- Veronica Braker, Vice President of Operational Excellence, Southwire Company, Decatur, IL
- Kori Carlson, President, Brooklyn Tool, Inc., Minneapolis, MN
- Dr. Maja Durant, Senior HR Director, Greif, Delaware, OH
- Kaytie Elder, IAM/Boeing Joint Apprenticeship Program Senior Manager, Boeing, Auburn, WA
- Dr. Susan Emmerich, Manufacturing Talent Programs Manager, BASF Corporation, Florham Park, NJ
- Stacey Heidbrink, Senior Responsible Care Director, The Dow Chemical Company, Fort Saskatchewan, Alberta, Canada
- Lynn Kier, Senior Director Strategic Communications, Shaw Industries, Charlotte, NC
- Joanna Perz, Global Sustainability Manager, Ingersoll Rand, Davidson, NC
- Steve Speich, Senior Vice President of Enterprise Operations, Winnebago Industries, Inc., Eden Prairie, MN
- Paula Timco, Associate Director, Sherwin Williams, Cleveland, OH
WiMEF’s year-round education programs develop core competencies and durable skills for leaders in the manufacturing industry with a goal of increasing the number of women in leadership roles. Since 2017, more than 1,200 women have graduated from the education programs and more than 20,000 have participated in the Virtual Learning Series.
WiMEF also hosts a bi-annual virtual career fair to connect top talent to leading manufacturing employers throughout the nation.
Moore thanks outgoing members of the WiMEF board for their outstanding service: Vanessa Davis, Novelis; Melissa DeTamble, Ascential Technologies; Mani Khanuja, Amazon Web Service; Shameka Lewis Dempsey, Kellanova; Melissa Rocha, Kymera International; Danielle Schneider, Pridgeon & Clay, Inc.
For more information, visit www.wimef.org and www.womeninmanufacturing.org.
January 2025 US Cutting Tool Orders Hit $199.9M, Up 9.2% From December
Shipments of cutting tools, measured by the Cutting Tool Market Report compiled in a collaboration between AMT – The Association For Manufacturing Technology and the U.S. Cutting Tool Institute (USCTI), totaled $199.9 million in January 2025. Orders increased 9.2% from December 2024 but were down 4.1% from January 2024.
“January was quite soft for most tooling companies, even more so than normal. New investments are on hold, and most shops are only buying what they need to keep spindles turning,” said Jack Burley, chairman of AMT’s Cutting Tool Product Group. “Until the political conditions settle and the uncertainty they create for manufacturing is resolved, I expect to see very little improvement in consumption, especially for small businesses. There are different opinions on the speed at which we can bring more manufacturing back to the United States, so we can only wait and see how companies respond.”
Eli Lustgarten, president at ESL Consultants, said: “Demand continues to suffer from economic uncertainty both here and abroad as well as from the changing political environment, especially with rising tariffs and the impact on supply chains and costs. Most major industrial end markets have become cautious: Heavy manufacturing sectors, including farm, construction, and mining equipment manufacturers, are undergoing substantial inventory liquidation in the first half of 2025. Signs point to a sluggish, if not volatile, first half of 2025. If political conditions and tariffs stabilize, end-market demand may begin to improve in the second half of the year and into 2026 as production increases and inventory liquidation ends.”
The Cutting Tool Market Report is jointly compiled by AMT and USCTI, two trade associations representing the development, production, and distribution of cutting tool technology and products. It provides a monthly statement on U.S. manufacturers’ consumption of the primary consumable in the manufacturing process, the cutting tool. Analysis of cutting tool consumption is a leading indicator of both upturns and downturns in U.S. manufacturing activity, as it is a true measure of actual production levels.
For more information, visit amtonline.org.
Manufacturing Technology Orders Post Strongest January Since 2022
Orders of manufacturing technology, measured by the U.S. Manufacturing Technology Orders Report published by AMT – The Association For Manufacturing Technology, totaled $357.3 million in January 2025, a 29.8% decline from December but a 5.7% increase from January 2024. Compared to an average January, the value of orders placed in January 2025 was 16.2% higher, making it the highest January since 2022. However, the number of units was 12.2% lower than the average January – the lowest level for any January since 2016.
Orders from contract machine shops, the largest customer industry, underperformed the market for much of 2024 but rebounded in the last four months of the year. That momentum did not carry into 2025, with machine shop orders in January declining by nearly one-third from December. While the monthly decline was the largest in any December-to-January period since 2020, the year-over-year decline from January 2024 was half the decline seen between January 2023 and 2024.
Aerospace orders in January hit their lowest monthly order level since the machinist strike at Boeing began in September 2024, coming in at nearly half of December 2024’s level. Despite the decline, orders were up 11% from January 2024, and output increased, indicating the potential for future demand. While the aerospace sector increased output in January 2025, overall manufacturing output fell modestly as output of motor vehicles and parts fell sharply. In this environment of falling output, automotive manufacturers reduced orders in January 2025 to almost two-thirds below their December 2024 levels. While most customer industries saw month-over-month declines, medical manufacturers increased their orders in January 2025 to the highest level since September 2023, underscoring the industry’s growing importance as a manufacturing technology customer.
After the shallow downturn of the last two years, order activity – measured both in value and units – seems to have found a bottom. In the recovery after the manufacturing downturn of 2015 and 2016, the market expanded from its bottom for 31 months to its next peak, which resulted in a cumulative 42% growth in orders. Thus far in 2025, industrial production remains flat, with capacity utilization dipping modestly in January after increasing for the final two months of 2024. If the data begins to show rising capacity utilization in February 2025 and beyond, we can expect order activity to gain momentum as the first quarter of 2025 comes to a close.
While the possibility of a strong opening to 2025 remains in sight, and rising utilization rates generally indicate an impending increase in order activity, Oxford Economics modestly downgraded their global growth forecast recently. They cited the rising uncertainty of global trade, which has caused hesitation among those making capital investments. Although we can see the ingredients for an impressive recovery before us, the actual outcome could be as flat as the table upon which they sit.
For more information, visit www.amtonline.org.
Verisurf Signs Agreement to Be Acquired by Sandvik
Verisurf Software, Inc., announced that it has signed an agreement to be acquired by Sandvik, a global high-tech engineering group providing solutions for the manufacturing, mining, and infrastructure industries. This partnership marks an exciting new chapter for Verisurf, as we join forces with Sandvik to expand our capabilities and continue delivering industry-leading 3D metrology software solutions.
Verisurf will operate as a separate business unit within Sandvik Manufacturing and Machining Solutions, complementing and enhancing Sandvik’s position in industrial metrology. The acquisition is subject to customary regulatory approvals and is expected to close in Q2 2025.
Verisurf’s Founder and President, Ernie Husted, will continue to lead the company, ensuring a smooth transition while maintaining its core mission, vision, and dedication to customer success. Verisurf remains committed to delivering innovative, flexible, and user-friendly metrology solutions, and this partnership with Sandvik will create new opportunities for growth and advancement.
Verisurf extends its sincere gratitude to its dedicated team, whose expertise and passion have been instrumental in the company’s success. Additionally, Verisurf would like to thank its valued customers and partners for their trust and continued support. This milestone represents an exciting step forward, and Verisurf looks forward to the opportunities that lie ahead under the Sandvik umbrella.
“This is an exciting milestone for Verisurf, and we are eager to build on our success with the support of Sandvik. Thank you to our team, customers, and partners for your trust and commitment—we are just getting started,” said Ernie Husted, Founder & President of Verisurf Software, Inc.
For more information, visit verisurf.com.