From the editor
Darryl Seland
From the editor | Darryl Seland
Fail to prepare, fail to succeed.
Preparation
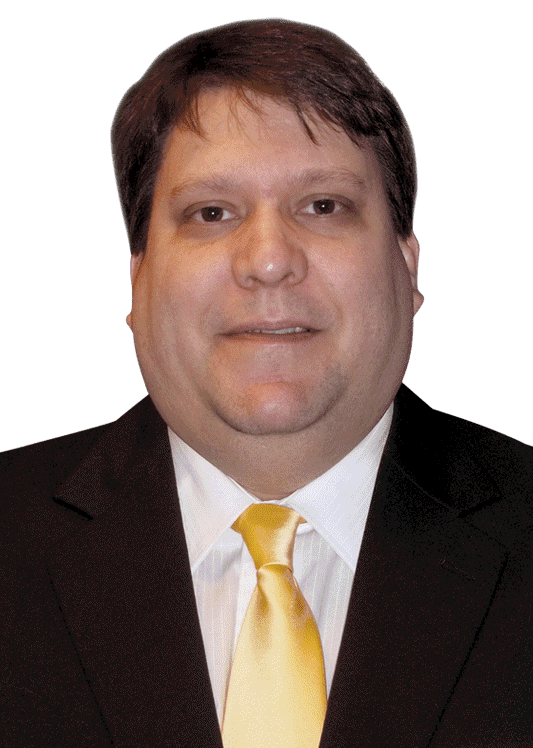
Famous college basketball coach John Wooden said, “Failing to prepare is preparing to fail.” It’s hard to argue with someone who won ten national championships in a 12-year span.
It’s actually an offshoot of a Benjamin Franklin quote, “By failing to prepare, you are preparing to fail.” And I am sure you would have no problem believing these are not the only two famous quotes about preparation. There are plenty, and each inextricably links preparation with success. Many provide a connection between preparation and some less tangible ideas, such as luck and opportunity, and their path to success—a kind of two or three degrees of separation between preparation and success. In any event, again, it’s hard to argue with the thoughts of a 10-time national championship coach on the subject.
After all, why would athletes train and practice for hours on end, why would we stand in front of the mirror practicing that big speech, and why would we study for that big test? So we can get that much closer to the vision for our success, whether it’s winning the big game, nailing that speech, or landing that first job. Practice makes perfect!
“Failing to prepare is preparing to fail.”
Preparation also can put us on the path to solving that big problem. Take for instance the workforce gap in manufacturing. Planning an approach can make all the difference.
As author Kathleen Kosmoski writes, “The manufacturing industry is facing a critical workforce challenge. With a growing skills gap and an aging workforce, manufacturers are struggling to find and retain qualified employees.
“The National Association of Manufacturers reports that 77% of manufacturers are struggling to fill open positions. According to a study by Deloitte and the Manufacturing Institute, the U.S. manufacturing sector could see a shortage of 2.1 million workers by 2030, potentially costing the economy $1 trillion in lost productivity.”
A key to potentially solving this problem could be Registered Apprenticeship Programs. As Kosmoski suggests, “While not the only tool in addressing workforce shortages, apprenticeship programs offer manufacturing companies many benefits.”
As I write this column, The Quality Show 2025 is about to begin in Nashville, and I have been the guy in the mirror practicing his remarks.
So I hope we had a chance to see you at the show. And check out Kathleen’s article, “Registered Apprenticeship Programs Offer Significant Value for Manufacturing Employers” and everything else we have to offer in this month’s Quality.
Enjoy and thanks for reading!