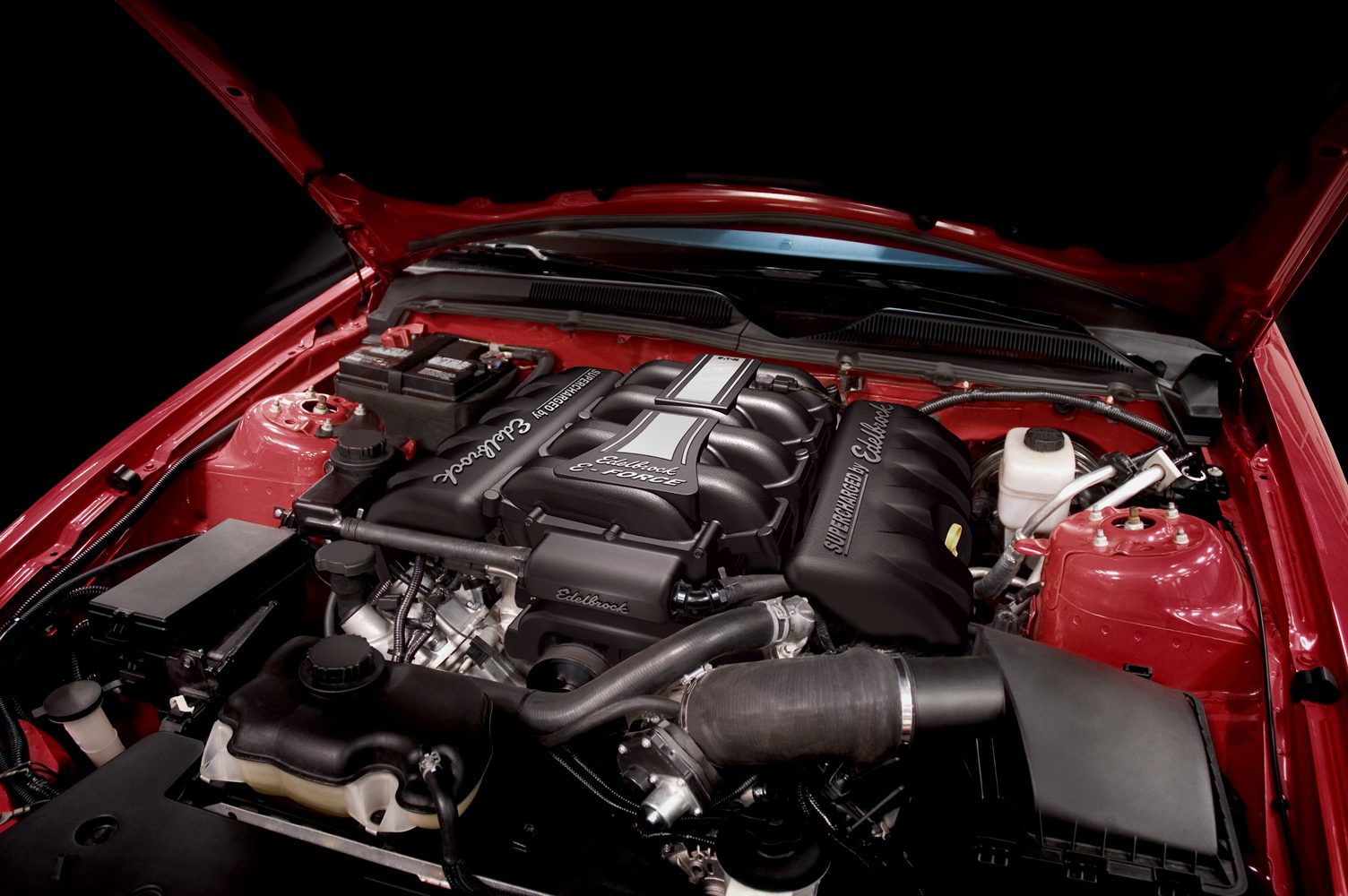
This Case Studies Special Advertising Section features manufacturing companies with real-world challenges using quality equipment, software and services to solve their problems and improve their processes. These problem-solving stories describe myriad manufacturing challenges and how the correct application of a supplier’s product or service made the difference, providing quantitative benefits to quality and manufacturing issues.
The suppliers in this special section present these real-world problems and solutions to help Quality Magazine subscribers who may have similar experiences.
Case Studies
— Special Advertising Section —
Edelbrock Generates High Performance ISO Audits with GAGEtrak®
In 1938, Edelbrock started in a modest four-car repair shop in Los Angeles and today, the Edelbrock name is known worldwide for manufacturing a wide range of high-precision, high-performance engine components. Kevin Brewis, Edelbrock’s Calibration Technician, is responsible for ensuring that the company’s thousands of gages, fixtures and pieces of test equipment are properly managed, tracked and calibrated across five divisions to meet ISO 9001 certification.
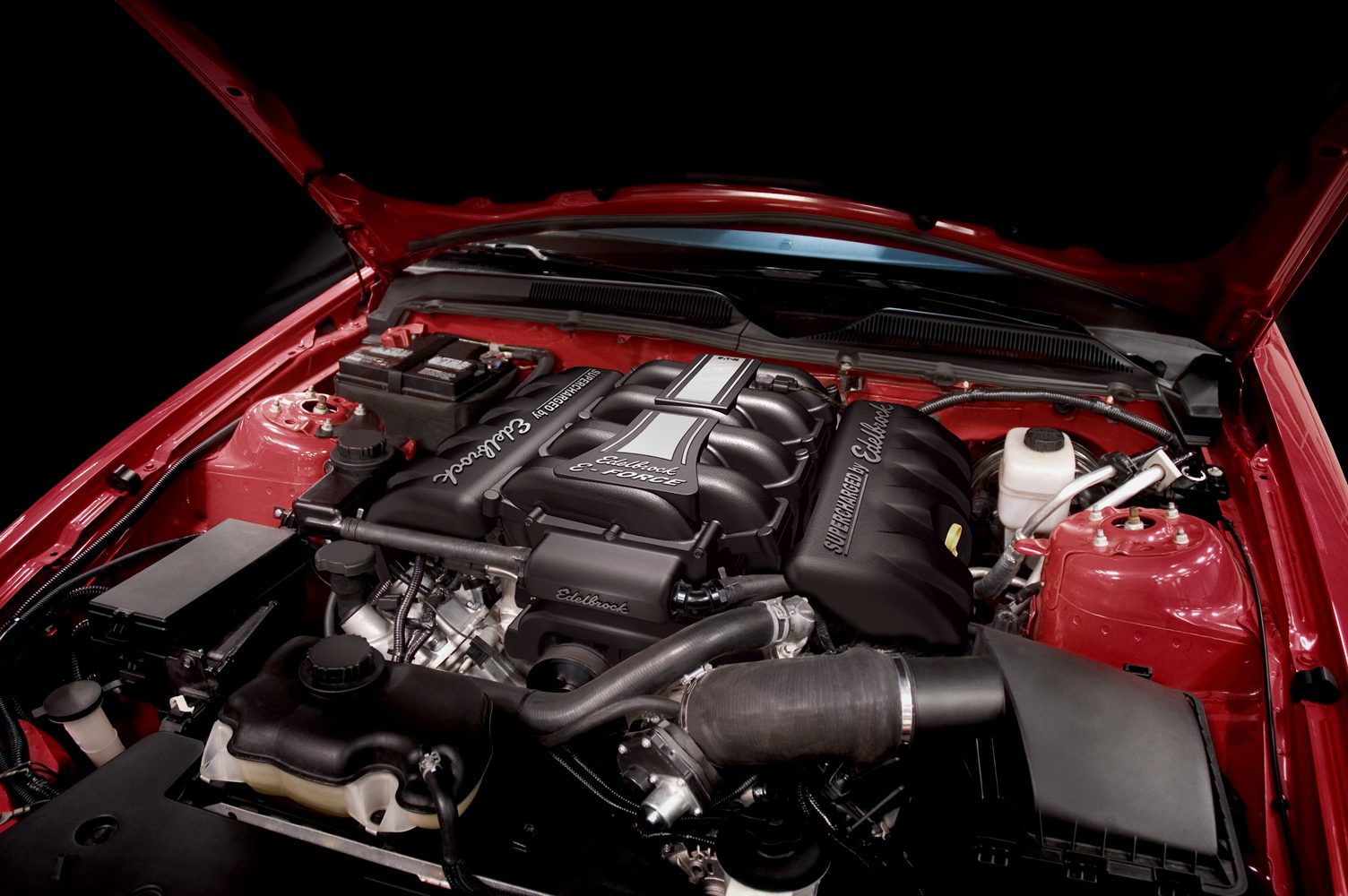
Image courtesy of Edelbrock.
While Edelbrock has used GAGEtrak since 1998, Brewis became the main user in 2008 and found right away that “GAGEtrak is very user-friendly and easy to learn.” Brewis likes that GAGEtrak allows him to track replacement costs on any gage, print monthly workload reports ahead of time and search and track tool history, allowing him to show an auditor exactly when a tool went missing as needed during an audit.
Brewis also likes that GAGEtrak can “...pull up my calibration records and print a calibration sticker [with the GAGEtrak Calibration Label Kit] in less time than it takes to boot up my computer.” Brewis estimates GAGEtrak “pays for itself ten-fold every year” and noted that “without GAGEtrak, this job would be impossible.” Brewis has also had great success with the CyberMetrics support team, commenting that “there hasn’t been a question they haven’t answered or a problem they haven’t solved.”
GAGEtrak is used at thousands of facilities worldwide to improve measurement quality, assure compliance and increase efficiency. Contact the GAGEtrak experts today to learn how GAGEtrak will do the same for your company.
Vision for the Win … Non-Contact Measurement Tops Traditional CMM
CMM touch probing surely has its place in measurement and inspection processes, however it is not always an optimal solution for certain part geometries and applications. Roush Yates Engines (RYE) of Mooresville, NC and its manufacturing division, Roush Yates Manufacturing Solutions (RYMS), recognized there were better options for QC on shims and bushings it manufactures for NASCAR’s “Next Gen” Car.
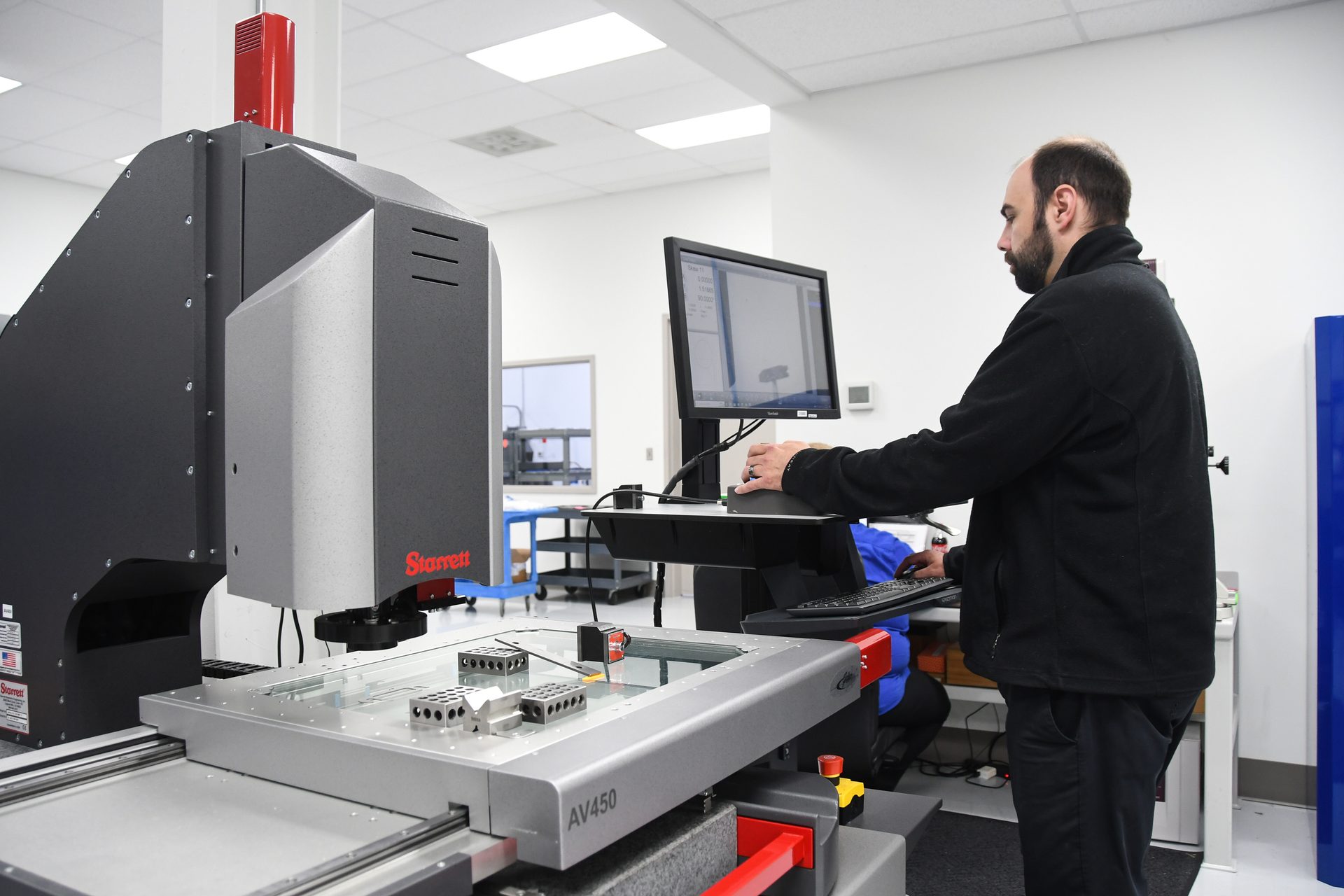
Roush Yates Manufacturing Solutions Quality Control Manager, Ryan Osborne performs first article inspection on the Starrett AV450 vision system.
In the case of the NASCAR “Next Gen” Car’s Bushing, using a touch probe to measure the radii on the undercut presented several challenges which increased inspection time and costs. RYMS Quality Control Manager, Ryan Osborne said, “The undercut was almost impossible to check accurately with a touch trigger CMM. The radii size as well as tool offset issues were difficult to see and determine.” In another race car part example, measuring a NASCAR “Next Gen” Shim to meet specifications presented challenges when probing with a CMM due to the part’s size and flatness.
Non-Contact Vision Provides Solution
RYMS reviewed how the Starrett AV450 vision system could provide the first line of defense for ensuring they were making parts right, the first time. Todd English, Vice President, Strategic Partnerships & Marketing at RYE said, “The Starrett vision system was able to measure the bushing undercut in an accurate, efficient and timely manner.” Osborne agreed: “When it comes to checking the small radii, the vision system is far superior to traditional touch trigger CMMs. Multiple optic zoom levels allow us to clearly see the tangent lines of the radii, giving our machinists critical feedback on challenging features.”
For measuring the shim, the benefits of using the vision system are just as impressive, especially for achieving accuracy and repeatability. The camera on the vision system focuses on the part without needing to touch it, ensuring that the dimensions are within specifications.
Osborne said, “The AV450 is saving time inspecting the first piece by obtaining good measurements right away, instead of having to go back and forth with production on whether the dimension is good or not. We have saved hundreds of hours since implementing the system.”
(949) 348-1213
Empower calibration service providers to deliver consistent, precise solutions
Micro-check Calibration Pvt. Ltd. (Micro-check) is an India-based calibration service provider using Renishaw's cutting-edge calibration systems to support their small and medium-sized customers. They offer a range of calibration services to Indian machine manufacturers, imported machine tool installations and other large machine tool end users.
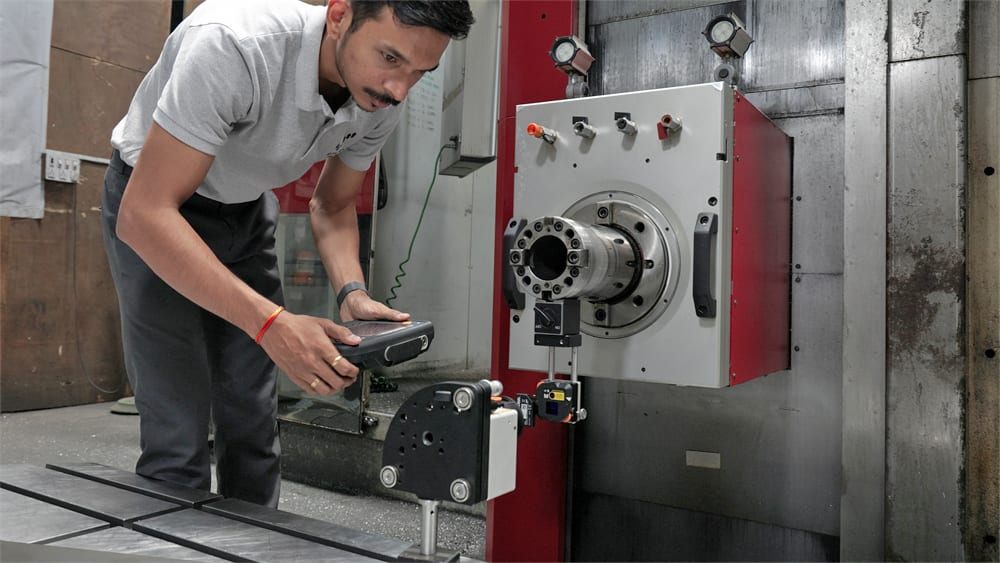
Micro-check has worked with Renishaw since 2016, using calibration products such as the XL-80 laser interferometer, QC20 ballbar, and XR20 rotary axis calibrator, to provide services to machine manufacturers. They recently expanded their offering by adding the Renishaw XK10 alignment laser system to their suite of tools.
“We use the XK10 system to measure the horizontal and vertical straightness of a set of 25-meter machine tool castings and the parallelism between these two castings. Regardless of the measurement direction, the data results were highly consistent which demonstrates the system's remarkable accuracy and repeatability, which was very impressive.” — Mr. Sunil Navale, Managing Director at Micro-check Calibration Pvt. Ltd
This strategic investment on the XK10 system has further enhanced Micro-check's ability to provide comprehensive testing and optimization solutions for their customers.
AFS Improves Trim Press Accuracy and Throughput with Delta Motion
Advanced Foundry Specialists (AFS), a leading provider of finishing room automation for the foundry industry, faced a serious challenge in its hydraulic trim press operations. There is no room for error in the trim process for components such as brake calipers for the automotive industry, as customer quality controls are understandably stringent. Faulty parts—cracked brake calipers, for example—could cost lives.
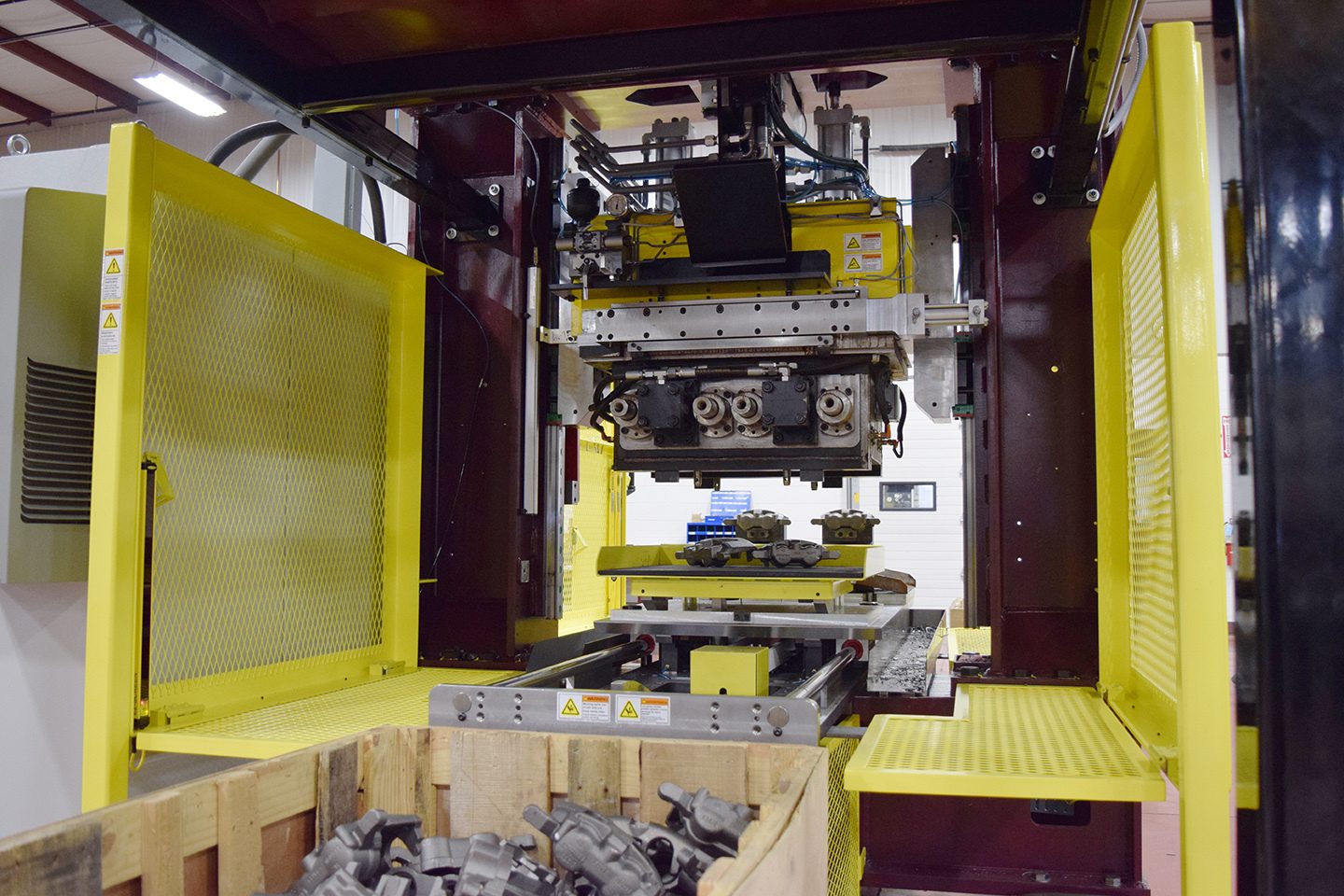
As demand for higher production speeds grew, their PLC-based motion control system simply couldn’t keep up. Operators were forced to choose between speed and accuracy, risking costly damage to tooling and finished parts.
To address the limitations of the PLC-based system, AFS implemented Delta Motion’s RMC controllers along with high-resolution linear transducers. Accurate closed-loop control allowed precise positioning of the trim press tooling, even at high speeds. The system could detect misloads and stop the press instantly, protecting both the equipment and the part. To speed production, AFS runs the presses at a rapid speed and then slows for trimming using the RMC’s on-the-fly parameter tuning to maintain location accuracy at maximum throughput.
The results were significant. AFS improved press cycle times by up to 20%, allowing for greater throughput without compromising product quality. At the same time, the risk of scrap and rework from misloads was drastically reduced. Delta’s system also improved operator safety and simplified setup with a user-friendly interface requiring no programming expertise.
With over 30 Delta-equipped trim presses now in the field, AFS has delivered consistent, high-speed, high-quality performance for its customers—turning component trimming from a risky process into a safe, reliable, scalable solution.