Machine Vision 101
Machine Vision 101
Vision & Sensors
V&S
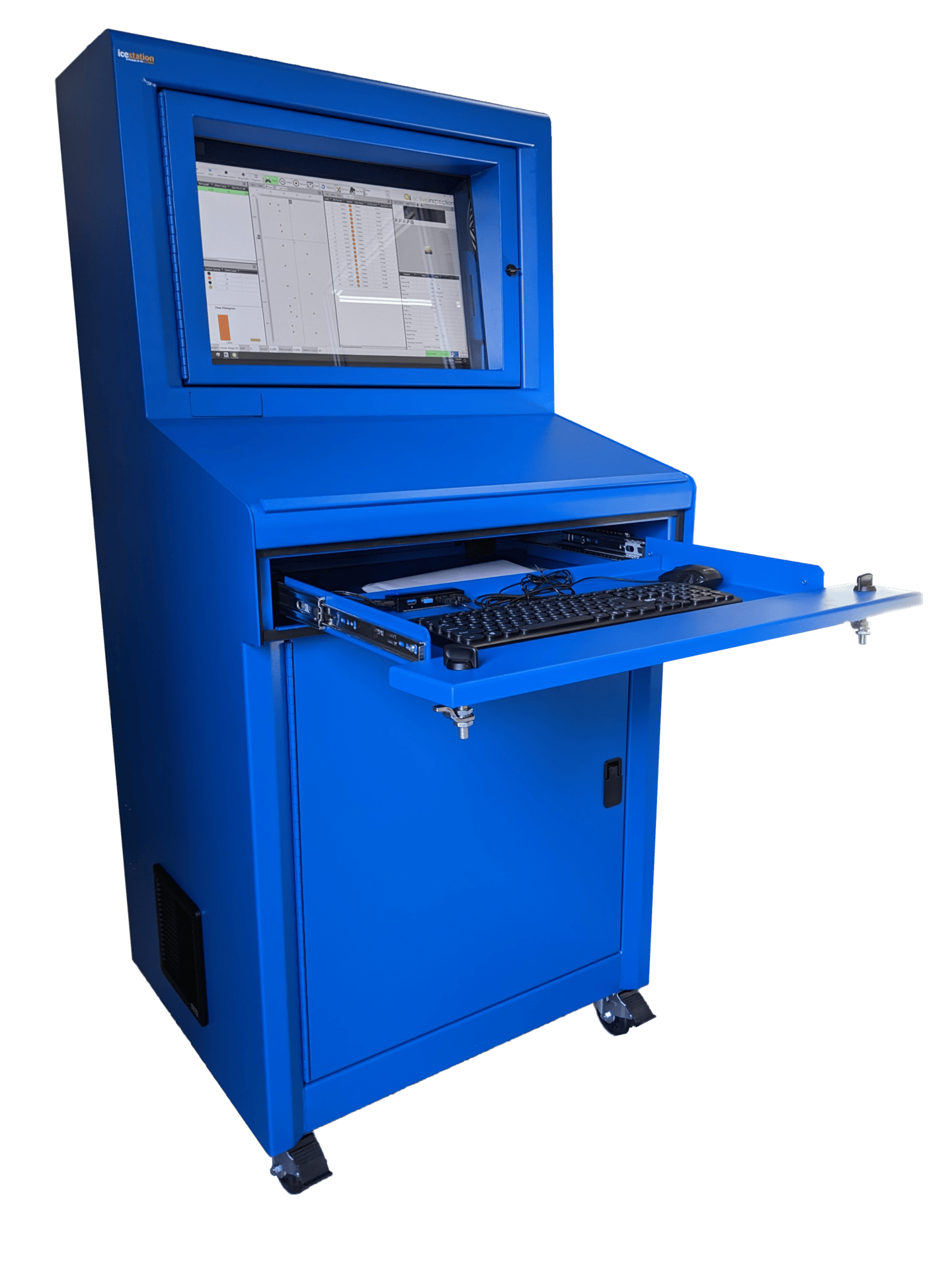
Complex machine vision inspection systems have become a key component of the manufacturing process.
By Glen Ahearn
System Integration:
Consolidating Vision Systems into the Manufacturing Process
Complex machine vision inspection systems have become a key component of the manufacturing process. By Glen Ahearn
System Integration:
Consolidating Vision Systems into the Manufacturing Process
Steady and consistent quality inspection plays a pivotal role in the manufacturing process. An increasing number of manufacturing plants are being fitted with multiple machine vision inspection systems to cover the entire production chain, ensuring higher-than-ever levels of quality. The automated exchange of consistent information between these different systems in a manufacturing environment is the essence of system integration, allowing for improved productivity and quality, reduction in cost and waste, and overall innovation. In my role as sales and application support manager, I work with many of the systems integrators who rely on our products to support their development of vision systems. We sat down with Dr. Arun Dalmia, founder and president of Active Inspection, a systems integrator based in Grand Rapids, MI, to ask him some questions on how system integration has helped his clients build robust and sustainable manufacturing processes and how the role of systems integrators is evolving.
Active Inspection has been in business for over two decades designing and developing industrial machine vision and machine learning solutions. Alongside supplying a suite of standard vision systems, they also build custom vision systems to provide solutions for more complex problems.
Active Inspection provides solutions using vision systems including aerial, line scan, 2D and 3D, color, monochrome, visible spectrum, short wave, infrared, and ultra.
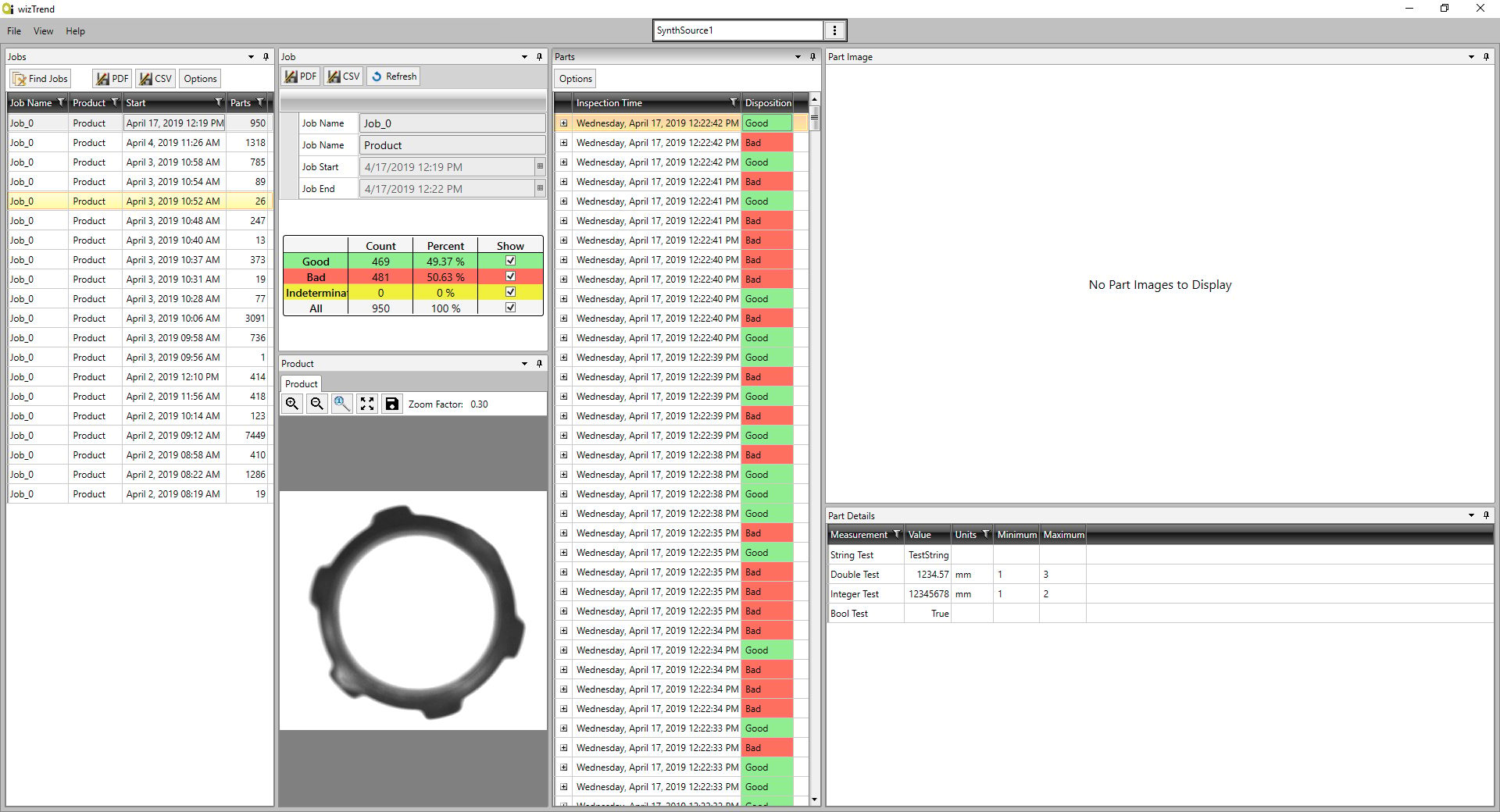
Data analytics solution for acquiring, storing, and analyzing vision data from multiple vision systems.
Explain to us how a systems integrator works with a customer.
Our first interaction with a new customer centers around understanding their requirements and needs, and more importantly discovering the problems they face with their current setup. Figuring out which part of the problem we can effectively solve is the next order of business. We analyze to see if it is logical and realistic to solve the problem they are trying to solve, based on the technology, the hardware, the software, and even their budget limitations. Being transparent and honest about how effective the solution will be given these constraints is essential.
After the initial assessment, we move to provide a plan for an end-to-end solution, picking the right technology components—the camera, the lighting, controls, software libraries, interfaces, etc. We provide a proof-of-concept, a feasibility study, to show the components we have chosen would work for them. Thereafter we move on to implementing, installing, training the customer, and providing the product lifetime support. Our company and our team of engineers are very responsive to our customers. We work very closely with them to ensure that all their needs are met, which I believe is a very critical part of the integration process.
What types of applications are you asked to build systems for most often?
We provide a lot of our expertise to line scan applications. We work with a wide variety of industries from automotive to pharmaceutical to continuous/web inspection for film, plastic, and paper, to food processing. Our work in deep learning applications is growing too. Where classic image processing and machine vision tools fail, we find deep learning is able to provide good solutions. We are also relying more on high-speed video recording and diagnostic systems.
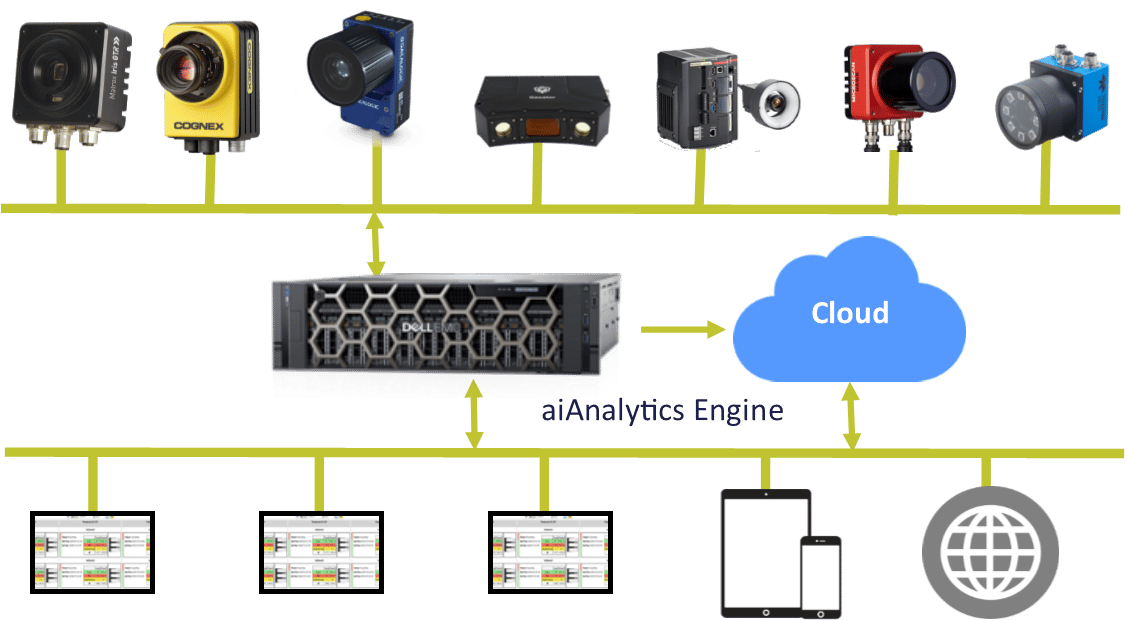
Reviewer application for monitoring and trending of vision system results.
Please tell us more about the high-speed video recording and diagnostic systems.
With manufacturing happening at higher and higher speeds (up to two, three and five parts per second), our systems are able to capture between 500 to 2,000 frames per second, something even the human eye cannot register. With AI replay, which is the ability to scroll back the video on the production process, the information is invaluable. We can create a large buffer and go back anywhere between five minutes to five hours of the recording, analyze frame by frame and pinpoint exactly where in the process the problem occurred and what caused it.
How is technology driving better systems?
About one-third of Active Inspection’s efforts are dedicated to R&D. We work with some large automotive and pharmaceutical companies who are trying to push the technology envelope. They present us with common problems that do not need to be fixed in short term, but they are interested in a solution in the next two to three years to better streamline their production process.
We work with these clients to develop new, custom solutions for them or try to evaluate what is feasible. These are tougher problems that typically do not fall into very standard system integration. Because we are not a “standard system integrator” and are able to provide a lot of software development capability, we are able to fill in a lot of gaps. There was a time when we wrote software from scratch, but now our goal is to license or purchase as many of the components that are available. At the same time, we have the capability to go deep into these gaps and fill them with some custom solutions.
When you started Active Inspection did you see an opportunity in the market and decided there aren’t enough systems integrators who take it to that next step with R&D?
Yes, the one gap we see is that typical system integrators tend to use off-the-shelf cameras that come with their own set of tools. The available solutions tend to be a selection of ready components and existing tools. At the most, they customize panels and electrical and add a mechanical converter. But in terms of core machine vision and software, their contribution is limited, resulting in a limited solution.
For a company like Active Inspection, with a strong machine vision and software background, we can fill in some of the gaps. Using custom algorithms or custom development we are able to provide better solutions. Another factor that is coming into play now is the progress in camera technology. Twenty years ago, the camera was a stand-alone component that took a picture of a part and sent a signal to a receptor to register whether the part was good or bad. Today we are dealing with complex integrated systems. The information comes from a level two control system, where detailed information such as hours of production, particulars of the parts in production, etc., are relayed.
When integrated with a PLC, the system can trace the number of parts that were made that day and register the number of rejected parts from that batch. At a later date it will be possible for the system to trace back the data from that day and see why the parts were rejected, what was the problem, what the rejected parts looked like, and even details about their size and measurement. This level of detail can be useful to a line supervisor to study the defects and rectify the cause of the problem.
Going up the chain, we can even create interfaces through web technology or mobile technology where a plant manager is able to access some amount of this quality data. Today, quality data is accessible to different levels in the organization, delivering the information they need in a timely manner.
How has systems integration changed over the last decade?
Three decades ago, when I started in the industry, vision systems, even basic inspection systems, were not a necessary component of the process, rather it was added as an auxiliary piece. Today, complex machine vision inspection systems have become a key component of the manufacturing process, to a point that if the vision system fails or is not functional, production is stopped until the problem is fixed. With manufacturing happening at such high speeds with massive outputs, a small defect that is not caught on time can prove very costly.
Do some industries rely on integrated machine vision systems more than others? Are you seeing its use in new applications?
Some industry segments widely use machine vision on a routine basis, and others are still to be introduced to the technology. But definitely, awareness is building about its usefulness and many more industries are adopting vision systems as a part of their manufacturing and quality control processes.
The automotive industry is a very large consumer of machine vision, using thousands of cameras along their production lines, each camera doing specific tasks and error-proofing at every step of automation. Historically, machine vision was used as a final quality check at the end of production. The goal today is to catch the error or defect as early as possible so as not to waste resources, particularly in high-speed and high-volume production setups. In this age of 100% quality inspection, error-proofing at every stage allows for fewer production jams and more productivity, while avoiding waste of material and time.
One industry that adopted automated inspection and automation later is the food processing sector. This is a labor-intensive industry, but we are now seeing that they are opening up to adopting machine vision or inspection automation more and more.
Can you touch upon the cost involved in integrating machine vision systems?
Historically a fully installed machine vision system could have cost between $500,000 and $1,000,000. Now, thanks to technological advances and the volume production of cameras costs have come down, and an investment of $50,000 and $100,000 would get you a high-end vision system. The cameras of today come for a third of the price and offer five times higher performance and bandwidth. Smaller manufacturers, in many industry segments, are now able to justify the ROI on a system in shorter time periods and are seeing the value in adopting machine vision systems.