How XRF works, its advantages over traditional coating analysis methods, and its critical applications in ensuring product quality and compliance. By Damien Blondel
Ensuring Coating Quality:
The Power of XRF Analysis in High-Tech Manufacturing
XRF
H2 Deck Info By Paragraph Style Bold
Headline
X-ray fluorescence (XRF) is a powerful analytical technique widely used for coating analysis across various industries, including automotive, aerospace, and metal fabrication. This nondestructive method provides precise measurements of coating thickness and composition, supporting quality control and optimizing production processes. Following a brief overview of XRF principles and a review of its advantages over traditional coating analysis methods, this article explores how XRF analyzers—whether handheld or integrated into automated production systems—can enhance quality control practices.
In industries where precision and reliability are paramount, the quality of coatings on materials plays a critical role in product performance, durability, and compliance. From aerospace components that require protective layers against extreme environmental conditions to electronic circuit boards that depend on precisely applied metal coatings for functionality, ensuring coating integrity is a top priority. One of the most powerful tools for analyzing coatings in quality control applications is X-ray fluorescence (XRF).
XRF technology provides a nondestructive, accurate, and efficient means to assess coating composition and thickness, making it indispensable in high-tech manufacturing sectors such as aerospace, automotive, electronics, and medical devices. This article explores how XRF works, its advantages over traditional coating analysis methods, and its critical applications in ensuring product quality and compliance.
Applications of XRF in Quality Control
Aerospace and Aviation
Aircraft components must meet stringent safety and performance standards, particularly regarding corrosion resistance and durability. XRF is commonly used to verify the thickness and composition of protective coatings, such as anodized aluminum layers and non-chromate conversion coatings. Ensuring proper coating application helps prevent premature wear and structural failure, enhancing the longevity and reliability of aircraft parts.
Automotive and High-Tech Manufacturing
Automotive manufacturers rely on XRF to ensure consistent and precise coating application, particularly for anti-corrosion layers on aluminum components. For example, in lightweight vehicle manufacturing, aluminum coatings protect critical parts from oxidation and wear. XRF analysis helps maintain quality standards while supporting sustainability efforts by reducing material waste.
Medical Devices
Medical implants and instruments often require specialized coatings that enhance biocompatibility and durability. XRF ensures that coatings such as titanium, chromium, and gold are applied correctly and meet stringent regulatory requirements. This is crucial for patient safety and long-term device performance.
Energy Sector
Optimizing the performance, efficiency, longevity, and safety of fuel cells requires that the coatings applied to fuel cell components, such as bipolar plates and membranes, are of the correct thickness and composition. XRF handheld and in-line analyzers can measure catalyst coatings (platinum, nickel, iridium, or ruthenium) or protective coatings (manganese, cobalt, aluminum) of metallic interconnects and balance-of-plant components.
XRF Principles and Coating Thickness Measurements
XRF is an elemental analysis technique that uses high-energy X-rays to excite atoms within a material, causing them to emit characteristic secondary (fluorescent) X-rays. These emitted X-rays are unique to each element, enabling precise identification and quantification of materials present in a sample.
When applied to coatings, XRF can measure thickness coating from some tenths up to few tens of microns, using fluorescence signal attenuation through the material. This is particularly valuable for multilayer coatings, where distinguishing between different materials is essential for ensuring compliance with engineering and regulatory standards.
Challenges and Considerations in XRF Coating Analysis
While XRF is a powerful tool, there are some challenges to consider:
- Complex Multilayer Coatings: In some applications, the same elements may be present in multiple, sometimes ultrathin layers, making accurate differentiation difficult.
- Calibration and Standardization: Ensuring precise measurements requires proper calibration using reference standards.
- Material Density Variations: The accuracy of XRF readings can be affected by variations in the density of underlying substrates, requiring careful interpretation of results.
Advantages of XRF for Coating Analysis
Compared to other coating measurement techniques, XRF offers several key advantages:
- Nondestructive Testing (NDT): Unlike destructive testing methods such as cross-sectioning, XRF enables manufacturers to analyze coatings without damaging the sample.
- Rapid Analysis: Results are typically obtained in seconds, usually no longer than a minute, enabling real-time quality control and reducing production downtime.
- High Accuracy and Sensitivity: XRF can detect even trace amounts of coating materials, ensuring precise thickness and composition measurements.
- Multilayer Analysis: XRF can measure coatings consisting of multiple layers, which is essential in advanced manufacturing applications.
- Minimal Sample Preparation: Unlike certain traditional methods that require elaborate sample preparation, XRF can analyze coatings with little to no preparation.
Coating Thickness Measurement with Handheld XRF Analyzer
Handheld XRF analyzers are highly portable, enabling rapid and accurate elemental composition analysis and material identification on site. They can be precalibrated for a range of applications, including checking alloy grade specifications, the composition of glass or other materials, and layer thickness measurements of coatings. Easy to use and carry, fast and accurate, XRF handheld analyzers are the preferred method for thickness measurement of large parts, as they can be transported wherever they are needed.
XRF analyzers can measure layers made of almost any elements, such as metals used for galvanization, electroplating, or nonchromate coating, as well as silicon against corrosion for example. In the analyzer’s user interface, users select the number of layers and their composition. A one-point calibration on a reference standard is recommended to tune the accuracy. Once calibrated the instrument is ready: simply place the analyzer on the sample to analyze, press the trigger and, in typically less than 30 seconds, the coating thickness is displayed on the analyzer screen.
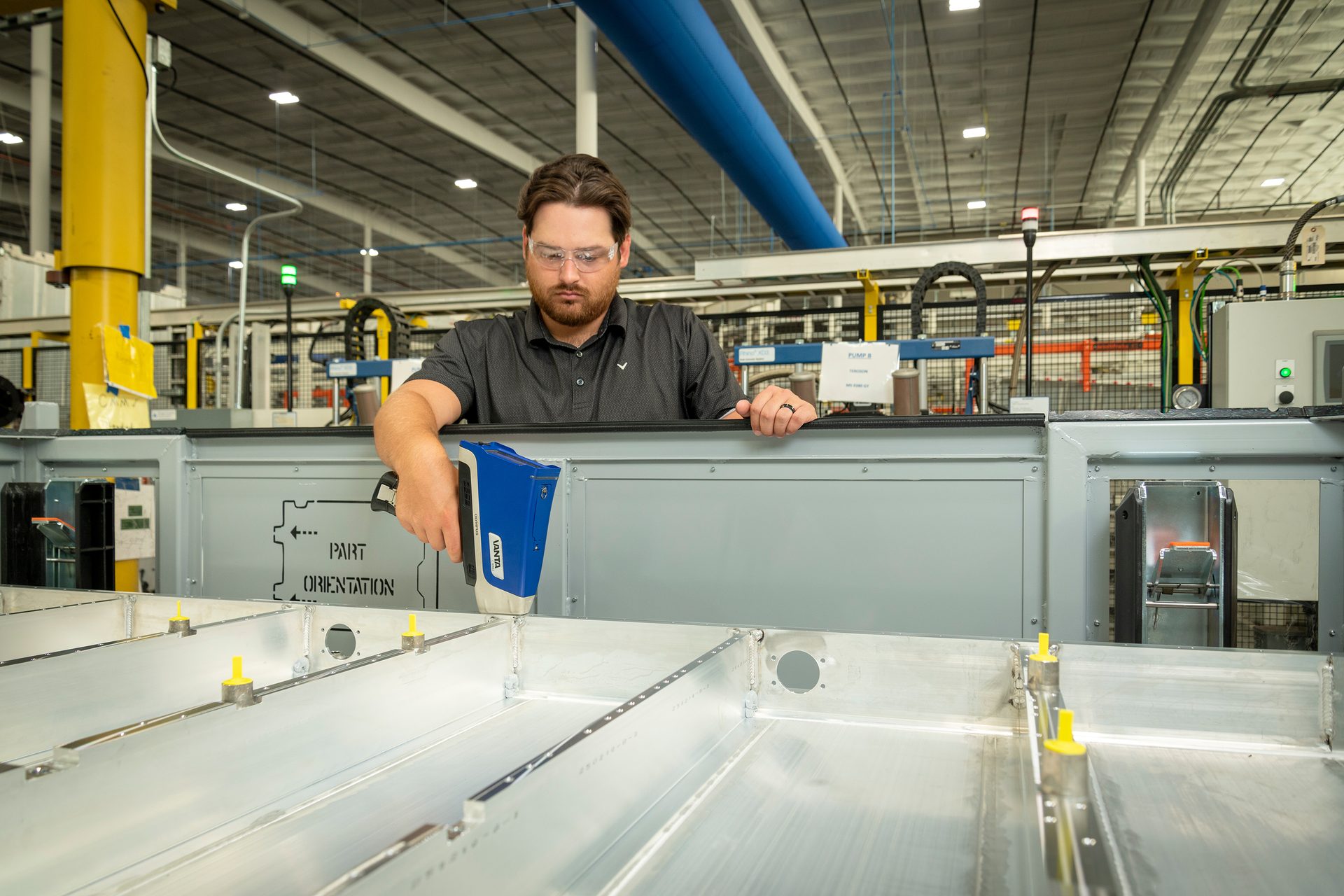
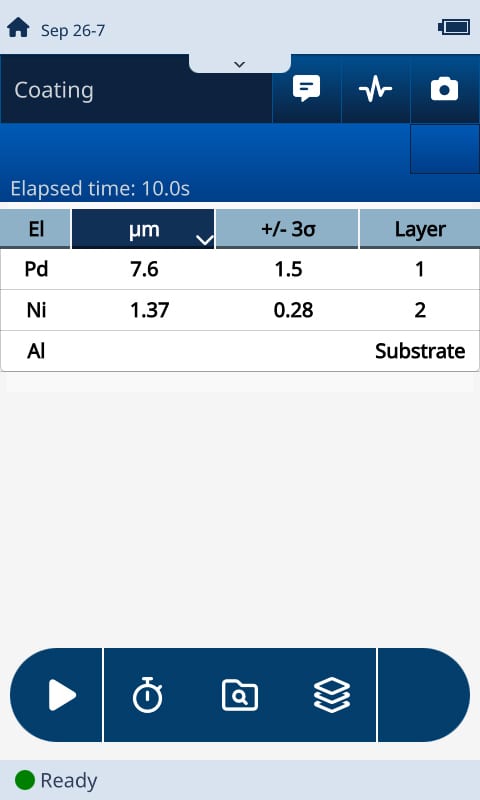
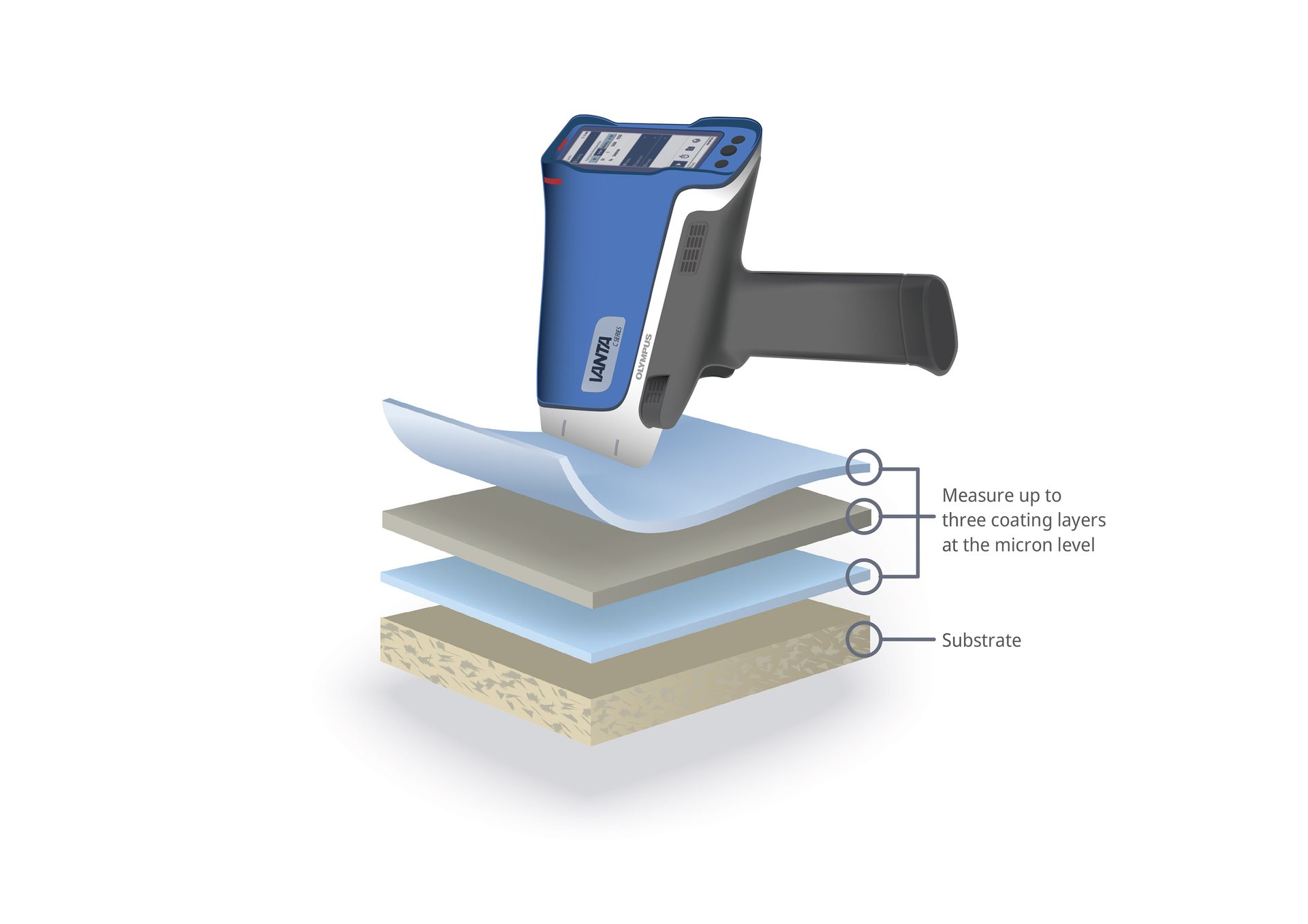
Figure 1. This XRF analyzer can detect and measure up to three coating thicknesses on a substrate.
Figure 2. Results screen from a handheld XRF analyzer displaying the thickness of palladium and nickel coating in an aluminum substrate.
Figure 3. This handheld XRF analyzer is used to analyze coatings in automotive manufacturing to help ensure quality.
Application Example: Titanium-Zirconium (Ti-Zr)-Based Conversion Coatings
Titanium-zirconium (Ti-Zr)-based conversion coatings are used as an alternative to banned chromate coatings. Portable XRF analyzers can provide a rapid, nondestructive method to ensure that Ti-Zr-based conversion coatings have been applied and fall within the required thickness range. Data provided in Figure 1 illustrates the accurate coating thickness capabilities.
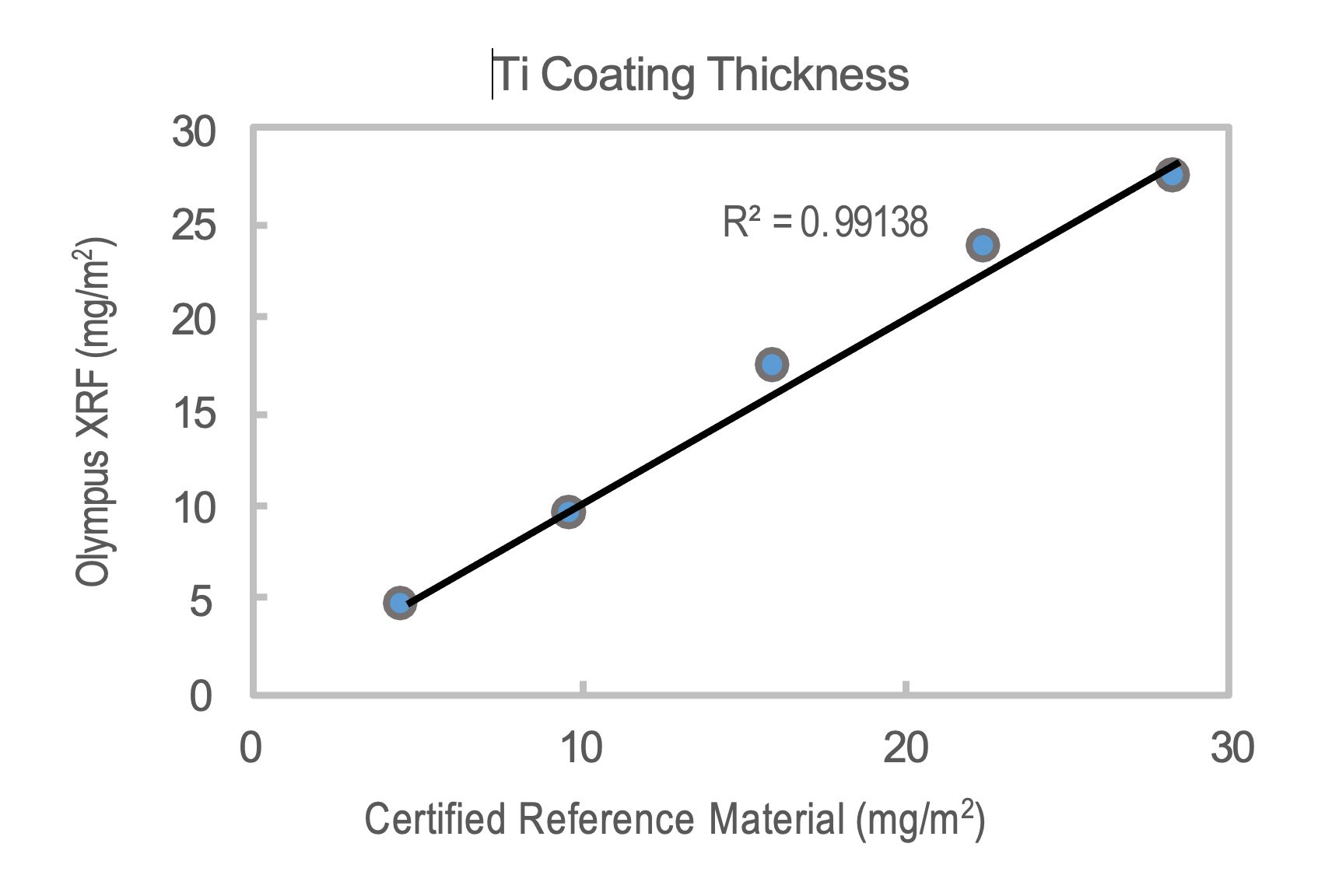
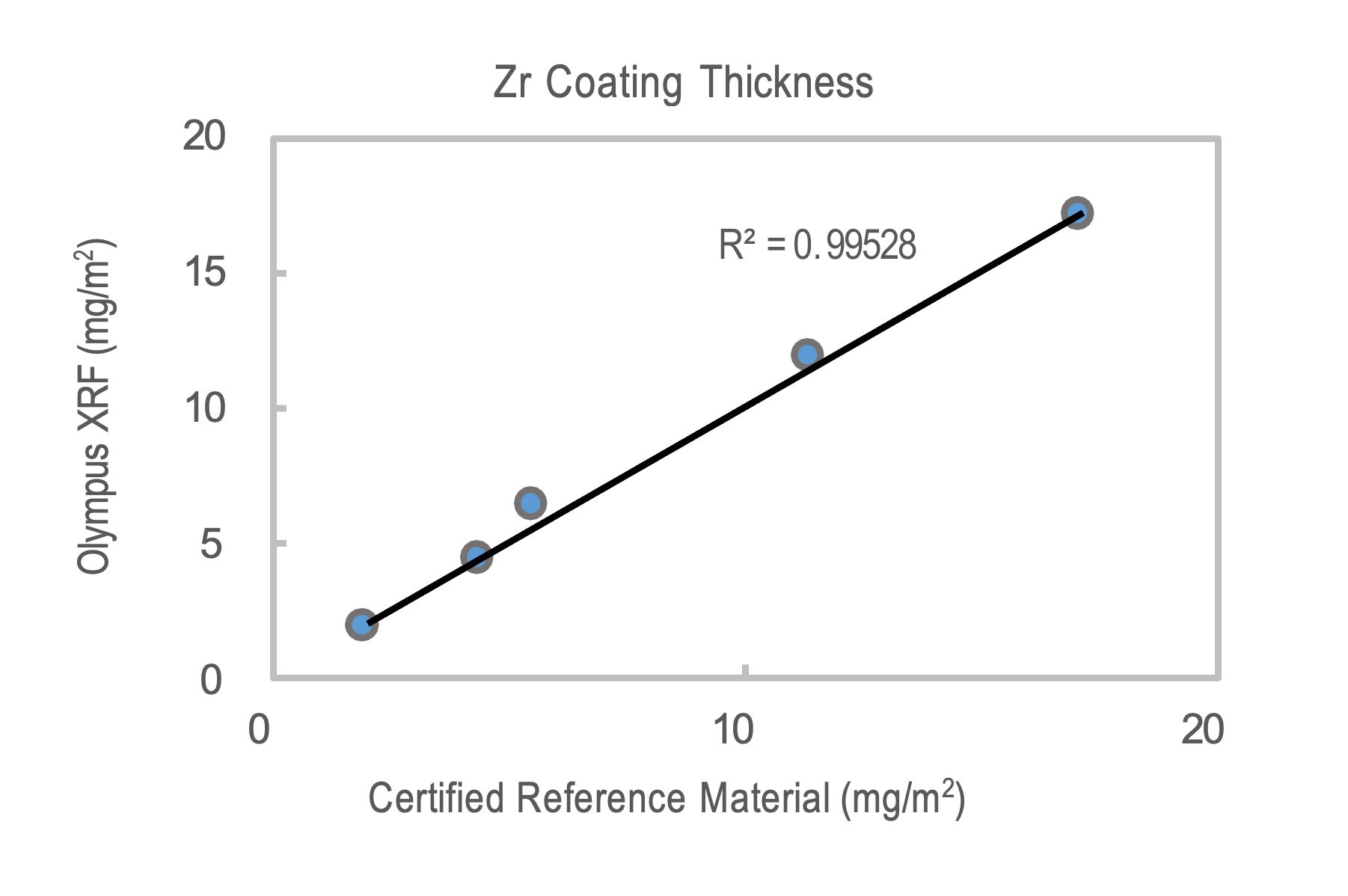
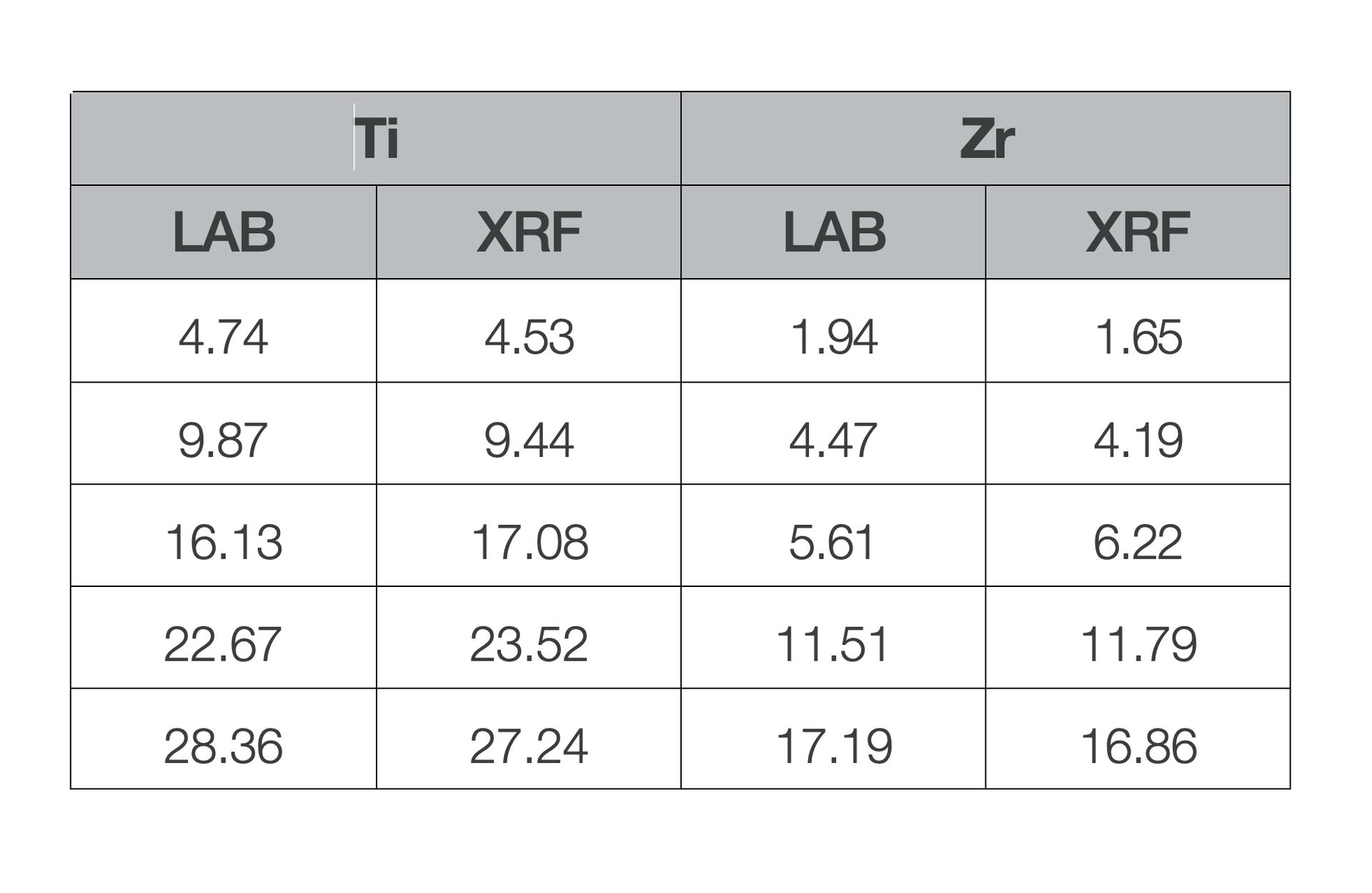
Figure 4. Ti and Zr coating thickness measurement accuracy
Automated Coating Thickness Measurement with In-Line XRF Analyzers
In-line XRF analyzers provide automated material analysis and coating thickness measurements directly on production lines. Using the same measurement principles as XRF handheld analyzers, they enable full inspection of coatings for metal part fabrication, films, glass and other components. Compact and rugged, they integrate easily with robot arms or 3D scanners to analyze large areas or to perform a large number of tests without human error. Measurement data is automatically shared with local databases and documented for complete quality control and traceability.
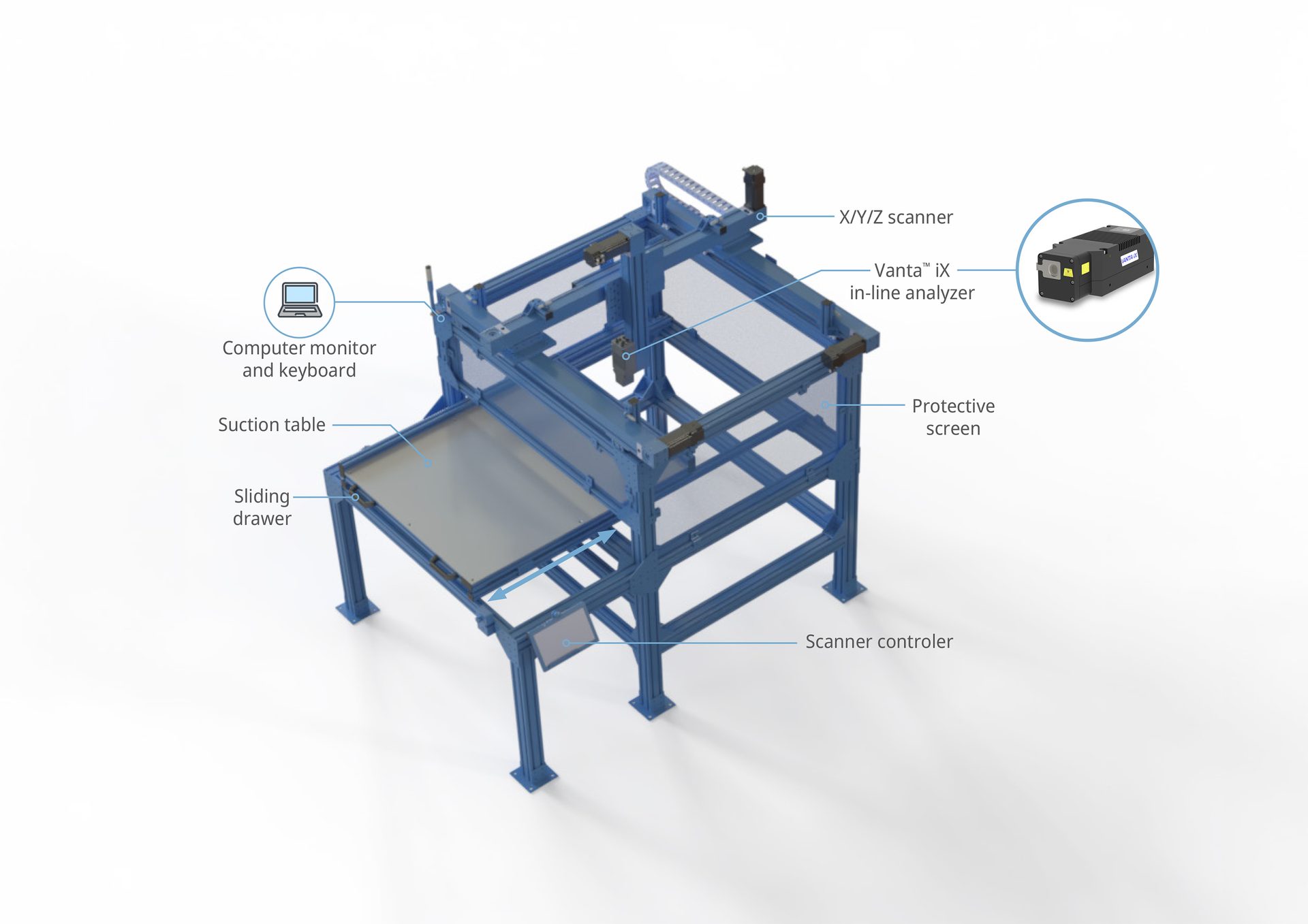
Figure 5. Automated XRF analyzer on a 3D scanner.
Conclusion
XRF is a game-changing tool for coating analysis, providing manufacturers with a fast, reliable, and nondestructive method to ensure product quality and compliance. From aerospace and electronics to automotive manufacturing, XRF plays a critical role in maintaining high-performance standards and reducing production risks. As technology continues to evolve, the adoption of XRF for coating analysis will continue to grow, driving improvements in quality control processes across multiple industries.