Robotics
Vision & Sensors
V&S
H2 Deck By Bold Name
h2 xxxxxx
H1 xxxxxx
h2 xxxxx
Robotic automation delivers consistent quality. By Dr. Satyandra K. Gupta
How AI-Powered Robotic Automation Impacts Manufacturing Quality
The robotic automation journey for most companies begins with the need to address the labor shortage. For instance, high-mix surface finishing applications — sanding, polishing, grinding — are ergonomically challenging and therefore have a high labor churn. This is a major problem for a wide variety of companies that cannot find people to work on surface-finishing lines. Recent advances in artificial intelligence (AI) used in smart robotic cells are, however, helping to compensate for manufacturing labor shortages. Smart robotic cells can now enable robots to program themselves from task descriptions. The availability of 3D vision and force sensors allows robots to perform complex operations autonomously. The deployment of smart robotics cells helps surface-finishing companies realize additional benefits as well:
- Increase human productivity and reduce the need for humans to perform ergonomically challenging work
- Expand production capacity and offer flexibility
- Eliminate programming efforts associated with traditional robotic solutions
- Reduce overall cost
In addition, AI-powered robotic automation can dramatically increase product quality. We are living in an era of ever-increasing product complexity, emphasis on premium performance, focus on accountability, and intense global competition. Customers expect flawless product, and regulators hold manufacturing companies responsible for delivering the promised performance. Earning and maintaining customer trust is paramount to survival in today’s environment for every manufacturer. This article explains how AI-powered robotic automation impacts manufacturing quality.
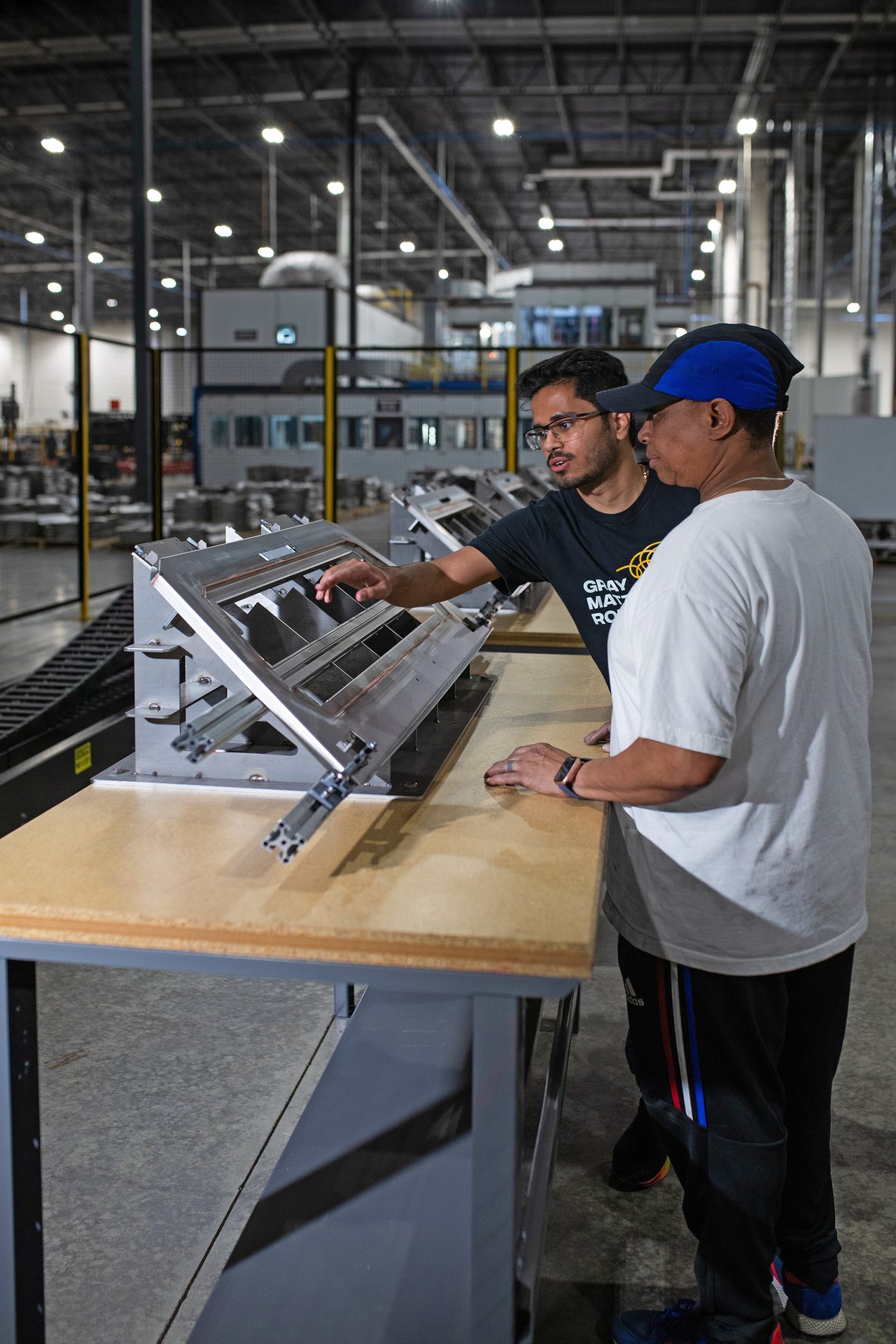
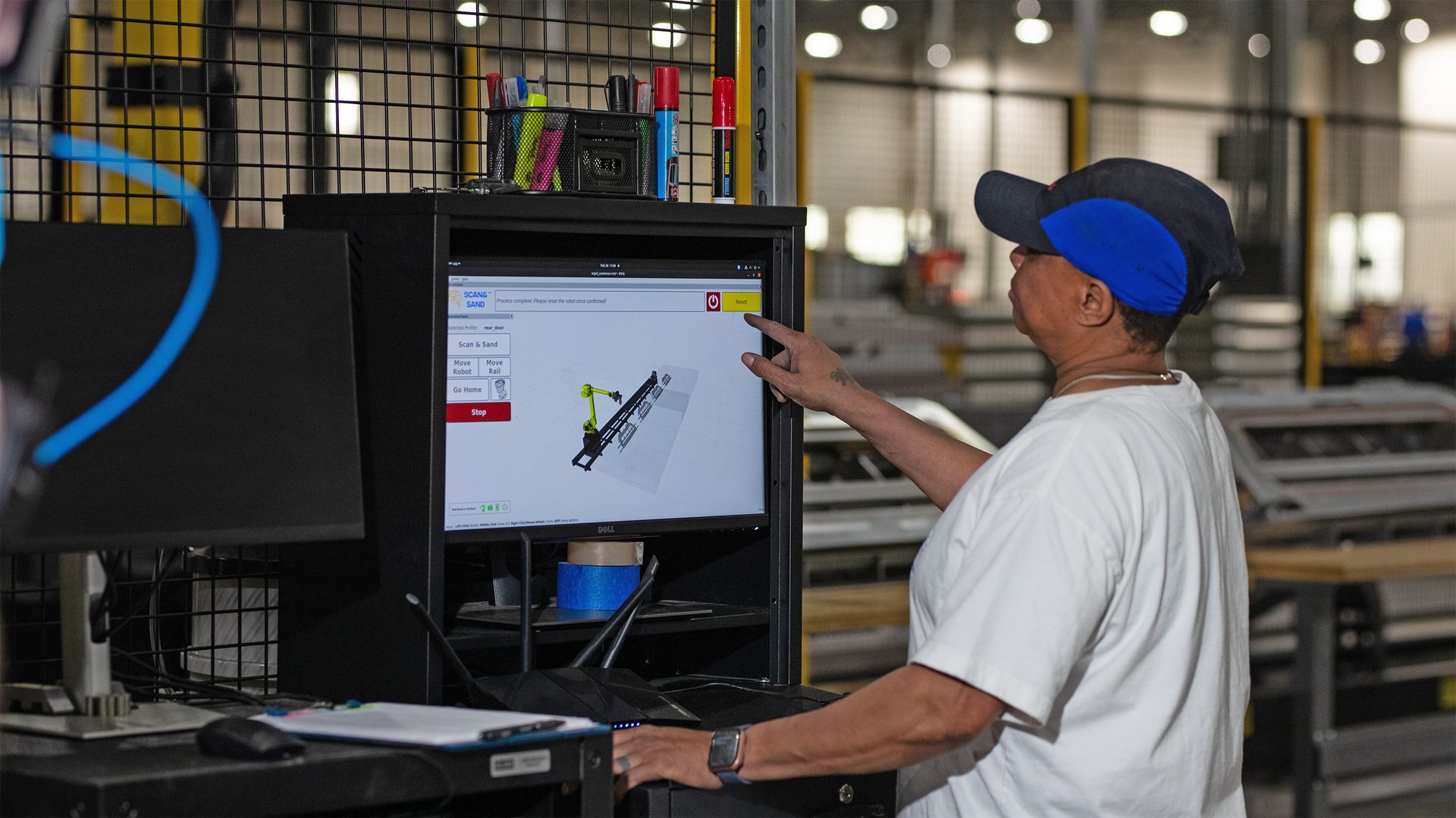
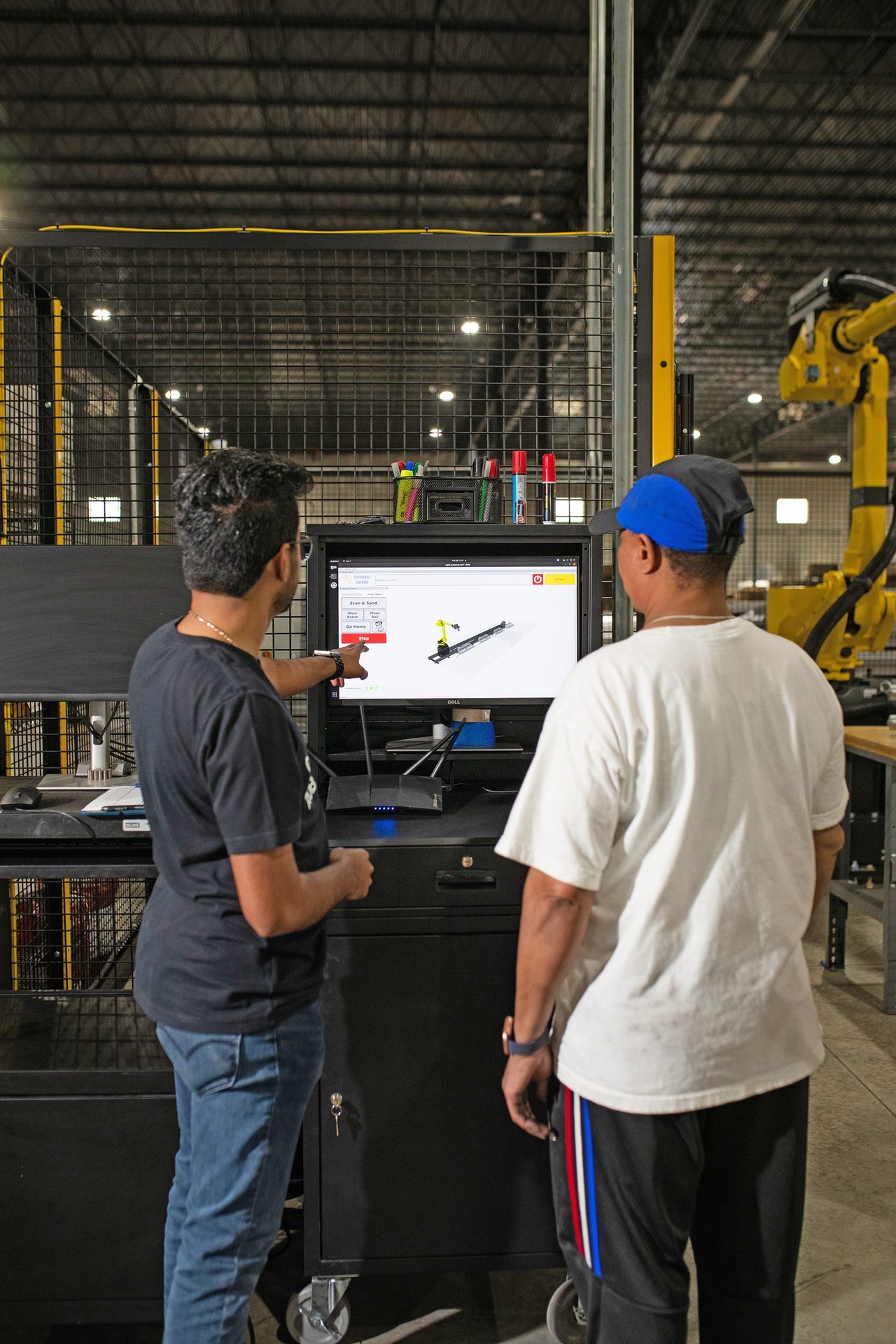
Quality Assurance and Traceability
Over the last few years, we have seen many instances of products being recalled when a manufacturer failed to meet the promised level of safety or performance. Many product recalls are attributed to manufacturing quality problems. A significant recall can easily become a very expensive ordeal due to lost sales, replacement costs, government sanctions, and lawsuits. Product recalls can quickly destroy a manufacturer’s profit and reputation. To do well in the current climate, a manufacturer must consistently deliver high-quality products to its customers.
In manual manufacturing operations, companies need to employ sophisticated quality management systems that require installing new hardware to inspect parts and collect process-quality data. There is no other option to mitigate the risk of a product recall.
AI-powered robot cells ease the burden by offering a new means to ensure quality control in a more affordable manner. A beneficial side effect of deploying robotic cells is that these same cells can play a key role in collecting critical information to ensure the quality of manufacturing operations without incurring any additional costs. Here are a few examples of how robotic cells help in delivering high-quality, trustworthy products:
- The robotic cell can record all relevant processing data. For example, as a robot performs a sanding operation, it records the RPM, the force applied by the tool, and the tool velocities used to process the part. The system can also record facts about the sanding tool itself. All this information creates a detailed auditable trace confirming that the part was processed according to quality standards.
- Many robotic cells implement an inspection step to ensure that the part processing has been successfully completed. Data collected during this step can be used to create a digital certificate of specification compliance. In fact, inspection data can be used to construct a digital twin of the as-manufactured part. This model can also be useful in efficiently automating downstream processing steps.
- When robots begin work on a part, an initial measurement step is performed on the raw material loaded into the cell. Let us again consider the sanding example. Usually, an optical scan of the part creates the model for generating tool trajectories, giving the robotic cell the data it needs to monitor tool wear and part behavior during processing. If any anomaly is detected during processing, the system can make inferences about the incoming material quality and alert the upstream process team.
Improving Quality and Reducing Waste
Robotic automation delivers consistent quality. Human operators are prone to making mistakes when they experience fatigue and cognitive overload. When a company experiences significant labor churn in a tight labor market, it needs to deploy new workers with no prior experience. New workers tend to make more mistakes compared to experienced workers. Robots follow specified rules, so using robots helps remove most of the human variability error from processes. Automation can be highly repeatable and therefore improve the overall process. Robots reduce the need for rework and the amount of scrap. Less scrap means less landfill waste. Therefore, robots not only improve quality but also reduce waste.
Using Digital Twins of Robotic Cells to Prevent Failures and Continuously Improve Process
Many robotic cells implement an inspection step to ensure that the part processing has been successfully completed. Inspection data can also be used to automatically construct a digital twin of the as-manufactured part. This model can be useful in efficiently automating downstream processing steps. AI-based prognostics and health management can leverage digital twins to ensure that the onset of adverse events are automatically detected so that corrective actions can be taken. For example, the digital twin can use the force and vision data to determine the cause of rapid tool wear in robotic finishing and take corrective measures to prevent it.
The need for continuous improvements and process optimization requires the system to build its own process model. A digital twin can use machine learning to safely conduct autonomous experiments and build a model for selecting the optimal process parameters for sanding a new material.
AI-Based Defect Detection in Automated Production
Deep learning is a specialized type of artificial intelligence. It is different from traditional learning in a few key ways. First, traditional learning algorithms often require hand-engineered features to represent data, which can be time-consuming and require domain-specific knowledge. In contrast, deep learning algorithms automatically learn features from raw data, making them more flexible and adaptable to different types of data.
Second, deep learning algorithms can handle large amounts of data and can learn from vast amounts of training data, making them well-suited to big data applications. Traditional learning algorithms, on the other hand, may struggle with large datasets or require significant computational resources to process them.
Third, deep learning algorithms can model highly complex relationships between inputs and outputs, lending themselves to tasks such as image and speech recognition. Traditional learning algorithms may struggle with highly nonlinear relationships or complex patterns in data.
Finally, deep learning algorithms have achieved state-of-the-art performance on a range of tasks, such as image and speech recognition, natural language processing, and game playing. Traditional learning algorithms may not be able to match the performance of deep learning algorithms in these tasks.
Using deep learning for defect detection offers a high degree of flexibility as the network can be customized to detect specific defects based on the dataset. Additionally, the parameters learned for one network can be applied to similar networks, resulting in a high rate of success in detecting surface defects using minimal training data. Another advantage of this approach is that customized code is not required. Using labeled data for various defects with an appropriate network creates a highly adaptable mechanism for detecting defects.
Deep learning algorithms can be trained to detect defects in products — such as cracks in metal parts or streaks on painted surfaces — in real-time, reducing the need for manual inspection and increasing overall efficiency. Deep learning algorithms can also be trained to inspect and classify products based on specific criteria, such as size, shape, and color. This can help reduce human error associated with manual steps and improve the accuracy of quality control in manufacturing.
Reducing Human Errors by Improving Training
Humans continue to play important roles in manufacturing facilities that use robotic automation. With traditional interfaces, training employees to effectively work with robots takes significant time and resources. This is becoming a major challenge in today’s era of high labor churn.
Most traditional approaches were not designed with ease of training in mind. AI-powered training can provide real-time feedback, guidance, and assistance to employees during the training phase, helping them navigate complex tasks or troubleshoot problems effectively. Active learning can monitor mastery of a task and so employees can focus on areas where they need more practice. Moreover, virtual assistants equipped with AI can offer interactive support and tutorials, improving user productivity and learning outcomes during the training phase. Many quality problems can be traced to human error. Improved training can prevent human errors and improve overall product quality.