H2 Deck By Bold Name
h2 xxxxxx
H1 xxxxxx
h2 xxxxx
Test & INspection
Automation in physical properties testing is a strategic investment that enables higher precision, greater throughput, and more actionable data. By Robert Egginton
The Energy is Worth the Effort - the Catalyst to Automate
Test & INspection
H2 Deck Info By Paragraph Style Bold
Headline
This article explores the role of automation in quality assurance, with a focus on physical properties testing and metrology. We begin by outlining key automation concepts and their relevance in improving consistency, efficiency, and data integrity, before examining a real-world application in the energy sector—automated crush strength testing of catalyst pellets.
Automation concepts
The benefits of automation are well-established: it enhances consistency and repeatability, reduces testing time, lowers operational costs, and ensures the integrity of collected data. These advantages support the broader goals of smart manufacturing and align with the principles of Industry 4.0 by enabling more responsive, scalable, and connected systems.
Automation in the context of quality assurance and metrology refers to the use of systems, software, and machinery to perform repetitive or precision-critical tasks with minimal human intervention.
Human-machine interface: What to automate
Certain aspects of the human-machine interface are especially well-suited to automation. These include tasks that are:
- repetitive and pose ergonomic risks, such as repetitive strain injuries,
- performed in challenging or hazardous environments,
- physically time-consuming,
- prone to [human] error, such as sample loading and test setup.
Automation also supports objective-driven processes such as standards-based quality control testing, which demand statistical confidence and significant test volumes. Automating these elements not only mitigates risk but also enables skilled operators to focus on higher-level tasks such as data analysis and process optimization.
To successfully automate a testing system, every candidate step must be clearly defined at the right level of detail and function as a self-contained operation set. Each step also needs to be supported by technology that can reliably replicate it and be seamlessly integrated into the broader system.
Automation in mechanical testing
In the realm of force and torque testing, implemented in R&D, product design or QC stages, automation delivers measurable improvements across time, cost, accuracy, and throughput. Automated systems streamline mechanical testing processes by eliminating repetitive setup and execution steps. This leads to faster cycle times, reduced manual labor, and more efficient use of technical staff.
Cost efficiency is realized through reduced labor requirements, fewer retests due to errors, and better resource utilization.
Accuracy improves because machines can apply force and motion with precision, adhering to international standards without the inconsistencies associated with human operation.
Throughput increases significantly as systems can run continuously, often processing more samples and generating more data in less time. This improved responsiveness directly supports many production efficiency and quality assurance goals.
Some testing standards specify a recommended hardware setup, including performance and precision levels that automated systems can consistently meet or exceed. By minimizing the potential for human error, automation helps ensure that test results remain valid and reproducible over time and by extension, consistent at global locations across the business.
Importantly, automation does not necessarily eliminate human input but rather leverages human expertise by removing low-value tasks and focusing attention on interpretation and decision-making.
Mechanical testing of physical properties under tension, compression, or torque loading, serves two main functions in quality assurance: validating product design and monitoring ongoing production consistency. Automation supports these objectives through both hardware and software enhancements.
Automation In and Around the Universal Testing Machine
The universal testing machine (UTM) is a modular system, with each element—whether hardware, software or flesh and blood—forming part of a system focused on a specific end objective. These physical elements and procedural steps could all be candidates for consideration to automate.
The industry context and purpose of the system’s implementation heavily influence the feasibility and execution strategy of an ‘automation upgrade’. A phased approach is common, beginning with basic automation and expanding incrementally by adding sample handling, integration with quality systems, and data management tools.
Energy sector example: Catalyst pellet crush testing
Catalyst pellets are essential for refining and chemical processing—in addition to processing-related roles in agriculture, food and beverage, and pharmaceuticals—where they must withstand pressure and mechanical stress within reactor systems. Crush strength is a critical factor in determining the operational durability of catalyst pellets. The ability to resist deformation or fracture under loading directly affects performance and lifespan. Regulatory and industry standards often mandate detailed documentation of testing conditions and results, making reliability and traceability essential.
Crush testing typically follows established protocols, like those documented in ASTM D4179 and ASTM D6175 test standards for single pellet/particle test samples, specify sample loading, compression rates, and evaluation criteria. These tests are inherently destructive and require statistical evaluation of multiple samples per batch—ASTM D4179 specifies 50 to 200 individual pieces.
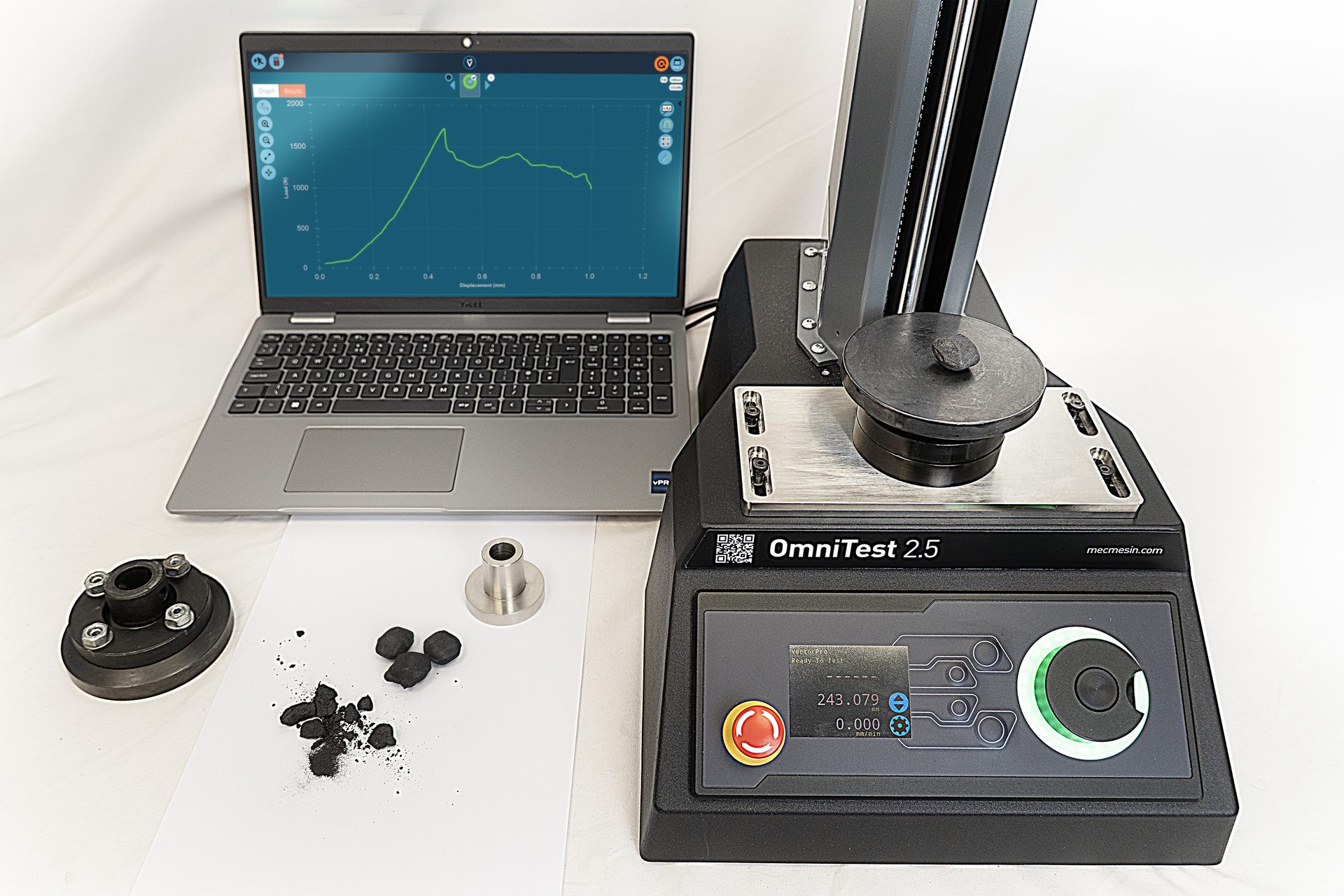
A single test sample is placed, crushed and the real-time results are displayed. The procedure is initiated from the software by the operator and the next sample in the batch is tested by repeating the process.
These types of tests in the energy sector provide a powerful example of automation's benefits, expanding on the above crush strength testing of single catalyst pellets. Though it may represent a small part of the overall production process, automating this test delivers measurable benefits in terms of consistency, efficiency, and compliance.
Automation is a natural fit for such testing. The process is highly repeatable and well-standardized, and benefits from precision loading, consistent force application and robust data capture. By automating this single, self-contained testing operation, organizations can achieve a high return on investment (ROI) without overhauling their entire production line. This modular approach enables gradual adoption and scale-up as needed.
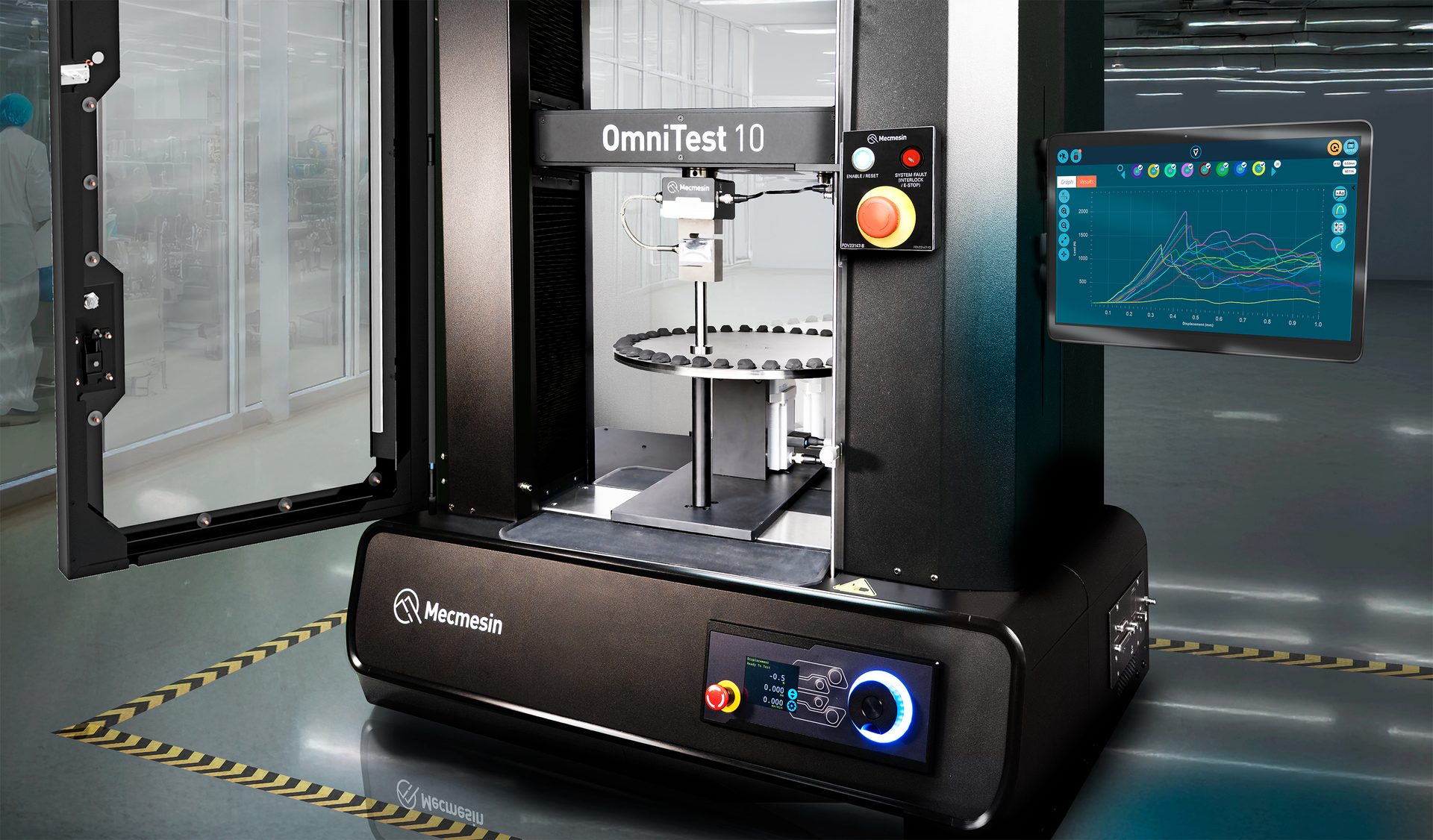
Automating the physical compression test of the samples includes the positioning, the crushing operation and rotating the platen for the next sample to align under the compression probe. Human operators load a number of specimen pellets onto the next platen for the next cycle. The software already has the built-in capability to capture the data for multiple tests and calculate graphical and tabular results according to an ASTM materials standard.
In addition to performance optimization, regulatory pressure in the energy industry further drives the need for automation. Quality documentation, test repeatability, and traceable results are often non-negotiable. Automation ensures that these requirements are consistently met, while also providing operational benefits such as faster turnaround and higher sample throughput.
As global energy demands rise, so does the need for efficient, reliable materials testing in this industry. Automation provides a “cool-headed” solution to this high-pressure challenge.
Software: The heart of metrology automation
While hardware handles the mechanical aspect of the test, software is the engine that powers automation. Modern testing platforms rely on software to control workflows, acquire data, analyze results, and manage traceability.
Workflow orchestration through software allows for consistent execution of operational steps, repeatable sequences, and flexible programming of test routines. Data acquisition is synchronized with load and displacement sensors to record every moment of the test. Automated calculations determine physical properties such as peak load, stiffness, energy absorbed or apply a formula to return a specific attribute, such as ‘crush resistance’.
Computer control of universal testing machines has been standard practice for years, allowing users to precisely set test parameters, monitor data in real time, and generate reports. However, fully automating a testing system may need to go further—potentially requiring low-level Programmable Logic Controller (PLC) integration to integrate peripherals like feeders, ejectors, or sensors, closing the electro-mechanical loop and synchronizing every part of the process.
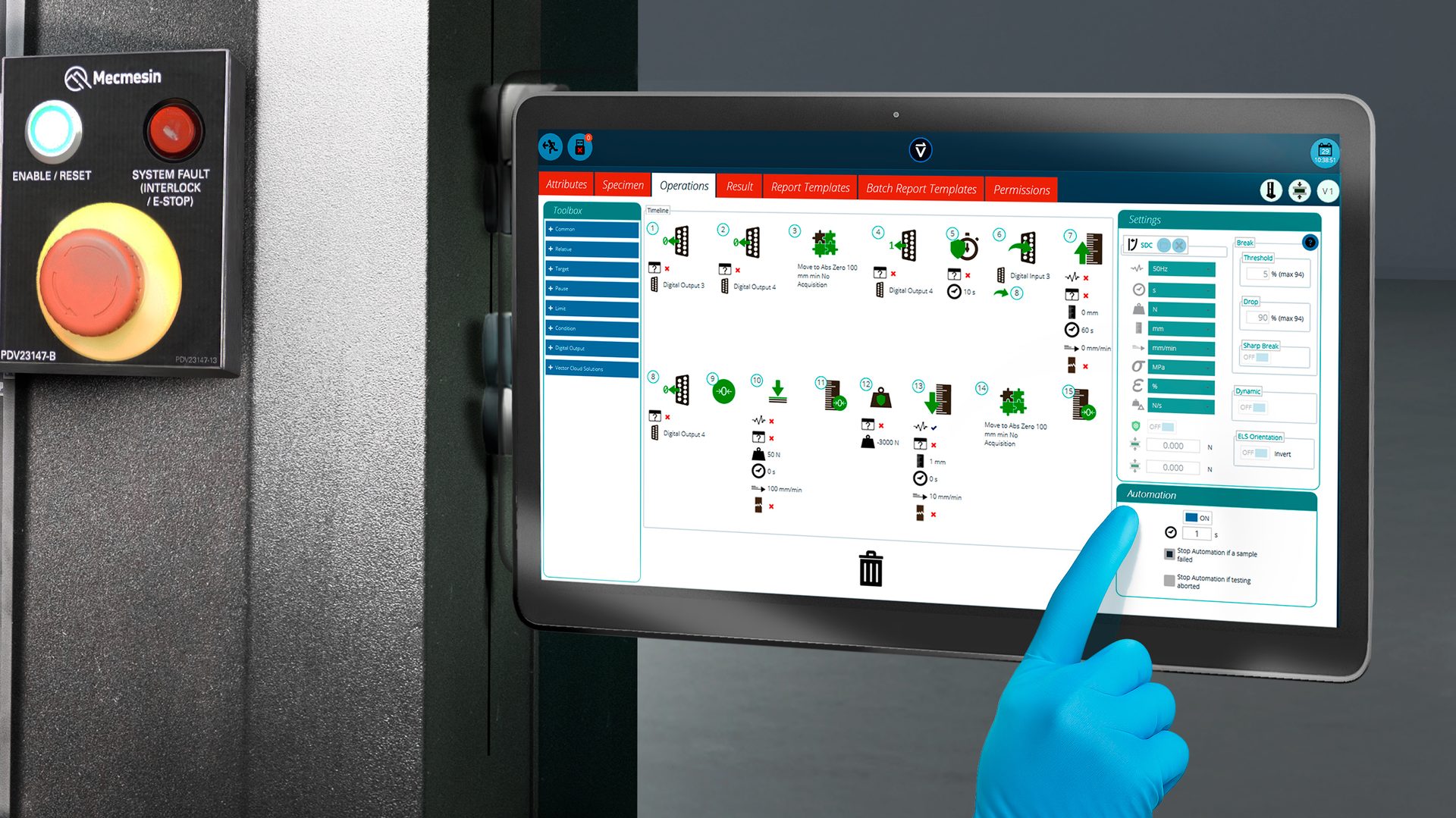
UTM software controls the 15 operational steps in this ASTM test procedure. A fully automated solution will require the software to respond to digital I/O triggers synchronized to hardware events, by interfacing completely—waiting, responding and sending instructions to the next element, automatically. Some human interaction will be needed to hand off control.
Stepping it up
In addition to software customization, the next logical step in extending the automation capability of a test system may require changes to its physical hardware. This might include integrating robotic arms for sample handling, modifying or upgrading grips to suit automated loading, or adding sample hoppers and feeders to streamline throughput. These components work in concert with the software and PLCs to create a fully automated, repeatable testing process tailored to specific sample types and test environments.
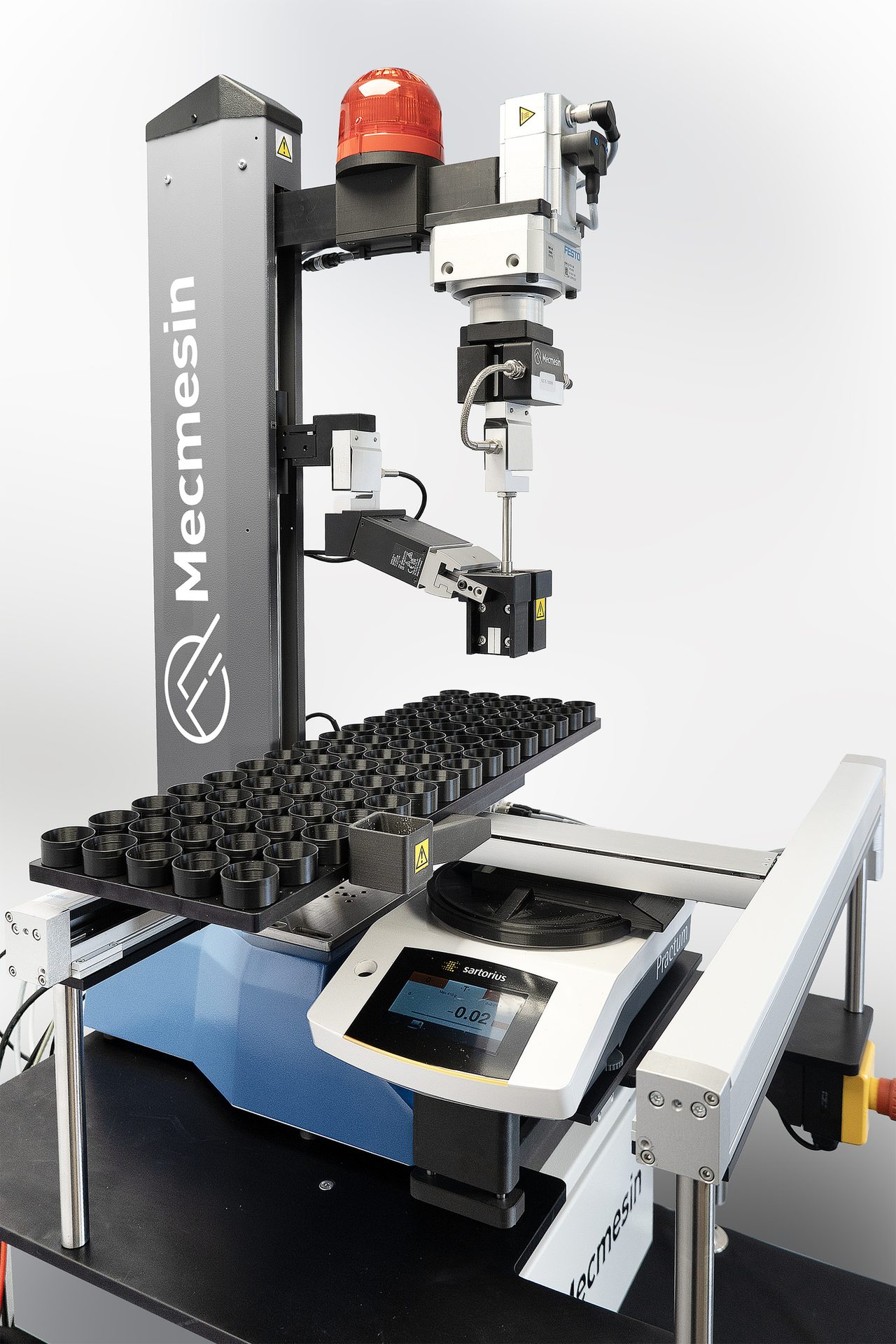
A robotic arm and pneumatic grips synchronized with hand-picking test specimens from a tray of 75 in a single batch run. Additional outboard components (a weighing station) are connected to complete each step in this particular self-contained procedure.
Conclusion
Automation in physical properties testing is a strategic investment that enables higher precision, greater throughput, and more actionable data. From general principles to specific applications like catalyst pellet testing, automation strengthens quality control while freeing human talent for higher-value tasks. By integrating automated systems into broader workflows and leveraging the power of software, manufacturers can build smarter, more responsive testing environments—a foundation for the next generation of quality assurance in the energy industry and beyond.
The decision to implement automation (as with many change initiatives) is often guided by return on investment. Organizations must consider time savings, reduced rework, increased test reliability, and the redeployment of skilled personnel to higher-value tasks.