Products
the latest products to help you improve your manufacturing process
SinceVision SHS Series High-Speed Camera
SinceVision has announced the release of its SHS Series High-Speed Camera, a powerful new tool designed for real-time imaging applications in industrial inspection, scientific research, and media production.
The SHS Series addresses a critical challenge in high-speed imaging: how to capture and transmit ultra-fast, high-resolution footage without delay. Featuring a full HD 1920×1080 global shutter CMOS sensor and CoaXPress 2.0 four-channel interface, the SHS Series achieves frame rates of up to 2250FPS and transmission speeds up to 50 Gbps—significantly reducing latency and eliminating post-capture bottlenecks. The SHS Series includes four models: SHS-101, SHS-103, SHS-201, and SHS-202.
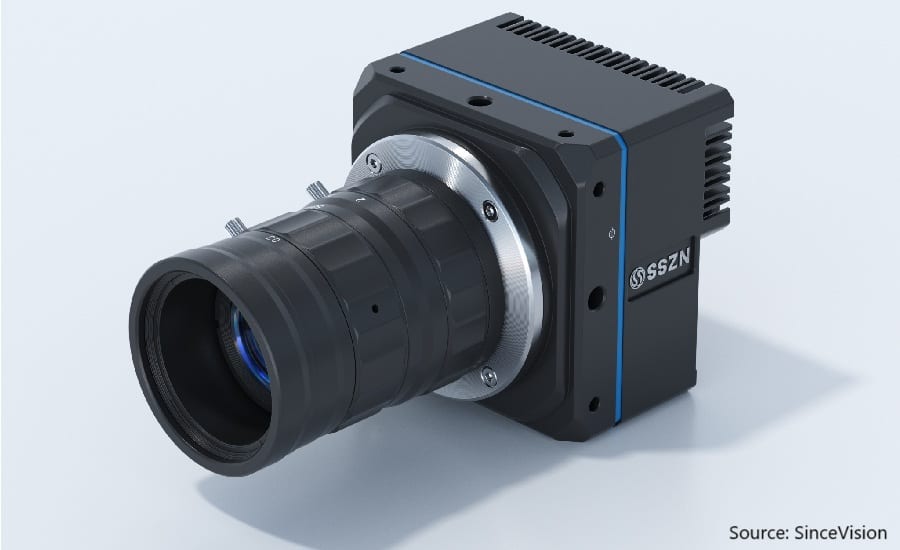
“We designed the SHS Series for engineers, researchers, and filmmakers who need real-time feedback without compromising image quality,” said Jack Li, global sales and marketing director at SinceVision. “This camera delivers clarity, speed, and reliability in one compact unit.”
Key Features:
- Resolution & Speed: 1920×1080 at 2250FPS with ROI support for higher frame rates
- Transmission: Real-time data transfer via CoaXPress 2.0 (CXP-12 × 4 channels)
- Design: Ultra-compact (72×72×60mm), weighing only 430g, with effective heat management
- Software: Intuitive, self-developed acquisition software with a frame-loss protection mechanism
- Durability: IP64 rated, tested for 70g impact, and certified for EMC environments
Applications Include:
- Industrial: Laser welding monitoring, automated machinery observation
- Scientific: Fluid mechanics, fracture testing, microfluidic experiments
- Sports & Biomechanics: Motion tracking, trajectory analysis
- Film & Broadcasting: Super slow-motion special effects capture
The camera also comes equipped with SinceVision’s proprietary image acquisition software, engineered to be both powerful and accessible, even for non-specialists. The software includes robust data integrity tools to prevent frame loss—critical in environments where accuracy is paramount.
SinceVision
https://www.sincevision.com/
Xiris Automation NIR Weld Camera System
Xiris Automation announced the release of its NIR (Near Infrared) Weld Camera System with a remarkable 140+ dB High Dynamic Range (HDR) imaging capability with advanced NIR illumination that can be synchronized to the camera.
Tailored especially for open arc welding processes where a clear view of the arc and surrounding background is needed, the NIR Weld Camera System delivers crystal clear views of the welding electrode, weld arc, melt pool, and surrounding background.
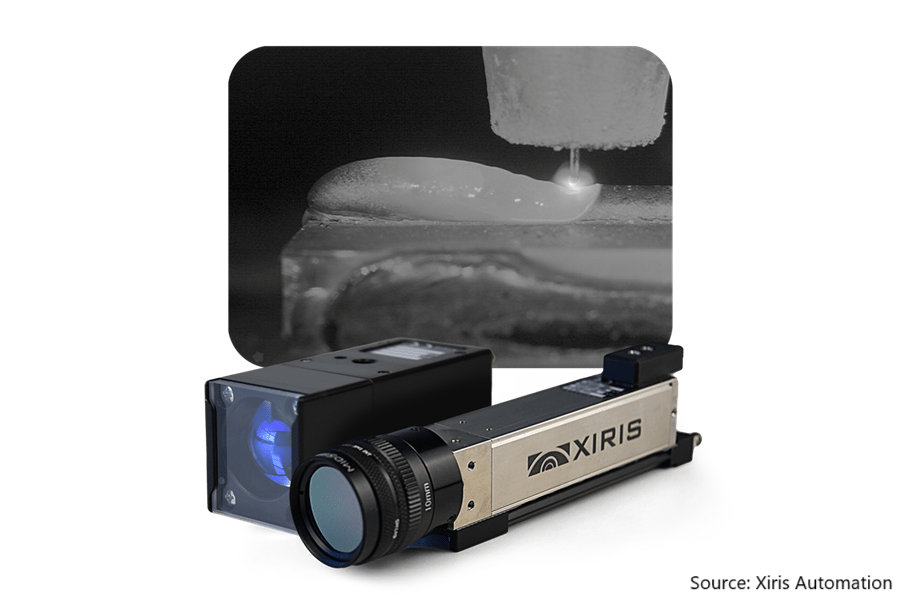
With its modular design of camera plus up to 3 remote LED light sources, the system can seamlessly integrate with any welding automation equipment, providing excellent image quality for process research, additive manufacturing, welding education and welding production applications without the use of dangerous to eye lasers.
Using a NIR camera and NIR LED illumination together, the system generates stable, robust images of high contrast weld features that enables both manual remote monitoring as well as advanced Machine Vision analysis. The LED illumination module can be mounted remotely from the camera, providing flexible optical setups.
Stable, high contrast images are key to making precise geometric measurements and defect detection of weld processes. Combined with Xiris’ AI-powered machine vision package WeldStudio™, users can measure and track vital welding features, or detect defects in their process to meet the demands of even the most challenging fabrication standards in use today.
The Near Infrared Camera System is suitable for integration into most types of weld automation systems, particularly for demanding GMAW and GTAW processes.
Xiris Automation
https://www.xiris.com/
X-Rite CiF3200 Imaging Benchtop Spectrophotometer
X-Rite Incorporated announced the launch of the CiF3200 imaging spectrophotometer, designed for color measurement of small, odd-shaped, multi-colored, and highly reflective items. With a minimum measurement area of just 2mm, the CiF3200 allows manufacturers to set and communicate digital color standards for small components, improving quality control and reducing rework. It’s ideal for applications where detail, consistency, and accuracy are essential, such as luxury goods, consumer electronics, and plastic components.
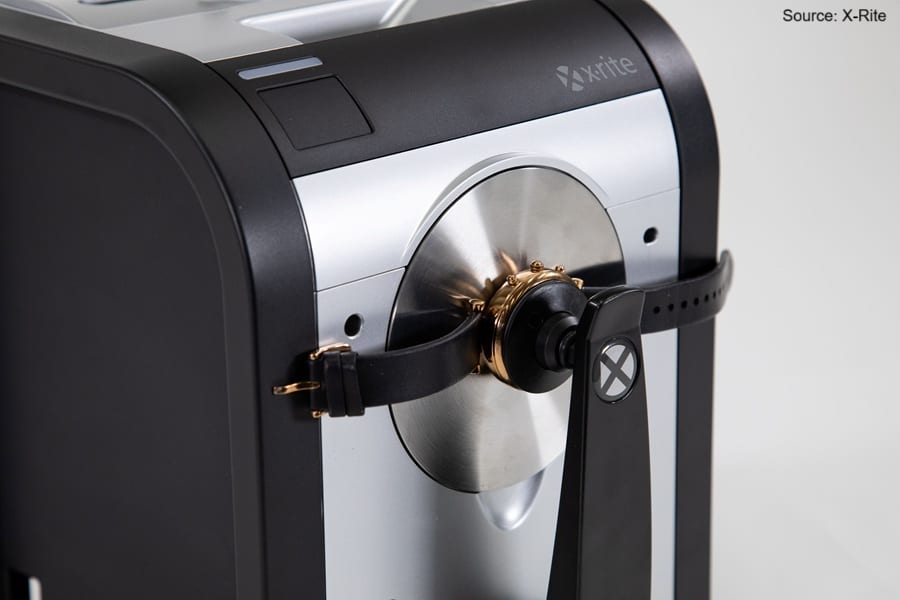
The CiF3200 combines advanced features such as virtual apertures ranging from 2–12mm, on-screen targeting for precise sample alignment, and automatic multi-color extraction to deliver fast, repeatable color measurements and support objective, data-driven evaluation. The CiF3200 sphere benchtop spectrophotometer offers simultaneous SPIN / SPEX capability. It enables brilliance measurement, which is critical for quality control on metals and materials that may exhibit visual variation due to surface finishing and metallic reflection. Whether maintaining color harmony for luxury watches or verifying part-to-part consistency on small, molded goods, the CiF3200 helps manufacturers elevate quality assurance with confidence and efficiency.
“With the CiF3200, we’re addressing a unique need in the industry – how to consistently measure color on small or oddly shaped parts,” said Dave Visnovsky, Product Manager, X-Rite. “By combining advanced targeting and imaging with sphere measurement technology and an aperture as small as 2mm, the CiF3200 allows customers to digitize their standards and streamline quality control in ways that simply weren’t possible before.”
The CiF3200 enables users to:
- Set and communicate digital color standards for small or complex components.
- Verify each measurement spot with live on-screen targeting.
- Capture and store measurement images for traceability.
- Extract multiple colors from a single sample for comprehensive analysis.
X-Rite Incorporated
https://www.xrite.com/categories/benchtop-spectrophotometers/cif3200
KUKA Automated Arc Welding
KUKA Robotics’s automated arc welding portfolio consists of the KR CYBERTECH nano ARC Edition robot for simple, cost-effective welding that provides dynamic automation in price-sensitive markets. The Edition robot is available in two reaches from 1,440 mm to 2,010 mm and features a hollow wrist with bearings on either side of the robot with a diameter of 46 mm and a repeatability of 0.04 mm. The robot delivers an extremely high path accuracy and speed to workpieces for maximum efficiency and less downtime.
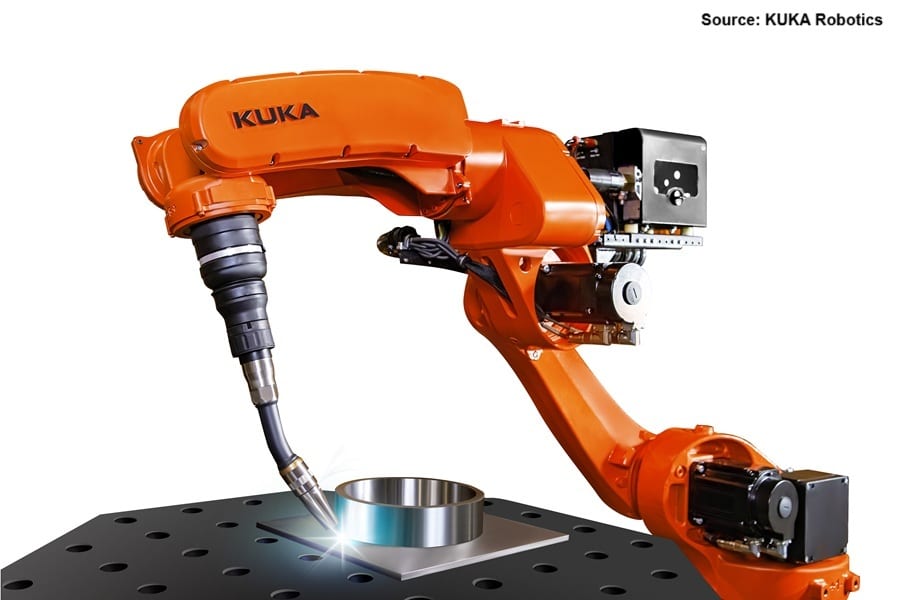
Edition robots use the latest-generation KR C5 controller and appropriate welding software, such as KUKA.ArcTech Basic. The variant offers simplified, focused and reliable technology as well as significantly lowering procurement costs.
KUKA will also debut the new arc cellerate cell, the company's standardized welding solution designed to offer an economical and efficient option for high-mix, low-volume applications. Available in both index and side-by-side configurations, these fully equipped cells are ready to perform a wide range of welding tasks, delivering exceptional flexibility for diverse manufacturing needs.
KUKA Robotics will feature automated arc welding robotics and technology at FABTECH 2025 from Sept. 8-11 at McCormick Place in Chicago, Ill. Visitors to booth #B17039 in Hall B of the North Building will see live demonstrations of the company’s KR CYBERTECH nano ARC Edition robot.
KUKA Robotics
my.KUKA.com
Instron AVE3 Advanced Video Extensometer
Instron® announced the release of the AVE3, an advanced non-contacting video extensometer that delivers precise strain measurement with unparalleled, micron-level accuracy for tensile, compression, and bend testing.
The highly versatile AVE3 can measure both modulus and strain to failure on a diverse range of materials such as plastics, metals, composites, biomaterials, textiles, and elastomers—along with sensitive materials like films and foils. Compliant with ISO 9513 and ASTM E83, the AVE3 allows labs to reliably test to any standard with one device, without needing to purchase and maintain multiple clip-on extensometers.
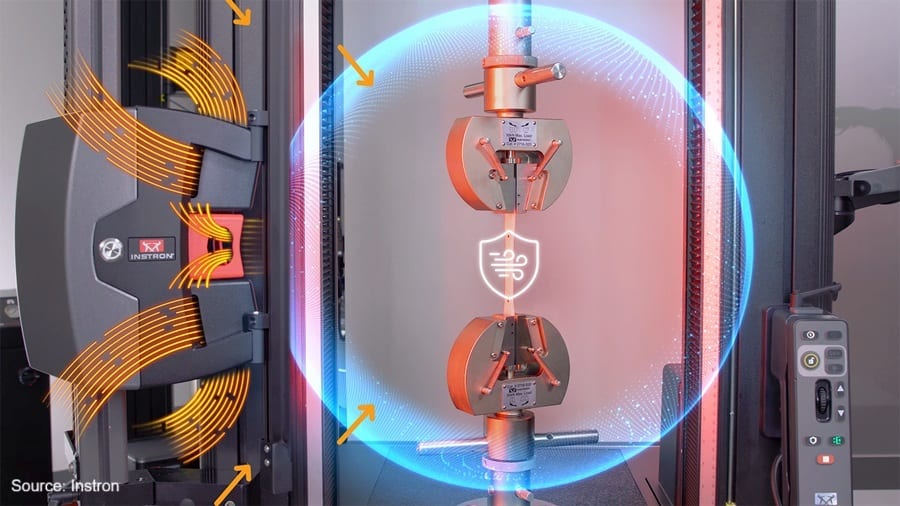
The AVE3 can be configured to accommodate a range of gage lengths and elongations. New kinematic mounting enables each lens to automatically snap into the factory-calibrated location, making it easy to capture accurate data every time.
To guard against typical lab air disturbances like HVAC systems and human operators' movements, the AVE3 uses Instron's patent-pending Constant Density Air Tunnel (CDAT) technology, which creates a force field–like protective barrier around the test space.
This CDAT airflow technology eliminates errors, reduces noise in test data, and improves accuracy by as much as five times (compared to video extensometers without CDAT technology).
In addition, Instron's Dynamic Cross-Polarized Lighting system provides a robust solution for fluctuating lighting conditions in different lab spaces. The patented system dynamically adjusts its illumination levels to ensure all markings on the specimen are perfectly illuminated for consistent results in any test environment.
Designed for compliance with ISO 6892-1 and ASTM E8, the AVE3 extensometer enables closed-loop strain rate control — the preferred mode for testing strain rate–sensitive metals. This capability is especially valuable for laboratories focused on achieving consistent, repeatable results across different systems and locations. Leveraging CDAT airflow technology and advanced dynamic lighting, the AVE3 delivers a virtually noise-free strain signal, eliminating the need for heavy filtering that can distort results or introduce lag in test control.
"Environmental variability has long been the Achilles’ heel of optical strain measurement. Even minor shifts in lab temperature or lighting can introduce significant signal noise and undermine data integrity," said Casey Willis, Instron's Product Manager for strain measurement devices. "The AVE3 directly addresses these pain points with its patent-pending CDAT (Constant Density Air Tunnel) airflow technology and a patented illumination system — two core innovations that ensure consistent data, even in variable lab conditions. For labs that demand reliability at the highest level, the AVE3 sets a new benchmark."
Instron
www.instron.com
Large LK Metrology CMMs
Inspection using a coordinate measuring machine (CMM) in a production environment brings enormous advantages compared with transporting components sometimes considerable distances to a separate quality control (QC) room. Benefits include faster inspection, quicker reporting, reduced lead-times, rapid feedback on part conformity for prompt adjustment of manufacturing processes, increased output, reduced scrap and raised efficiency. Eliminating the need to transfer parts to another location saves labor costs and time, reducing the risk of damaging the parts being handled. It also allows the QC function to be closely integrated with production and automated if desired.
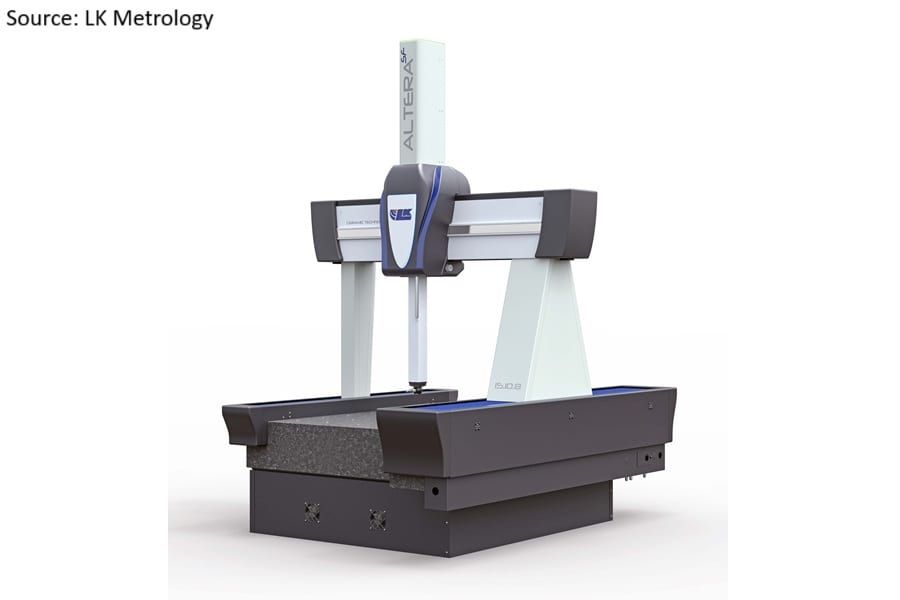
To meet such high precision inspection requirements in the rugged environment of the shop floor, CMM manufacturer LK Metrology, whose manufacturing facility is in Castle Donington, Derbyshire, has introduced eight bridge-type Altera SF models having laboratory-grade accuracy. These CMMS were launched at Control 2025, the annual international trade fair for quality assurance held at the Messe Stuttgart, Germany.
Normally, industrially hardened CMMs with the necessary temperature compensation and vibration isolation tend to be small to fit into confined spaces, but these new models have generous nominal axis travels ranging from 1,000 x 1,000 x 800 mm up to 4,000 x 1,500 x 1,500 mm. The large measuring volumes mean that bulky workpieces can be inspected near where they are produced, while the extra capacity affords more operational flexibility by allowing QC requirements to be met across a wider variety of component sizes.
All SF-series CMMs have a ceramic bridge and spindle with outstanding stiffness-to-weight ratio, thermal characteristics, dimensional stability and longevity. Friction drives with air bearings provide smooth axis movements, leading to high accuracy laser or analogue scanning, or touch-trigger probing. Either a Renishaw PH10MQ PLUS indexing probe head may be used, or a REVO2 head which converts the CMM into a 5-axis Scantek model. Both heads support multi-sensor technology.
Covers protect the guideways from thermal influence, accidental damage and contamination, aided by positive internal air pressure to prevent the ingress of dust and vapor particles. Fans under the granite table ensure a continuous flow of ambient air to avoid thermal imbalance in environments where there is no temperature control, as is the case on most shop floors. Temperature sensors embedded in each axis of the CMM monitor heat fluctuations within the structure and compensate all measurements to a 20°C reference. Optionally, thermistors can be clamped or attached magnetically to a workpiece, or integrated into its fixture.
In a notable departure from the construction of LK's other ceramic-type CMMs, which use stainless steel linear encoders, Altera SF machines incorporate glass-ceramic optical scales that have zero thermal expansion as well as superior immunity to contamination, minimizing potential sources of measurement error. The low-maintenance scales have excellent long-term stability, while signal stabilization results in low and predictable interpolation error.
Elastomer anti-vibration and shock-absorbing mounts isolate the CMM from sources of mechanical disturbance, such as machine tools. Passive anti-vibration may be specified, but to ensure maximum measurement accuracy, active intelligent anti-vibration is recommended. It involves built-in magnetic field sensors that detect the load on the table and monitor its height and level, enabling them to be automatically adjusted electro-pneumatically to within ±0.1 mm and 0.9 mm respectively. As the sensors are non-contact, they remove the disadvantage in traditional mechanical-pneumatic compensation systems of having an integrated tappet, or plunger, which is exposed to contamination and is a potential conduit for vibration transfer.
Altera SF machines, with their proprietary LK NMC300 multi-purpose controller and CAMIO software suite, are ready for in-line or line-side automation to suit large volume production. Status lights on the CMMs are standard, as is real-time monitoring of quality data, CMM performance and system status on smart devices. Numerous safety features ensure the safety of personnel and of the equipment itself, without compromising productivity and efficiency. An optional EcoAir function reduces compressed air consumption by 95% when the CMM is idle to reduce operating costs. Likewise, power to the CMM motors is automatically switched off after a period of inactivity.
LK Metrology
lkmetrology.com
New MVTec HALCON Version Includes Deep Learning-Based Technology
MVTec Software GmbH is launched the new version of MVTec HALCON on May 27, 2025. Version 25.05 of the standard software for machine vision includes numerous improvements as well as a new technology that combines deep learning algorithms with classic methods.
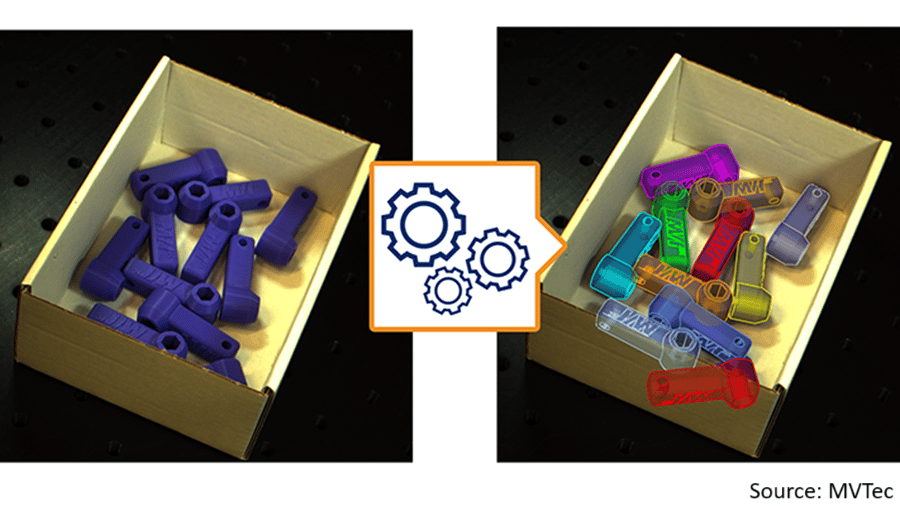
“We always want to offer our customers the latest machine vision technologies and continuously update existing features. With the new HALCON version, we have once again achieved this goal. With Deep 3D Matching, we are providing a technology that has never existed in this form before. At the same time, we have further improved the performance and usability of existing deep learning methods,” says Jan Gärtner, Product Manager HALCON at MVTec.
Deep 3D Matching, which was already available with limited functionality in the previous version, is particularly suitable for bin-picking and pick-and-place applications. Depending on the requirements, one or more cost-efficient standard 2D cameras can be used to determine the position. As part of the improvements, the neural networks have been optimized for deep learning-based text reading. In addition, the code reader for QR codes has been improved, a new set of operators for image acquisition have been added, and many other smaller improvements have been made.
“At the moment, a particular important topic for MVTec is the new development of the integrated development environment HDevelopEVO. Users can already test HDevelopEVO. For the new version, we have extended the range of features that can be used,” explains Jan Gärtner.
Deep 3D Matching is a new deep-learning-based technology for fast and robust 3D object detection and pose estimation using 2D images. It requires minimal parametrization and delivers high performance, making it ideal for applications such as bin picking and robotic handling – even in challenging conditions.
With HALCON 25.05, users can now train their own Deep 3D Matching models independently, without requiring MVTec support. A new renderer allows them to generate training data from a CAD model of the relevant object and thus also enables training exclusively with synthetically generated, labeled data. This allows for a very flexible setup and can cover various object properties like reflections and transparency.
With the new training functionality, customers can now create 3D matching applications tailored to their specific needs and environment. If desired, model training can still be commissioned as a paid service through MVTec.
In some applications, running Deep OCR’s detection model, which localizes word regions in the image, may not be feasible due to tight cycle time constraints. In such cases, users define text regions manually or through rule-based image processing, which can lead to inaccurate recognition due to suboptimal crops.
With HALCON 25.05, Deep OCR thus includes an alignment step before recognition. This step refines rough word crops, significantly improving reading accuracy even when text regions are placed imprecisely. As a result, users can bypass the detection model while maintaining reliable OCR results – leading to a considerable reduction in processing time.
This makes text recognition workflows not only more flexible but also much faster, as precise ROI (region of interest) placement is no longer required. The alignment step itself is highly efficient and adds only minimal processing overhead.
With version 25.05, HALCON improves its code reader with QR code rectification, enabling reliable reading even on curved or deformed surfaces. This expands application possibilities in industries such as logistics, packaging, food production, and bottle labeling, where QR codes often appear on non-flat materials. The rectification process ensures higher readability without requiring perfectly flat surfaces. It is optional and can be enabled as needed. While processing time is slightly longer than standard QR code reading, the improved robustness makes it a valuable addition for demanding applications.
The 25.05 release of HALCON also adds the possibility to interrupt training for Generic Shape Matching, giving users greater flexibility and control over the process. Training can now be stopped manually or limited with a timeout (e.g., after 1 second), ensuring efficient operation without unnecessary waiting times. Previously, once training started, it had to run to completion, which could lead to delays – especially in embedded applications with limited resources. Now, users can seamlessly integrate training into their workflows, preventing long processing times and improving responsiveness.
HALCON 25.05 introduces a new set of image acquisition operators designed for seamless integration with state-of-the-art camera technology. While MVTec has always focused on efficient camera connectivity, modern standards like GigE Vision and USB3 Vision bring both new opportunities and new challenges. The new interface simplifies camera handling while providing full control over advanced configurations.
These new operators provide a clearer, more intuitive interface, optimized for standard use cases, while maintaining full control over the GenICam GenTL architecture. Additionally, they support multiple streams if provided by GenICam GenTL devices. Users can expect performance equal to or even faster than previous operators, ensuring a smooth transition to the latest camera technology.
Together with HALCON 25.05, a new version of HDevelopEVO is also available, which provides users with various new features.
HDevelopEVO 25.05 introduces support for referencing procedures stored in external files. Users can now split their programs into multiple files and reference procedures across them. This enables cleaner program structure and is a first step toward future support for modular libraries.
To address a common need in machine vision workflows, the latest version also adds the gray value histogram – one of the most frequently used tools for image analysis. It enables the user to visualize the distribution of pixel intensities in an image and to interactively set thresholds to select relevant regions for further processing.
Lastly, to support developers more effectively, HDevelopEVO 25.05 also introduces AI assistants. These include an interactive chat, agents for, e.g., IDE commands and shell commands, and automatic code completion. Users can choose between cloud-based, self-hosted, or local AI models while maintaining full control over data and model usage. The AI assistants must be explicitly activated by the user.
MVTec
www.mvtec.com
HBK T210 IO-Link Enabled Torque Sensor
Hottinger Brüel & Kjær (HBK) has added IO-Link functionality to its T210 torque sensor, helping engineers perform R&D and end-of-line torque testing more efficiently while streamlining their processes.
The T210 provides precise torque, rotational speed, angle and power measurements – all in a compact, easy-to-integrate format. Each unit is delivered with an individual test report and is suited to a wide range of industries, including automotive, machinery manufacturing, pharmaceutical production, and high-end appliance and commercial goods sectors.
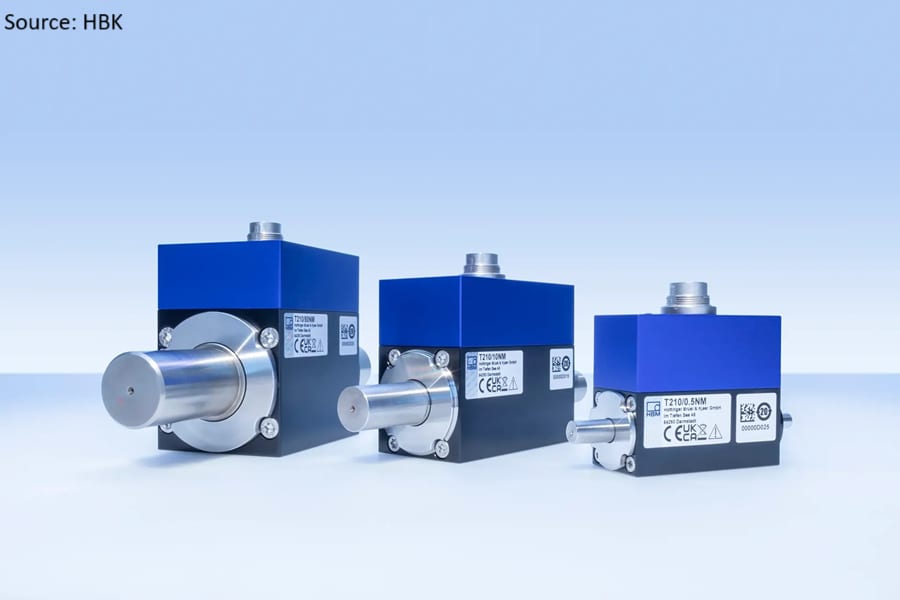
IO-Link is a fieldbus-independent, standardized communication interface that allows for digital, bidirectional point-to-point data exchange. Using standard M12 cables, the T210 can be quickly integrated into existing systems and connected to an IO-Link master. The IO-Link master manages protocol conversion and makes real-time measurement data available to all common fieldbus and automation systems, including EtherCAT and Profinet.
The new IO-Link interface enables the digital transmission of not only measurement data but also extensive process, diagnostic and statistical information – making it easier to optimize processes and analyze performance in different applications.
Compact and strain-gauge based, the shaft-style T210 is designed for easy integration into test benches, automation systems, or direct connection to the device under test. Its non-contact energy and signal transmission system ensures long-term reliability and high measurement precision.
Along with the new IO-Link interface, the torque sensor also includes voltage and frequency outputs for torque, speed, and angle, giving engineers flexibility across a wide range of applications, from development testing to automated end-of-line testing.
The T210 is available in nine nominal torque ranges from 0.5 N∙m to 200 N∙m, and can be paired with a variety of accessories, including cables and bellows couplings. This makes it simple to integrate into existing setups – or quickly reconfigure for different measurement tasks.
Hottinger Brüel & Kjær (HBK)
www.hbkworld.com
Siemens Next-Generation Motion Control System
At this year’s AUTOMATE, Siemens announced the launch of its enhanced motion control portfolio, featuring SINAMICS servo-drive systems and the new SIMATIC S7-1200 G2 controller, delivering enhanced performance and flexibility for basic automation applications including handling, moving, positioning and processing.
The new solution combines three key innovations:
- Advanced SINAMICS S200 and S210 servo-drive systems
- New SIMATIC S7-1200 G2 controller
- Compatible SIMOTICS servomotors
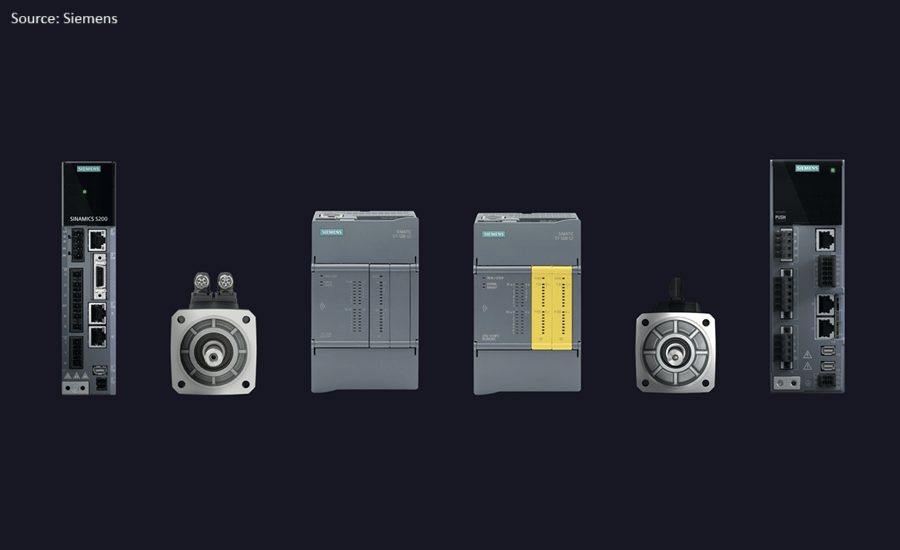
“This holistic system approach represents a significant leap forward in basic automation capabilities,” said Craig Nelson, product manager, motion control, Siemens Industry, Inc.
- Key features and benefits include:
- Enhanced processing power with dedicated communication performance and extended memory
- Support for up to 31 PROFINET devices with synchronized program execution
- Integrated motion control technology objects for simplified system configuration
- Advanced safety features up to SIL3 / PLe and Category 4 certification
- Near Field Communication (NFC) capability for wireless access to diagnostic and device data
The new portfolio offers scalable solutions with various power options:
- SINAMICS S210 is available in voltage ranges from 200–400V with power ratings up to 7 kW
- Ultra-fast current controller response time of 62.5 µs
- Flexible configuration options for single axes, coordinated axes and simple kinematics
This cost-optimized solution includes comprehensive safety features, wireless diagnostics capabilities, and seamless integration with the Siemens TIA Portal, making it ideal for manufacturers seeking to modernize their automation systems.
Siemens
usa.siemens.com/servo-drives
usa.siemens.com/efficient-motion-control
KUKA Showcases Inspection Automation Solutions at Automate 2025
KUKA Robotics, in collaboration with System Partner IVISYS, showcased its automation solutions for pallet inspection at Automate 2025, held May 12–15 at Huntington Place in Detroit, MI. The joint exhibit emphasized the critical role of precision and reliability in pallet manufacturing, featuring PALLETAI—an advanced system designed to ensure pallet quality at every stage of operations.
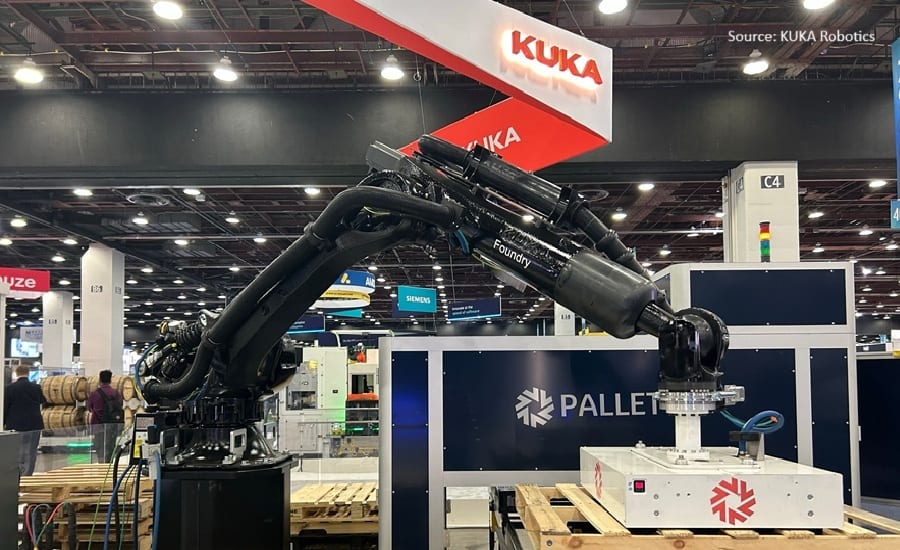
In a demonstration, KUKA featured its KRQUANTEC-2 high-payload robot in a wooden pallet manufacture and refurbishment simulation scenario. For such applications, KUKA’s QUANTEC robot family covers a range of payloads from 120kg to300kg and reaches from 2,700mm to 3,900mm.KR QUANTEC-2 robots also feature digital motion modes/software add-ons that allow manufacturers to select the optimal robot motion for their specific applications. “Path mode,” for example, provides greater accuracy and precision while “dynamic mode” increases speed and reduces cycle times. Plus, the KRQUANTEC-2 family encompasses variants for special certifications and product classifications such as Hygienic Oil (HO) or Foundry (F).
In the demonstration cell, the robotic system picked up a pallet, scanned it and assessed its quality based on customer-defined criteria before directing it to the appropriate stack. Technology partner IVISYS' PALLETAI pallet inspection solution scanned pallets and generated real-time data, assessing compliance with user-defined quality standards. High-resolution images were then fed through AI neural networks and transferred to the IVISYS cloud for immediate analysis.
As with all the company’s automation solutions, those shown at Automate 2025 are backed by KUKA’s expert service and support for training, complete system engineering and simulation, readily available spare parts, robot refurbishment and more. All these features are easily accessible through the my.KUKA.com site, and KUKA maintains corporate offices and production operations, along with integration partner facilities, conveniently located throughout North America to provide responsive customer service and support.
KUKA Robotics
kuka.com
Mahr MarTest 800 EWR Digital Test Indicator
Mahr Inc. announced newly updated MarTest 800 EWR digital test indicators. The new versions of the 800 EWR incorporate an enhanced measuring system that provides longer measuring ranges of up to ±0.035"/±0.9 mm and ±0.086"/±2.2 mm, allowing for better accuracy and versatility.
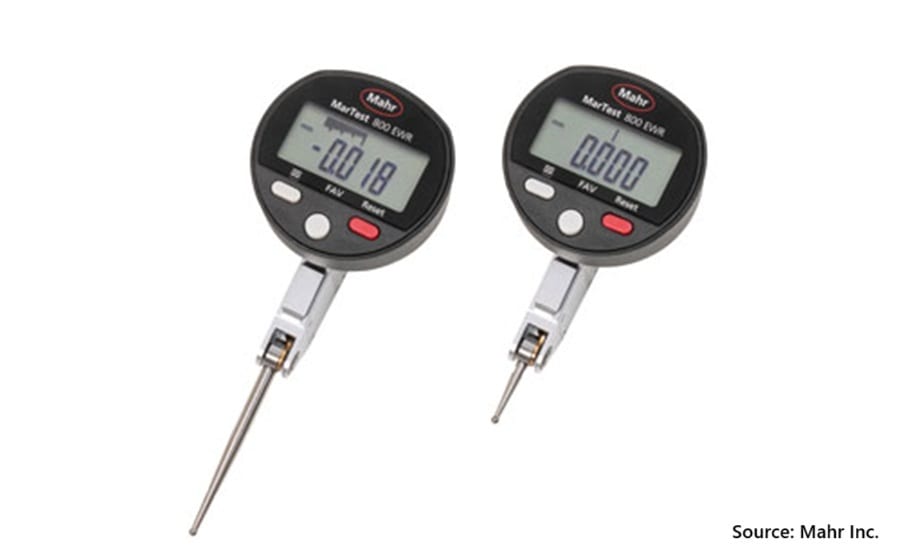
The MarTest 800 EWR combines the benefits of digital indicators, providing a longer measuring range with high resolution, enabling users to measure faster, more easily, and more reliably while minimizing errors. Combined with the ability to automatically sense measuring direction, rotate the bezel 360°, and overtravel protection features, the 800 EWR test indicator can replace numeral mechanical test indicators. The MarTest 800 EWR’s operating unit is also protected against coolants and lubricants, with a protection class of IP65. Its shockproof design and precision bearing supported lever contact offer maximum reliability in harsh environments. The full-surface glass display provides protection against liquids and dirt, which cannot penetrate the sealed housing.
Mahr Inc.
www.mahr.com
ABB AI-Powered Flexley Mover Mobile Robot
ABB is extending its portfolio of fully autonomous mobile robots by equipping its Flexley Mover® P604 with 3D visual simultaneous localization and mapping (Visual SLAM) navigation and user-friendly AMR Studio® programming software. The launch marks another milestone in ABB’s journey towards autonomous mobile robots that are more versatile, efficient and easier to use.
“ABB has perfected robot eyes, through 3D AI vision technology; hands, through advanced force-sensing, precision dexterity and machine learning; and independent mobility, through 3D mapping”, said Marc Segura, President for ABB Robotics. “Fusing these technologies gives our robots a complete and dynamic understanding of the world around them, enabling safer, more intelligent and autonomous operations for our customers across automotive, manufacturing and logistics.”
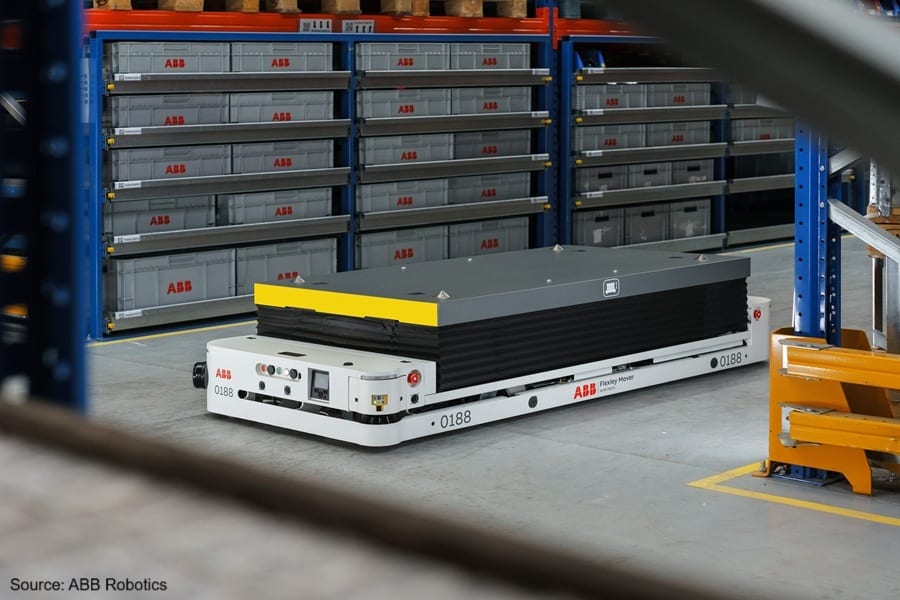
ABB’s Flexley Mover is designed to lift and transport objects across a variety of payloads in a variety of settings, enabling greater efficiencies in applications including intralogistics and kitting operations.
Accurate to within 10mm, the positioning technology is matched to an AI learning algorithm that enables each robot to generate its own maps of its workspace and securely share this knowledge with other robots in its fleet, to enable fully independent, flexible and scalable navigation alongside human workers, with no need for additional infrastructure.
According to Industry ARC (Analytics Research & Consulting), the market is expected to grow at a rate of 21.4 % percent CAGR by 2030 to reach $14.4.4bn1.
The capabilities of 3D AI vision are further amplified by ABB's innovative AMR Studio software, which provides a user-friendly platform for creating and configuring routes and tasks for AMRs, from standalone units through to entire fleets.
With simplified programming and graphical interfaces, the software reduces commissioning time by up to 20 percent compared to conventional systems, with potential cost savings of up to 30 percent.
Throughout this year, ABB will continue to focus on fusing its precision hardware with artificial intelligence and software, towards further autonomy and versatility.
Marc Segura concluded: “We’re in a new era of robotics innovation. Robots that can do more things, in more places, and do it faster, safer and smarter directly open the door to greater productivity and eliminate the need to invest in specialist skills or infrastructure. With our 50-year heritage as the original robotics innovator, we remain at the forefront of not just developing the latest technologies, but also engineering them for commercial use, at scale.”
ABB
www.abb.com
ABB Robotics & Discrete Automation
go.abb/robotics
Fixtureworks Stablelock Clamps
Fixtureworks® has bolstered its array of clamps, modular fixturing and set-up accessories by offering the stable and reliable Stablelock Clamp series.
Stablelock Clamps offer a rigid clamping mechanism with a ball and tapered wedge clamping design with spring force for superior mechanical positive clamping. Clamping force is constant and strong no matter the user or the application. A "click feel” at the end of clamping ensures reliable and safe operation while indicator lines on the handle and body align to clearly show when the clamp is locked or unlocked.
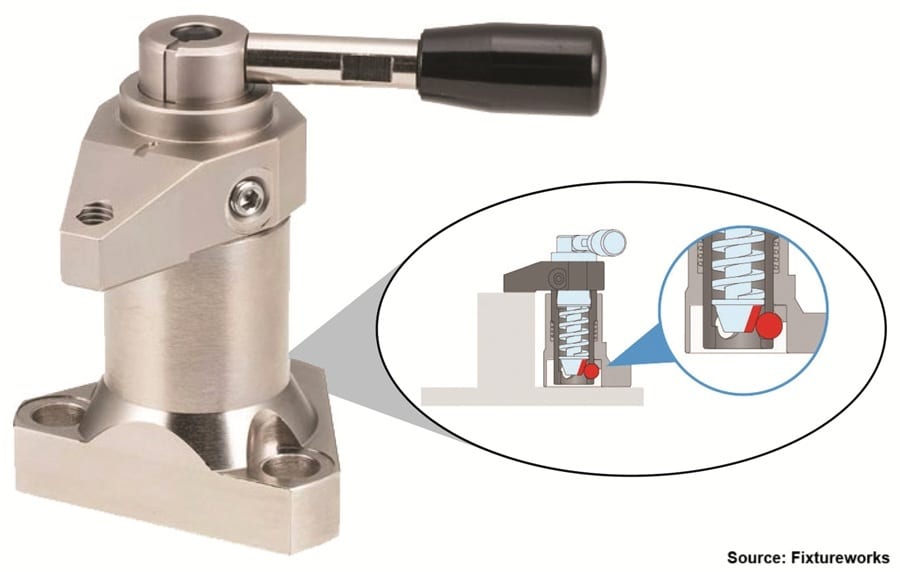
Fixtureworks Stablelock Clamps are available in a variety of clamping modes…swing, pull, push, side and thrust. The versatility of the modes offer expansive range of arm travel and length of arm options and makes these clamping choices for a variety of clamping, fixturing and workholding applications…and especially useful for highly repetitive clamping jobs.
The Stablelock Swing Clamps (QLSWW) swing into position and clamp straight down onto the workpiece for direct downward pressure. They feature constant clamping force and a clear clamping point. Turning the handle swings the arm into position. As the arm contacts the workpiece, the spring is compressed, and the tapered surface pushes the balls out to clamp the workpiece. Spring-loaded, these clamps generate constant clamping force with positive locking and spring force.
The handle’s "click feel” at the clamping end point, prevents workpiece damage due to overtightening while indicator lines on the handle and body align to clearly show when the clamp is locked or unlocked. The arm swings completely out of the way to allow for easy loading and unloading of the workpiece.
The QLSWW swing clamps, with steel electroless nickel plate bodies and lever arms with black plastic covers on the lever, offer ease of operation both in clockwise and counterclockwise motions, while the rotation of an ergonomic handle simultaneously swings the clamp arm out and over the workpiece and into the clamping position (up to 155° rotation). Then a final pressure on the arm draws the arm down and applies direct downward force on the part.
The Stablelock swing clamps are offered in clockwise (QLSWWR) and counterclockwise (QLSWWL) direction. They offer 19 lb. of operating load and up to 224 lb. of clamping force while being only over three inches in height in the clamped position and a little over a pound in weight all adding to their versatility.
In addition to Stablelock Clamps, Fixtureworks offers shaft locking clamps other quick change pneumatic clamping fasteners, quick action spring plunger clamps, handle and levers, knobs and grips, equipment handles, handwheels and cranks, hinges and latches, leveling supports, industrial rubber bumpers, stops and wheels, fixturing clamps, clamping locating systems, work positioning elements, vises, grippers and mechanical linear actuators.
Fixtureworks
www.fixtureworks.com
Musashi AI Surface Inspection AI Software Upgrades
Musashi AI introduces the latest updates to Cendiant® Inspect turnkey AI software and our Automated Shaft Inspector.
In automotive manufacturing, grinding machines are used on parts such as camshafts to achieve the desired profile. A part defect known as chatter can occur during the grinding process due to tool imbalance and machine vibration, leading to part quality issues and customer complaints. A new surface inspection model developed for Cendiant Inspect software specifically targets this issue, offering results similar to those achieved with dedicated optical shaft measurement machines.
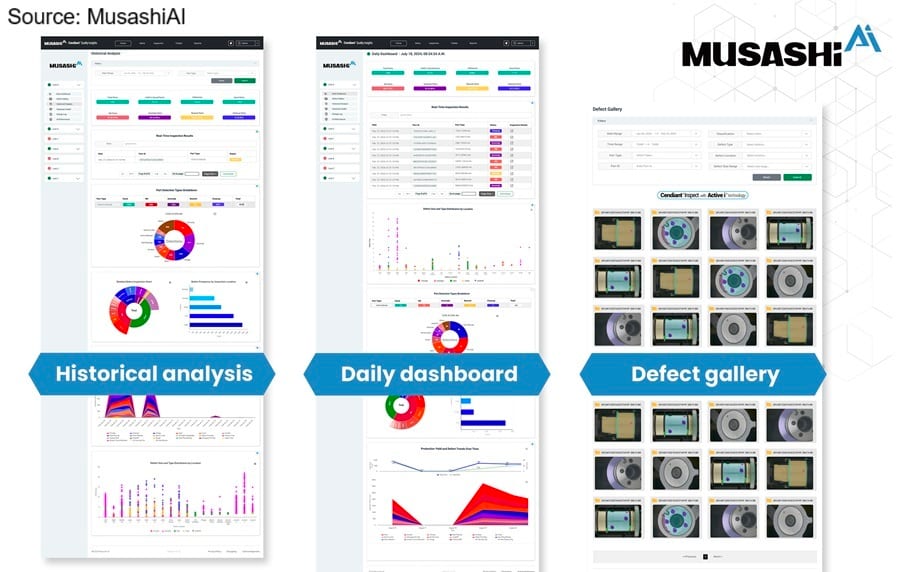
“Chatter is a production outcome that is common but difficult to detect, and this is a recurring message Musashi has heard from its customer base as of late,” says Frederick Reinink, business development specialist at Musashi AI. “With this new model, Cendiant Inspect delivers accurate and repeatable detection of defects that are nearly imperceptible to the human eye while replacing the need for time-intensive and costly optical shaft measurement machines. Ultimately, this reduces waste and rework.”
In addition to the software update, Musashi AI debuted a chatter inspection module at Automate 2025. The unit can be added easily to the standard Automated Shaft Inspector machine.
“AI-enabled automated inspection software today must be flexible enough to address a wide variety of complex applications across industries,” says Pierre Quenioux, North America sales manager at Musashi AI. “The introduction of the chatter inspection model is just an example of how Musashi AI can incorporate different inspection methods with our software to reliably detect the most challenging types of defects. We leverage our proven experience with complex automotive parts to provide automated AI solutions for high volume applications in the electronics, consumer goods, oil and gas, food, and paramedical industries as well.”
Improved Inspection, Faster Integration
Newly added to the Cendiant Quality Insights data visualization and insights platform is a ticketing system that keeps Musashi AI engineers in the loop. This tool allows customers to interact directly with the Musashi AI team to provide real-time feedback on inspection performance, allowing the team to address false negatives, anomalies, system changes or deviations, and overall system performance.
“With our surface inspection upgrades and the direct feedback ticketing system, Musashi AI streamlines processes for businesses and speeds up integration and deployment for integrators and manufacturers,” says Edward van Amstel, managing director of Musashi AI.
Musashi AI
musashiai.com