Face of Quality
Jim L. Smith
Face of Quality | Jim L. Smith
The marriage of quality and lean.
Link Quality and Lean, Part 2
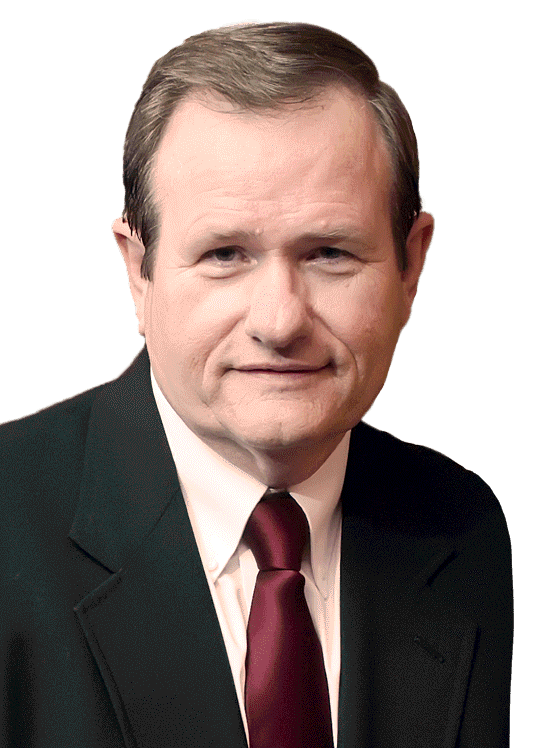
In part 1, we explored the linkage of quality and lean. In this segment, we will discuss how quality and lean should be married together in product and process redesign and improvement.
The answer is neither simple nor straightforward. During my time as quality systems manager at a research and development facility for a large manufacturing organization, we were effective at achieving some early success, and later team efforts exceeded expectations.
In many respects, the customer is the ideal place to begin the journey. You might begin by asking, “What are the required activities needed to create and deliver value to the customer without waste or additional steps in the process?”
Many think this might be easier in large organizations with a lot of resources. Of course, that makes sense, but the journey can be much more challenging because these companies generally have a lot of built-in inefficiencies. However, most companies that begin as smaller entrepreneurial enterprises have an edge, at least in the beginning, in that they typically are the definition of lean.
Initially, smaller enterprises have no additional capital to spend on processes that don’t directly add value. However, as these companies grow, steps are typically added as the division of labor increases along with the associated staff to support it.
As the number of steps, processes, and personnel grows, so does the variation which becomes the enemy lurking in the shadows. This variation reveals itself in output, the number of opportunities for mistakes, and the additional tracking of scrap but also with rework and repair activities necessary to prevent these problems from escaping into the hands of the customer.
Depending on the situation, organizations soon seek out a quality improvement strategy/activity, such as Six Sigma, to improve customer satisfaction. Or, maybe as a companion initiative, they look at lean manufacturing to reduce costs, thwart off a low-cost competitor or avoid market-driven pricing.
In either case, the objective is really the same… Hold onto and expand market share by delivering only what the customer wants. To achieve this, the organizations need to focus on both quality improvement through variation reduction and lean manufacturing.
When undertaking a lean activity like a kaizen event to restructure the workflow, organizations must focus on how well the current process operates and ask themselves three simple questions. (1) How well do the current processes match the customer requirements? (2) What are the sources of nonconformance in the existing production activity? (3) What are the current process capabilities?
The answers to these questions should then be fed back into process and product redesign to improve not only takt time but throughput as well.
Before beginning any undertaking, but especially with lean, a roadmap is required.
Before beginning any undertaking, but especially with lean, a roadmap is required. Without a map you can get lost in a quagmire of complexity. Analyzing the operation’s equipment, materials, processes and links with suppliers and customers prior to the kaizen event helps ensure success.
It must be clearly understood where the operation stands today compared with the quality needs of the customer. It also must be clear how close the operation can come to achieving a Six Sigma level of nonconformance free output.
Certainly, the measurement of results is critical and needs careful management. Peter Drucker, the late management consultant and author, reportedly said, “What gets measured gets improved,” and this holds great significance in the context of lean manufacturing. Consequently, organizations must measure the right things to get the right results from this effort. With that in mind, where we take these measures is equally important.
The commonly accepted method of process measurement (i.e., inspection) might not be right for a lean environment, but may be necessary as part of customer stipulations. Appropriate measurements of inputs and in-process activities are required to ensure the redesigned process stays in control. In any lean activity, the controls must be consistently monitored and improved.
Measurements should also take customer needs into consideration as well as customer satisfaction. They shouldn’t be restricted to just internal use or needs.
It should be stressed that any effort taken to implement quality objectives and lean methodologies is really complementary, and the two should be considered in tandem and not as discrete activities.
It is also important to remember that the speed at which a lean conversion journey is implemented often compromises the ability to do the thorough process analysis required for a Six Sigma result. However, choosing to implement a lean event in a timely manner might optimize the takt time but also increase the rate at which a nonconformance can be produced. Hence the need for a good roadmap coupled with the appropriate measures to avoid getting stuck in the quagmire.