Quality Edge
John Vandenbemden
Quality Edge | John Vandenbemden
Let’s begin with some basic facts and considerations to prepare the auditor to assess chemical management.
ISO 45001 and ISO 14001 Auditing Chemical Storage
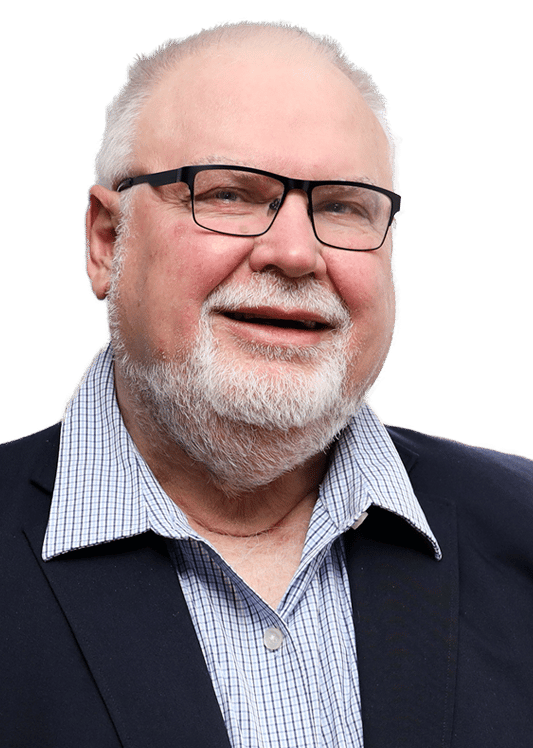
Auditing standards such as ISO 14001 and ISO 45001 often create questions for auditors concerning managing and storing chemicals under requirements of operational controls, emergency preparedness and compliance obligations. The common theme surrounding these questions is normally the auditor’s lack of knowledge of chemicals. Auditing is more than I store the chemicals in a flammable or acid cabinet. There are chemicals that should not be stored next to each other. To reduce this knowledge gap let’s begin with some basic facts and considerations to prepare the auditor to assess chemical management.
PEL is the permissible exposure limit required by OSHA regulation; it is the maximum amount of a particular substance legally allowed in the workplace air. While TLV is the threshold limit value recommended by the America Conference of Governmental Hygienists (ACGH); TLV is not legally enforceable. If no PEL or TLV is established, other exposure levels are often provided by the National Institute for Occupational Safety and Health (NIOSH), from other countries and sometimes from the manufacturers themselves. We must keep in mind that one should not judge a chemical by its PEL or TLV alone because very few chemicals have been thoroughly tested for long-term health hazards, such as reproductive effects or the potential to cause cancer.
Physical Data is important because it provides basic information about chemical properties needed to decide how to store chemicals, how to avoid or fight fires and how a chemical will react. It also indicates in what chemical state, liquid, gas or solid, you will find a product at the process temperatures and conditions used within the workplace. This is important for understanding the most likely ways the chemical can enter your body – such as breathing it in, swallowing it or absorbing it through the skin or eyes.
Caption
The standard provides a systematic approach to sampling without overtaxing resources.
This was meant to provide auditors with facts that they need to consider when assessing how chemicals are managed and stored by their clients.
Physical Property Considerations
- BOILING POINT- This is the temperature at which a liquid boils. Flammable liquids usually have a low boiling point, which can present fire hazards. The boiling point, like the vapor pressure, is a good indication of how easily the product will evaporate and give off vapors. If the product is a mixture, the boiling point may be presented as a range (such as 10-30 degrees Celsius or 80-100 degrees Fahrenheit).
- VAPOR PRESSURE - At a given temperature, a certain proportion of a liquid will evaporate and form a gas. The pressure of that gas at the surface of the liquid is called the vapor pressure. The higher the vapor pressure, the more easily a liquid will evaporate and catch fire. Liquid materials that evaporate easily are considered volatile liquids; this means that air concentrations of vapors can build up quickly, even though the substance you are working with is in a liquid form. Liquids with high vapor pressures may be particularly hazardous.
- VAPOR DENSITY - The weight of vapor or gas compared with an equal volume of air. A vapor density of less than one means that the substance will tend to rise in still air; a vapor density greater than one means it will fall. Substances with higher vapor densities will concentrate in the bottom of tanks and other enclosed areas. Therefore, if you were at the bottom of a tank, you would be more likely to breathe more of it.
Fire And Explosion Consideration
- FLASH POINT - The lowest temperature at which a liquid will give off enough vapor to be ignited with a spark. Liquids with low flash points are more dangerous than those with high flash points (above 200 degrees Fahrenheit). If a liquid has a flash point around 70 degrees Fahrenheit (room temperature) or less, all it takes to ignite a fire is a spark or even a welding arc. It is necessary to manage and store chemicals at temperatures below their flash point.
- STABILITY - Indicates how well a material in the workplace can resist changing its form when it is exposed to heat, water, and air or mixed with other chemicals. A stable material will not change easily, even under extreme conditions. An unstable material will change easily. Examples of changes are:
- Exploding under a very hot condition.
- The chemical breaking down and releasing toxic vapors or fumes. An unstable material creates a possible safety hazard unless it is stored and handled very carefully.
- INCOMPATIBILITY – There are chemicals that one should avoid contact with even if it is part of a chemical mixture. Since incompatible substances may react when mixed to form a new hazardous chemical. This may result in a fire or an explosion that can create new and different hazards.
Hazardous Considerations
- DECOMPOSITION OR BY-PRODUCTS – There are material(s) formed when a substance breaks down or decomposes under specific conditions. For example, carbon monoxide is a by-product of the chemical reaction-taking place in a gasoline engine.
- POLYMERIZATION – A chemical reaction that occurs when a material is exposed to air, water, heat or other conditions that cause the release of a large amount of heat and, in some cases, toxic gas. Most materials that are likely to react in this way are treated with inhibitors, materials that prevent this type of chemical reaction during the manufacturing process. These inhibitors in turn may be toxic. Special storage procedures must be implemented to prevent serious injury.
This article was intended to provide auditors with facts that they need to consider when assessing how chemicals are managed and stored by their clients. Since auditors are not conducting compliance audits the auditor must rely on procedures and operational controls their client has implemented. This includes operational controls put in place to ensure compliance. Thus, even though it is not a compliance audit the operational controls must be effective to meet the compliance obligations including managing and storage of chemicals. There are many clients who use chemicals within their processes but do not have a strong knowledge of the considerations highlighted in this article.