xxxxxx xx
xxxxxxxxxx
column | Francois Gau
aerospace
aerospace
Manufacturing Quality starts at the quoting stage, including quality costs. Don’t miss any critical requirements. It may be too late when you get the purchase order…
Why Should We Position Manufacturing Quality at the Center of our Businesses?
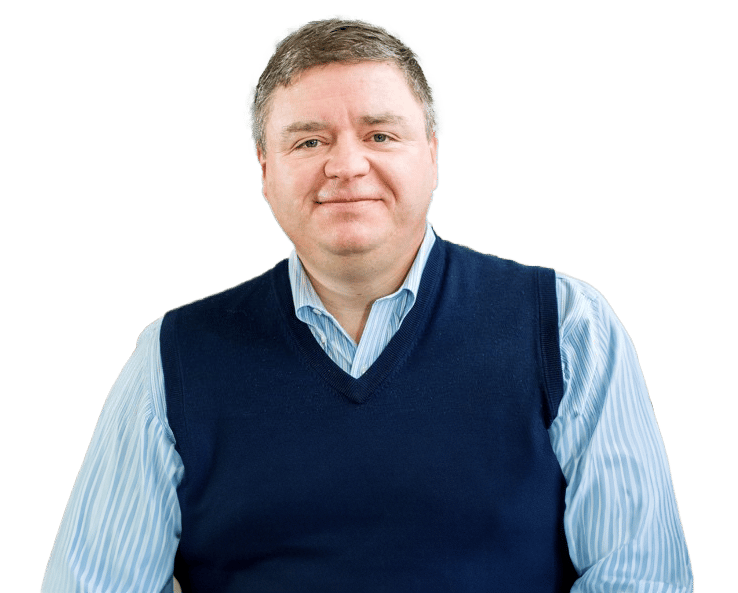
H2 Deck By Bold Name
h2 xxxxxx
H1 xxxxxx
h2 xxxxx
I have had the privilege of working with hundreds of manufacturers—ranging from small shops to large enterprises—across a variety of industries. I hold a particular affection for aerospace as I grew up in Toulouse, France (the home of Airbus), and began my career at Honeywell Aerospace in France and the U.S. Later, I joined Kennametal, where I led several market segments and expanded my expertise into the automotive, energy, and medical sectors. Today, as the CEO of GrowthHive, I help dozens of manufacturers navigate the challenges of growing their businesses.
Over the past decade, I’ve had one simple realization:
Parts and assemblies requests for quote(s) by the front office come with increasingly tighter tolerances, massive documentation submissions, and “flow-down” requirements that aren’t easy to spot on a 2D print or 3D model.
Manufacturing quality interpretation is unfortunately the norm and it is costly. Almost every one of my clients encounter challenges on parts and assemblies that require more time than planned. Many must rework the part or assembly to get back on “specs”, that were, in theory, already outlined in the original requirements. Worse, their customers rejected the parts adding delays, costs, and frustration across the supply chain. It is becoming a business challenge for some of us.
Furthermore, as reliance on 3D models grows, and with no universal standard yet for defining manufacturing quality requirements (or specifications), it is left to us, manufacturing business leaders, to anticipate what’s required to reduce interpretation and related costs, delays and frustration.
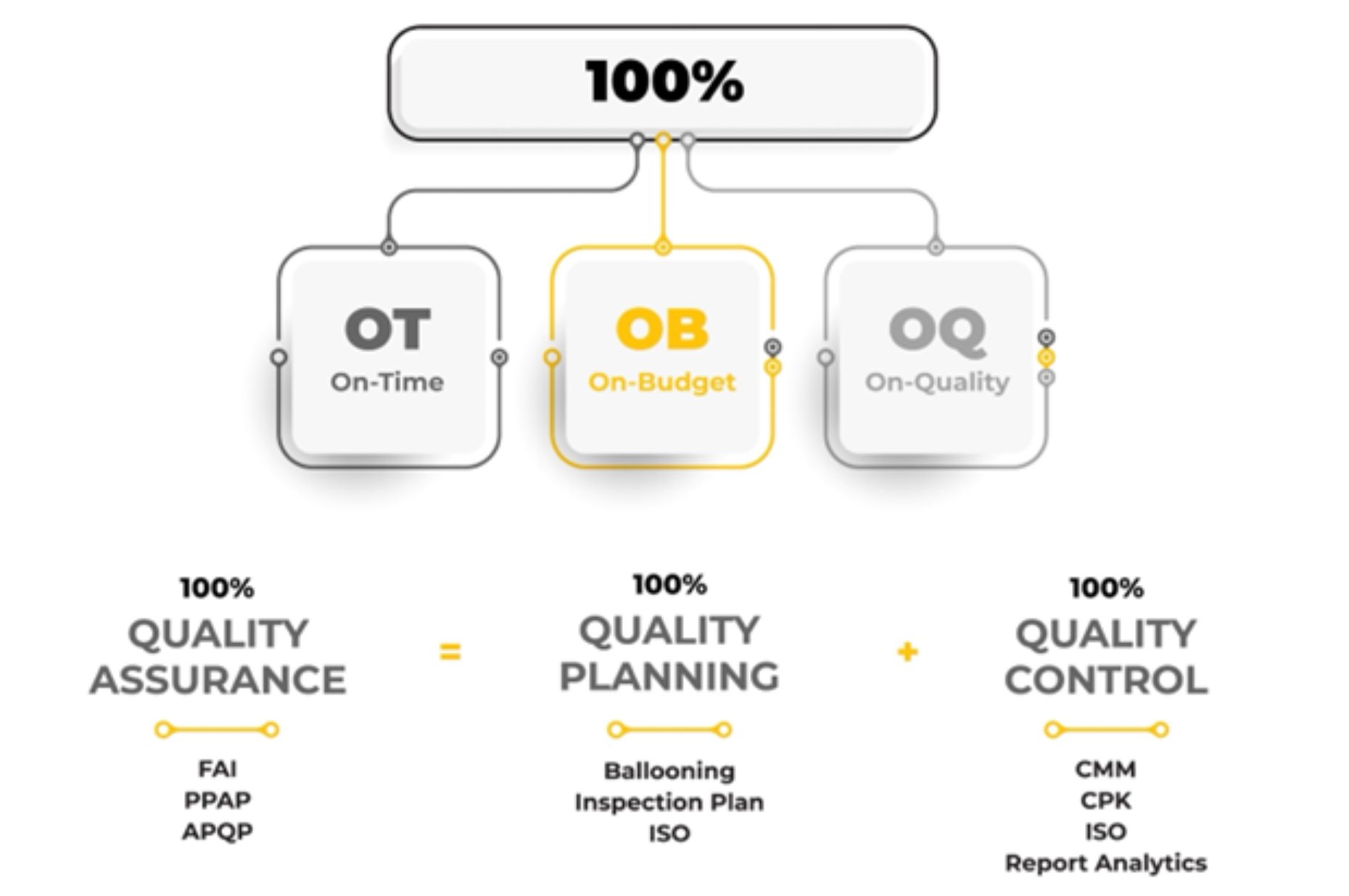
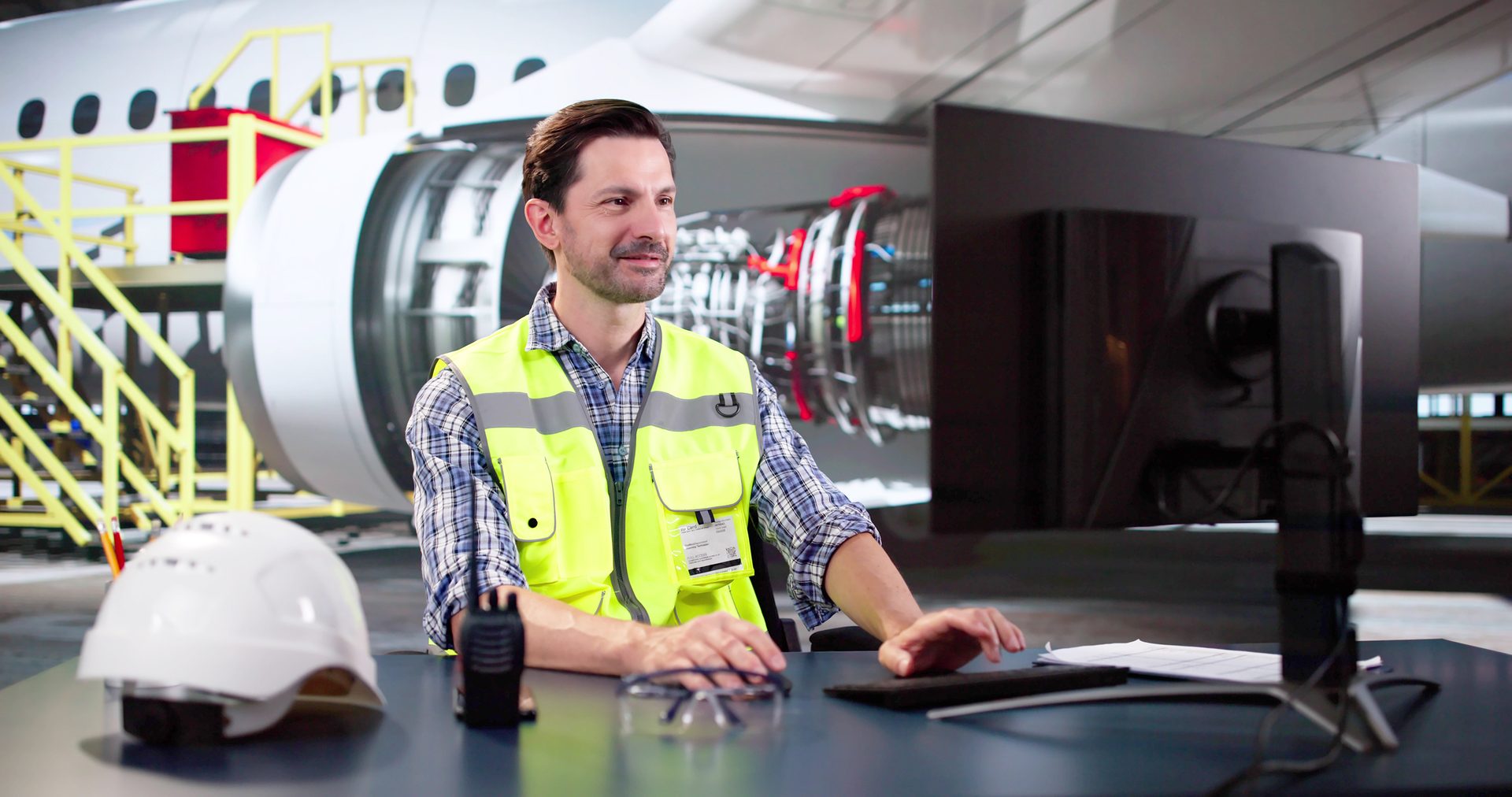
Source: AndreyPopov / iStock / Getty Images Plus via Getty Images.
Source: www.highqa.com
Of course, if you’re an OEM/buyer, you play a critical role as well— by ensuring that all the information you’re sharing with your manufacturing partners is accurate, up to date, and revisions are clearly reflected in your packages, hence reducing or removing any interpretation from the get-go.
Simple question: Are we able to calculate the real cost of manufacturing quality?
Many of the tools we need are available: “Ballooning” a part from a 2D print or 3D model continues to improve rapidly. Real-time connectivity with a wide range of measuring devices is now possible. Analyzing quality data and producing FAI and other reports from a single database is far more efficient than using paper, pencils, and spreadsheets. Even real-time sharing of quality data between suppliers and manufacturers is no longer a future vision—it is a reality.
Tools alone won’t solve the challenge. We’re facing a breakthrough, or decision point: We need to bring manufacturing quality at the center of our business processes.
To do so, let’s think of quality as two major contributors to our businesses: Manufacturing Quality Planning (QP) —which involves interpreting flow-down requirements and defining how features will be measured—and Manufacturing Quality Control (QC) —which ensures that the plan is executed correctly and that parts meet specifications.
Both are critical in different ways from a business management perspective:
- Quality Planning (QP) ensures that there’s no interpretation as to what needs to be done and how, from a quality standpoint.
- Quality Control (QC) ensures that parts are produced to specifications.
However, QP & QC together present a business dilemma: Striving for perfection in both areas will be too costly and take too long.
On-the-job experience and strong core skills are critical for accelerating the quoting process. Skilled quotation engineers can quickly spot features that will present challenges. Similarly, Quality planners (QP) excel at sifting through dense documentation to spot the fine print that could get a company into hot water later down the line.
The reality is—we need both perspectives in the room when reviewing new parts or packages. This collaboration needs to be seamless. Avoiding surprises is paramount to speeding up and streamlining the entire process. As the old saying goes, “Measure twice, cut once.” By the time the purchase order (PO) arrives, it’s often too late to address overlooked details. Conversely, if it takes a week to send a quote, customers will move on to other suppliers. Striking the right balance between speed and thoroughness is key.
Meanwhile, on the other end of the plant, a familiar refrain echoes everywhere I go: “We’re late…” Quality control (QC) teams are often the last link in the chain, picking up the process under pressure—with everything needed yesterday.
If you’re like many of us, you’ve probably experienced days, weeks, or even months of parts sitting on the shelf —ready to ship but held back by a missing report or the need for rework due to a late discovery of a critical spec.
Now imagine how much cash can be liberated from your operations if all of that had been properly planned from the start, with the right tools in place to capture, analyze, report, and share manufacturing quality data in real time.
Not only do I work with top-tier manufacturers in highly regulated industries, but I also work with numerous software companies involved in quoting, CRM, ERP, quality management, CAD/CAM and more. Currently, I have the privilege to work on exciting breakthrough solutions with the founders and team at High QA, a manufacturing quality management software company. In both worlds (manufacturers and software), I witnessed a rapid proliferation of ever-increasing standards and requirements —all for very good reasons. And this trend shows no signs of stopping.
This patchwork of requirements, software, and processes needs to be harmonized—so that all the talented people we have can play in sync, like a well-conducted symphony. Let’s find a better way forward. Together.
I’d love to hear your thoughts; feedback is always welcome.