xxxxxx xx
xxxxxxxxxx
Aerospace CT
aerospace
aerospace
Implementing X-Ray CT technology provides a pathway to increased efficiency by overcoming production bottlenecks, addressing issues related to a shortage of skilled labor, and navigating supply chain challenges. By Paul Brackman
Advancements in Industrial X-Ray Computed Tomography
The global backlog of unfilled aircraft orders is at its highest ever, with more than 17,000 jets waiting in production, according to Oliver Wyman’s Global Fleet and MRO Market Forecast 2025-2035. Based on current production rates, producing these jets will take 14 years. While this backlog can be attributed to many factors, some primary contributors include production bottlenecks, lack of skilled labor, and supply chain issues.
Advancements in industrial X-Ray computed tomography (CT) technology offer a method of modernizing and enhancing traditional quality processes to help aerospace manufacturers keep up with demand while also managing a mounting backlog. These compact and easy-to-use solutions deliver advantages over common nondestructive inspection methods, including increased speed, repeatability, efficiency, and more accurate defect detection. The complete 3D data CT technology captures can be used as a digital twin for additional advantages that are key to leveraging innovation to address the record-high industry backlog.
Reducing bottlenecks by modernizing NDE with digital X-ray
Many of the most common nondestructive evaluation (NDE) methods for quality control in aerospace components have limitations in what can be inspected in a production cycle. Many legacy NDE methods, such as eddy current and ultrasonic testing, for example, require skilled operators to take manual measurements. Film X-ray must be developed and inspected before any useful information can be gathered.
Simple automation can be achieved through robotic process substitutions; however, these techniques are still subject to innate limitations. For example, ultrasonic testing typically requires surface treatment of the component before performing inspection. Eddy current testing is only valid if the material of the component is conductive. Both techniques are limited in their abilities to inspect internal geometries. Penetrant testing is considered an affordable nondestructive method of detecting surface-breaking material defects. Its effectiveness, however, depends on surface roughness pre- and post-cleaning. It is also limited to inspecting accessible surfaces and marking defects connected to the surface, leaving the possibility of defects in blind holes and internal geometries.
Blade scan with ZEISS VoluMax 9 Titan CT scanner.

Blade scan with ZEISS VoluMax 9 Titan CT scanner.
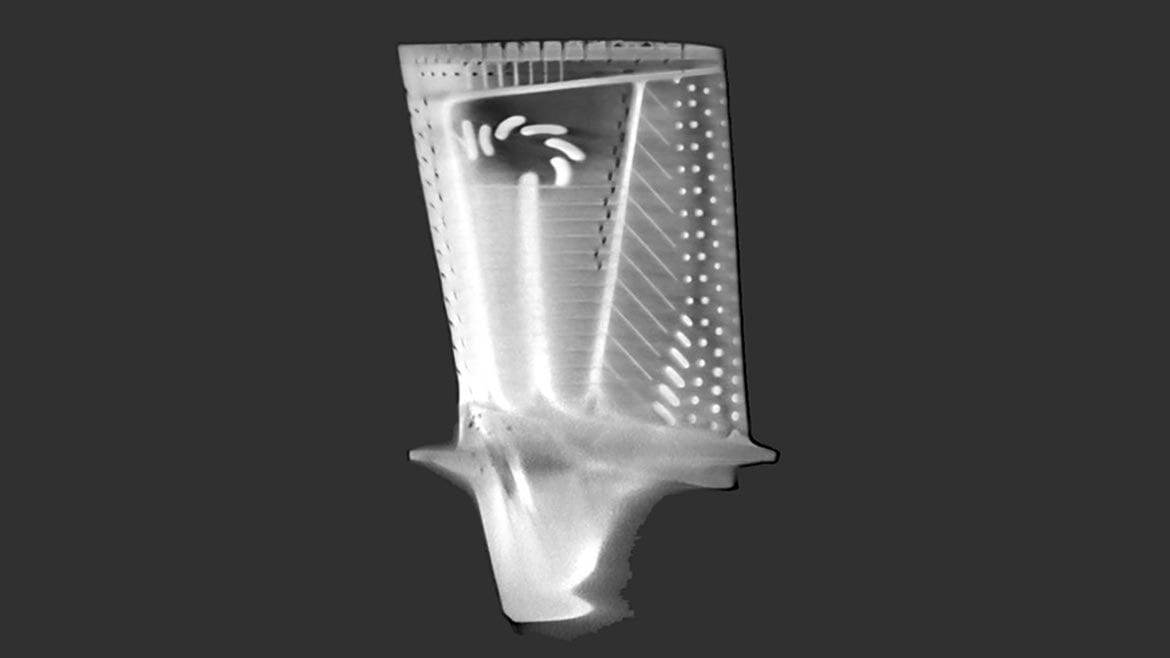
Modernizing nondestructive evaluation (NDE) with digital X-ray improves the speed and accuracy of the defect detection process for aerospace components by condensing an often multi-step process into a single scanning session. In addition, X-ray can be automated and operated easily with minimal training, and parts do not need to be conductive, nor do they require pre- or post-cleaning processes. X-ray also captures the entire part volume, revealing the size, shape, and location of defects for faster and more comprehensive defect detection.
Digital X-ray furthers these advantages with substantial improvements over industrial X-ray film systems. With its ability to produce an image immediately, digital X-ray is significantly faster, eliminating the need for film development and inspection time. Digital X-ray also supports the long-term data retention requirements common in the aerospace industry. By retaining digital files on servers, manufacturers save costs and space and eliminate the need for manually storing film in a temperature-controlled room.
Accelerating inspection with easy-to-use technology
Advancements in X-ray CT technology increase inspection speeds in ways that are not possible with other nondestructive evaluation techniques. For example, 3D CT technology enables high-volume inspection, allowing for the simultaneous scanning of batches of parts.
After scanning, advanced metrology software automatically separates the data for individual part evaluation. With a few clicks, the software analyzes internal and external structures, detecting flaws such as porosity, inclusions, and shrinkage. Identifying these issues earlier in the production process minimizes costly rework and delays. This same dataset can also be used for other processes aside from defect detection, including geometry evaluation. By eliminating the need for separate processes for different evaluations, manufacturers save time and get more mileage out of a single scanning session.
Inspection software augmented with artificial intelligence (AI) increases inspection speeds and accuracy while also helping aerospace manufacturers cope with a lack of skilled labor. The technology can detect defects automatically by learning to recognize, identify, and classify more than just conventional pores and cracks, to also detect misshapen or missing features. For some manufacturers, AI-assisted inspection has increased defect detection accuracy by up to 50%, leading to improved consistency and reducing reliance on operator skills.
Detractors of 3D X-ray CT will say that the technology is not without limits—part geometry and orientation can negatively affect scan quality. However, recent advancements in hardware and software negate or reduce these imaging artifacts. Hardware modules such as scatterControl minimize artifacts to deliver high image quality comparable to line-array detectors, in a fraction of the time. Advanced software corrections (multi-material beam hardening correction) can further improve the data, resulting in a high-quality digital twin of the scanned component. As a result of these corrections, subsequent data evaluation is much smoother and easier to perform.
A complete digital twin derived of 3D CT data supports supplier traceability and confidence, and facilitates clearer communication, reducing delays and misunderstandings.
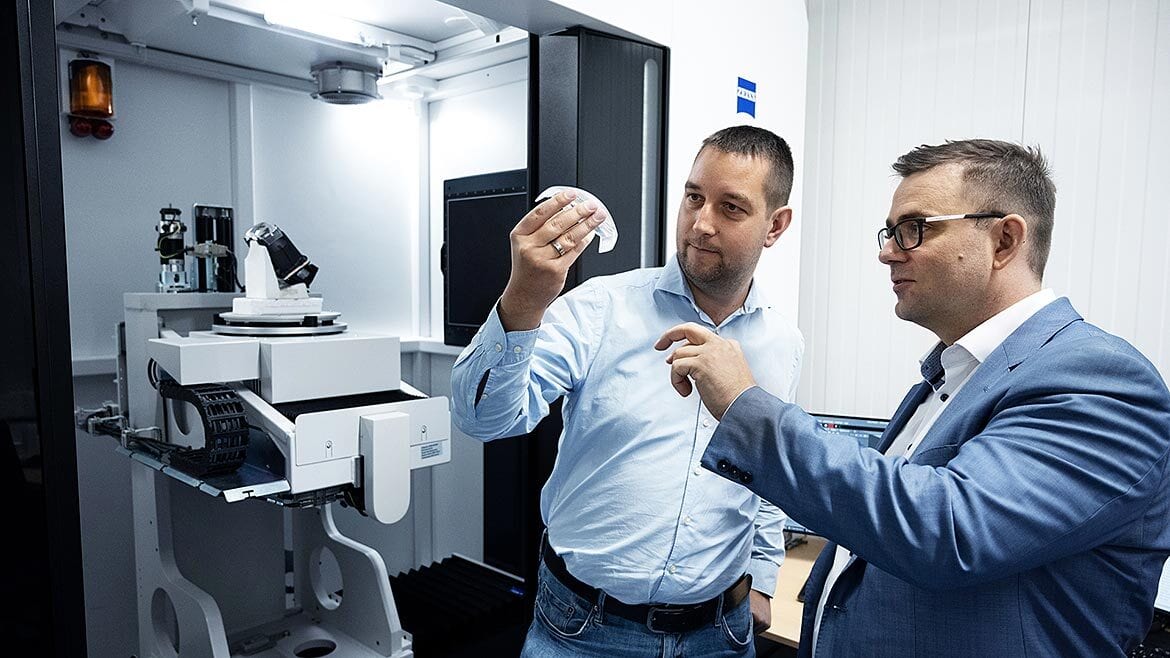
Advancements in X-ray CT technology increase inspection speeds in ways that are not possible with other non-destructive evaluation techniques.
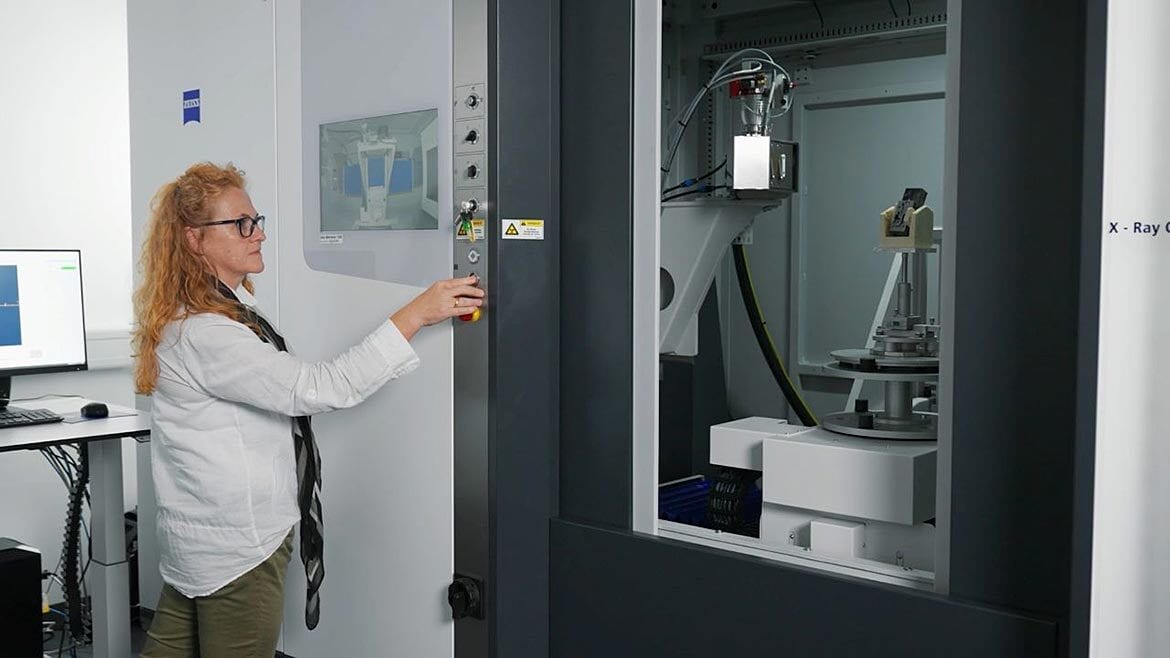
Leveraging digital twin creation for process improvement and beyond
As aerospace manufacturers grapple with supply chain challenges, some are turning to additive manufacturing (AM) to help overcome them. AM offers advantages that support faster production times, bringing down the process for designing, producing, and testing new blades from as long as three years to just a few weeks or months. However, AM also comes with disadvantages. For example, blades often crack internally during printing, a problem that can be resolved with tuning adjustments in an iterative process. X-ray CT quickly captures a digital twin of the blade that guides these iterations with reliable internal and external inspection. This data visualization enables manufacturers to implement a successful additive manufacturing process that shaves years off production time.
Aerospace manufacturers can also maximize the value of their 3D CT data by archiving the digital twin for future reference, trend analysis, and quality tracking. Archiving data also supports supplier traceability and confidence in part geometry, materials, and processes, and facilitates clearer communication, reducing delays and misunderstandings.
Time is a critical commodity in the aerospace manufacturing industry, and modernizing traditional processes can help manufacturers make the most of it. Implementing X-ray CT technology provides a pathway to increased efficiency by overcoming production bottlenecks, addressing issues related to a shortage of skilled labor, and navigating supply chain challenges. It also enhances quality control and ultimately reduces the significant backlogs that major manufacturers face. By adopting these solutions, aerospace companies can tackle current challenges and position themselves for a more agile and digitally integrated future.