Standards
Vision & Sensors
V&S
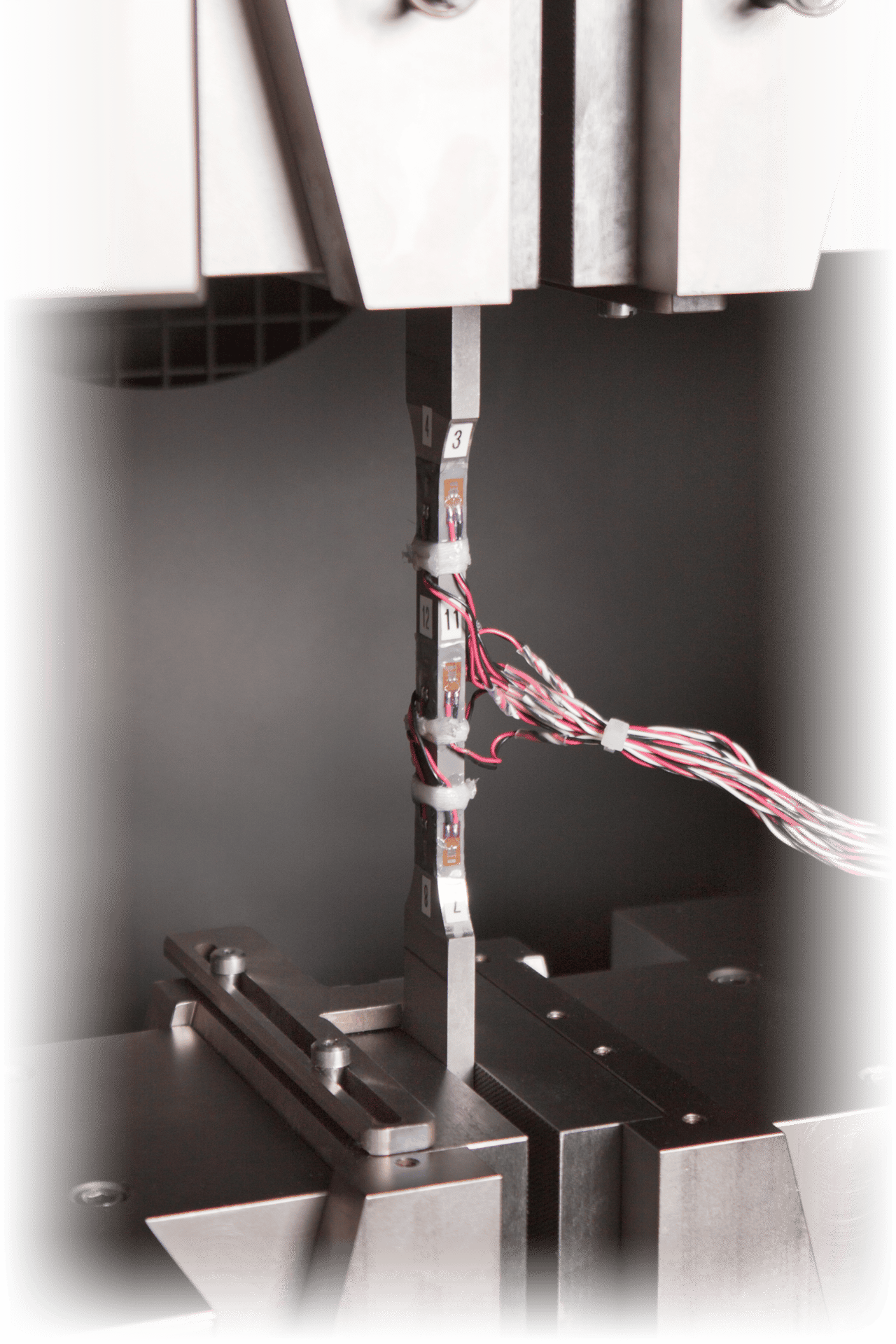
H2 Deck By Bold Name
h2 xxxxxx
H1 xxxxxx
h2 xxxxx
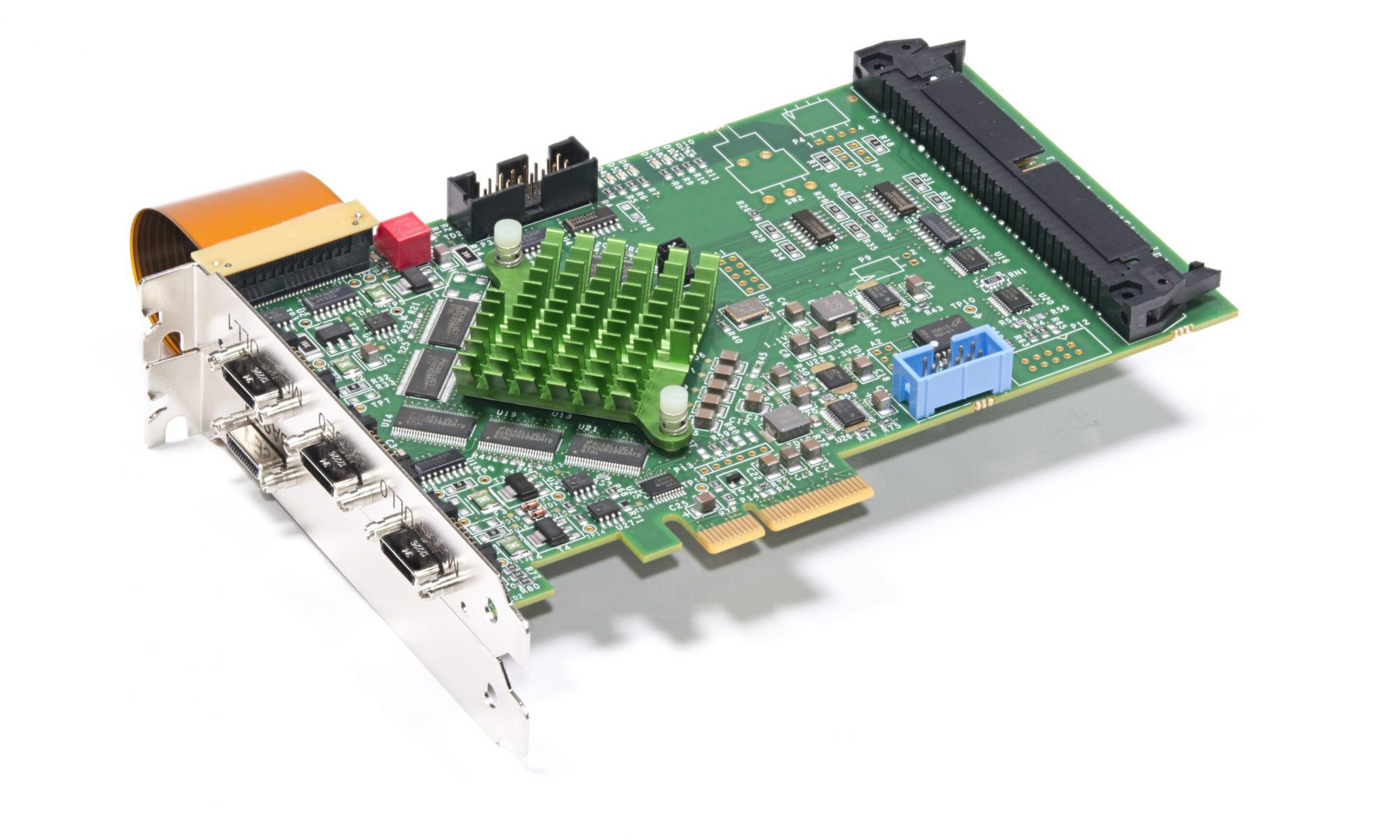
With so many interfaces available, why is Camera Link still viable? By Donal Waide
Camera Link
Proves the More Machine Vision Changes, the More it Stays the Same
Over the past decade the machine vision industry has witnessed transformative change in interface standards. For instance, CoaXPress 2.1 (CXP) — the industry’s most powerful interface — can now stream image data from camera to host PC at a previously unattainable 12.5 Gbit/sec per link with the potential of 50 Gbit/sec when a single quad-link camera is connected to a quad-link CXP frame grabber. More gains in throughput are on the horizon as camera manufacturers continue to push bandwidth limits with larger sensors, increasingly higher pixel counts, and faster frame rates.
While this progress has been welcomed by system integrators at the high end, the machine vision landscape can often consist of applications that simply don’t require the blazing speeds of CXP or 25 GigE Vision, and furthermore, can’t justify their expense. These low- to medium-performance use cases include automated inspection processes, science research, medical imaging, and others in a data rate range between 100 MB/sec to 800 MB/sec. Integrators designing these less demanding systems are staying the course with a well-established interface with a robust track record of handling large amounts of data easily and securely: Camera Link.
Published by the Automated Imaging Association (AIA) in 2000, Camera Link was the first high-speed digital camera interface standard. It works by transmitting serialized data streams based on LVDS (Low Voltage Differential Signaling). Basically, a parallel-to-serial transmitter is used at the camera while a serial-to-parallel receiver is on the frame grabber inside the PC. The current AIA Camera Link standard is version 2.1, which defines the cable, connector, and signal functionality between the camera and the frame grabber.
Over the years, Camera Link has taken modest steps forward. Camera Link 1.1, published in 2004, added the Gen<i>Cam software standard for plug-and-play interoperability. In 2007, Camera Link 1.2 integrated Power-over-Camera Link (PoCL) and mini SDR connectors. Originally there were only three variations of Camera Link: Base (255 MB/sec at the maximum chipset operating frequency of 85 MHz), Medium (510 MB/sec), and Full (680 MB/sec). Deca mode (80-bit, 10-tap) was later added boasting the power to transmit 850 MB/sec. Like Medium and Full, Deca configurations require the use of a second cable.
In 2012, the AIA launched Camera Link High Speed (CLHS), a standard based on data packet delivery rather than serial. Hypothetically CLHS can transmit 3.125 Gb/sec over copper or fiber optics. Adoption rate for CLHS has been slow, however, hampered by its lack of support for DMA (Direct Memory Access) and not being backwards compatible with older CL devices. Only a handful of manufacturers are offering CLHS products, limiting competition (pricing) and options for customers.
Why Camera Link is Still Viable
In an industry marked by rapid technological advances, the demand for Camera Link has remained constant for more than two decades. In fact, according to one leading research company, Camera Link is expected to experience continued growth globally due to an increasing need for high-quality imaging in machine vision, healthcare, and surveillance. The North American market for Camera Link products is predicted to grow ten percent annually until 2030.
With so many interfaces available, why is Camera Link still viable? There are several reasons:
- Camera Link delivers an attractive performance-to-cost ratio for low- to mid-range vision applications. As an older standard, Camera Link products are manufactured in high volume, therefore reducing the costs for off-the-shelf cameras, frame grabbers, and especially cables, due to widespread availability.
- Adding to this cost effectiveness is PoCL (Power over Camera Link) and PoCL Lite (a smaller PoCL interface). PoCL achieves savings associated with the elimination of a separate power supply and additional cable for the camera. What’s more, a single cable carrying both data and power promotes simpler system design, just as it does with Power over CoaXPress or PoE.
- Camera Link systems are highly deterministic, meaning they can transfer data in a time measured method. This is especially useful where missed frames and data lagging due to interruptions from the CPU simply cannot be ignored.
- Camera Link frame grabbers transfer image data to memory using DMA channels. In doing so, Camera Link does not burden the computer’s CPU, freeing up PC capacity for image processing.
- Camera Link offers excellent I/O flexibility and capability. Because of more demanding synchronization, most line scan cameras use this standard.
- Camera Link products are interoperable, providing users with the flexibility to choose the best camera, frame grabber and cable without worrying about compatibility between different manufacturers. There are hundreds of Camera Link products on the market today, increasing availability in the supply chain and reducing system integrator costs.
- Camera Link products use the same cable connection, so compliant cameras and frame grabbers can easily be interchanged using the same cable. This is important when upgrading an older Camera Link system with a newer camera or frame grabber.
- Camera Link cables are inexpensive because their pinouts, lengths, and construction have all been standardized. Also, the number of wires required to transmit data enables more compact cable designs that are less prone to breakage.
- Cable length — always an important system consideration — with Camera Link can reach 10 to 15 meters. By using high-quality frame grabbers and special shielded cables, distances in the field can be increased beyond those limitations. Fiber optic extender options are available for Camera Link connectivity up to 100 meters (about 328.08 ft).
Although Camera Link cannot compare to many of the newer interface standards in performance aspects, the interface does support relatively high pixel depths, fast frame rates, and large image sizes. For instance, if you deploy a base-configuration CL camera and a quality frame grabber you can expect to acquire 4MP images at 50-60 frames-per-second or faster. Use of a medium- or full-configuration camera may result in image acquisition of 1280 × 1024 images at 500 frames-per-second. A 4MP camera can hit just under 170 frames-per-second in Deca mode.
Camera Link Frame Grabbers
When smart cameras were first introduced, many in the machine vision industry assumed that the era of the frame grabber had passed. Smart cameras use USB or Ethernet to connect to the PC, therefore eliminating the need for a frame grabber. Yet even the most advanced smart cameras have proven to be only appropriate in low-end applications— the cabling alone limits the data rates for these cameras. For fast, high-quality imaging with maximum design flexibility, a frame grabber is required, especially in industrial inspection.
Unlike a smart camera system, Camera Link frame grabbers do far more than simply capture images from a video stream. Camera Link frame grabbers can:
- Pre-process and compress data before transmitting it to the host PC.
- Precisely synchronize camera triggers and strobe lighting to start image acquisition.
- Connect with proximity sensors and motion encoders.
- Control camera exposure, among other functions critical to a successful vision application.
So, what should you look for in a Camera Link frame grabber? First, make sure that the frame grabber supports the camera’s mode (base, medium, full, Deca), tap configuration and pixel depth. Also, if you are using PoCL, verify that your frame grabber and cable supports it. If not, you will need to use a power supply for the camera. These are the very basics. Depending on the application you’ll also want to consider Camera Link frame grabbers featuring:
- Scatter-Gather Direct Memory Access: This type of DMA moves image data into host memory without consuming CPU resources, leaving the CPU 100% available to process incoming images. The DMA engine will also cache scatter-gather instructions so when access is blocked, the engine can continue to run and move image data into host memory, meaning no images are lost during times of heavy memory and bus traffic.
- The DMA engine should be able to DMA into completely fragmented host memory buffers and not only into contiguous pre-boot allocated host memory, giving you greater control over the system.
- Factory support for both Linux and Windows. There are many reasons why designers chose to deploy their application on Linux over Windows: stability, transparency, and costs. Choose a frame grabber supplier that supports both.
- Support for DMA into GPU memory on both AMD and NVIDIA platforms. GPU processing is one of the best solutions to deal with today’s high-speed cameras, and this support will make the image movement side of an application simple and easy.
- A simple, easy to use and learn Software Development Kit (SDK) to get images into an application from the frame grabber. The SDK should have enough power and flexibility to help you get an application written quickly and efficiently, plus offer APIs that let you program the boards at many different levels, from low level hardware control to high level board-generic circular buffer management.
An Existing Solution for New Challenges
On the high end of the machine vision market, innovation is disrupting the industry —and quickly separating winners from losers. However, with most imaging applications today requiring between 100 to 800 MB/sec data rates, the oldest standard for digital cameras, Camera Link, remains a top choice for system integrators. Before you give into the impulse to specify the latest, fastest machine vision interface, do your homework and explore if Camera Link creates greater performance and value.