Test & INspection
As the pandemic and advances in technology impact the field, education and training remain paramount — especially for newcomers. By Genevieve Diesing
How a Shrinking Workforce Affects Testing and Inspection in
NDT
Nondestructive testing (NDT) embodies a range of test and inspection measures that quality leaders use to find defects or discrepancies without compromising part integrity.
The field continues to advance rapidly, with testing methods improving to boost accuracy and enhance efficiency and throughput. As pressure on manufacturers to get products to market increases, this pushes them to invest in quality and that drives improvements in NDT testing, experts say.
“There are numerous methods of test and inspection under the NDT umbrella, and they all depend on how the product is used, material classification, and failure modes,” says Matt Gormley, technical sales engineer, Pinnacle X-Ray Solutions.
Most companies tend to choose NDT over destructive testing to save on cut-up part cost if they can, he adds.
“NDT is quality; without it you risk product integrity, potential failures with fatigue [and] corrosion,” he explains.
Changing techniques
As technology evolves, older NDT methods are being upstaged by new tools such as automated ultrasonics and digital radiography (DRT), which utilizes digital detector arrays.
Testing and inspection techniques have become more standardized and automated, experts say.
For example, many inspections are tooled so that repeatability is always ensured, says Greg Weaver, founder and president, WeaverNDT. “This, as well as preset system settings and controls, are the trends I have been seeing,” he adds.
Digital and robotic technology has also increased significantly, especially as the workforce shrinks.
The equipment and technology available for automation is almost everywhere, says Gormley.
“Any inspection technique has evolved to in-line, at-line, robotic, fully and semi-automated capabilities,” he explains. “The theory and method of inspection has not changed much over the years. The ability to provide more accurate, repeatable, and the increased dataset to make better decisions however, has. Through transformation of using digital techniques, we are allowed to produce data that can be more valuable than ever before.”
Automated imaging and analysis is both challenging and rewarding, Gormley adds. While providing valuable data in 2D and 3D formats, inspection images can be automatically analyzed.
“This can be very effective for high volume production environments where assistance is provided in making accept/reject decisions,” he says. “The data can even be correlated and evaluated behind normal day to day operations for trends in part and/or system performance. This enables artificial intelligence platforms, and predicative failures of product upstream manufacturing.”
Robotics require properly developed work instructions, however. Quality teams especially need adequate training from equipment manufacturers and the proper time to learn. With the right education, automation can go far, experts say.
Shared accountability
Testing and inspection efforts go hand-in-hand with quality, and quality managers and NDT leaders share the responsibility for reliable process controls, says Toni Bailey, owner, TB3, NDT Consulting.
“The QA managers and NDT management should be one group with the same goals,” Bailey explains. “Engineers and production managers are heavily involved in quality and forcing [quality assurance teams] to cut corners to meet numbers and demand.”
Due to the collaborative nature of the work, “We need more people, better attitudes, better training and more accountability for actions and decisions,” Bailey says. “Management flows that burden QA and NDT causes them to lose those key people.”
The pandemic has only worsened this dynamic, Bailey says.
“We are losing key people due to added stress,” she says. “All industries are suffering in the same way, but the impact is critical in the NDT field.”
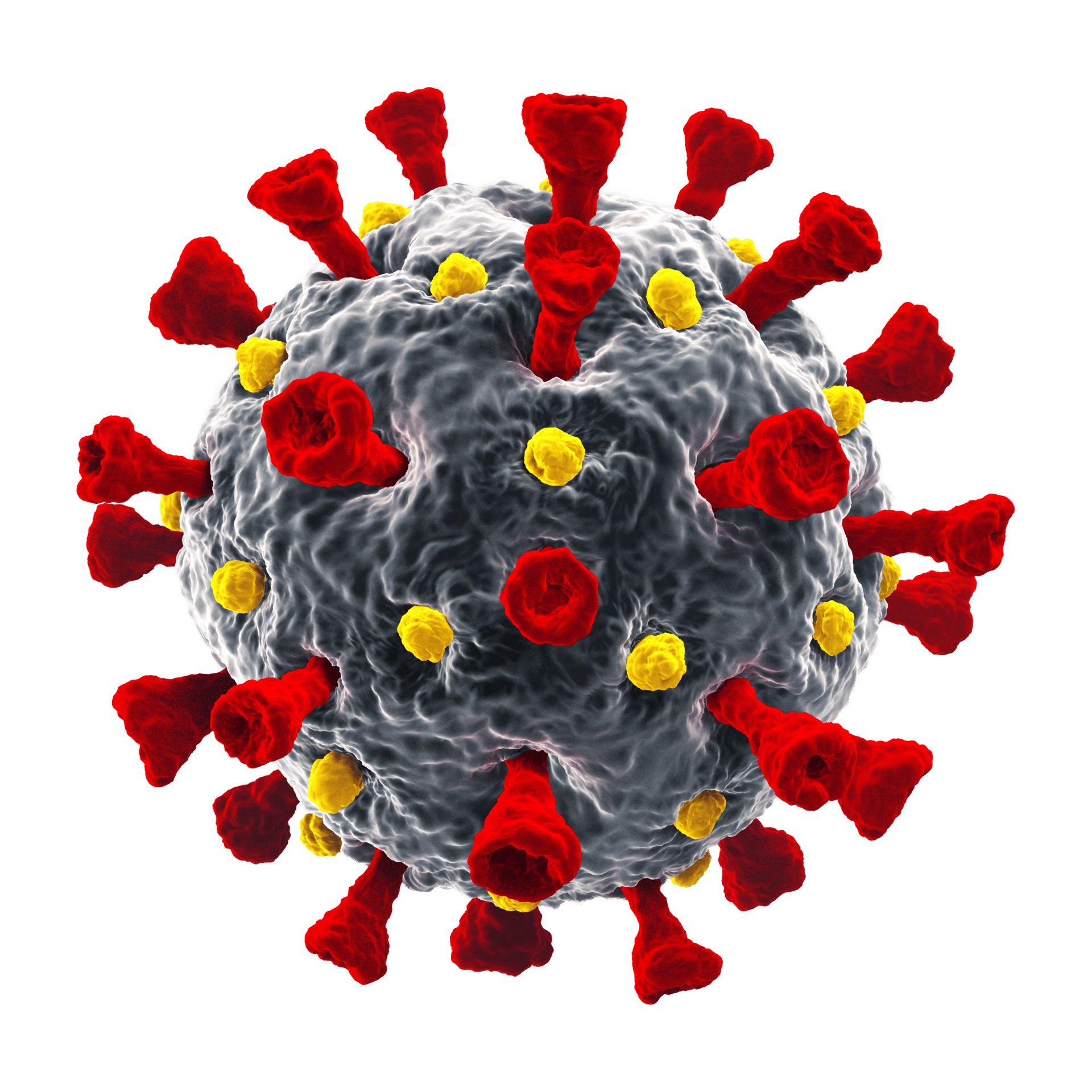
Inspections are required, and clients continued to test their critical components through the pandemic.
COVID’s impact
The pandemic caused a major reduction in human travel, which led to reduced needs for operating airlines, and vehicles, Gormley says.
“Manufacturing took an immediate drop in the number of employees it needed to keep up with the low demand, and thus were challenged with layoffs to offset the decreased demand,” he says. “Test and inspection in these industries are required, and thus the need for both internal and external laboratory services suffered.”
Weaver says that his customers were not greatly affected, although the volume of work shifted dramatically. Still, inspections are required, he says, and his clients continued to test their critical components through the pandemic.
Changing workforce patterns
While COVID dampened demand early on, the skills gap and labor shortage that has plagued the industry for more than a decade is still in full swing.
As new NDT methods advance, quality professionals require new training, and technicians transitioning from film techniques to non-film techniques need hands-on experience.
And as quality assurance managers rapidly leave the field, a management and NDT knowledge gap widens.
Older inspectors are forced to adapt to new computer technologies, and younger inspectors, who may be great with software, lack basic NDT education and quality standards.
“The largest trend I see in NDT is the loss of the retiring trained professionals,” Weaver says. “There is not a large enough funnel of talent coming up to replace them and this may become a big issue for the industry in the coming years.”
Because the pool of qualified and certified NDT technicians is small, companies struggle to balance the demands of production managers and engineers while training staff and meeting production quotas.
Since COVID hit the manufacturing industry hard, Bailey is noticing a production boom “to get back to pre-COVID production numbers,” she says.
However, not all manufacturers are investing in the labor needed to manage this growth responsibly, she says. This is especially key when it comes to quality.
Quality control departments need more training and accountability, she says.