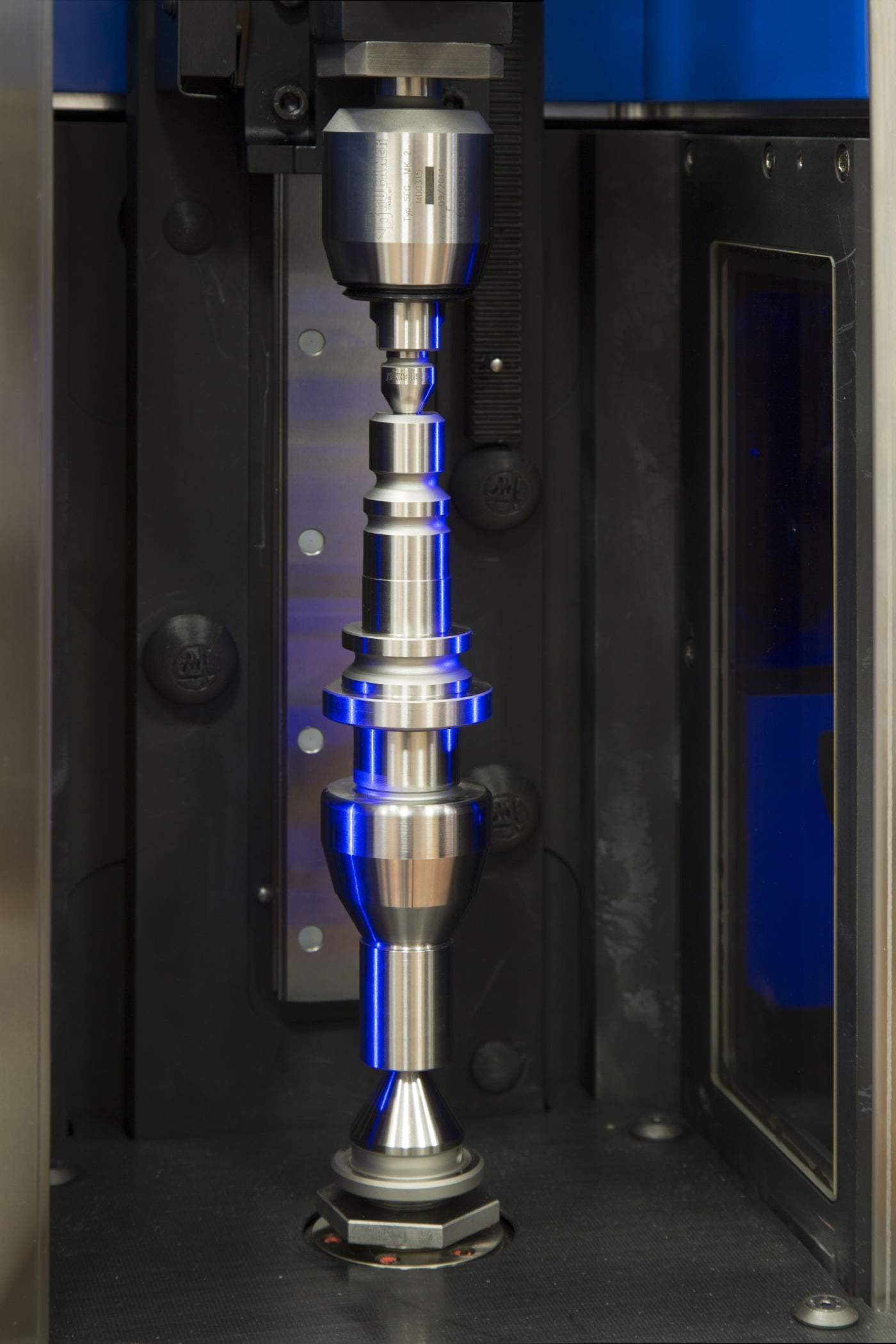
Recently, an automotive parts manufacturer was searching for a system to measure over 4,000 individually machined components a day. The company wanted a measurement system that would integrate into an automatic production line to measure shaft-shaped, largely axially symmetrical workpieces. To accomplish this, it evaluated various methods and inspection systems for the process, including the following:
The key component missing from the above methods was the ability to provide 100% inspection at high throughput, which is not sustainable for many measuring systems. The solution was found in a Marposs’ 2D optical architecture system, which offers speed, accuracy and flexibility.
Optical 2D systems are based upon state-of-the-art area image sensors and can perform many micrometric-precision checks on parts with an unprecedented speed. These systems use multiple image sensors integrated in fixed positions across the product structure to cover the entire measurement range so that neither the image sensors nor the part being measured must travel along the Z-axis. This means that images acquired by different sensors are perfectly combined together, resulting in one single image of the part with zero discontinuities or gaps at the stitching edges. The measurements are defined, configured and displayed on the graphic user interface shown on the touchscreen monitor built into the 2D optical system.
These 2D optical systems are capable of measuring parts up to 300 mm (11.8”) in length and 60 mm (2.36”) in diameter without any vertical movement of the sensors or the part itself. (1,200 mm and 200 mm diameter with some vertical movement). They utilize noncontact optical scanning to provide rapid and accurate measurements. These may be taken in static mode or dynamic mode using part rotation. Industrial grade optical sensors and the digital signal processing technology make accurate and reliable measurements. Measurements that are challenging on other measurement systems such as eccentric parts, pin bearings on crankshafts or measurements at structural junctions may also be taken reliably.
The basis of 2D optical technology is projecting the shadow of the edges of the part to be measured over a linear array of photodiodes (CCD) by means of a collimated beam of light. The dark-light and light-dark transitions are localized on the CCD sensor having subpixel resolution and correlate to the dimensional value of the shadowed area.
The transmitter produces visible blue light (light (λ=460nm), which is generated by an LED. This gives the emitter strength, reduced dimensions, long life (20,000 hours), absence of thermal drift and regulated power emission through feedback from the power supply. The light rays are expanded—then collimated—by a stationary lens and sent to the part to be measured. The transmitted light is gathered by the receiver, spatially filtered and projected onto the CCD sensor. A one-dimensional image on the CCD sensor is the reverse and, therefore, a negative of the scene viewed by the emitter.
The CCD is electronically read and the signal processed using special algorithms, allowing localization of the dark-light transitions on the CCD to be determined and correlated with the dimensional value of the shaded areas corresponding to the profile of the part being measured. To maintain this level of accuracy, it is essential that the part be adequately cleaned before being loaded on the bench.
In order to cover a larger measurement field than possible with a single sensor, various CCD probes can be arranged so that there is a slight overlap between each other. To reset the sensors, so that the reading has no discontinuity when passing from one sensor to the next, the gauge is fitted with a resident master on one of the centers. The reset cycle must be performed regularly.
When inspecting flat faces perpendicular to the rotation axis, the light beam cannot be used. A mechanical touch probe, fitted on a carriage with a radial movement in relation to the part, is used so that every radial section required can be touched. Its position in the axial direction is measured by the optical system, assessing the dimension of a conical section of the probe.
The measurement cycle can be performed in two ways:
The profiles of parts measured dynamically can be filtered to remove any components due to vibrations or components due to roughness that are irrelevant.
The measuring cycle consists of the following phases:
Optical 2D systems are designed to allow for rapid integration of the measurement data for statistical process control (SPC). This allows extremely efficient monitoring of the manufacturing process and allows rapid intervention when necessary. This ensures that workpieces maintain a consistently high quality. The measuring systems are simple to operate, allow non-operator-dependent measurement results, and deliver easy to understand measurement results with analysis functions where required.
Optical 2D systems are used in the automotive market to inspect turbochargers, engine valves, pistons, crank, drive and gear shafts. Both the aerospace and automotive sectors commonly use optical inspection for ball screws and shafts. Medical device manufacturers also use 2D optical systems to inspect implants, bone screws and rotating instruments.
In the aforementioned example, our Tier automotive manufacturer was using a robot loaded work cell designed and built to keep up with the 4,000 pieces per day. But, optical 2D systems are equally at home performing audit inspections with manual operations being handled by a trained technician. When measuring cylindrical components, 2D optical systems offer flexibility, speed and ease of use to be used in a variety of applications, whether a production environment or in a lab.