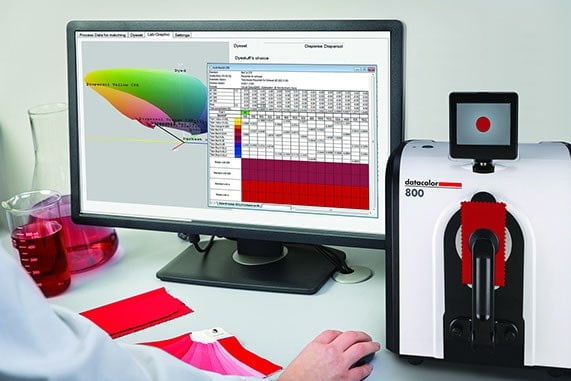
Color is just one of the many aspects of an effective quality control program that needs to be strategically managed to ensure accurate and consistent end products. However, color can be surprisingly challenging to get right.
Without an integrated digital color management workflow, manufacturers risk delivering products with mismatched components, colors that flare under different lighting sources, and other color mishaps that dramatically impact consumer perception of product quality. Thankfully, with the right tools and processes in place, today’s manufacturers can assure customers that their products will be color accurate each and every time—without added costs, production delays or wasted resources.
Visual color evaluation can seem straightforward enough. You simply compare an end product to the color standard to gage whether the two match. However, the problem with this approach comes down to subjectivity.
People will both see and describe colors differently, even when variable conditions such as lighting have been made uniform. In fact, everything from an individual’s age, medications and mood can impact their color perception, and that is in addition to external environmental factors like lighting, background, altitude and noise. Furthermore, color perception is impacted by the physical characteristics of a product, such as its gloss level, opacity and texture.
That is why modern manufacturers rely on color management solutions to accurately measure, display and analyze color—thus bringing objectivity into the process, in addition to measurement and analysis far beyond the limitations of the human eye.
Digital color management typically encompasses a hardware and software component that work in unison to ensure uniform and accurate color. One of the most important considerations is your color measurement instrument or spectrophotometer. Spectrophotometers measure light reflected or transmitted across the visible spectrum and compare it to reference samples. They provide spectral data that can be used to calculate tristimulus values for various conditions and calculate color recipes for commercial color matching.
Your color measurement hardware is supported by color management and quality control software. This allows for the communication of digital color standards between brands and manufacturers at the onset of the manufacturing process, which can save significantly on development and shipment of physical samples, can help identify potential color challenges well in advance, and can help manufacturers eliminate samples that do not meet specified tolerances before they are presented to customers.
There are countless variables to consider when implementing a new digital color management system or upgrading or expanding an existing color control workflow. Here are a few of the key considerations:
For those looking to perform quality control checks directly on the production line, portable versions of spectrophotometers can be invaluable tools for on-the-go color measurements. Plus, today’s portable color measurement options are more compact and accurate than ever before. Using these tools, manufacturers can realistically measure every lot produced and communicate that measurement data back to the customer, thus allowing automatic rejection of lots that do not meet required production tolerances.
Another essential consideration is the makeup of your end product. For those manufacturing multi-colored, textured, small-sized or irregular-shaped materials, advanced hyperspectral imaging spectrophotometers are necessary to enable digital color measurement. Traditional spectrophotometers do not have the flexibility to tackle products with color variation that are very small, such as small buttons, hair samples, yarn dyes, small gems, granulates, pellets and watch parts.
And for those who manufacture goods that vary in temperature from the production line to the end product, it is also important to consider whether and how one’s color measurement technology can compensate for these hot-to-cold variations. Changes in product temperature correlate with color changes, which can impact colorimetric data and lead to quality management headaches. Accounting for these variations is important for accuracy and consistency.
It is critical to look for a “close-tolerance” spectrophotometer—a designation reserved for precision instruments that are manufactured to the highest quality standards and that have the best inter-instrument agreement (IIA). High IIA is vital for those with multiple manufacturing sites, or who need to communicate color data across a supply chain, because it ensures compatible color results no matter which instrument is used or where those instruments are located.
IIA is also increasingly important in today’s work environment where significantly more individuals are working from home than ever before. Not only does this require the flexibility to bring compact spectrophotometer solutions away from the manufacturing site and into one’s home, but it also demands that these solutions produce compatible results with other spectrophotometers used on the production line.
Ultimately, the right color-management solution should be intuitive to use and tailored to your specific quality control requirements. A color management solutions provider can work with you to analyze your workflow, production and communication needs, and other industry nuances in order to make strategic recommendations that ensure every aspect of your color control program is optimized for your needs, while also being cost-efficient and effective.
No matter the equipment on hand, the only way to ensure consistent, reproducible and accurate color measurements is by establishing a repeatable color measurement technique and maintenance schedule.
Color measurement technique often starts with proper sample preparation, which varies by product and requires that every possible variable in the measurement process be controlled—from temperature and lighting to humidity and cleanliness. For example, samples with inconsistent colors or surface effects should be measured multiple times, while rotating and repositioning the sample between readings, and the resulting data averaged in order to compensate for measurement variability. On the other hand, samples that are not opaque often need to be folded, wound or stacked to ensure measurements are not impacted by the background color.
Color measurement technology should also be maintained according to the manufacturer’s maintenance and testing schedule, which includes daily calibration according to manufacturer recommendation and the specific needs of the quality program, with adjustments for any variables within the testing environment. Diagnostic tools can also be used to perform semi-monthly checks of instrument performance in both single- and multi-unit deployments.
When it comes to color, accuracy and consistency are imperative, as they are associated with a product’s quality. Manufacturers need to deliver products with the right color each and every time to ensure customer satisfaction. Thankfully, with the right color management partner, technology and process in place, getting color right does not need to be challenging.