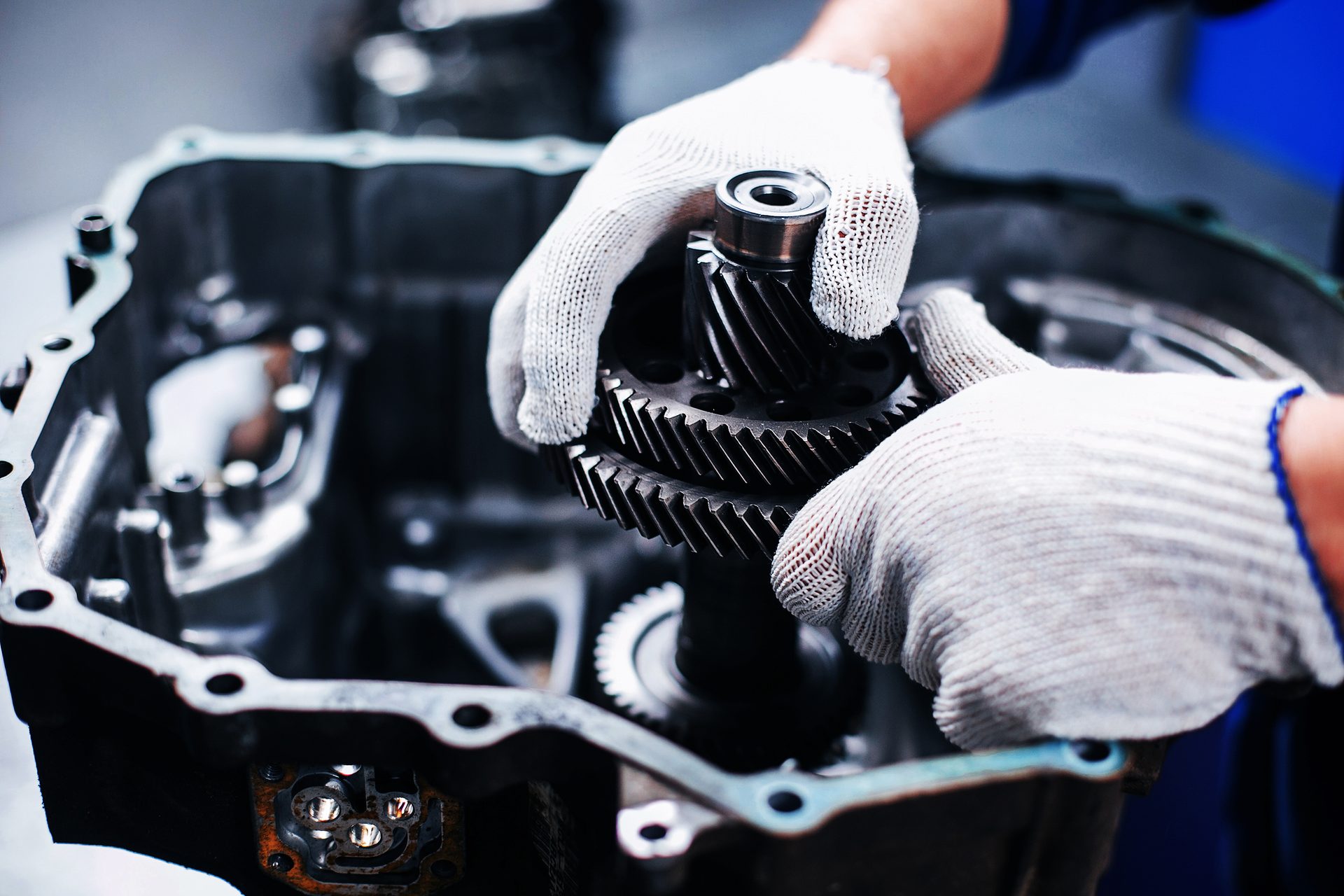
H2 Deck By Bold Name
h2 xxxxxx
H1 xxxxxx
h2 xxxxx
Management
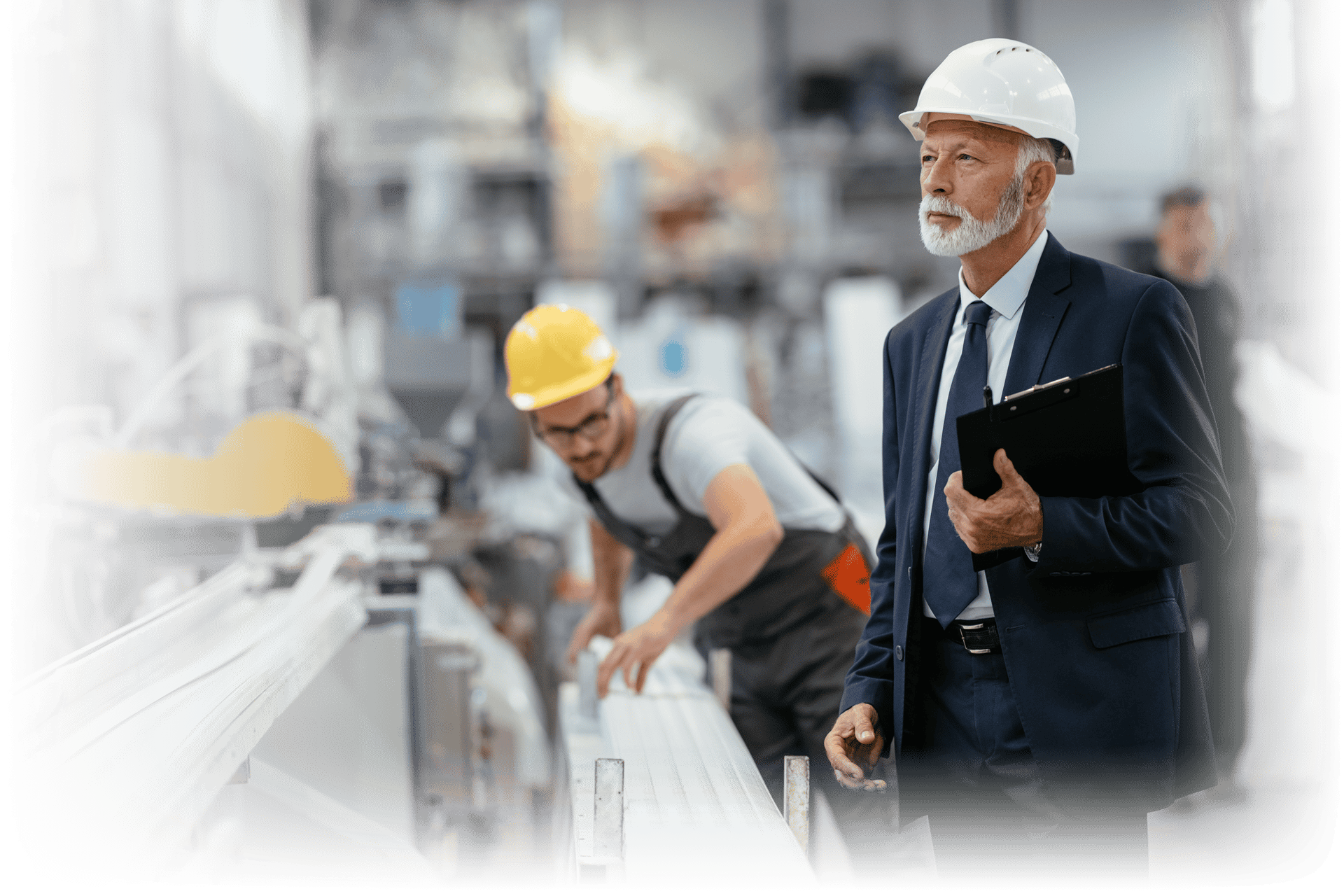
The results of Quality’s 2025 Leadership Survey. By Michelle Bangert
Leadership 2025
Leadership
2025
Management
H2 Deck Info By Paragraph Style Bold
Headline
It’s time to talk Leadership. Something good is going on in Pennsylvania. And Maryland too. These states had several companies represented in our Leadership top five. Many of the companies had a long history, going back more than a hundred years, and some well before that. One company was founded in 1797. Read on to learn more about these pillars of success, both in terms of longevity and quality.
1. Garlock Leads the Way
Manufacturing success at Garlock Sealing Technologies.
Garlock Sealing Technologies, Palmyra, NY | www.garlock.com
Garlock Sealing Technologies has been around for more than 130 years. Today the company uses lean techniques such as kaizen and 5S, as well as Six Sigma, to reach their continuous improvement goals. They manufacture sealing solutions with an emphasis on safety, longevity and productivity.
“At Garlock, we pride ourselves on developing solutions, not just products,” according to the company website. “Throughout our 130-year history, this approach to product innovation has led to numerous game-changing technologies that deliver unprecedented value, longevity, and reliability for our customers.”
In addition to focusing on customers, the company also prioritizes the environment. “Garlock is also focused on the creation of a more environmentally sustainable workplace,” according to the website. “Since 2005, Garlock has invested over $35 million in these initiatives, including replacing inefficient wastewater treatment plants, restoring valuable wetlands on campus, and constructing new, energy-efficient manufacturing facilities.”
1
2. Centuries of Progress
Metal powder innovation since John Adams was in office.
Höganäs, Hollsopple, PA | www.hoganas.com
Not many companies doing business today have been around since 1797. Höganäs has. Today the metal powder company has about 2,300 employees and offers more than 3,500 products, mostly customer specific, from 15 production centers around the world, according to the company website.
In October last year, the company celebrated twenty-five years in North America. “It was a true pleasure to celebrate our 25-year anniversary in North America with our employees, customers, suppliers, group management and other important partners,” said Dean Howard, market president, North America on the company’s website. “Our team has built a great foundation over these years through hard work, dedication and perseverance. Everyone should be very proud of their contribution in reaching this important milestone. I look forward to continuing the journey!”
This location in Pennsylvania hosts the regional headquarters, management, sales, Tech Centre and administration, along with an atomizing plant, manufacturing low alloys. All four U.S. sites employ around 350 people.
The company prioritizes sustainability and innovation. According to the company, “Höganäs makes a difference through our metal powder solutions and know-how. We believe that metal powders can and should be used in industry to a much larger extend than today and that they can contribute to sustainable growth. That is why our vision is “driving positive change through material innovation”.”
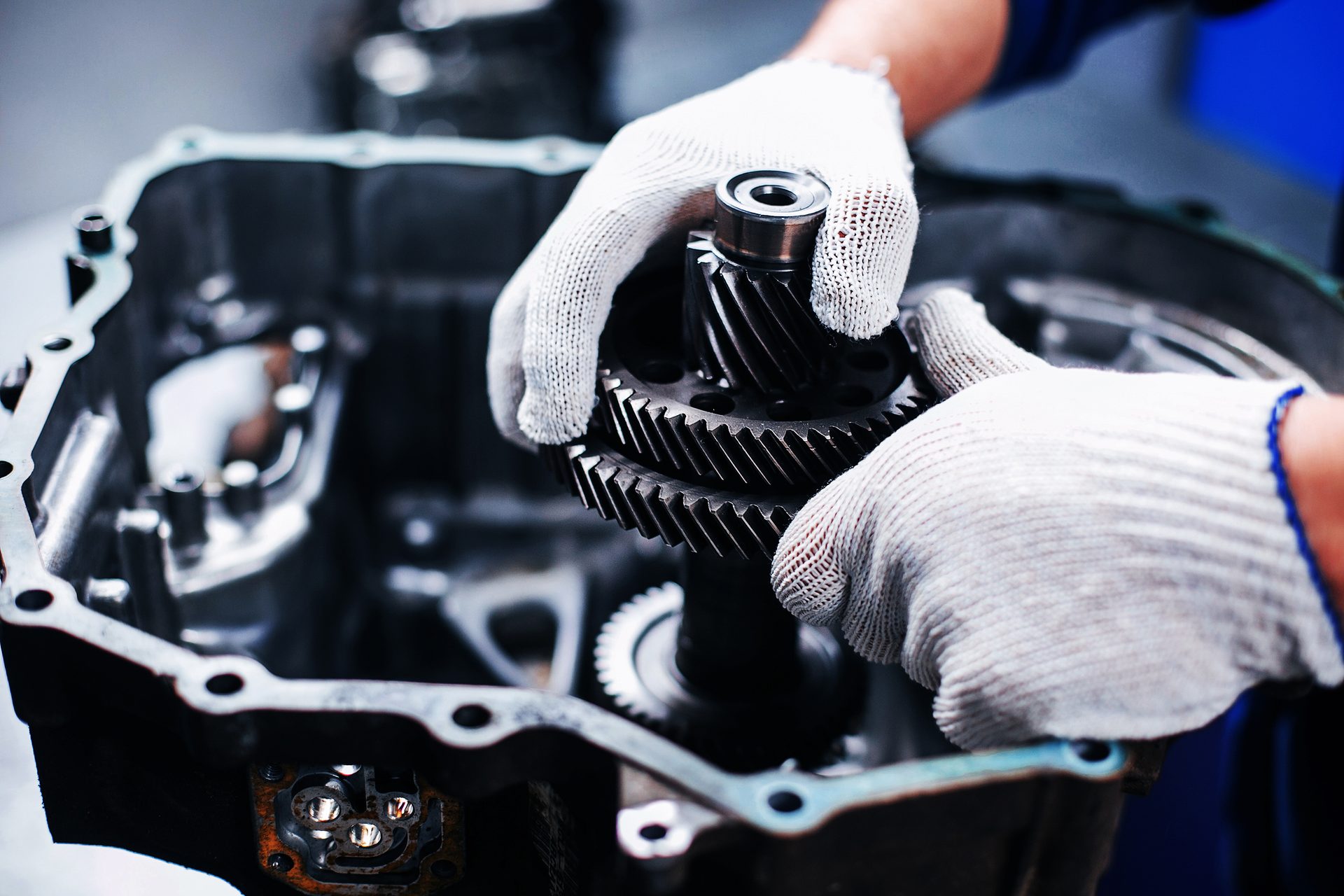
2
Source: Hoganas
3. Success at Smiths
If you’re looking to see what top companies in quality are doing, read on.
Smiths Detection, Edgewood, MD | www.smithsdetection.com
Smiths Detection may not be a household name but you have likely used one of their products. Next time you go through airport security, look at the X-ray screening machine.
The company’s main product is X-ray screening machines, both in the TSA lines as well as the lower level of the airports, used in countries around the world.
The company maintains its high quality through programs such as Six Sigma. “From there it’s the culture we have and our basic values of integrity, respect, ownership, customer focus and passion,” says Clint Lancaster, senior manufacturing engineer, Smiths Detection.
The company handles a lot of government contracts, with all the regulations that involves, as well as adhering to ISO standards. This makes for a challenging environment but a successful one.
“We’re aligned from the top to the bottom, everybody’s on board with communications and so forth,” he says. “The Smiths Excellence System drives what we do, and it’s how we can get such massive programs out globally.”
They recently launched an internal communication platform called Buzz, similar to X or Facebook for employees, so people in the United States can communicate with colleagues in the UK, India or Malaysia. The company’s parent company is Smiths Group in the UK.
For other plants looking to improve quality, Lancaster says communication is key. “A lot of our success is that we’re able to communicate across divisions, across departments, similar to what the automotive industry uses,” says Lancaster, who used to work in the automotive field. Smiths Detection uses a form of APQP that they call PLP for product lifecycle program. “We design and innovate our product ourselves, from cradle to grave.” It starts from the inception of an idea until the company’s “gate 6” where they decide whether to continue a product or if it has ended its useful life.
The next goal is moving more towards Industry 4.0 and harnessing more data. Lancaster, a retired Marine, says he wanted to give back to the military by getting involved with this type of company.
“It’s exciting work.”
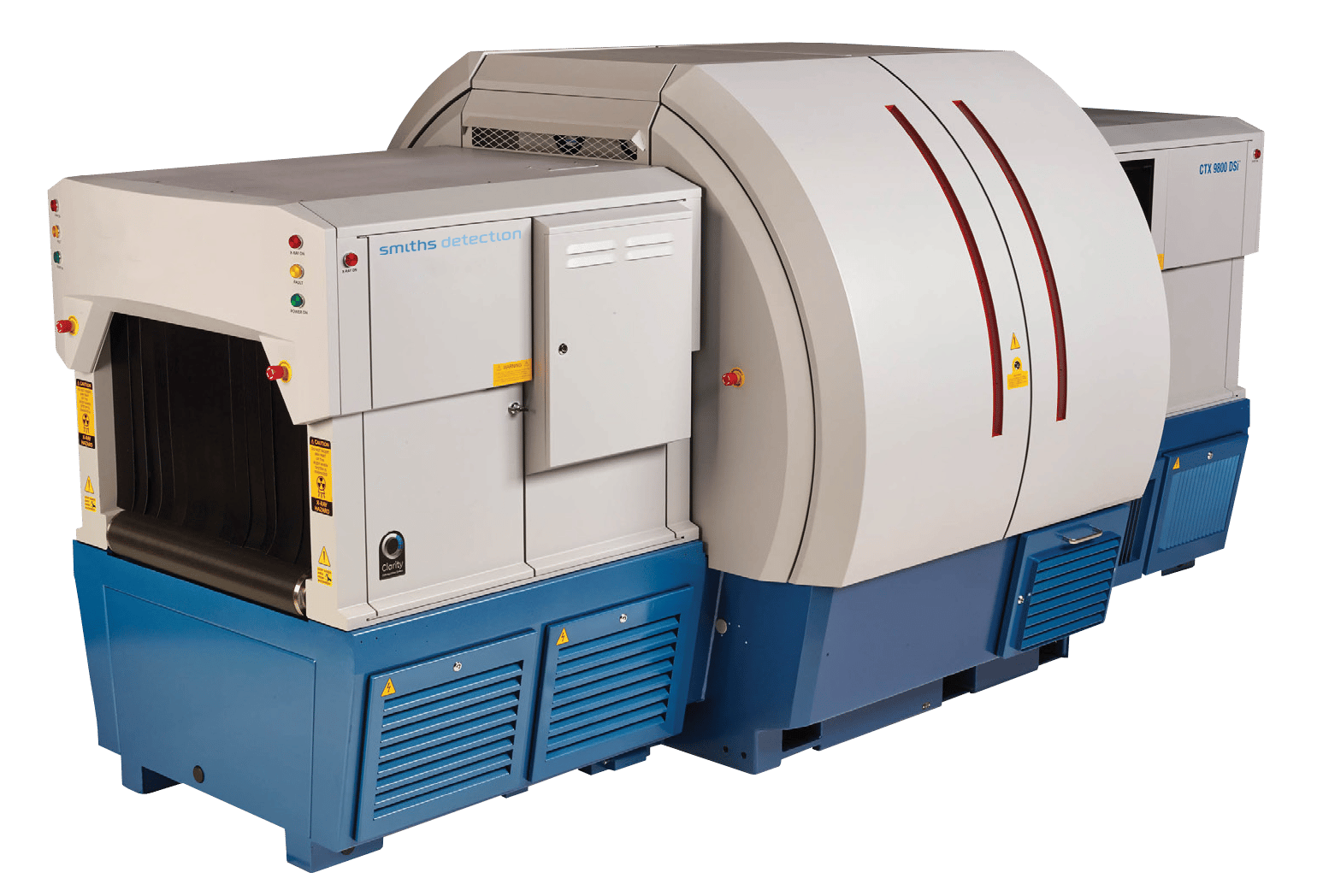
3
Source: Smiths
4. Littlestown Leads the Way
If you’re looking to see what some top companies in quality are doing, read on.
Littlestown Foundry, Littlestown, PA | www.littlestownfoundry.com
Littlestown Foundry is not afraid of innovation.
Luther D. and Emory H. Snyder started the Littlestown Hardware and Foundry Company Inc. in 1916. Today, the company is even making parts for the solar industry.
“Obviously to be in business for 108 years you have to have done some things right,” says Steven Kress, V.P. & General Manager, Littlestown Foundry. “Quality really separates us. The quality of our castings is at the highest level.”
The quality inspection department might be one person, but 97 people are inspecting a part along the way. Employees have been trained to look at a part before they start working on it, which means there are a lot more eyes on a part. Each employee is empowered to fail a casting or to point out a defect.
For companies who are looking to improve quality, Kress says ISO is a big factor.
“ISO has been a major part of our success. We’ve been ISO certified for almost 20 years now. That is the thing that has separated us from everybody else. It drives us and makes us responsible for the parts we make. We don’t just work on ISO at the end of year to pass an audit. It’s something we do every single day, it’s integrated into everything we do.”
In addition to their traditional castings, the company has been manufacturing new parts for solar field applications. “It has been an interesting transition for us, but a successful transition,” he says. “Green energy is a real thing and we’re trying to be part of that growth.”
The company is not afraid to learn from other companies—if you’re arrogant about what you know, you’ll be left behind, Kress says—and they also are happy to host other foundries to share their expertise. “We’re not hiding anything, we let people come in and tour all the time.”
They treat employees well, with benefits such as 401(k) matching, pensions, and good health insurance. The employee average at the company is 10 years, though the president and V.P. of Operations have been with the company far longer: 50 years for the president, 40 for the V.P. of Operations.
Kress worked for the company in college. He left and later ran his own business for 27 years. Ten years ago the company approached him to see if he would come back. He’s been back since.
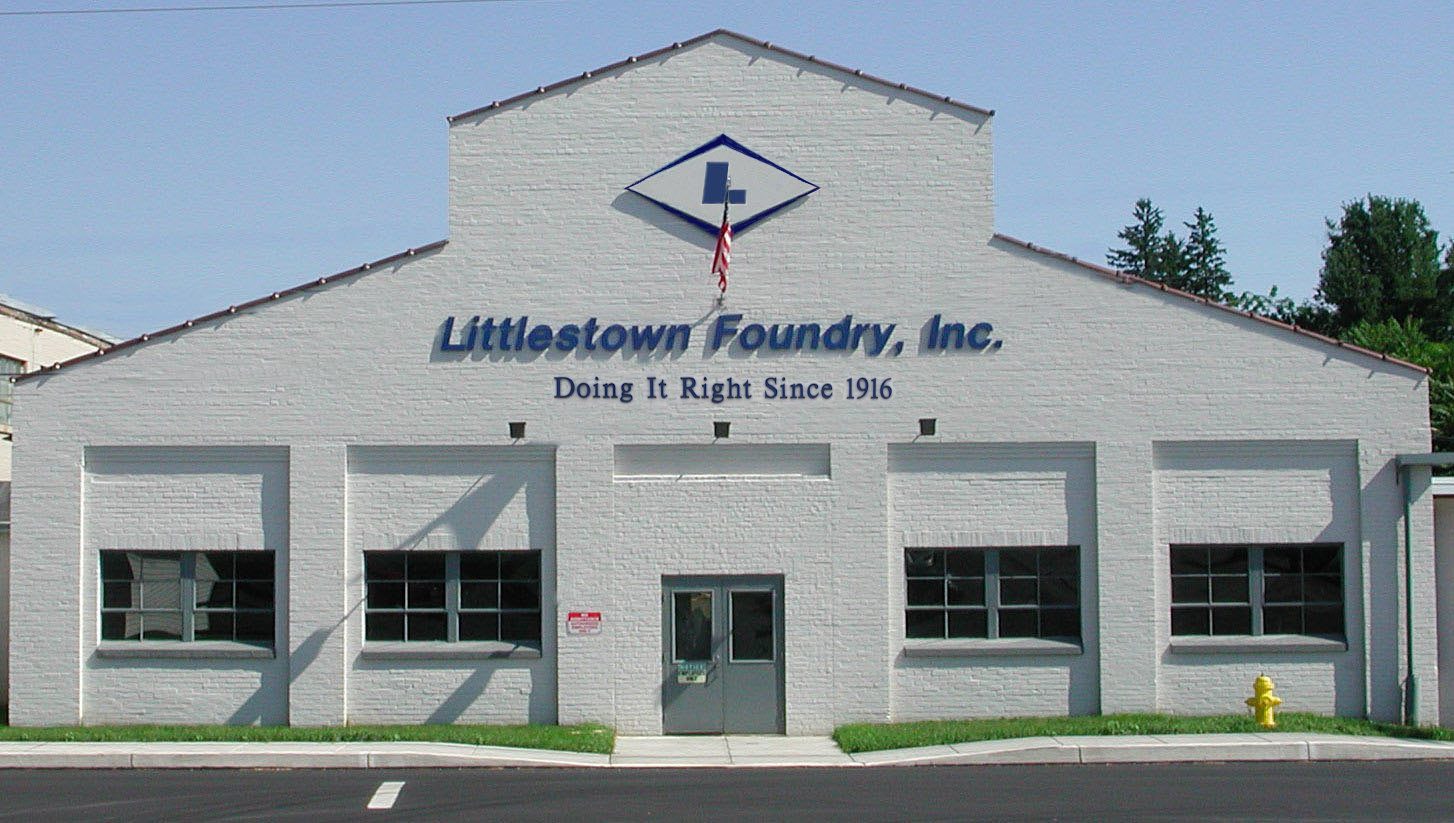
4
Source: Littlestown Foundry
5. Top Quality at New Vista
If you’re looking to see what some top companies in quality are doing, here’s your chance.
New Vista Corp. Baltimore, MD | www.newvistacorp.com
The view from New Vista Corp. looks bright, as the company is seeing demand in new markets.
“We’re in a good time right now for American manufacturing,” says Walter Milligan, sales and marketing manager at New Vista Corp. “I’m looking forward to seeing how it develops.”
“The biggest thing now is expanding the industries we serve. Traditionally most of our customer base has been automotive, but we’ve seen a surge in aerospace opportunities.”
With this increased demand, the company is focused on expanding into new markets such as aerospace, defense and medical.
New Vista Corp. is ISO 9001 certified, an endeavor that was well worth it, says Milligan. They take quality seriously and always follow up with customers to see how their machine is working out. Customer satisfaction is important. “We try to communicate with them at every point in the process, so there are no surprises,” Milligan says.
They often receive repeat customers. “For us the best indicator of a job well done is when the customer comes back and buys more,” Milligan says.
The company does ongoing training and makes sure employees know how their work affects the key performance indicators at the company. As a smaller company, they also have the opportunity to mentor staff as well. In addition to keeping customers happy, they also know how to treat employees well.
“One of the things that makes New Vista a good place to work is that we make sure employees are in a good place for their skills,” Milligan says. “I started in engineering, but it turned out not to be a good fit.” He transferred to the sales and marketing side, and has been “working here happily for seven years.”
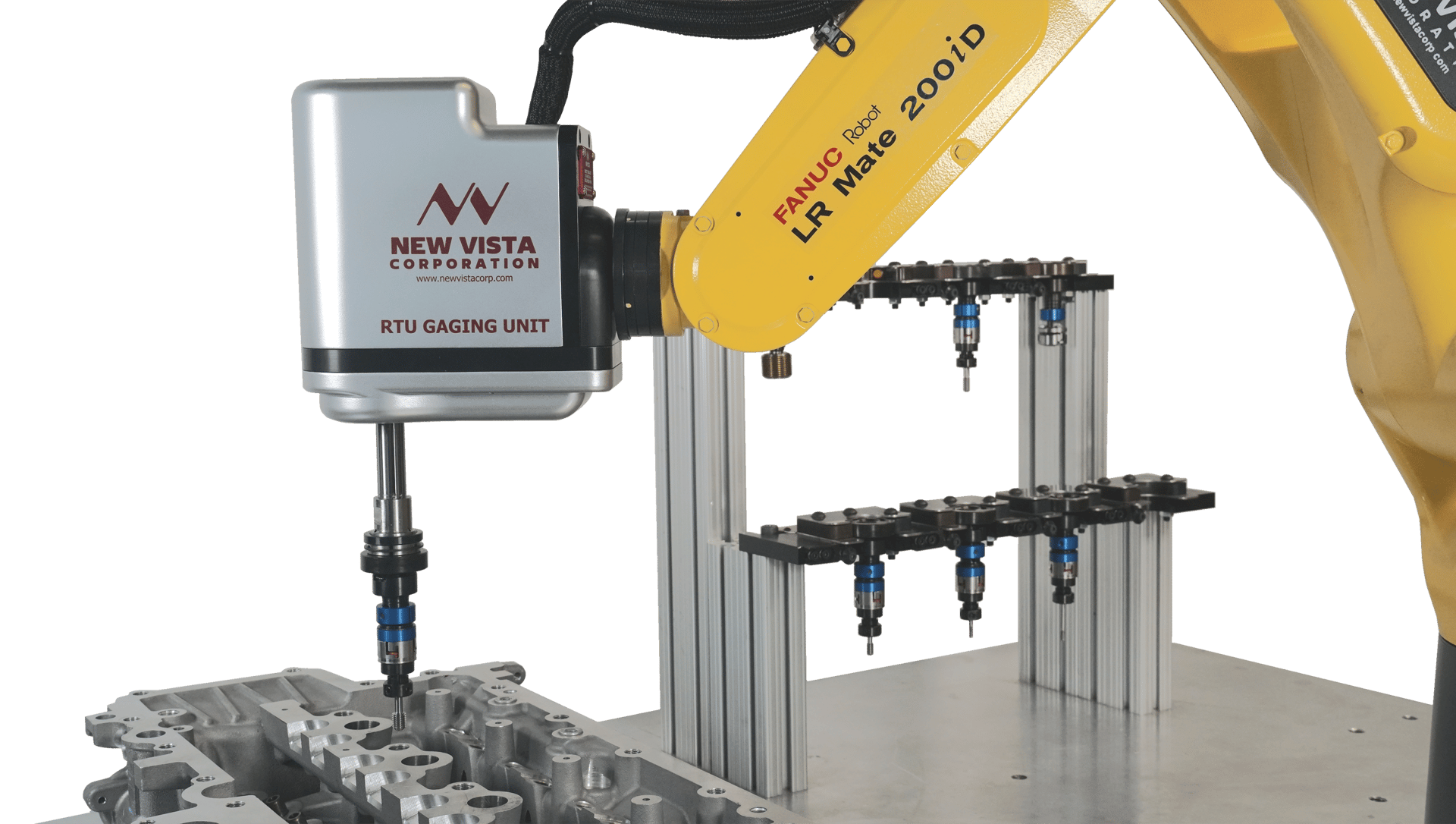