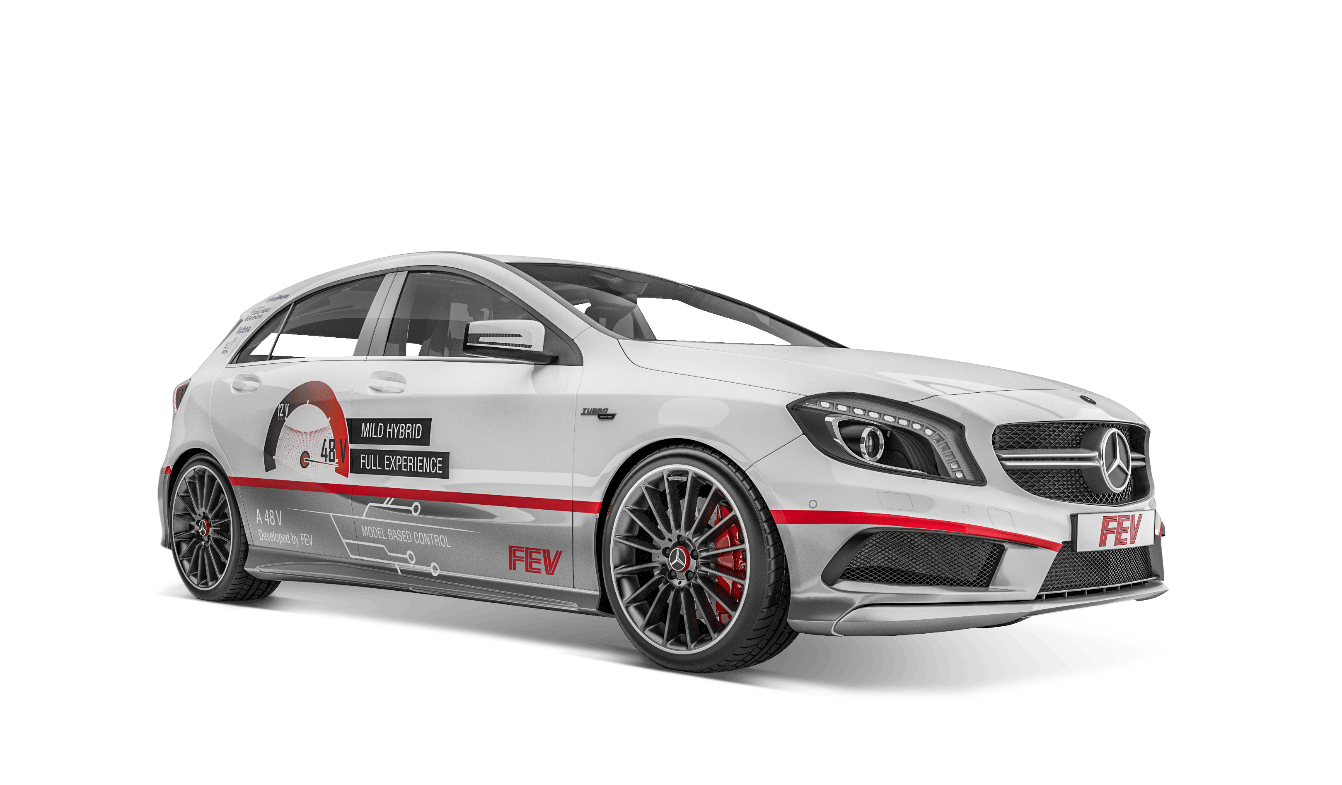
Management
The annual Quality Leadership ranking showcaseS companies leading the way despite manufacturing challenges. By Michelle Bangert
Employee Appreciation Will Get You Far
Maybe it’s a chili cook-off. Maybe it’s recognition. Or maybe just respect.
Whatever it is, top companies know how to treat employees well—and get results. When I spoke with this year’s top Quality Leadership companies, several themes emerged. Employee retention, respect, and teamwork were all priorities. Technology, training and standards are also important.
The survey was conducted in fall 2022. As usual, companies were evaluated on a range of factors, including continuous improvement and quality programs; contribution of quality to profitability and shareholder value; average number of hours that employees receive quality training; scrap and rework as a percentage of sales; warranty costs as a percentage of sales; and registration to various standards such as ISO 9001.
Does your company deserve to be on our annual Quality Leadership ranking? If so, look for our survey this fall.
Thank you to all those who completed this year’s survey.
1. SEG Automotive
Novi, MI – www.seg-automotive.com
Those in the automotive industry will likely recognize SEG Automotive. According to the company, their products are used by almost all major car makers.
“Mobility is an intrinsic human desire – and we at SEG Automotive have been its motor since in 1914,” Ferdinando Sorrentino, CEO of SEG Automotive, says on the company’s website. “Our powertrain components power over 300 million vehicles on the road today. And, beyond that, we have also been a continuous motor for innovation in our field – from the first starter motor to 48V hybridization, light electric mobility and now high voltage solutions. With our vision, we express our desire, and confidence, to extend this role as the ‘motor of the mobility of today’ into the future.”
The company’s product portfolio runs the gamut. It includes an entry-level segment as well as premium solutions, passenger cars and commercial vehicles. No matter what the product, they aim to improve a vehicle’s fuel efficiency and CO2 footprint.
Quality is a key part of their success. The company adheres to worldwide standards and complies with international automotive requirements such as IATF 16949. According to the company website, “Our Quality Policy and Quality Principles combine preventive quality assurance and continuous process improvements with a quality mindset throughout our organization: Quality is a responsibility of every employee at SEG Automotive, from our apprentices to the executive board, at manufacturing plants as well as in all governance functions.”
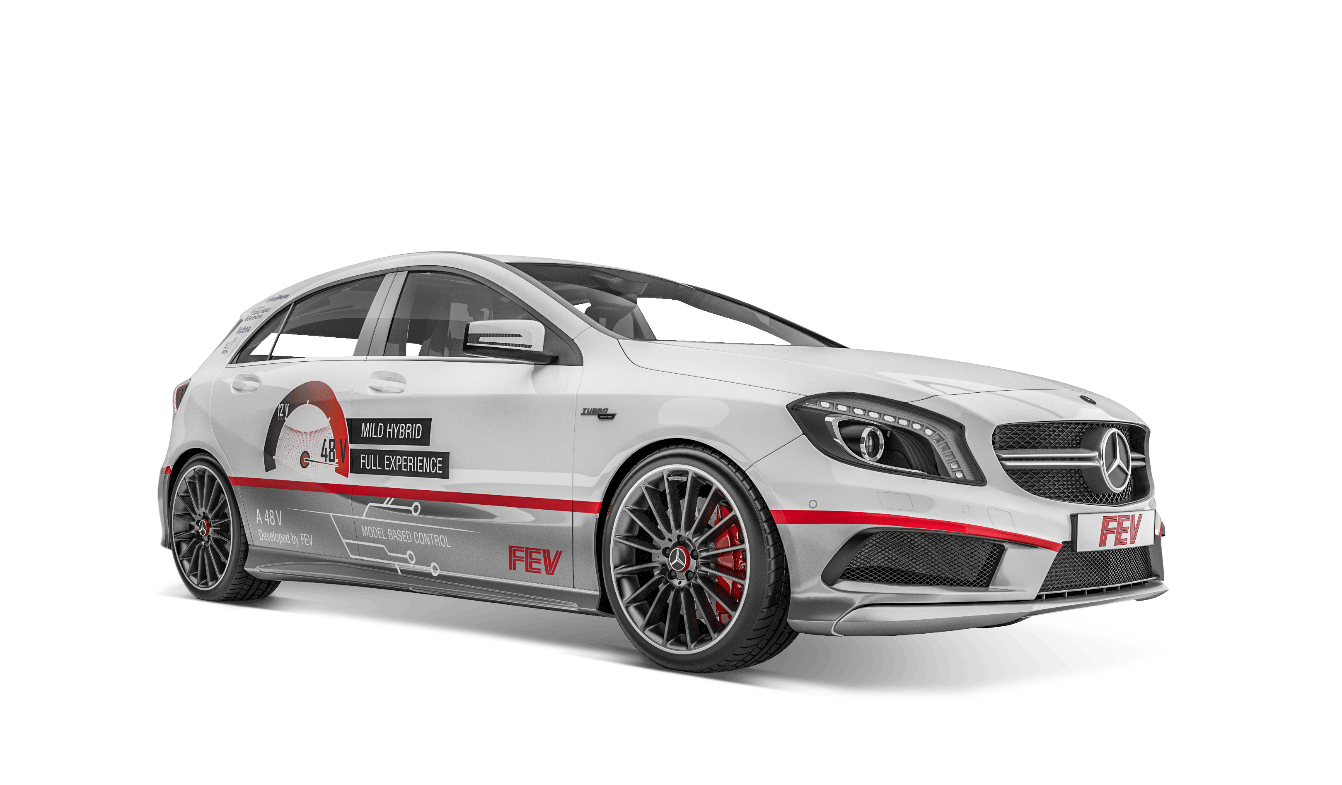
1
Source: SEG Automotive
2. DIT-MCO
Kansas City, MO – www.ditmco.com
DIT-MCO celebrates its 75th anniversary this year.
Andrew J. Zawisza, quality assurance manager at DIT-MCO International, has been with the company for more than 33 years—yet fourteen people have more seniority than him.
The name comes from Drive-In Theater Manufacturing Company. Though the company sold off that portion of the business in the 1950s, the name stuck. The company now makes aerospace testing equipment, with the main product line being ground support testing systems. They also produce parts for the U.S. Department of Defense aircraft.
Dealing with supply chain issues – lead times of more than a year for some components – means that the company has had to raise levels of inventory, not an ideal situation, but they’ve been able to adapt through it all. “It keeps us on our toes,” says Zawisza.
The company has been AS9100 certified for over 20 years. The day we spoke, he had had two meetings with Boeing; one focused on Advanced Product Quality Planning. With the AS9100 standard, he notes that employees must understand the importance of quality on everything they build. “There’s no lackadaisical attitude,” he says.
For other companies looking to improve quality, Zawisza says to focus on documentation and training. “Training is always the biggest thing for us,” he says.
Though their work is not seasonal, he notes that the last quarter of the year is always particularly busy. This year one employee in particular did a “fantastic job getting systems out to customers by the end of the year. She was able to finish critical assemblies in record time.” The company recognized her with a monetary award and presentation in front of the production team.
This seems to touch on two things that many people look for in their career: recognition and compensation. It’s no wonder that the company has such loyal employees.
“I really rely on my quality team for all of their expertise and dedication," says Zawisza. “The team approach is very important to me and I am extremely happy with the way our team works together, day in and day out.”
The company offers fun activities for the staff such as a Halloween costume contest and a chili cook-off. Zawisza won the chili cook-off a few years in a row, but has been shut out the past few years, he says. In keeping with the spirit of continuous improvement, he says it’s time to up his game.
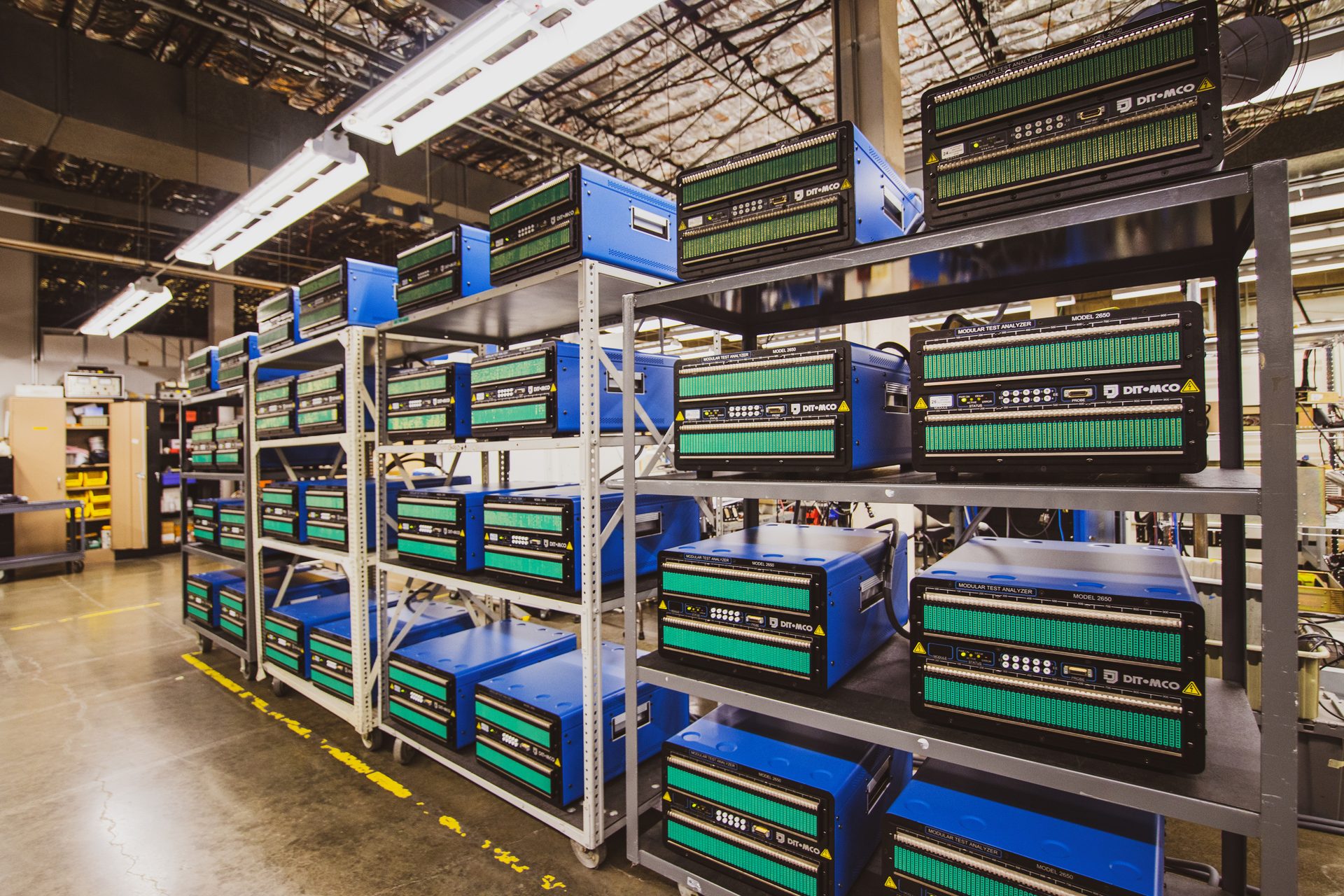
2
Source: DIT-MCO
3. Electro Product Management Inc.
Fairfield, NJ – www.epmtechsales.com
You may recall EPM from last year’s ranking. The company specializes in designing tests and screening procedures for electronic components used in the aerospace, defense, and industrial electronics industries. When I last spoke with Ray D’Alessandro, VP-Engineering, the company was working on their cyber security compliance. Department of Defense contractors will eventually be required to be compliant, and the company continues to be a leader in cyber security.
Since they have achieved this cyber security status, they are currently ahead of the industry. Less than 30% of companies are where they need to be with cyber security compliance, according to their auditor.
This year I also spoke with his daughter and general manager Angela D’ Alessandro who has been with the company for 18 years. She says the company focuses on quality and treats employees well.
Employee retention is an important factor in their success. Several employees have been with the company throughout its 21-year history. Several others have been around for 18 years. In looking at the company organizational chart, there are a lot of double-digits.
With such a stable workforce, the company doesn’t need to work on constantly dealing with turnover. “It makes life easier,” says Angela. Though this doesn’t mean they don’t do training. Longtime employees developed cyber security training and continue to maintain their skills. The company has several certifications: ISO 9001:2015, AS9100, and ESD-S2020.
“Each employee is trained for a different operation,” Ray explains. “The idea there is to make sure that there’s always a qualified employee to take over if someone is out sick, especially with COVID. Each employee is trained on multiple levels. We can’t just put anybody anywhere.”
“We owe our success to our whole team of who have been with us for close to 20 years,” says Angela. “We work together very well because we created an environment of flexibility, safety, and respectfulness. And even with 20 years under our belt, we continually work to get even better, and even more efficient. This is without a doubt a team effort and we are proud of that.”
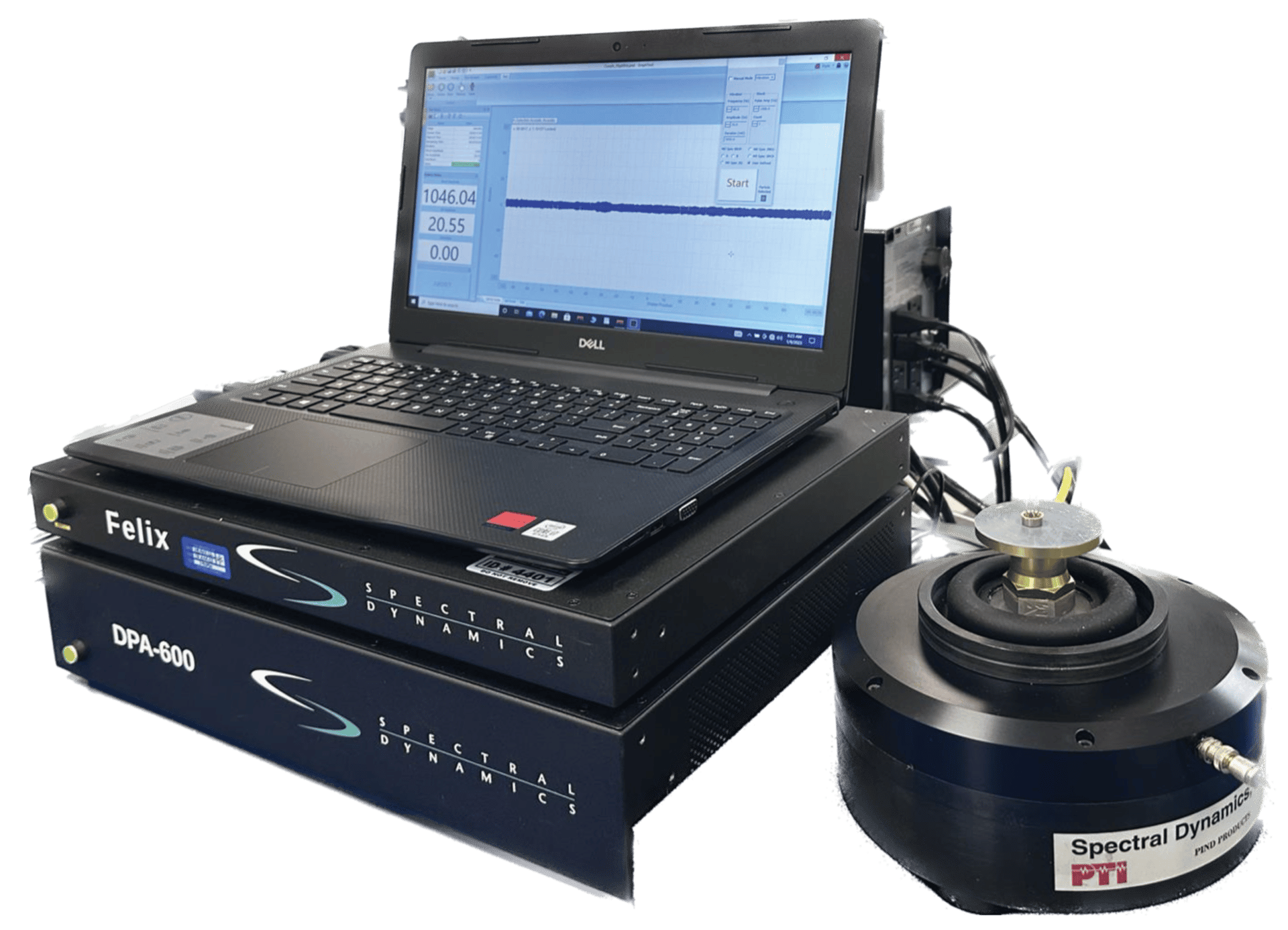
3
Source: EPM
4. Reed Switch Developments Corp.
Racine, WI – www.reedswitchdevelopments.com
Debra Dahlin’s late father, Harold, and his business partner John Hammond started Reed Switch Developments Corp. 56 years ago in the Dahlin family basement. The three-person company began with standard products but saw a need for custom applications, eventually providing “unique products for just about any industry,” says Dahlin, the company's second-generation family owner and president. The company grew from the basement to the dining room to a shared industrial complex to its own facility.
In 2022, this 100% woman-owned small business celebrated two key milestones: its 55th year in business, and 35th anniversary as a Wisconsin manufacturer.
“Our general philosophy is to try and be proactive rather than reactive,” says Jeff Rosenbaum, engineering/QA coordinator. Before, “tribal knowledge would get misplaced.” Now they focus on sharing information so that knowledge doesn’t disappear when someone retires or moves out of a particular position.
“Most of our business comes from OEM custom assembly work,” Rosenbaum says. “There was a time when we would just do simply what a customer would ask of us, without sharing our expertise.” Today, that has changed. “As we work with customers, we get very in-depth, we work with them to define those expectations, we are very honest and open with them: “Yes, this may cost you a little bit more, but here’s the savings that you will see on the other end, with labor savings and a plug and play product,” Rosenbaum says. “We’ve actually converted skeptics into customers with this value-added approach.”
This past year the company also had its highest sales ever. Dahlin says that their team approach is at the core of their success. Suggestions are encouraged and rewarded regularly. Team members are recognized at a monthly meeting and receive a monetary award for these ideas.
Choosing employees is important as well. “We want someone who is quality minded, detail minded, inquisitive, curious, creative, all things we value,” Rosenbaum says. “In looking at automation and process reevaluations, we always want to know, how might we do this better the next time?”
Lean is one key to their success. Internal process standardizations have helped productivity and quality. Continual staff training also helps to make this happen, starting with the first ninety days and ongoing thereafter.
Rosenbaum offers this advice for those looking to improve quality: “My perspective would be to keep an open mind and stay creative. Never rule out someone else’s opinion or the possibility of there being a different answer. It doesn’t always have to be ‘that’s the way we’ve always done it.’ Whatever makes your product a quality product, do it, and stay true to that.”
“If you think, ‘we’ve always done it this way,’ you’ll be out of business at some point,” Dahlin adds. “We wouldn’t be in business for 55 years if we didn’t continually adapt. Otherwise you’re going to get washed away.”
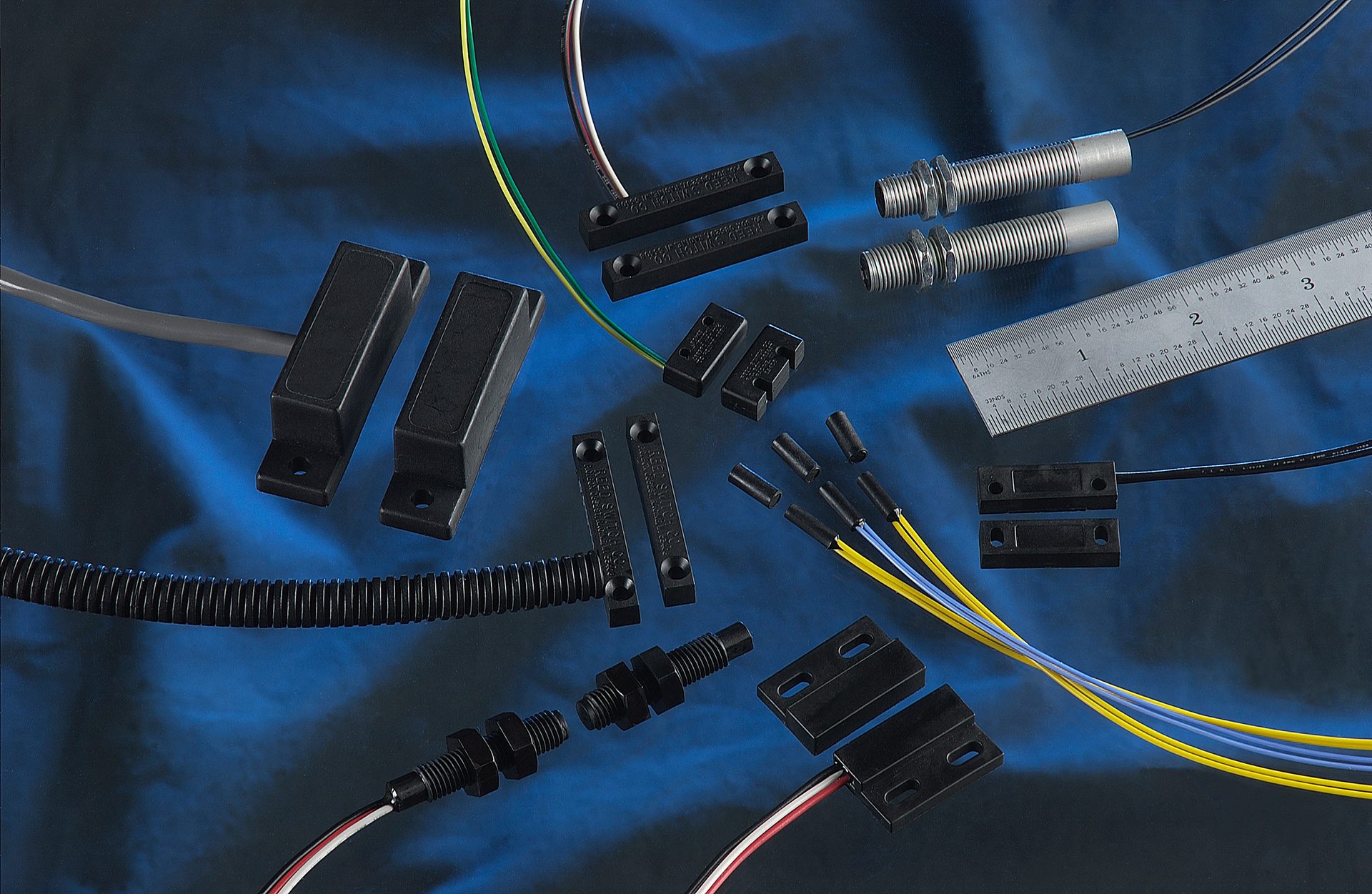
4
Source: RSD
5. THK
Schaumburg, IL – www.thk.com
With a new U.S. HQ President, Nobufumi Sato, THK continues to adapt. According to Tony Peera, new field development manager, business strategy division of THK America Inc., “THK (“Toughness," " High Quality," and " Know-how") is the mark of linear motion, producing high quality and high precision LM guides, ball screws, cross roller rings, actuators, and other products that can be found in almost any industry and application.”
Along with a host of new products, the company had a record sales year in 2022. Perhaps you saw one of their two large booths at IMTS, with robots serving bottled water. And careful readers will note that THK also made our top five list last year as well. In addition, the company recently incorporated their business in Mexico.
He says, “THK’s flagship product, the linear motion (LM) guide system and patented Caged Ball Technology, can improve many applications’ accuracy, speed, assembly times and end user costs. THK’s LM Guides assist machine tools and industrial robots to become capable of ultra-precise operations, and semiconductor-manufacturing devices can operate in submicron units. More recently, the system has been applied in electric vehicles, new 3D print technologies, precise medical and surgical machines, and humanoid robotics.”
Predictive failure detection is possible with their new technologies like OMNIedge and The THK Sensing System that offer customers the ability to access vital data through their PC or smartphone.
But any technology is powered by people, which is reflected in the new company policy. The 2023 company policy states: “One step by 100 people is greater than 100 steps by one person. Let us not make one person take 100 steps. Let us work together to ensure everyone takes one step further. Grow your ability to convey a message. Grow your ability to be understood.”
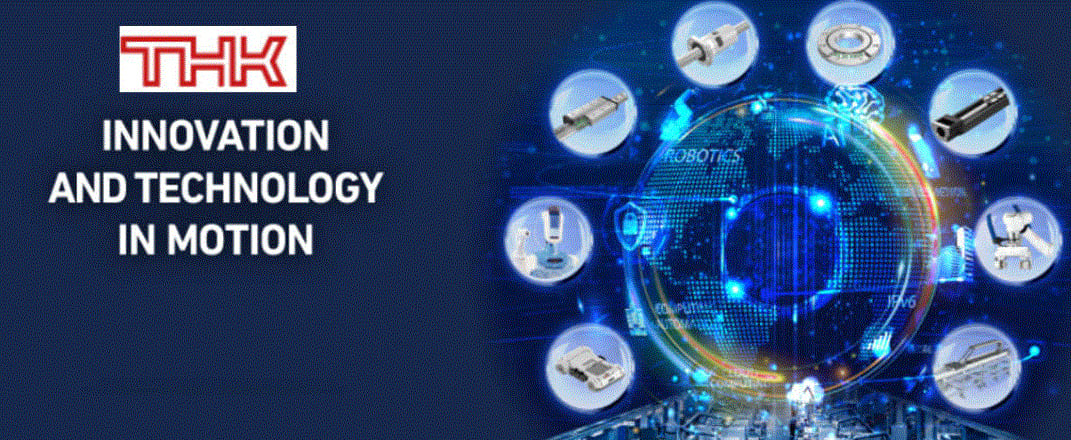