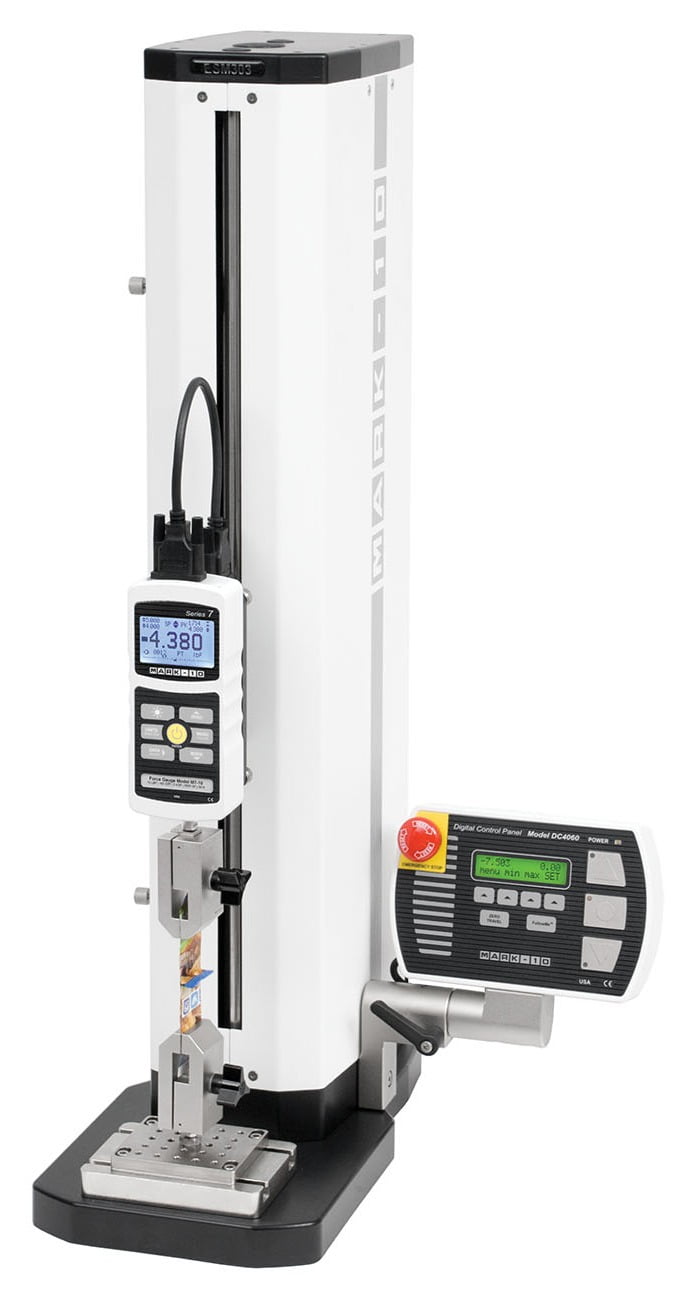
Force measurement is the measure of a push (compression) or pull (tension) against an object. It sounds elementary enough, but it’s a crucial part of quality control testing with more and more applications in today’s globalized supply chain. The needs for force measurement are all around us.
Conventional wisdom stated that high force applications are best served by a materials tester, a machine capable of measuring stress, strain, and many other advanced calculations, in addition to accurately measuring very small deflections via extensometers. Simpler force measurement devices were relegated to low force applications. This generalization often missed the point that there are plenty of simpler, high force applications and plenty of more complex, low force applications. Today’s manufacturers of materials testers and force measurement products recognize these diverse needs, and offer solutions for a broad force range.
In this article, we’ll explore the myriad ways in which force measurement can be a sufficient solution to quality control objectives in production and laboratory environments. While materials testers may be needed to fully analyze the mechanical properties of incoming materials, such as metals, elastomers, and textiles, force measurement systems are more at home testing finished products and components – applications where force data is more important than a detailed analysis of mechanical properties.
Ensuring Product & Consumer Safety
Engineers need to test for various material properties to assure a safe, properly functioning product is manufactured. Companies establish high / low acceptance criteria or a minimum force requirement to compare measurements, thereby ensuring performance and minimizing the risk of defects.
Ensuring Compliance
Compliance is an ever-increasing burden on industry, as the web of local, national, and international standards and regulations expands. In certain sensitive industries, such as medical device and aerospace, non-compliance can lead to penalties and restricted market access.
While ensuring compliance is becoming more difficult, there are many established force measurement standards and methods prescribing how to accomplish particular objectives. Depending on the manufacturer’s particular product, industry, and customer base, they may follow ISO, ASTM, and/or numerous industry-specific standards. Test methods detail what equipment to use, how to prepare samples, what results to obtain, and how to analyze those results.
Established standards aren’t always enough for a manufacturer’s particular needs, so it’s common that companies also develop their own internal test methods and baseline quality metrics.
Product Design & Improvement
Smarter, lighter, faster, better design objectives push the limits of continuous improvement. The data obtained through force measurement can help inform product designers, giving them empirical evidence to support the expectation that their design will be successful once released to production.
Quality Validation
The role of the Quality Department is to make sure that a product is manufactured in conformance to agreed-upon standards. Force measurement data helps isolate problematic individual products, lots, or batches. Armed with this data, quality control and engineering professionals can determine the source of the problem, whether it’s a design issue, component defect, production problem, or other cause.
In short, virtually anyone manufacturing a product. The longer explanation is that certain industries have greater needs than others. Whether small or large, domestically focused or international, the following industries represent an outsize share of force measurement applications:
Medical Device Manufacturing
Medical device manufacturers have been in the spotlight recently, due to their heroic efforts in supplying ventilators, personal protective equipment, and other lifesaving products to fight the COVID-19 pandemic. Consider medical packaging, often involving a disposable sealed pouch. Pouches must be sealed effectively to prevent contamination, while being easy enough to open by medical personnel. Force measurement can verify that such packaging falls between these acceptable limits. Force measurement can also determine if a needle is sharp enough, if a luer connector is sufficiently attached to a tube, or if a bone screw is sufficiently anchored.
Automotive and Aerospace Suppliers
From wire harnesses to radio dials, and from window shades to steering wheels, motor vehicles and aircraft have almost unlimited testing needs. Force measurement can verify that wire terminals are crimped sufficiently, that radio volume dials provide optimum resistance while rotating, and that steering wheel-mounted volume controls have a satisfying click when engaged.
Packaging
Why should we need a special kitchen tool just to force open the bottle cap of a jar of pickles? Bottlers must monitor the removal torque of jars, bottles, and containers, whether they contain motor oil or perfume, to ensure a satisfactory customer experience. When opening a bag of pretzels, whether via shear tab or pulling at a seal, packages must be intact when they arrive on your kitchen counter, but still easy enough to open without scattering snacks across the floor. Force tests can quantify the likelihood of a satisfactory customer experience.
The force measurement equipment menu is long and extensive. Deciding what to order is made easier by answering a number of questions about the application, such as:
Basic Instruments
The ubiquitous force gage is an instrument, which may be handheld or mounted to a fixture or test stand. It contains an internal load cell, with electronics and a display. A threaded shaft is commonly affixed to the load cell, and protrudes from the housing of the instrument. Grips, fixtures, and implements to engage the sample may be mounted to the shaft.
Force gages are available in many force capacities, from as low as 50 gF (gram-force) full scale to as high as 2,000 lbF (pound-force). In the U.S., a majority of force testing procedures call for results in lbF (pound-force). In most other countries, results are commonly expressed in N (Newtons), kN (Kilinewtons), or kgF (kilogram-force). Force gages have selectable units of measurement to accommodate local preferences.
Choosing an appropriate capacity is one of the most important considerations in selecting a gage. As a general rule, force gages should be used at no less than approximately 5-10% of their range. For example, an application requiring 8 lbF is best matched by a 10 lbF capacity force gage. A 1,000 lbF capacity instrument would yield low accuracy and coarse data resolution.
While force gages contain integral load cells, in certain applications a complete instrument cannot be placed at the site of force, for example in measuring the downward force of a hydraulic press. In these cases, a remote load cell paired with an indicator is a viable alternative. Such systems closely resemble force gages in terms of features and available force ranges.
Benchtop Systems
A force gage or load cell can be mounted to a test stand, ensuring axial alignment with the sample and providing repeatable test speed. Test stands can be manually operated via hand wheel or lever, or motorized. While manual test stands are generally inexpensive and portable, speed cannot be guaranteed, thus limiting their ability to conform to test methods requiring specific test speeds.
In addition to regulating speed, motorized test stands can be programmed to perform more advanced functions, such as auto-reversing at a force limit, distance limit, or sample break. It can also cycle continuously between limits, for fatigue testing, and maintain a load over a period of time, for durability analysis.
Software
Force measurement manufacturers offer software packages specific to their products. However, because most force measurement instrumentation can communicate via USB or RS-232, users may choose to use a third-party SPC application, or develop their own program to interface with the instrument and process data according to their needs.
Often, the stickiest part of a system configuration is how to engage the sample. For common applications, such as peel testing and tensile testing, there’s a wide variety of task-specific grips with proven track records. In other applications, for example engaging a small component in a drivetrain assembly, custom fixturing may be needed. Rapid advancement in 3D printing has democratized the process, bringing custom fixturing within reach of many more companies with limited personnel or financial resources.
Whatever the grip or fixture, it must hold the test sample in a repeatable position, thereby ensuring that test results are compared on an apples-to-apples basis. Additionally, if a vise-action grip is used, consideration should be given to samples sensitive to extraneous loads. Clamping force should be controlled and consistent.
Understanding the language of force measurement can help achieve quality control objectives simply and economically, enabling manufacturers to confidently produce and market their products around the globe.