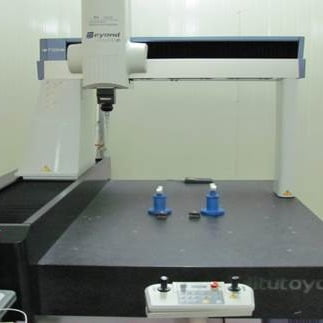
My work in inspection, and as a quality management system auditor, provides numerous opportunities to acquire knowledge. It also provides areas of risk for ensuring valid and reliable results. One risk that keeps repeating itself in my audit findings is the treatment of surface plates. Instead of being treated as a precision device, they are treated as an area to stack tools, parts and other debris. The root cause of this treatment is the lack of knowledge about the surface plate and its mistaken identity as just a table. Let’s take a journey of the history and recommended care for the surface plate.
The surface plate was designed and developed as a precision tool by Henry Maudslay and Joseph Whitworth in order to ensure the production of identical tool parts. The first surface plate was composed of cast iron. The first surface plates were sold in 1904 by the Crown Windley company. During World War II, metal was in high demand which resulted in the introduction of using granite, a non-corroding metal that is extremely hard and non-magnetic.
Engineering and manufacturing specifications are demanding tighter tolerances, which elevate the importance of accurate measurements. To deliver measurements, each piece of metrology equipment requires a base plate.
Granite is the most common material used for surface plates. The surface plate does require maintenance. The following are recommendations for maintaining these precision instruments:
Along with checking the flatness of parts, surface plates can identify part warpage. The surface plate is the “0” reference point. If a height gage is used on the plate, the inspector can place the gage anywhere on the plate and zero the gage. This can be completed in conjunction with a gage block. The gage block is removed, and small parts can be accurately measured. This is also a technique to verify small parts for flatness.
The surface plate is an underrated metrology tool. It has been more than 80 years since granite was identified as an alternative to cast iron. Granite surface plates have become foundation for many standards in metrology. The coordinate measuring machine (CMM) does represent the acceptance of granite as the only material used in this vital area of metrology. Hopefully, you were able to obtain knowledge and insight on why I feel it is critical to properly maintain surface plates. Valid and reliable results must be acquired in order to make proper decisions on the disposition of parts.