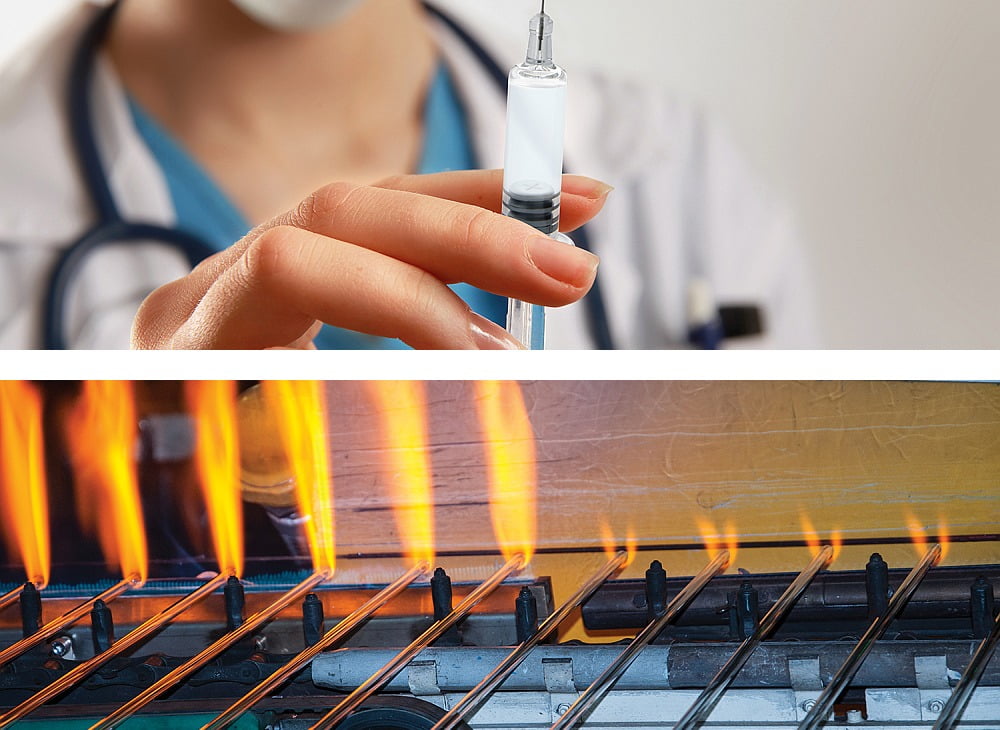
This Case Studies Special Advertising Section features manufacturing companies with real-world challenges using quality equipment, software and services to solve their problems and improve their processes. These problem-solving stories describe myriad manufacturing challenges and how the correct application of a supplier’s product or service made the difference, providing quantitative benefits to quality and manufacturing issues.
The suppliers in this special section present these real-world problems and solutions to help Quality Magazine subscribers who may have similar experiences.
Case Studies
— Special Advertising Section —
Nipro Corporation was established in 1954 under the management philosophy of contributing to society through its business activities. Today, Nipro PharmaPackaging products are used on a global scale and lead the world market. The Nipro brand is highly regarded worldwide for its technological superiority and high quality.
Diana Coblentz of the Westport, IN location reports that prior to GAGEtrak, the company used an Access program that was designed in-house. They later decided that a validated system was required to track their gage and calibration data, so they selected GAGEtrak, the world’s #1 calibration management software solution.
Since 2007, Coblentz has used GAGEtrak to manage the calibrations of approximately 250 gages and notes that she has configured the software to email her a list of calibrations due every day, which saves time and assures that no gage will be forgotten. Coblentz says that GAGEtrak is, “…efficient – covers all areas needed for calibration.” Coblentz also reports, “Our customers like this system better than what we had.”
The company has also taken advantage of GAGEtrak regional training and the calibration label kit to reduce the learning curve and improve efficiency even further. And on the CyberMetrics support team, Coblentz says, “Everyone I have worked with for support was very helpful and nice to work with. The support team does a great job.”
GAGEtrak is used at thousands of facilities worldwide to improve measurement quality, assure compliance and increase efficiency. Contact CyberMetrics today to learn how GAGEtrak will do the same for your company.
A manufacturer of headphones required a quantifiable method of describing the feeling of earpad cushions against a consumer’s ears, and gauging the ability of headphones to fit snugly over a period of time. It was determined that force measurement was an ideal method by which to quantify the differences in “feel” from one set of headphones to another.
A Mark-10 horizontal motorized force tester pulls the earpads apart, and monitors the relationship between force, time, and distance. Custom fixtures engage the manufacturer’s earpads, as well as their competitors’. The tester is used for the following testing methods:
By correlating force, distance, and time, the manufacturer reports that they can better optimize their product designs to meet and exceed customer expectations.
888-MARK-TEN
Tel: 631-842-9200 x13 | Fax: 631-842-9201
www.mark-10.com
Manual gauging processes were incapable of delivering the throughput necessary to achieve a high-volume part-manufacturing target at Olympus NDT. By automating inspection processes using a programmable shop floor gauging system, they gained manufacturing capacity, improved part quality and reduced scrap.
Olympus NDT is a leading manufacturer of non-destructive testing (NDT) instruments used in industrial applications. Their cutting-edge technology can identify hidden flaws and imperfections in a range of parts and materials. They manufacture precision wedge components to correctly align parts for non-destructive part testing. Demand for NDT wedges has grown rapidly in recent years, and the increased workload made automation essential to achieve manufacturing efficiencies.
While the dedicated 5-axis CNC milling machine and loading robot allowed production through multiple shifts, post-production inspection of the wedges was creating a bottleneck and costly downtime. Manual gauging techniques were slow, and the increased production was placing a high demand on labor. Renishaw’s Equator™ gauging system was considered the ideal in-process solution, ensuring reliable inspection results and maintained repeatability at high operating speeds.
Automating the wedge inspection process using Equator helped Olympus NDT achieve its manufacturing and throughput goals. The complete implementation is an alternative to labor-intensive manual gauging and has also delivered rapid ROI. The solution clearly demonstrates how production bottlenecks can be overcome. The system is located adjacent to the CNC machine, carrying out 100%-part inspection rather than sample inspection. The ability of the Equator system to interface directly with the CNC machine allows necessary offset updates to be made automatically when drift in feature size or position is detected resulting in minimal reject parts.
Challenge:
When a customer in the surface metrology industry needed help finding a better way to inspect freeform optics, they asked Aerotech for a solution that would allow them to measure faster, more precisely and with the smallest possible machine footprint.
Solution:
With 50 years of expertise specializing in custom-engineered precision motion products, Aerotech was able to develop a custom solution to measure parts up to 40 percent faster with a 60 percent smaller machine footprint than conventional Cartesian systems. The measurement device, called the surface measurement motion platform (SMP), is now available to other Aerotech customers as a standard product that can be customized to meet their specific needs.
The SMP integrates four axes of motion to deploy an innovative spiral scan. The workpiece is positioned on the lower-axis, rotary, air-bearing stage. Linear, vertical and rotary stages on the bridge above it move the measurement sensor, allowing the user to maintain a constant distance and normalcy to the optic being measured. This configuration gives users precise control of the measurement.
Unlike a Cartesian system using a raster-scanning technique, the SMP’s spiral scan saves time by eliminating extraneous linear motion. Because the part is continuously rotating below the sensor, users can scan over the entire part with less motion, which enables a smaller machine footprint as well.
aerotech.com/smp
sales@aerotech.com
412.963.7470