H2 Deck By Bold Name
h2 xxxxxx
H1 xxxxxx
h2 xxxxx
Software & Analysis
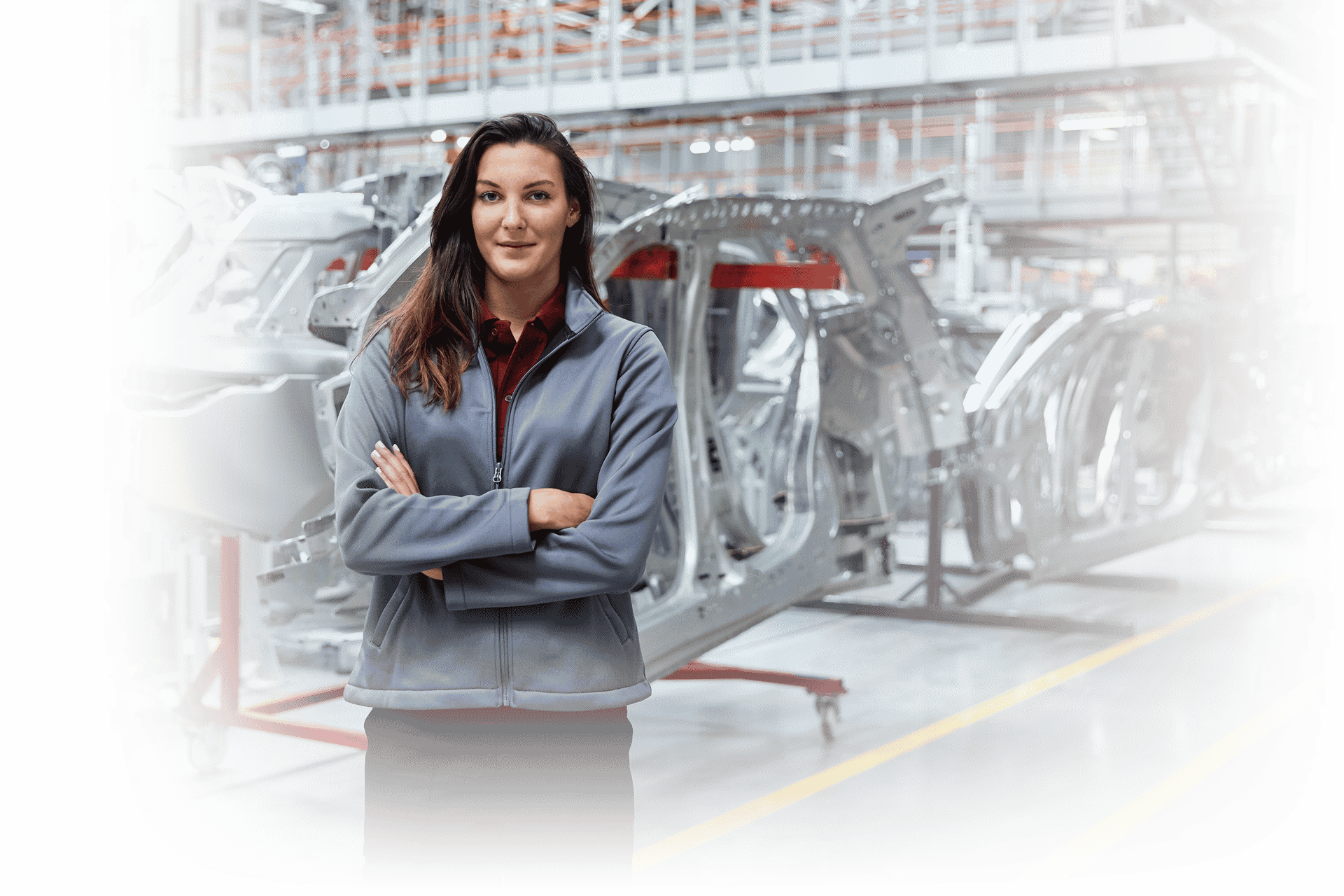
The manufacturing sector may be facing challenges, but the future is full of possibilities for those willing to innovate, adapt, and invest in their digital future. By Matt Riesenbach
Move Forward, Not Backwards in 2025: A Manufacturing Tech Outlook
Software & Analysis
H2 Deck Info By Paragraph Style Bold
Headline
The manufacturing sector continues to face significant challenges, from labor shortages to macroeconomic pressures, creating an uncertain business environment. The growth of U.S. manufacturing presents mixed signals—while some domestic resurgence has occurred in response to global supply chain disruptions, other reports suggest that manufacturing is not fully returning home. U.S. election cycles further compound this uncertainty, as they often bring hesitancy for change and slow decision making when it comes to investment. However, now is not the time to hold back on the digital transformation progress the industry has achieved since the pandemic. The market is ripe for innovation and investment, and manufacturers should capitalize on the opportunities ahead, rather than sitting on the sidelines.
As we look toward 2025, several key trends are expected to shape the industry, presenting small and mid-sized businesses (SMBs) with opportunities for growth and transformation.
Innovating through labor shortages with automation
The labor crisis in manufacturing has shifted from finding workers to managing high rates of attrition. During the pandemic, the sector lost 1.4 million jobs, and forecasts from the Manufacturing Institute predict that 2.1 million positions will remain unfilled by 2030 due to a lack of skilled workers. Inflation has further compounded this problem, raising production costs and making it harder to attract and retain talent, which is driving the persistent labor shortage the industry is seeing. Recent economic uncertainty due to inflation and global conflicts in late 2023 led many SMBs to freeze hiring entirely or downsize. As they continue to innovate and adapt to navigate around these factors, manufacturers must be careful to balance labor costs with potential drops in demand.
According to a report from the U.S. Chamber of Commerce, even if durable goods manufacturing achieves full employment, only 75% of vacant positions could be filled. Looking at this issue globally, Korn Ferry estimates that by 2030, a staggering 85 million jobs may remain unfilled due to the lack of skilled labor. This shortage is accelerating the adoption of automation and artificial intelligence (AI). Automation is no longer seen as a threat to jobs but as a necessary solution to complement the existing workforce and alleviate the labor gap. More manufacturers are investing in technology such as robotics and AI-driven systems to improve efficiency and reduce reliance on human labor. Tools like enterprise resource planning (ERP) systems are becoming essential to managing operations and helping SMBs streamline their processes. As we move into 2025, technology integration will continue to play a pivotal role in addressing labor shortages and optimizing production.
Building resilience against cyber threats
With the industry’s growing adoption of automation and interconnected systems comes with increased exposure to cyberattacks. The manufacturing sector is a leading target for cyberattacks. The risks are particularly high for critical industries such as pharmaceuticals and aerospace, where ransomware attacks can have widespread repercussions. A prime example of this vulnerability is the ransomware attack on Change Healthcare, a medical firm, which caused severe disruptions to pharmacies across the U.S. This attack resulted in significant delays in the distribution of prescription medications for more than 10 days and ultimately led to a $22 million ransom payment.
As manufacturers continue to integrate more advanced technologies, cybersecurity will remain a top priority for manufacturers. Companies will need to partner with vendors that can provide regular software and hardware updates and robust cloud-based data backup solutions. In addition, employee training on cybersecurity best practices, such as using strong passwords and identifying phishing attempts, will be essential. Research from the Ponemon Institute and IBM reveals that 21% of data breaches result from employee or contractor negligence, highlighting the critical role of human error in cybersecurity breaches. By embedding cyber resilience into their organizational culture, manufacturers can not only protect themselves but also enhance the security of their broader business networks. Investing in cybersecurity now will help safeguard against costly attacks in the future.
Future-proofing supply chains with analytics
Post-pandemic supply chains have been slow to recover. Ongoing material shortages, resource constraints, and logistical hurdles continue to challenge manufacturers. Geopolitical tensions, such as the U.S.-China trade war and the war in Ukraine, further destabilize supply chains. Natural disasters like hurricanes, floods, and droughts add another layer of unpredictability, disrupting production in key regions.
In response, many companies are rethinking their supply chain strategies, moving away from “just-in-time” production models and adopting “just-in-case” approaches. Diversifying suppliers and investing in more localized and resilient supply chains are becoming common tactics for navigating these challenges. End-to-end visibility into the supply chain is crucial for overcoming these disruptions. Delays, stockouts, and inefficiencies can be mitigated using advanced data analytics. SMBs, which may lack sophisticated internal data analysis teams, can benefit from ERP systems that offer analytics capabilities to help them identify hidden patterns and trends, enabling smarter, data-driven decisions. By 2025, manufacturers will increasingly rely on predictive analytics to maintain supply chain visibility. ERP systems equipped with these advanced tools will provide manufacturers with the insights they need to anticipate challenges and adapt in real-time, positioning them to stay competitive in a complex global market.
Empowering teams with enhanced user experience
As younger generations, particularly millennials, begin to take over leadership roles in family-owned SMBs, their familiarity with seamless digital experiences, like those offered by smartphones, is driving demand for more user-friendly interfaces in manufacturing technology. This demographic shift, combined with the labor shortage, is pushing manufacturers to not only focus on technical upgrades but also prioritize the user experience of their software and systems.
Modern ERP solutions have evolved significantly, offering SMBs the operational intelligence and flexibility that were once only accessible to large enterprises. These platforms can now predict market trends, automate complex tasks, and provide real-time insights that guide strategic decision-making. However, to appeal to the new generation of leaders, these solutions must also be intuitive and user-friendly. This shift toward a better user experience is key to empowering workers at all levels of the organization to adopt and effectively use these advanced systems. As a result, manufacturers will need to ensure that their digital tools are not only technically capable but also accessible and easy to use.
Leveraging AI for smarter, faster manufacturing
Artificial intelligence (AI) and machine learning (ML) are making significant strides in manufacturing, offering solutions to some of the industry’s most pressing challenges. While AI is still considered a developing technology, its potential in manufacturing is undeniable. AI-powered systems are already being used to monitor production lines, analyze images or data to detect defects, and identify anomalies in real-time. This can significantly reduce waste, improve product quality, and ultimately enhance overall efficiency.
Machine learning algorithms are also being leveraged to optimize production processes. These systems can analyze historical and real-time production data to fine-tune equipment settings, increase efficiency, and reduce energy consumption. AI and ML are making manufacturing operations smarter by providing predictive insights that help managers make more informed decisions, such as when to perform maintenance or how to adjust production schedules based on demand. Generative AI, another promising innovation, is poised to offer SMBs powerful tools for tasks like automating report generation, conducting predictive analysis, and optimizing workflows. By using AI to manage inventory, forecast demand more accurately, and allocate resources more efficiently, manufacturers can achieve more sustainable growth and stay ahead of market demands. As these technologies mature, they will become increasingly essential to the future of manufacturing.
Embracing innovation in 2025 and beyond
The manufacturing industry stands at a crossroads. While there are undeniable challenges—from labor shortages and economic uncertainty to cybersecurity risks and supply chain disruptions—there are also significant opportunities for growth. Manufacturers that embrace digital transformation and invest in automation, AI, and predictive analytics will be better positioned to navigate these challenges and capitalize on the opportunities ahead.
The labor gap can be addressed through technology, not as a replacement for human workers, but as a way to augment the workforce and fill critical roles. Cybersecurity must become a priority to protect operations from growing cyber threats, especially as more businesses move to cloud-based systems and interconnected networks. Meanwhile, supply chain resilience can be enhanced through advanced data analytics, giving manufacturers the visibility they need to respond to global disruptions more effectively.
As we move toward 2025, manufacturers that focus on adopting cutting-edge technologies, improving their user interfaces, and enhancing their cybersecurity measures will be the ones that thrive in this evolving landscape. The manufacturing sector may be facing challenges, but the future is full of possibilities for those willing to innovate, adapt, and invest in their digital future. In conclusion, while the road ahead presents both risks and rewards, manufacturers have a clear path to success through technology adoption and process optimization. By addressing labor shortages with automation, improving supply chain resilience with data-driven insights, prioritizing cybersecurity, and enhancing the user experience, manufacturers can transform their operations and drive sustainable growth. The key to success in 2025 and beyond lies in embracing these trends and making strategic investments today.