Trends
Trends
Vision & Sensors
V&S
H2 Deck By Bold Name
h2 xxxxxx
H1 xxxxxx
h2 xxxxx
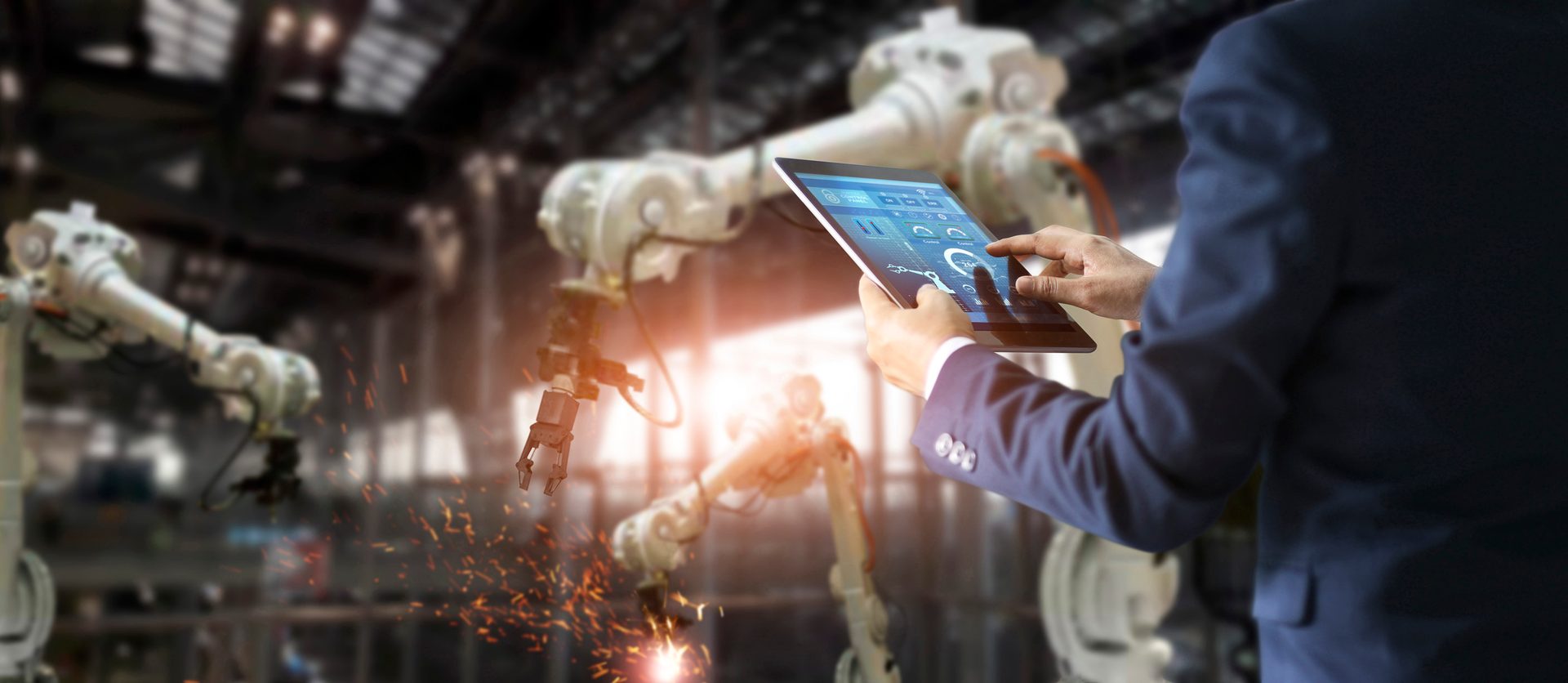
Dive into the world of artificial intelligence (AI) and machine learning and learn how to deploy and maintain this evolving technology. By Heath Stephens
Machine Learning and Artificial Intelligence Tools: The Benefits, How They Work, and Avoiding Common Pitfalls
In the past, most companies would record their process trends with pen and paper. Operations staff would be tasked with recording this data and analyzing it manually for any deviations. Today, control systems can record these trends digitally, and most companies now have volumes of process data at their fingertips. However, the analysis is still conducted in much the same way, with operations staff manually identifying trends to pinpoint what caused a spike or deviation from a normal process.
While this is certainly better than studying paper charts, in the end, you’re still doing the same thing. You’re a human looking at a trend line on a graph. While this can still bring some things to light, there are much more advanced and beneficial ways to process this data. Enter artificial intelligence (AI) and machine learning.
Defining AI and How it Works
AI is a popular buzzword right now. When referring to AI in manufacturing, we’re not talking about the chat-based AI platforms making headlines today, such as ChatGPT. For process analysis, we are talking about smaller AI models with a few dozen - or less - data points. AI and machine learning engines are multivariate analysis models that look at data and find correlations that would be difficult or impossible for a human to find.
Most current AI data analysis models are built to simply look at data: they don’t understand the process underneath. Some physics-based models may understand the process, but those generally require more training and setup time. As such, we will focus on some of the most popular data-driven modeling packages with AI tools that identify data correlations. Because the AI model treats all data equally, it will sift through and determine what is important and what is not – whereas a human might cherry-pick the data based on their process knowledge and available time.
Once the AI package has sifted through the data, it makes correlations and finds relationships based on what it deems important. Since humans are limited with time, they interpret the data based on preconceived notions that impact their analysis. In essence, humans typically prefilter the data used for analysis, whereas an AI model can be fed a broad array of data without bias.
For example, maybe it starts processing data regarding the cooling water temperature inside a vessel. The AI notices that when the neighboring vessel B is cooling, it’s affecting vessel A in a way your operators were not aware of. This leads to the discovery of an overall cooling water limitation that needs to be rectified.
AI is also good at detecting subtle relationships. Maybe a human notices that if value A increases, value B increases and causes a problem. But only AI notices that when value B increases and value A increases afterward, it does not cause a problem. AI models will deduce this not just by looking at one variable, but multiple variables altogether to make predictions.
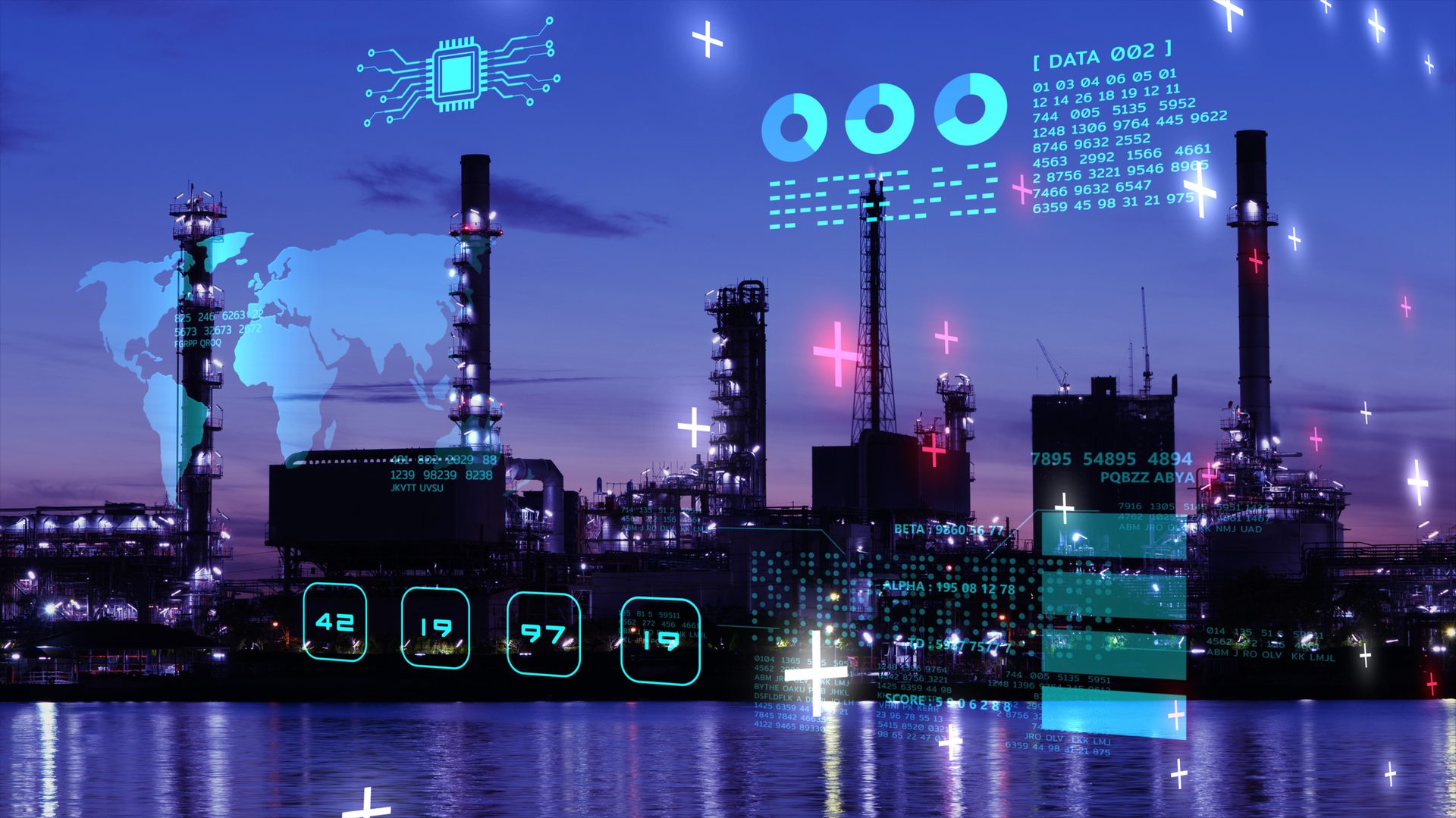
Caption
Machine Learning Defined
AI mimics natural intelligence so that every if/then statement does not have to be programmed manually with canned responses for met criteria, making machines emulate human cognitive processes. Machine learning is a subset of AI that uses a self-reinforcing training process to teach a machine to perform a certain task. Often, this involves the use of neural network statistical techniques that associate probabilities with certain data input patterns.
One example of this would be showing the tool pictures of what good parts look like and what bad/defective parts look like. If that machine is designed for a factory processing produce, it could be trained to knock out individual pieces of poor quality fruit from the conveyor line using a top-mounted machine vision system.
The Benefits of Utilizing Machine Learning and AI
AI allows users to better understand their processes and make more accurate and actionable predictions to improve their processes. This can result in improvements in quality, safety, throughput, and more.
One of the biggest benefits of AI is that it does not stop to take a break. Just like a fully automated process, AI is on the job 24/7 collecting and analyzing data.
AI and Machine Learning Tools
There are many readily available industrial AI tools and deciding which to use depends on budget, planned usage, and the available time for installation and maintenance. Most of these tools are designed to address reliability, quality, or uptime issues – often these issues are tied together.
Some AI software packages are installed on a PC and run locally. With this option, the equipment owner is responsible for setting up the software, configuring it, and looking at the data and results. Other AI options are cloud-based (software as a service – SaaS), where data is pushed into the platform and the software vendor analyzes the data.
Multivariate analysis software could be considered the primary tool category in the Industry 4.0 space for individuals looking to improve quality, predict downtime, and more. These models take data and ingest multiple variables, looking for leading indicators of issues. The user will need to define the parameters for the system because these packages generally do not understand the data they are viewing. They are only making statistical inferences. With these tools the user feeds historical training data into the system and defines different run periods that represent good and bad process behavior or outcomes. When presented with new data, these tools attempt to determine if the current patterns match something that was seen in the training data.
There are also AI tools that operate on the single loop control level, many of which have been available for ten years or more in modern control system platforms, options like “fuzzy logic” and neural network blocks.
Fuzzy logic tries to mimic human decision making and operates with a decision tree approach that can allow for more nonbinary choices – where the value is neither a 1 nor 0, instead more like .05 or .95. Fuzzy logic blocks can provide better performance with less oscillation or overshoot in nonlinear processes than traditional PID blocks.
Neural network blocks work similarly to some of the larger multivariate analysis blocks, mimicking how the human brain works. They involve neural nodes that build statistical models on training data instead of just applying a simple equation like a PID algorithm. This allows the model to better predict the desired control output based on your process conditions and gives you more flexibility to get the control value you want. Whereas with a PID algorithm, the user only has three tuning parameters to determine how it reacts to process changes. Usually, neural network blocks and fuzzy logic are sold as built-in functions or an add-on package for your control system.
Another option is an advanced process control (APC) package. This technology has been around for 30 years and has been somewhat ‘grandfathered in’ to the Industry 4.0 category. Many sectors are now adopting APC technology for their continuous processes, as it has come down in pricing, has improved usability and functionality, and has a decades-long track record of increasing profit margins.
Common Obstacles in Implementation and Maintenance of AI and Machine Learning
First, every user should realize that there will be some level of time commitment with any AI effort. The workload for an end user is highest at the implementation stage, but continued maintenance of an AI system is critical to ensure that the software continues to perform as needed.
Software Relies on the Hardware
The AI software is reliant on quality incoming data. No plant is perfect, and every facility will have instrumentation issues. The first pass at feeding data into these tools will often reveal gaps. Some possible issues could be a missing instrument for a critical process variable, instruments that are not sensitive enough or are not calibrated correctly, or the lack of sufficient historical data to provide a good training data set.
AI Can Only Make Recommendations
Once the data has been analyzed and revealed new insights, the problems can be identified. Then, instrumentation and/or process changes will need to be made. There needs to be a budget plan not just for the software costs, but also the costs of implementing the recommended changes. These changes may also require time and buy-in from other stakeholders.
Sometimes Human Intervention is Inevitable
If you have a software acting as a watchdog, you still need an operator to perform a corrective action when the alarm sounds. Even as the system becomes more advanced, a person will still need to check the findings and decide whether to follow the recommendations. A human will have the context that AI lacks.
To avoid these obstacles, follow these three suggestions to improve your outcome:
- Make sure you have good data funneling into the system.
- Be prepared to act on the recommendations of the system.
- Ensure that you are working with the right solution provider and software packages for the job.
Taking Advantage of AI and Machine Learning
AI and machine learning take data analysis to a level that humans alone are not capable of, providing real-time insight into your process in ways not previously possible. As with all technology, there are common obstacles to avoid, but if implemented and maintained correctly, a manufacturer should see significant production savings from higher quality, better throughput, reduction in scrap, reduced unplanned downtime, and other improvements.