Software & Analysis
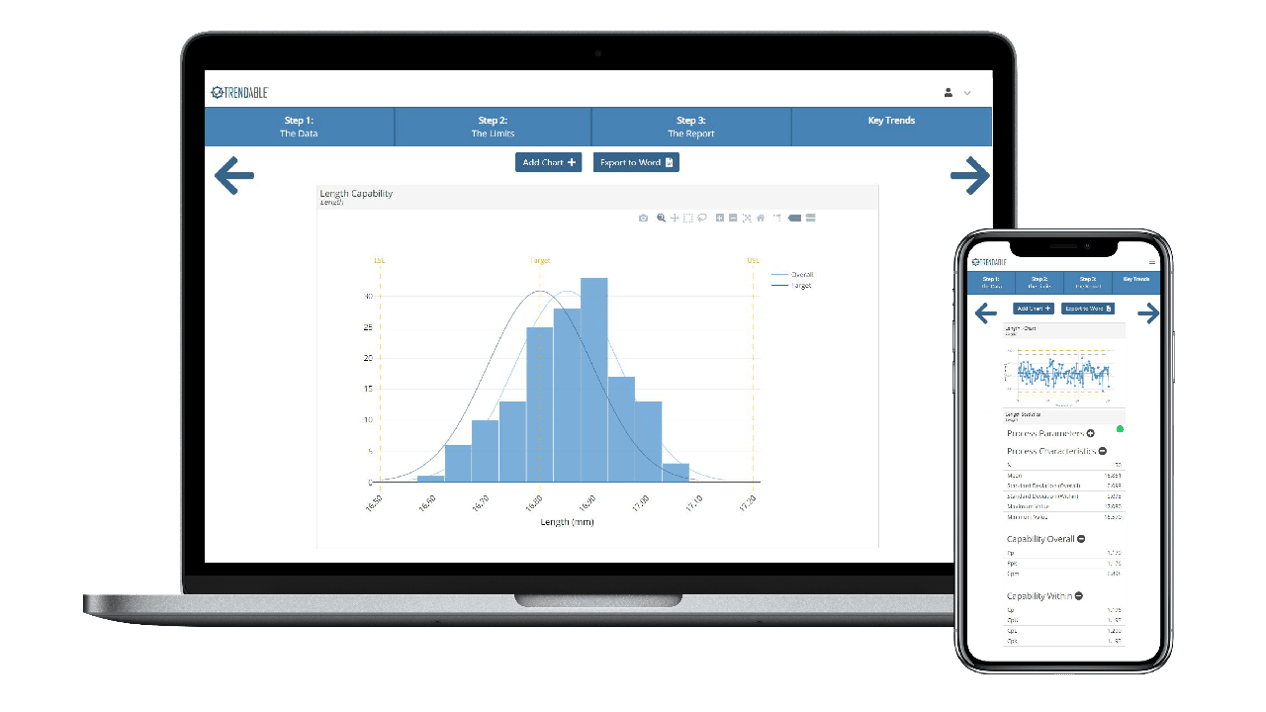
Machine learning, predictive analytics, and other new features are making statistical process control (SPC) software even more valuable. By Genevieve Diesing
Advances in SPC Software Make it Indispensable
Advances in
SPC Software
Make it Indispensable
Software & Analysis
H2 - Deck info goes here
By Paragraph Style Bolded
Statistical process control (SPC) software has become an indispensable tool for quality managers. It provides a comprehensive view of the production process, enabling managers to detect any deviations from the standard process and take corrective actions to ensure that the final product meets the desired specifications.
The future of SPC software looks promising, says Tamela Serensits, founder/CEO, Argolytics LLC, as advancements in technology are making SPC software more user-friendly and accessible. New features such as machine learning and predictive analytics are being added to SPC software, making it even more indispensable to an organization.
The Future of SPC Software
Tamela Serensits, founder/CEO of Argolytics, describes potential SPC hurdles, how SPC software can benefit manufacturers of all sizes, and how to embrace new technology.
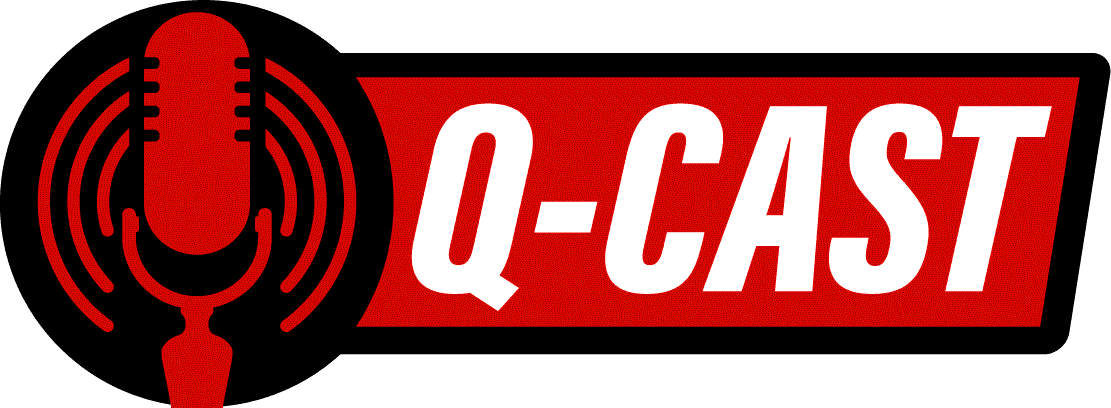
Such software helps answer key questions about process capability and stability. By automating the calculation process, SPC software helps practitioners perform SPC accurately and in real time.
SPC software provides a range of benefits for quality managers, including:
- Plotting histograms and calculating process capability indices to evaluate the normality of processes and determine their capability;
- Plotting control charts to evaluate the stability of processes as they run and provide early warnings of drifts and variation changes;
- Performing stratified analysis on processes to compare process runs and determine potential cause and effect relationships; and
- Providing digital dashboards and alarms to enable managers to manage by exception.
By reducing variation and increasing the uniformity of manufactured products, SPC software leads to increased quality and decreased costs for both customers and manufacturers, says Phil Mason, vice president of business development, Hertzler Systems.
“Excellent software bends to manufacturing processes to allow staff to follow established procedures and workflows while enforcing best practices for data collection,” Mason says. “This results in highly reliable traceability and data values that can be trusted to drive production.”
AdCreative Missing.
(double-click to add)
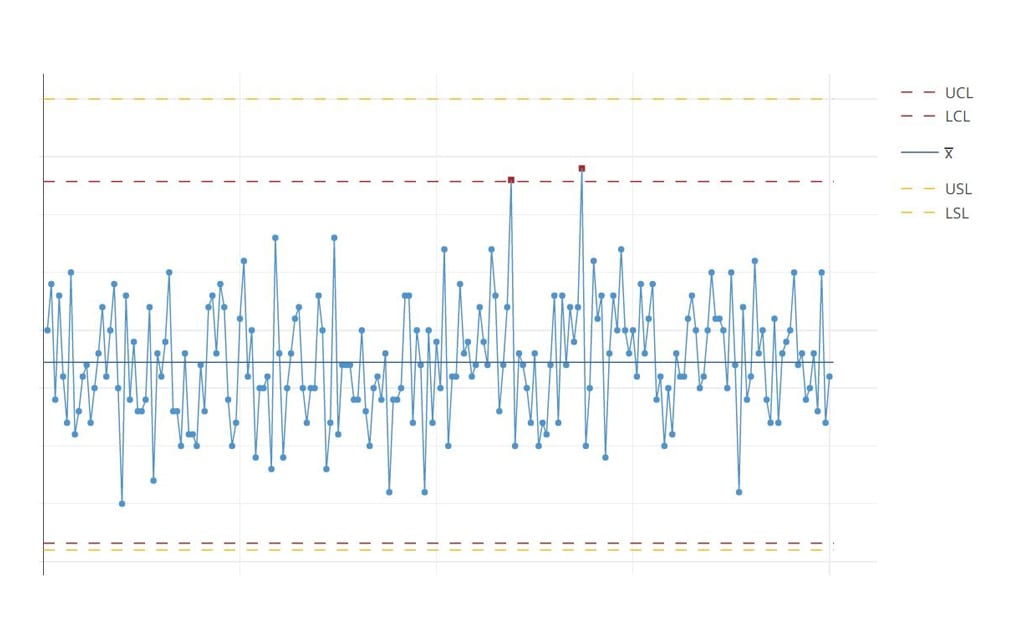
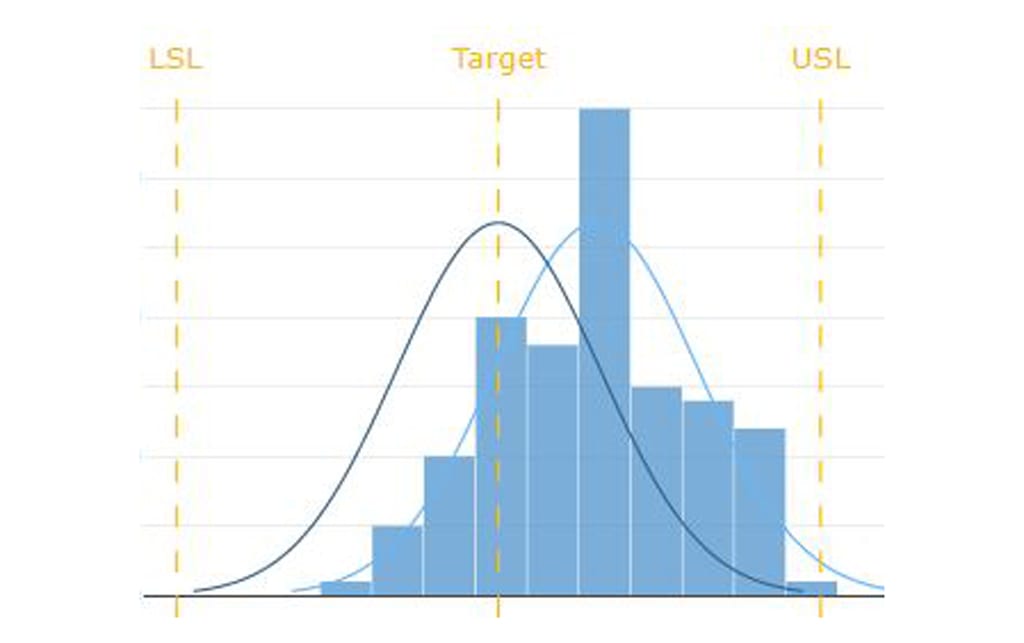
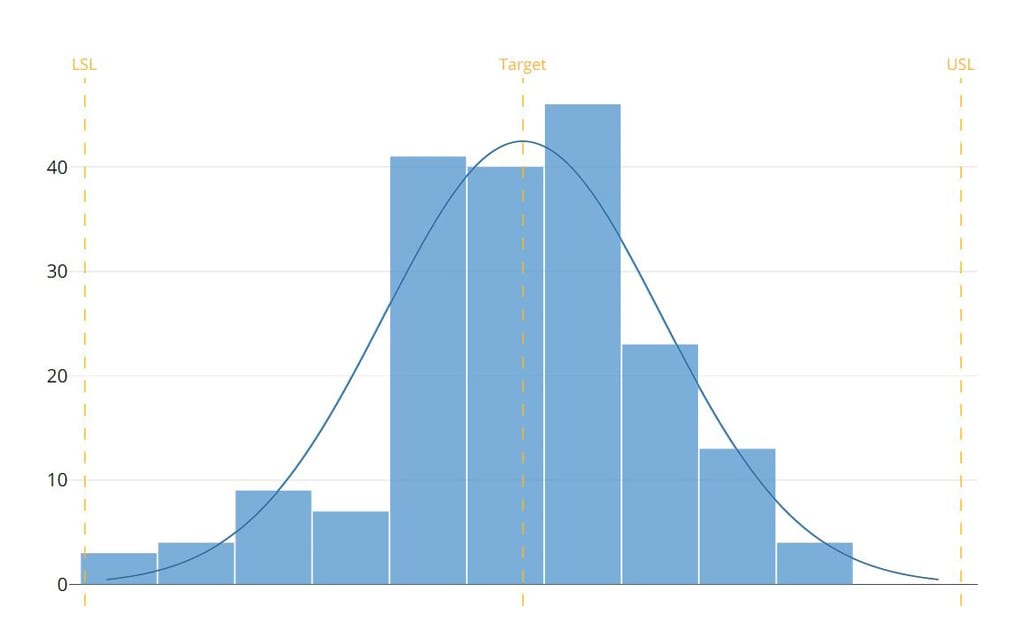
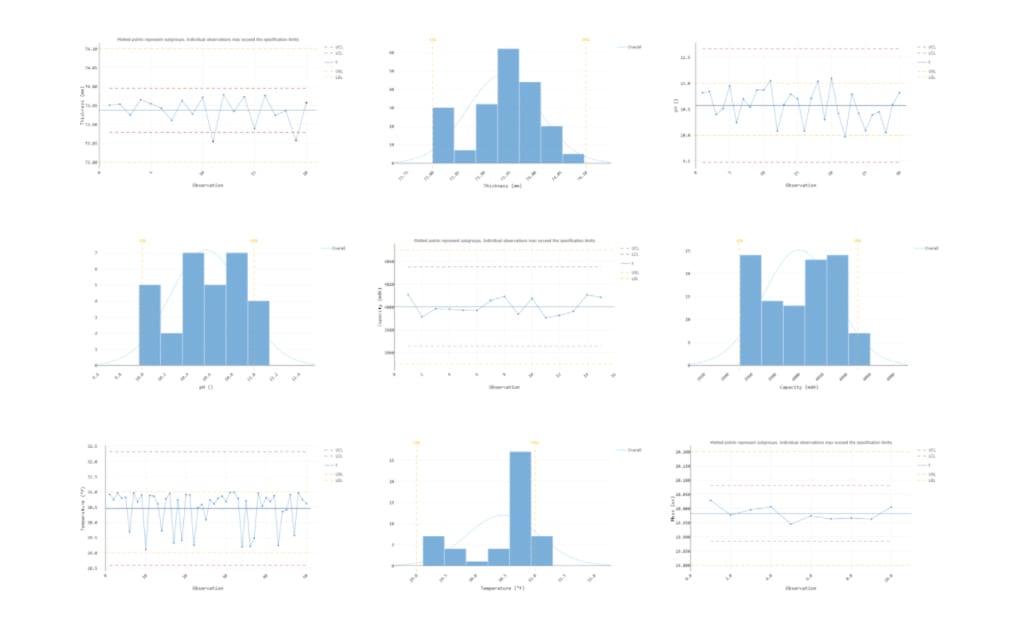
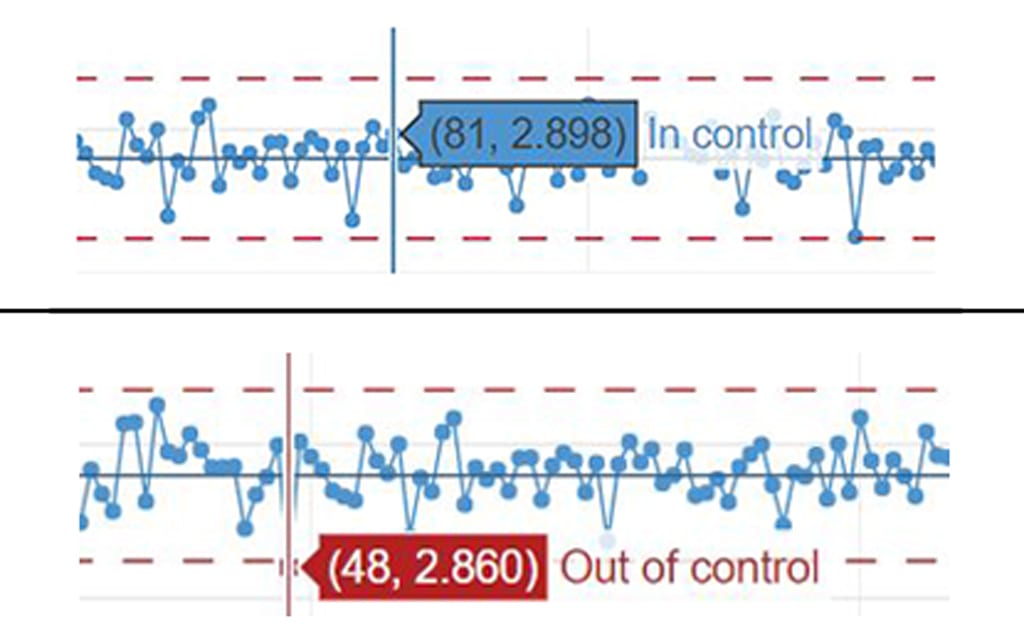
Staying up to date
Over the years, SPC technology has undergone significant changes to keep up with advancements in the computer industry, resulting in more user-friendly, accessible, and automated software solutions.
Early SPC technology started with Walter Shewhart’s work on control charts in 1920. Over the next 100 years, refinements and newer methods were introduced, says Ravi Khare, director and CEO, Symphony Technologies.
“Today, SPC technology encompasses several refinements and new methods, including the use of EWMA and CuSum charts for detecting small shifts in processes, multivariate control charts like Hotelling’s T2 chart, and pre-control charts for quick signals,” Khare says. Short-run SPC methods using Z and DNOM charts are also widely used.
However, SPC technology has evolved beyond these methods to encompass various changes in the computer industry, Mason says. One such change is the shift from local software to cloud systems, enabling users to access SPC software from anywhere, anytime. This has also led to the introduction of handhelds, laptops, and phones that can collect and analyze data, making SPC software more accessible than ever.
Another significant development in SPC technology is the shift from manual input to automated data collection through wireless gages, OPC, and edge devices. This has made data collection more efficient, accurate, and faster than ever before. Furthermore, the use of wizards and AI tools that mine data for trends and patterns contribute to improvements that are both predictive and prescriptive, thereby making SPC more valuable to manufacturers.
While these technological advancements have been beneficial for large manufacturers, smaller facilities have been left behind, Serensits says. One of the biggest hurdles for these facilities is data collection, with most of them recording their inspection and measurement information on paper.
“If there isn’t someone willing to transcribe all those hand-written notes into a computer program, talk of Industry 4.0 and data analytics is impossible,” Serensits says.
New User Requirements
As demand for customized products and services tailored to individual customer needs grows, manufacturers are producing smaller batch sizes and running shorter production runs in order to accommodate these unique requirements.
However, this shift in production strategy also means that there is a need for SPC methods that can monitor and ensure product quality during these shorter production runs, Khare says. In the past, SPC was primarily focused on monitoring process capability and stability over sustained long runs. But now, the focus has shifted towards methods that can enable quick setup changes and monitor quality during shorter production runs.
Therefore, statistical methods that can facilitate easy changeovers and quick setups are becoming increasingly important for manufacturers who want to maintain high levels of quality while also being able to offer specialized products to their customers.
From Quality Attributes to Process Parameters
Traditionally, SPC has been used to monitor product quality attributes such as fill weights or part dimensions. However, the modern trend is shifting towards monitoring process parameters. In the biopharma industry, for example, SPC techniques are used to monitor critical process parameters (CPPs) like process temperatures, pH values, and agitation rates in bioreactors to ensure a good outcome in terms of critical to quality attributes (CQAs) such as cell growth, cell viability, and low impurities.
Furthermore, the focus of SPC is shifting from monitoring CQAs to CPPs. This means that more emphasis is being given to automated proactive data collection through active transducers and IoT devices. The captured data is then extracted, transformed, and loaded into data warehouses for real-time access by SPC dashboards and alarms. “The use of IoT and ETL technologies is a major upstream enhancement to the traditional SPC tools and techniques,” Khare says.
With fewer people on the factory floor, technology needs to make up the difference, Mason says.
“Having a tool that integrates tightly with workflows and disparate data sources is essential,” he explains. “There is a lot more data being gathered today, but collecting huge amounts of data doesn’t ensure quality. Tools that can cut through the mountains of data and traceability to identify issues are critical.”
Statistical process control technology is evolving to meet the needs of small and medium-sized manufacturers. The shift towards monitoring process parameters and proactive data collection through IoT and ETL technologies is making it easier and more cost-effective for these businesses to implement quality control measures. With the right tools, small manufacturers can stay competitive and ensure that their products meet customer expectations.